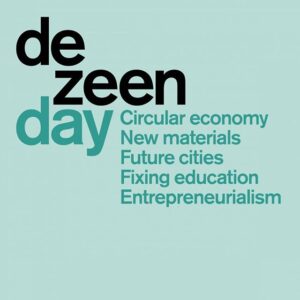
Dezeen Day
The first annual Dezeen Day conference, was definitely a sight to see and I will do my best to share my opinions on the day as a whole. I did not know what to expect going into the conference, but it seemed like it would be a fun time so I decided to go. It turned out to be an eye-opening and interesting experience.
Firstly I want it to be known that architects and designers think in such an interesting manner. I say this because you can see and hear the fascination they all have with life and building. They try to answer seemingly impossible questions. They design things through such innovative means. My brain was in pain throughout the day. It was not bad pain. It was the pain you get when learning something that is out of your comfort zone; it hurts now but you will feel amazing later. The way designers think allows them to have no fear of tackling large issues. The focus of this particular conference was on the Circular Economy and sustainability practices within design. In the design community, there is no one way to solve a problem. There are various ways to tackle an issue. Through the panel discussions and keynote speakers, we got a sense of how there are so many people working in different sectors of design to make this happen. I will reflect on a couple of major talks and discussion points from some of the panel conversations.
The first talk of the day was my favorite, and it had a lot of information packed within it. Paola Antonelli, the Senior Curator of the Department of Architecture & Design and the Director of R&D at MOMA, gave an interesting perspective to the audience. Her belief is that the understanding of humans and their likely extinction can lead to better resulting futures. What I deduced from this was that being aware of extinction leads us to be aware of the future generations and people we may be affecting. It is important for us to focus on future scenarios and think about how our actions can hurt others. This begs the question, “What can people do?”. The rest of the conference was aligned toward answering the question of what can people do to make effective change for the future within design. Paola also stated, “We want people to understand the complexity of the systems but not to be scared of them.” Designers are able to readily grasp design thinking and problem solving, but a variety of people outside the field may not be able to implore the same skills. This makes it important for design to help others outside of its community, and Dezeen Day also had a discussion on education reform. The conference was interwoven and facilitated elegantly. Each panel there was able to feed into one another.
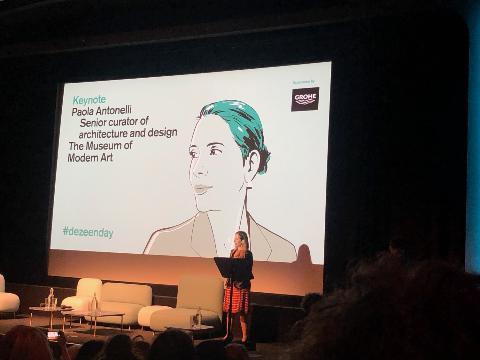
Paola Antonelli at Dezeen Day
There was a lot of information packed within this talk so I did my best to summarize a lot of her ideologies and main points of discussion. The talk had a focus on waiting for making things. Within the design community, ideas are a dime a dozen, but which ones are effective? Typically the ones that well mapped out and executed over time. This ties into her discussion about extinction. We are planning towards building better infrastructures to help humanity over time, and this takes a lot of diligence. This reflected the rest of the day in terms of discussions and panel conversations.
Throughout the discussion, Paola was highlighting the various art she curated for her Broken Nature Exhibition and the significance of each piece. Something of interest to me was the scientific lens that most of the pieces were taking. It lead to other discussion panels throughout the day focused on science, design, and architecture.
A final large takeaway of the talk was that anger could be a source of change.
The only way to live well is to be for others or amongst others. Anger could be a better engine to try and improve things in the future.
This mindset is interesting as it shows the raw emotion needed to drive change. Anger is a great motivator for change because when we are lukewarm, complacent and not very engaged with our surroundings, we have no reason to improve.
The rest of the conference was conducted through the lens of the initial talk. The discussion panels held were the following:
- Panel discussion: post-plastic materials
- Panel discussion: future cities
- Keynote: Liam Young
- Conversation: Designing for the circular economy
- Panel discussion: entrepreneurs
- Panel discussion: fixing education
- Keynote: Dr. Alexandra Daisy Ginsberg
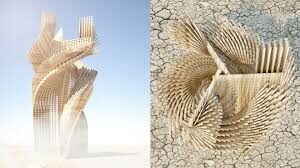
Work by Arthur Mamou-Mani
The ideals and conversations at the conference were outlined thoroughly with this introductory talk with Paola. I personally resonated well with the Panel Discussion for Post-Plastic Materials. The conversation was oriented towards the various ways we as humans can be innovative in the materials we are using. I was able to talk to some people from the discussion panel after their talk such as Natsai Audrey Chieza. She is a designer and founder of Faber Futures, and they create biologically inspired materials. After hearing the talk and seeing the work that these individuals are doing it opened me up to a critical lens of understanding with societal material usage. It also inspired me to think big in ways that seemed unfathomable. This was the result of listening to Arthur Mamou-Mani. Arthur is an architect and director of Mamou-Mani Architects. He also specializes in digital fabrication and advanced bioplastics. I was in awe by the extremely large structures he creates with 3D printing and the use of wood. I will be following up on his work later as well.
I also met some other people who helped with the conference. This included Stacie Woolsey who is a design graduate who created her own master’s course. We were able to have a fun chat before her actual panel discussion. She definitely is a great inspiration for young people who want to rid of the typical educational model. I will be discussing this thought process a bit more later.
There were a couple of conversations had about 3D printing and biomaterials that I will be discussing more in-depth because they require some more research. For the overall conference though, it was a good time. The staff was excellent, and the overall programming was extremely engaging. There was no moment without engagement talk wise. I am a reporter who mostly focuses on 3D printing, but after the conference, my eyes have opened up significantly to the importance of design practices. It was awesome to see people who were combining architecture, bioengineering, and design to build interesting things.
The post Dezeen Day Recap appeared first on 3DPrint.com | The Voice of 3D Printing / Additive Manufacturing.