The first day of the RAPID + TCT conference was bristling with activity. The first day mostly consists of lectures and workshops. At some other conferences, this is a secondary affair but here in Detroit we’re really seeing this to be the meat and bones of the conference on day one. There were a tonne of conference events and workshops today from the very general to the highly specific. There were workshops on casting materials for automobiles, implementing quality systems for medical devices, metal printing, and how to use 3D printers in hospitals and biomaterials. A lot of these were almost all day events with multiple speakers that were almost conferences in and of themselves.
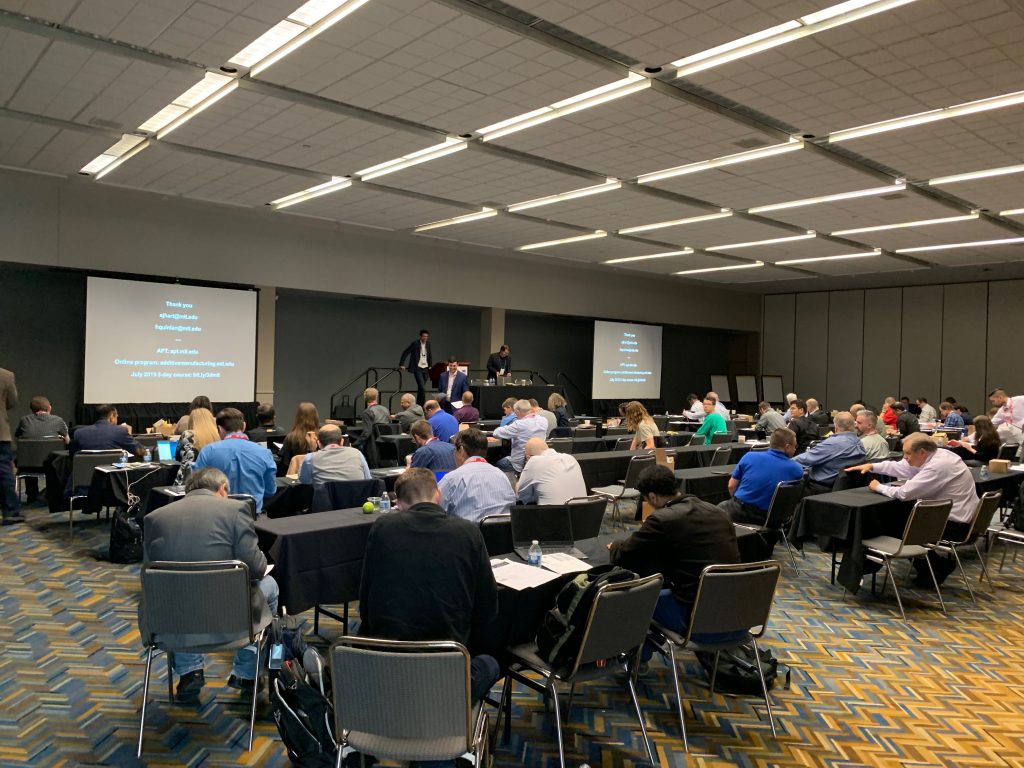
Professor Hart’s Workshop
Professor John Hart gave a great presentation on applying materials and processes to making 3D printed parts throughout the life cycle. This workshop was great for people trying to start business cases internally with 3D Printing. It covered things such as costing and the relationship with the design to the final part. Walking around through all the workshop rooms I was really spoilt for choice. I really do believe that the “workshop day” at Rapid is underappreciated and under-visited. There are people here and there is knowledge here that you really can not find anywhere else. Do not miss this first day if you want to come next year! Having said that there were thousands of attendees for the different workshops and the first day already felt like a big conference.
Things started to get much bigger when we went to the Ballroom for the main opening ceremony.

Erika Berg of Carbon and Vitorrio Bologna of Riddell
Erika Berg of Carbon and Vitorrio Bologna of Riddell keynoted on how their companies were working together to try to make individualized mass customized helmet liners for football helmets. Individual helmets and other sports gear could become a huge application for 3D printing. Using one build of a Carbon L1 3D printer all of the distinct parts of a helmet liner can be produced. The data comes from a scan of a players head which is now done by 3D scanners but Riddell wants to go to a home scan solution for that in the future. The data gets sent to Carbon which then calculates the optimal design of the helmet cellular structure which may have 140,000 struts. Riddell already has 4000 3D scans to work with as well as thousands of readouts of player crashes to tell them how to design the helmets. In the future, the team wants to put accelerometers and other sensors in all helmets to acquire more data that would let them produce better helmets. They want to implement this for all football players from the Pro’s and college to the youth level. All in all the approach with cellular structures and data gathering seems very sound and this is a huge application for 3D printing if it goes forward. I just have questions with the Carbon business model. If Riddell leases the printers if Carbon slices the files if Carbon determines the optimal structure of the helmet then what is Riddell?
If we look at firms such as Nike: Nike is the brand, they design the shoes and know how to market and brand them. Others manufacture. Now Riddell is outsourcing key ownership of the core design competency that they and firms like Nike have. Won’t they be tied to Carbon forever? Isn’t the core part of their helmets the connection between the “crash test data”, head scans and how to create the cellular structures for the helmets?
Carl Dekker of Met-L-Flo then came on. He is the current ASTM 42 Chairman and Advises SME. He presented awards on the best research paper and project. Fast Robotic Soft Matter 3D Printing for Neurosurgical Phantoms Fabrication by Michael Chang was the winner of the Dick Aubin Distinguished Paper Award. On the 23rd you can see him present it. On the research project side the winner was The Copper Cooler: Heat Sink for CPU’s by Lisa Brock and Gitanjali Shanbhag.
Industry consultant Todd Grimm then took us through the companies that had applied for the innovation award and revealed that 48 out of 400 exhibitors would be on a list to be considered. He then went on to detail all of the firms and their particular innovation in order to tell everyone “What’s New” at Rapid. I thought that this was a particularly helpful presentation for visitors. He also mentioned that the finalists for the innovation award would be: Digital Alloys, e3D, Fabrisonic, Formalloy, NXT Factory, Rapidia, Sigma Labs and Sintratec. I for one really can’t choose there are a number of very deserving firms there and also some very sympathetic teams. Usually one could guess but this time its wide open as far as I’m concerned.
Then the SME Industry Achievement Award was revealed. The winner was Ely Sachs. Ely was a Desktop Metal co-founded but also a core inventor of the “MIT patent” inkjet head based 3D printing technologies years earlier and a more than deserved winner! This was a very exciting almost my brain runneth over first day here in Detroit and I can’t wait to discover more.