DSM’s Hugo da Silva “I Don’t Think That Anyone Should Own the Ecosystem”
Hugo da Silva has been running DSM’s 3D printing unit now for over two and a half years. During that time the firm has shown itself a determined force in the market. DSM has been active in 3D printing materials for over 26 years and over the past two has redoubled its efforts. Beginning as a standalone SLA resin supplier the firm has evolved. The company has focussed deeply on verticals such as automotive, construction and manufacturing.
As well as these efforts the Dutch chemical, plastics, and food additive giant has partnered with end-users, service companies and startups extensively. Along with BASF it is DSM that has moved into the 3D printing space the most aggressively. BASF seems however to want control and end to end solutions all offered by the firm while DSM is more partner ecosystem minded.
I’ve been fascinated by how these large materials companies all approach our market very differently and we’ve been following them closely. DSM has been 3D printing passenger bridges, lead a round in Additive Manufacturing Technologies, worked with Twikit on developing solutions for automotive, offered a new fire retardant material, invested in Inkbit, headed up a group for flexible materials and worked with BAC to put parts on their car. At the center of all that activity stands Hugo who is a surprisingly serene, calm, cool and collected voice amidst the flurry of initiatives his company has deployed.
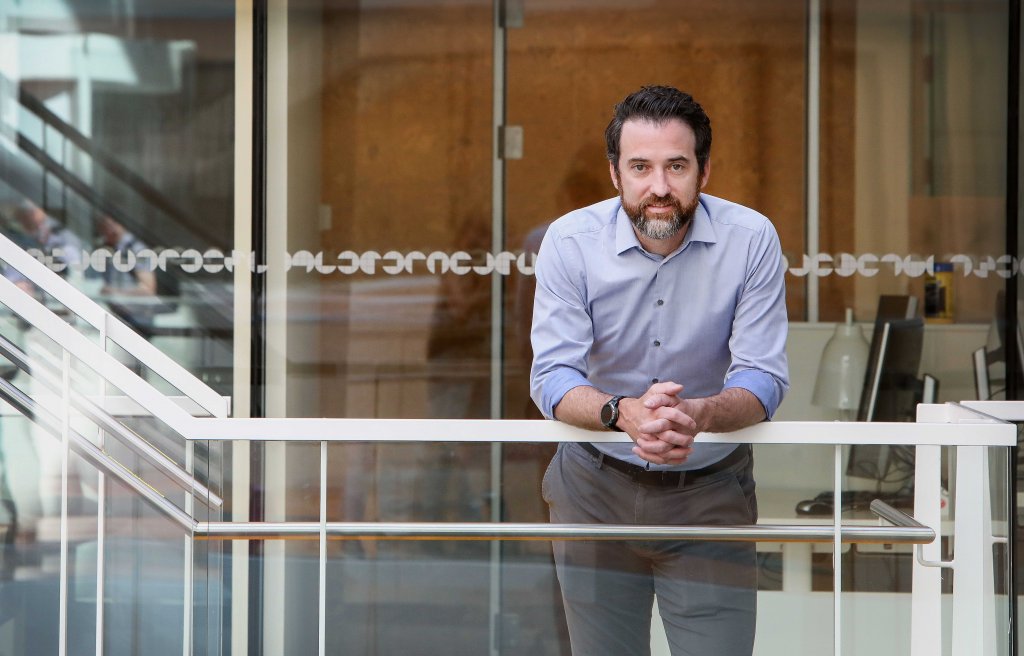
Hugo da Silva
He feels that “they’ve really made the move towards real manufacturing” and have had “good focus” on “bringing together” all of the disparate elements needed for that. The company, “filled its pipeline with real manufacturing projects, partnerships, commercial deals and venturing” that “make manufacturing happen.” DSM has made “quite some investments in the last few months” and this and it’s business development efforts have focussed on “real manufacturing of components” and “real manufacturing projects” with “a customer behind them.” His vision sees the firm “address manufacturing challenges through an ecosystem” where “DSM does not want to do it all.” In bringing about “the digital tools needed to enable manufacturing to happen” the I AM Tomorrow challenge, for example, they chose 6 startups out of 75 to together create the digital supply chain. In terms of the “digital workflow, things like prediction, manufacturing profiles, inspection” it is the combination of “all the companies in the ecosystem” that will make the “other pillars sustainable.”
