
Massachusetts-based additive manufacturing company RIZE is best known for its Augmented Polymer Deposition (APD) technology, which allows for the quick, easy release of supports from a 3D printed part. But we haven’t seen a new 3D printer from the company since it first introduced its industrial-grade desktop Rize One in 2016…until now.
Today at formnext in Frankfurt, the company officially launched its new XRIZE 3D printer – the first industrial desktop AM solution for manufacturing full-color functional polymer and composite parts. Additionally, RIZE is also taking the opportunity to introduce several materials and IoT solutions at the trade fair. All of these new products will provide the company’s customers with maximum flexibility and a fast ROI, while still offering the minimal post-processing they’ve come to expect from RIZE.
The XRIZE 3D printer leverages the company’s patented APD process by extruding an engineering-grade thermoplastic, while at the same time jetting cyan, magenta, yellow, and black inks through its industrial printheads. Then, Release Ink is jetted between the automatically-generated supports and the part, so that users can quickly peel the supports away for a smooth surface finish with no additional finishing required.
Typically when it comes to full-color 3D printing, users have to make trade-offs between color, price, and strength, choosing inexpensive colored parts that are not functional or paying a premium for working, full-color prints. Separate 3D printers are often required to deliver different capabilities, like providing full-color, end-use and production parts, being quiet enough for office use, and printing with carbon fiber and other similar materials.
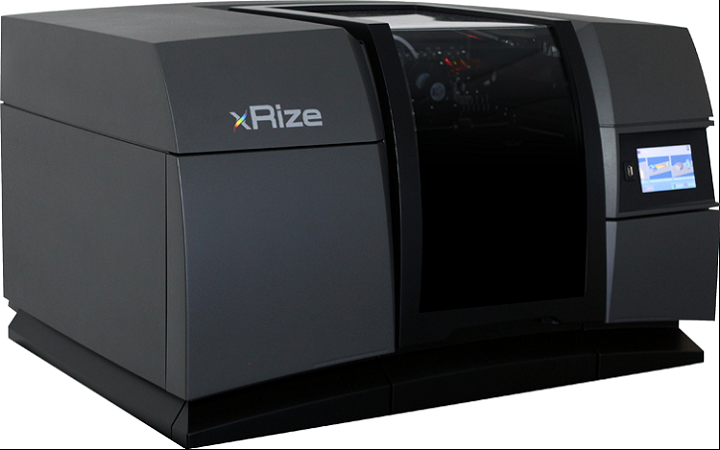
With the new XRIZE, users can now produce full-color, functional polymer and composite parts. The machine is safe, secure, and easy to use, with minimal material management, and is capable of fabricating prototypes for applications like consumer products, GIS mapping, FEA and stress analysis, anatomical parts for the medical field, package design, tooling with safety instructions, and parts for marketing and entertainment sectors.
The 61 kg XRIZE 3D printer comes with a heated build chamber, auto-leveling build plate, best-in-class Z axis strength, intuitive touchscreen, and automatic filament changeover. It has optional Internet and Cloud connectivity, and RIZE ONETOUCH software makes it fast and easy for users to import color CAD files and apply images, text, and texture maps to monochrome part files. The system has four-channel color, with an additional channel dedicated to Release Ink, and can use several kinds of materials, including RIZIUM One and RIZIUM Black.
Additional specs include:
- 310 x 200 x 200 mm build volume
- .250 mm or .125 mm layer thickness
- X/Y 300 dpi resolution, X 200 dpi resolution at .125 mm layer thickness
- Safe process and materials for office compatibility
The XRIZE can also run the company’s two newest materials: RIZIUM CARBON and and RIZIUM ENDURA. The former, an engineering-grade, carbon fiber-reinforced thermoplastic filament, has a higher modulus and excellent visual finish, and is good for applications like functional prototyping in manufacturing. Fiber-reinforced RIZIUM ENDURA has high impact strength and accuracy, is compatible with the company’s full-color inks, and is ideal for 3D printing large functional parts.
The company also introduced RIZE CONNECT at formnext today, which allows users to manage and monitor their RIZE ONE and XRIZE 3D printers remotely for maximum efficiency. RIZE CONNECT will send notifications, manage an enterprise print farm, and queue jobs from both desktop and mobile devices. Additionally, users can make parts with greater security and part traceability, thanks to options like digital part identification, QR codes, and version control.
RIZE CONNECT will be available in 2019.
“Our mission from the beginning has been inclusive and sustainable innovation. With this approach, we can take additive manufacturing anywhere and to everyone. The way to do that is to make industrial 3D printing easy, safe, and fully digital,” said Andy Kalambi, the President and CEO of RIZE. “Our innovative platform approach is the core to driving sustainable innovation. With the launch of XRIZE, RIZIUM CARBON, RIZIUM ENDURA and RIZE CONNECT, we are now realizing the potential of this platform, providing our customers with maximum flexibility, complete ease of use and quickest ROI.”
The new XRIZE 3D printer, with an MSRP of $55,000, will be available for purchase in 2019. To see this new system, and the rest of RIZE’s comprehensive product suite, visit booth C28 in Hall 3.1 at formnext, which ends on November 16th. In addition, Kishore Boyalakuntla, RIZE’s VP of Products, will be discussing the announcement in further detail during a presentation this afternoon, titled “RIZE: Announcing a Technology Platform for Connected Innovation and Scale,” on the TCT Stage.
Discuss these new products and other 3D printing topics at 3DPrintBoard.com or share your thoughts in the Facebook comments below.