We’ve got some 3D printing event news to share with you in today’s 3D Printing News Briefs, along with some business news and a story about a cool 3D printed container. At the TCT Show this week, Additive Industries announced a partnership with Laser Lines, and DEVELOP3D Magazine will soon celebrate product design and metal 3D printing at a live event. CRP Technology has created an updated 3D printed fairing for the Energica Ego Corsa superbike, and employees at the GE Additive Customer Experience Center in Munich made a 3D printed beer krug just in time for Oktoberest.
Additive Industries Partnering with Laser Lines
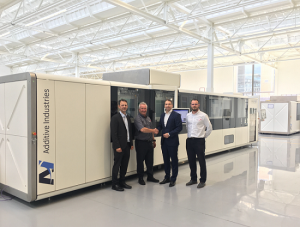
L-R: Mark Beard, General Manager UK, Additive Industries; Mark Tyrtania, Sales Director, Laser Lines; Daan Kersten, CEO, Additive Industries; and Phil Craxford, Sales Manager, Laser Lines
At the opening of the TCT Show, which took place in Birmingham earlier this week, Additive Industries announced a new partnership with Laser Lines Ltd. in order to speed up its 3D printing presence in the UK and Ireland. Laser Lines is a UK supplier of 3D printers, 3D scanning equipment, lasers, and related accessories, and will work together with Additive Industries to help grow the maturing market in the UK and Ireland for industrial 3D printers. Laser Lines will support Additive Industries in its work to further develop the industrial market for various applications in the aerospace, automotive, machine building, and medical sectors.
“With the recently announced expansion to the UK with a dedicated Process & Application Development Centre, we already acknowledge that the UK & Ireland is an important market that provides great opportunities for industrial companies to enter into industrial metal additive manufacturing,” said Daan Kersten, the CEO of Additive Industries. “With Laser Lines Ltd we add an experienced partner to our fast growing worldwide network that will work with us to identify and manage these opportunities that will contribute to our execution of our accelerated growth.”
DEVELOP3D Magazine Holding Live Event
Each year, DEVELOP3D, a monthly print and digital design journal, holds a live US event all about product design. This year’s DEVELOP3D Live event will be held this coming Tuesday, October 2nd, from 8 am – 6:30 pm at Boston University.
“We have some really fascinating folks coming to celebrate product design in the 21st Century,” Martyn Day from X3D Media, which runs DEVELOP3D, told 3DPrint.com. “We are especially pleased to have Ti Chang from Crave, Tatjana Dzambazova from new metals 3D printing company Velo3D and Olympian, Jon Owen from Team USA Luge.
“Our day is split with MainStage presentations from designers and the industry, together with a track dedicated to Additive Manufacturing, with all the latest in metals 3D printing.”
Tickets are just $50, and include full access to the conference and all 30 exhibitors, plus refreshments, lunch, and drinks at a social mixer. There will be 20 speakers presenting in two separate streams, and topics include CAD, topology optimization, 3D printing, virtual reality, and product development.
3D Printed Fairing for Ego Corsa
Together, Italy-based CRP Group and its subsidiary Energica have been using 3D printing and Windform materials to develop components for electric motorcycles and superbikes for a few years now. In April, the Ego Corsa electric motorcycle completed its third demo lap, and at the last series of road tests before the first edition of the FIM Enel MotoE World Cup, the 2019 2019 Ego Corsa prototype hit the track with a new 3D printed fairing, manufacturing by CRP Technology with its laser sintering technology and Windform XT 2.0 Carbon-fiber reinforced composite material. The 3D printed fairing update has improved the Ego Corsa’s aerodynamics.
“We have had the fairing available in short time. Thanks to the professional 3D printing and CRP Technology’s Windform composite materials, it is possible to modify motorcycle components – even large ones – from one race to the next ones, in order to test different solutions directly on the track,” said the Energica technical staff.
“This fairing is not only more aerodynamic, but it also has a smaller frontal and lateral section. These improvements led to achieve increase in terms of performance and they led to achieve greater manageability in fast corners.
“The Windform XT 2.0 has once again proved to be a high performance composite material. We are very happy how the 3D printed new fairing behaved during the tests.”
GE Additive 3D Prints Metal Beer Stein
Even though the month of October doesn’t start for another few days, Oktoberfest itself officially kicked off last Saturday in Germany. In order to celebrate the occasion, the AddWorks team at the GE Additive Customer Experience Center in Munich, which opened last winter, decided to take another look at the traditional glass beer krug; what we’d call a pitcher or stein in the US.
The unfortunate thing about glass is that it breaks. Obviously, if you’ve enjoyed too much beer at an event like Oktoberfest, the likelihood of breaking your glass drink container goes way up. So AddWorks decided to create a new prototype beer krug, but instead of using glass, they 3D printed it using a combination of stainless steel and titanium…and the result is pretty impressive.
Take a look at the video below, which stars the head of the Munich CEC (Matthew Beaumont), to see the whole process:
Discuss these stories and other 3D printing topics at 3DPrintBoard.com or share your thoughts in the Faceboook comments below.