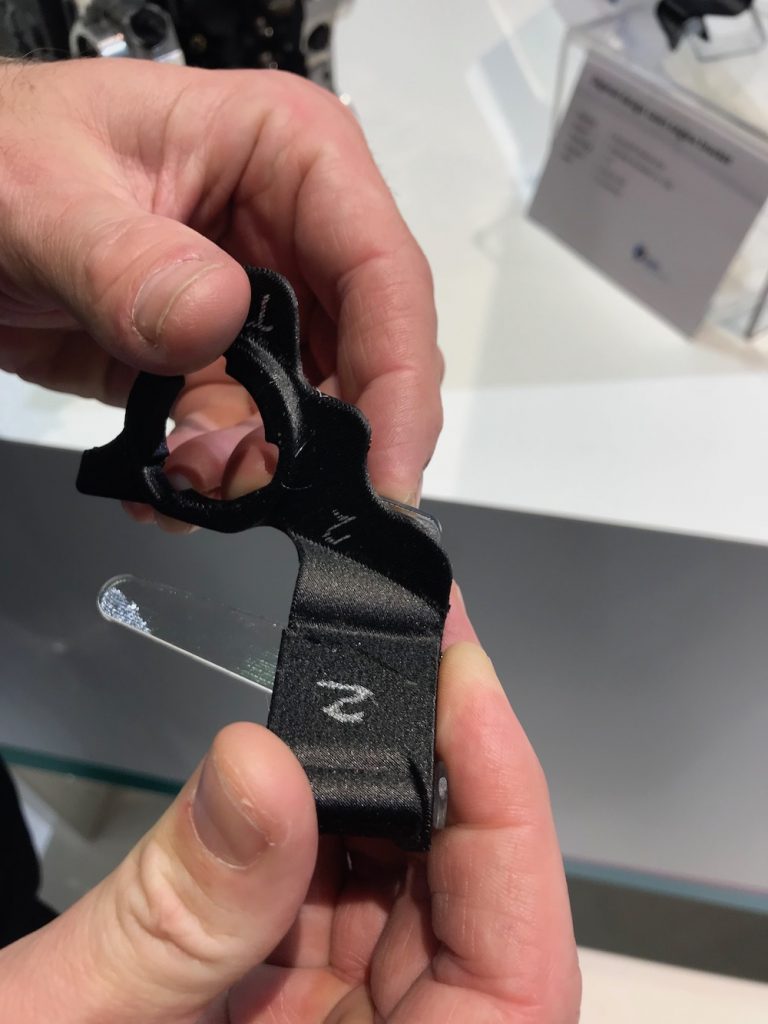
A DSM automotive part with predictive failure through Digimat
Hugo states that there is a fundamental difference between DSM’s approach and where other companies are headed. “I don’t want parts and pieces.” Instead “I want to help OEMs and customers understand how to optimize parts.” “We have a fundamentally different approach to partnering”…”I don’t think that anyone should own the ecosystem.” “If we draw a parallel to the Apple App store the one making the app owns the app” and “yes, the future is digital” but the way for “us to drive adoption for ourselves and others by sharing and enabling companies to work together.” Through this path, “everyone will make money” and this is why they are “heavy on venturing, not heavy on M&A.“
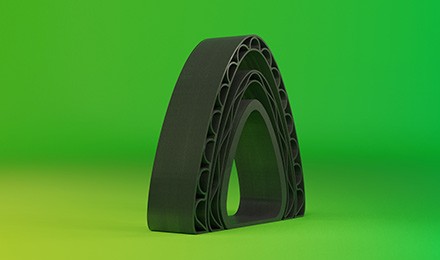
DSM Arnite material is a GF pet granulate made for large scale printing of things such as pedestrian bridges.
He believes that currently in 3D printing “in the digital era, the center of gravity, is on materials” and “materials companies have leverage because of the properties that they provide.” But, parts have to work, “if we print it a 100 times, test it a 100 times“.. in the “millions of combinations of settings” the parts have to function. He points to things such as the Twikit partnership on prosthetics, and CEAD’s 3D printing of recyclable polymer bridges using Arnite as “projects with real applications.”
The post DSM’s Hugo da Silva “I Don’t Think That Anyone Should Own the Ecosystem” appeared first on 3DPrint.com | The Voice of 3D Printing / Additive Manufacturing.
Formnext: Royal DSM, Chromatic 3D Materials, German RepRap to Develop Flexible 3D Printing Solutions
formnext 2019 just wrapped up in Frankfurt, but we still have plenty of news to share from the show floor, including the announcement of a new partnership between global science-based company Royal DSM, Chromatic 3D Materials, and German RepRap (GRR). Together, the three will be working to develop flexible, high-performance 3D printing solutions in polyurethane (PU) parts for a variety of industries, such as rail, footwear, and automotive.
Flexible materials can be used to make many different parts, but it’s not always easy to 3D print with PU and similar materials. That’s why these three companies, from different parts of the 3D printing value chain, are working together to remove the barriers from, and make sure that manufacturers have proper access to, the necessary expertise and resources for 3D printing high-performance parts with Chromatic’s FlexTune line of durable, flexible, and reliable PU elastomer materials.
“Many high-performance parts require a degree of flexibility in their daily use. Removing barriers that stand in the way of the adoption of this technology by teaming up with partners like Chromatic and GRR clearly underscores the power of DSM’s 3D printing ecosystem. Combining these partners’ expertise across the 3D printing value chain helps make 3D printing more attainable and offers manufacturers a complete solution,” stated Hugo da Silva, DSM’s VP of Additive Manufacturing. “Together, we can unlock the full potential of additive manufacturing and scale 3D printing to industrial production levels.”
In this partnership, GRR will make its knowledge and equipment accessible to manufacturers interested in adopting the FlexTune materials. According to Chromatic, this versatile line of materials can help make 3D printed products that go all the way from a flexible Shore A hardness of 40 to a rigid Shore A of 90. The company states that its “ability to customize the product is almost limitless.”
“The introduction of FlexTune 3D printable polyurethanes elastomers is a vital step for additive manufacturing to becoming the industrial process for manufacturing flexible parts. Elastomers are no longer just for prototypes, but durable enough to withstand the rigors expected of performance materials in commercial applications,” stated Chromatic 3D Materials CEO Cora Leibig. “The partnership of DSM’s market knowledge, GRR’s advanced printing capability and Chromatic’s ability to adapt thermoset materials to additive manufacturing is an exciting leap forward for the industry that we are proud to be engaged in.”
Examples of some of the specific applications that could really benefit from parts made out of flexible materials include train braking system gaskets, insoles for shoes, noise-reducing buffers and mechanical clutches for power transmission in cars, and hoses and bellows.
This isn’t DSM’s first experience with Chromatic – last year, it led a Series A funding round for the next-generation 3D printing materials company, and the two originally teamed up to introduce and explore thermoset materials for 3D printed parts, which offer more resilience and durability than thermoplastics. Now, partnering with GRR, both companies will be able to further market Chromatic’s FlexTune material line – now available around the globe.
“Due to this great collaboration with DSM and Chromatic our customers can now manufacture thermoset material parts that are difficult or impossible to produce by injection moulding,” said German RepRap CEO Florian Bautz. “At the same time the final parts have the same mechanical properties as injection-moulded parts, which brings major advantages for the future.”
The complete 3D printing solution that these three partners are offering will help many manufacturers enjoy the benefits of using flexible 3D printing materials.
Discuss this and other 3D printing topics at 3DPrintBoard.com or share your thoughts below.
The post Formnext: Royal DSM, Chromatic 3D Materials, German RepRap to Develop Flexible 3D Printing Solutions appeared first on 3DPrint.com | The Voice of 3D Printing / Additive Manufacturing.
3D Printing Industry News Sliced: Farsoon Technologies, Rize, Titomic, 3D Systems, Formlabs, Protolabs, Dassault Systèmes
Voxel8 Announces Series B Funding Round to Advance Its Multi-Material Digital Fabrication
Massachusetts-based Voxel8 was co-founded in 2014 by an interdisciplinary team of scientists and engineers from Harvard University, led by Dr. Jennifer Lewis. The company is working to develop digital manufacturing systems that will change up how we design, manufacture, and sell footwear and athletic apparel around the world.
Not long ago, the company introduced its multi-material ActiveLab Digital Fabrication System, which allows for the product development, wear testing, and production runs of high-performance athletic shoe uppers, in addition to other textiles. It’s designer-friendly, enabling automation and customization with zero tooling costs. The system uses ActiveMix extrusion technology to build 3D structures and thick films with variable cross sections directly on to textiles.
The 600 kg printer, with a 600 x 430 mm build platform, allows users to digitally design and fabricate shoe uppers, and is transforming how we develop and manufacture footwear and athletic apparel today. The system offers shorter manufacturing reorder lead times, significantly reduced design cycle times, and much lower costs for freight, labor, tariffs, and tooling. This gives customers the ability to design shoes, and other textile products, that include structural features and complex designs with little extra cost – affording them the opportunity to set up manufacturing facilities that are located closer to major end-user markets, like Europe and North America, and respond much faster to consumer demand.
Voxel8 seems to be doing pretty well for itself, and has just announced a Series B investment funding round, which was led by DSM Venturing – the venture investment arm of Royal DSM.
“Voxel8 is an excellent addition to our portfolio. Its multi-materials digital manufacturing platform is poised to dramatically impact the footwear and the sports apparel markets, strategic to DSM,” stated Pieter Wolters, Managing Director for DSM Venturing.
Additional participants in this round of Series B funding include HP Tech Ventures, as well as ARCH Venture Partners and Braemar Energy Ventures – two of Voxel8’s existing investors.
“Voxel8 is uniquely differentiated as a leader in multi-material digital manufacturing, which we believe will meaningfully expand the realm of possibilities for digitally manufacturing a wide range of products. Within the athletic footwear market alone, over 2.5 billion pairs of athletic shoes are manufactured globally each year,” said Jiong Ma, Braemar Energy Ventures. “Voxel8 is well-poised to capture substantial market share in athletic shoe upper manufacturing and, more broadly, medical and smart textiles.”
The company will use the funding to continue advancing its multi-material digital manufacturing.
“Our digital manufacturing systems are revolutionizing how footwear and athletic apparel is designed, manufactured, and sold to consumers across the globe,” said Travis Busbee, the CEO and co-founder of Voxel8. “We are excited to work with this team of world-class and experienced investors. Their global reach, expertise, and funding will accelerate the rapid adoption of Voxel8’s technology for high-volume production of athletic footwear and apparel.”
What do you think about this news? Discuss this story and other 3D printing topics at 3DPrintBoard.com or share your thoughts in the Facebook comments below.
[Images: Voxel8]
The post Voxel8 Announces Series B Funding Round to Advance Its Multi-Material Digital Fabrication appeared first on 3DPrint.com | The Voice of 3D Printing / Additive Manufacturing.
Interview with Scott Sevcik, VP Aerospace Stratasys, on 3D Printing for Aviation and Space
Out of all the possible industries that are deploying more 3D printers, aerospace is probably the most exciting. By reducing the weight of aircraft components, by iterating more, by integrating components and reducing part count and by making parts others can not, we can have a real impact on aerospace. From rocketry to commercial aviation, we’re seeing new applications grow across the board with OEMs and Tier 1 through 3 investing in qualifying parts and moving carefully into production. Stratasys has had a long history in making polymer aviation components, mainly for military applications. We interviewed Stratasys’ Vice President for the Aerospace Business Segment, Scott Sevcik, on what was happening in 3D printing for aerospace. Sevcik is an aerospace engineer who spent eight years at Lockheed in various engineering, project management, and business roles. He next worked in trying to deflect asteroids from hitting the earth and later worked at UTC aerospace, managing teams of 100 or more engineers and significant budgets before becoming their Manager Program Management. He then worked on MRO with 3D printing before working in various roles at Stratasys. He now manages their Aerospace business.
Sevcik was very enthusiastic about the prospects of both polymer and metal 3D printed parts for aviation and aerospace. Although Stratasys has worked behind the scenes extensively for military customers they were now really for the first time able to share some more public business cases. He really enjoyed working with Boom on their supersonic passenger plane initiative, for example. Sevcik connected with Boom over two and a half years previously. What started as a simple tooling engagement using Fortus systems evolved into much more.
“They were building up their factory” and “for the sake of speed started deploying 3D printing more extensively.”
He was happy that “very quickly it became a real partnership” and that he and his team were able to “work right there with them” and “dive in deep.” From the initial tooling, jigs and fixtures were also added to the project as was work on parts of Boom’s simulator aircraft. Now they’re looking at putting 3D printed parts on the actual model and later on the Boom aircraft. On the test vehicle alone there were “100’s of potential 3D printing applications, especially once the Boom team understood the technology comprehensively.”
Sevcik maintains that there is a “level of maturity with additive adequate for prototyping, tooling, and some parts on aircraft” but that many customers “see the risk on additive and see it as an unproven technology.” Now the industry is entering a different phase though, increasingly “you’re dealing with procurement people, the conversation is about risk reduction.” Especially for some applications, the combination of “Ultem 9085 for aircraft interiors with the Fortus 900mc system has a high level of maturity.”
“9085 is very useful when looking at the heat release from larger aircraft interior parts”, if “you’re looking at a foot by a foot parts or parts with more volume then let’s say a fist the heat release requirements of those parts makes 9085 a good material to use.”
As examples of such parts Scott cites “luggage bins, bulkheads, panels.” The company also has examples of parts being flown in business aircraft including serial production parts. Commuter aircraft parts, speaker enclosures and many more applications exist.
“Around 15 years ago Stratasys first got into tooling for aerospace and later into cabin interior.”
Other applications can be wholly new but Sevcik likes it when customers “challenge us” or “form a strong team with us.”
Sevcik can’t tell us much about Stratasys’ defense business lines. What is known is that the company has a strong defense base working with Lockheed, NASA and others. In military aviation repeatability on the 900mc has been demonstrated by the University of Dayton Research Institute (UDRI) and certified for parts for the Air Force. This year and a half process has led to “C5 and C130 parts being made.” Additionally, the United Launch Alliance, Atlas rocket has seen 3D printed ducting.
One other thing the company has been able to talk about is its Antero PEKK material. Sevcik says it’s especially useful for aerospace “because PEEK crystalizes so quickly” but with “Antero you have much more control over crystallinity” which lets you “make large PEKK parts.” Antero is “best suited for applications outside the cabin while Ultem is ideal for in it.”
“Filled Ultem grades can also be brittle and in some cases, semicrystalline PEKK can give a better fit depending on what you’re looking for.”
Antero can also be ESD safe which can extend its usefulness. He’s buoyed by their materials partnership with Solvay and thinks that Strategic Materials Partnerships strike the right balance between “open and closed.” It will “help expand the portfolio of materials….and give customers access to fully tuned closed systems.” Additionally, the company is looking at unlocking aerospace for “TPU” and “working with DSM on materials for SLA.”
Along with machine sales Stratasys is approaching the aviation market through its Stratasys Direct Service business and the Harvest unit which is AS 9100 certified. Many OEMs have “15% in house fabrication and outsource the rest to partners” and for these cases, OEMs want multiple partners. This means that in some cases Stratasys will work with partners and in some technically compete with them. Stratays wants to “support OEMs and help its partners and customers move into production” in this way it “meets OEMs and customers where they want to be met.”
The post Interview with Scott Sevcik, VP Aerospace Stratasys, on 3D Printing for Aviation and Space appeared first on 3DPrint.com | The Voice of 3D Printing / Additive Manufacturing.
DSM, Royal HaskoningDHV and CEAD design “world’s first” lightweight 3D printed bridge
Royal DSM Will Choose Ten Startups to Participate in the I AM Tomorrow Challenge
Royal DSM, headquartered in The Netherlands, is a global company based on science and sustainable living—with serious dedication to 3D printing also, as they realize the incredible potential such technology offers so many industries around the world. Now, they are offering an acceleration program in large-scale 3D printing and additive manufacturing for startups and scaleups, with a focus on data analytics, artificial intelligence, and related software. The teams will also participate master classes, be exposed to ‘exclusive’ networking opportunities, and receive expert coaching sessions.
The I AM Tomorrow Challenge, in collaboration with HighTechXL, Hexagon, and Ultimaker, chooses a limited number of companies to participate in the unique ten-week acceleration program meant to help launch new businesses or help existing ones evolve further. DSM offers funding or partnerships to some startups who complete the acceleration program, with applications accepted through August 8. Only ten companies will be chosen to attend, either at HighTechXL’s campus in Eindhoven or Boston, MA.
While many industrial companies are just beginning to embrace the benefits of 3D printing, a rare few others have been in on the secret for decades—and DSM is one of those pioneers, at the forefront of AM processes for over 25 years with their Somos® products. With an eye to the future and the realization of how important new startups are to the ‘digital ecosystem,’ DSM is helping to mold the continued expansion of 3D printing in the next decades.
The DSM team lists their reasons for creating the program:
- Recognition of the power of 3D printing
- World-class materials expertise
- Global reach
- Expansive industry network
- Financial resources
DSM has already invested in over 50 companies spanning Europe, the US, and Israel since 2001. This is their ninth challenge for startups, and all part of their mission to build sustainability throughout the world.
“Digitalization will transform the world of manufacturing. By building an ecosystem of partners, we can work together to create tools that support 3D printing design and production, helping our affiliates and customers create innovative new products in a more sustainable way. The I AM Tomorrow Challenge is a step toward a brighter future,” said Hugo da Silva, VP Additive Manufacturing DSM.
Hexagon’s Manufacturing Intelligence division is also working toward an end-to-end digital solution for AM processes, and they will be connecting with both DSM and partners in assessing and companies participating in the acceleration program that might be able to participate in development.
Royal DSM continues to be a force in 3D printing, from collaborations with companies like Briggs Automotive Company to partnerships with FormFutura and development of materials for new 3D printing systems. What do you think of this news? Let us know your thoughts! Join the discussion of this and other 3D printing topics at 3DPrintBoard.com.
[Source / Images: DSM press release]
The post Royal DSM Will Choose Ten Startups to Participate in the I AM Tomorrow Challenge appeared first on 3DPrint.com | The Voice of 3D Printing / Additive Manufacturing.