In Material Extrusion (FDM), we can now use inexpensive machines to make dimensionally accurate & tough parts in various materials at low cost. These parts can fulfill many industrial and manufacturing applications bar one glaring defect. Material Extrusion (FDM) parts are often ugly, and layers can be seen on the rough parts. FDM parts and materials are improving all the time; parts are getting smoother and better looking out of the machine. Clusters of FDM machines bring throughput and versatility and have begun to be used to manufacture parts at scale.
With Selective Laser Sintering (powder bed fusion), one can make thousands of individual parts in many different geometries. Highly detailed polyamide SLS parts have been used for tens of thousands of surgical guides and have found many industrial applications. All parts have to be depowered and cleaned of excess powder, however. Additional steps, such as mechanical finishing are often needed to close the open surface texture of SLS parts.

With Dye Mansion depowdering is combined with surface improvement and coloring to make parts more world proof.
With SLA (stereolithography, vat polymerization) tens of millions of molds have been made for jewels with millions more being used in the dental industry. Additionally, millions of intermediates have been made for aligners. Direct SLA parts in hearing aids have revolutionized the In The Ear hearing aid industry, winning the market in customized fit ITE hearing aids. And yet, every SLA part has to be cut off of supports manually, and most have to be filed down afterward. Parts have to be conveyed to a washing station and a UV flash machine.
Meanwhile, in the SLS world, the future of manufacturing consists of a man with a brush brushing off powder from a part. It won’t surprise you that a third of part costs are perhaps due to finishing and post finishing parts. We boast of machines that can, in a day, make a new part, only to casually leave out that this part may spend another day in a tumbler. We jump on the gleeful subsidy bandwagon that is Industry 4.0 while a lot of the cost of 3D printed parts is in conveyancing.
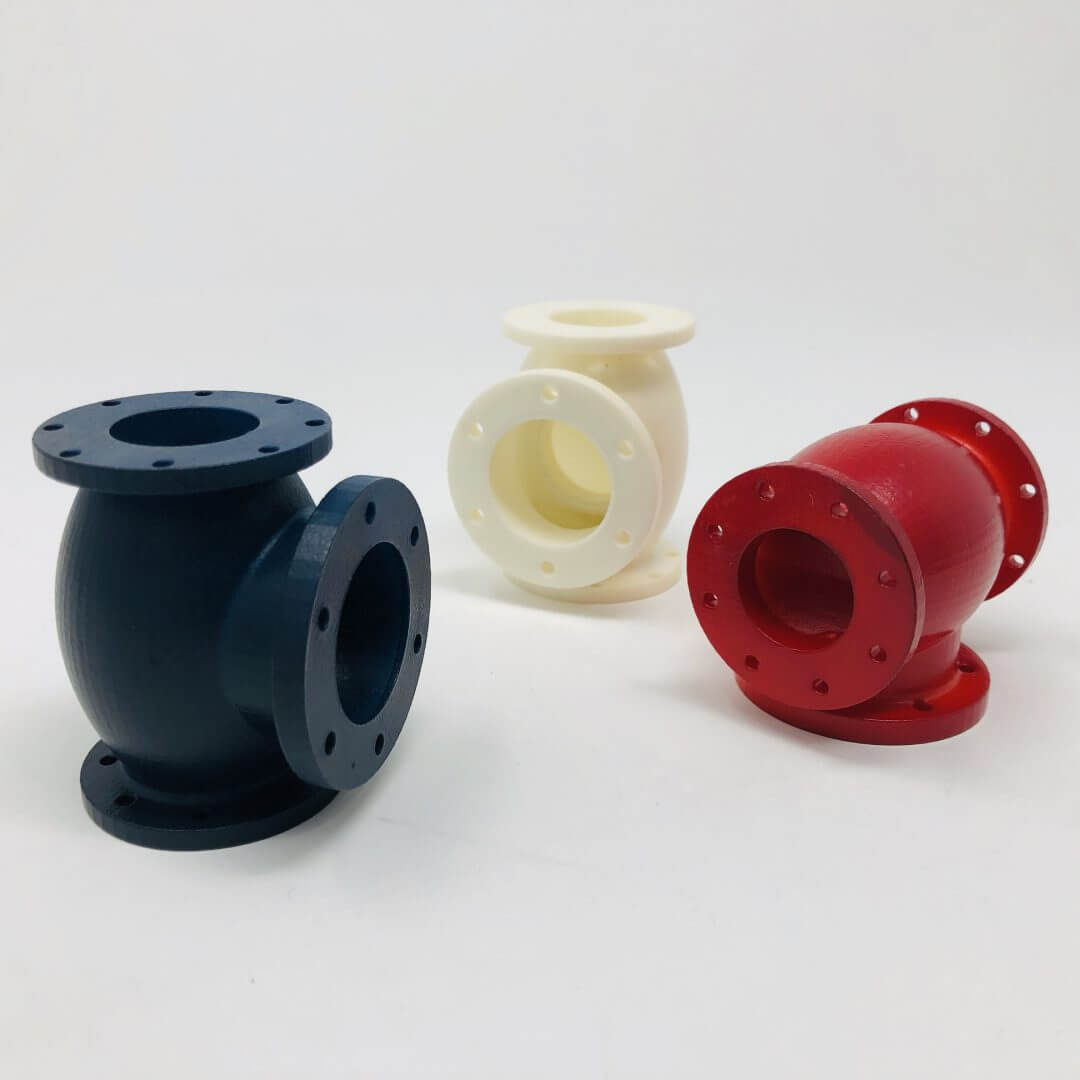
Additive Manufacturing Technologies‘ automated surface finishing colors and finishes in one step.
Significant part costs comprise of people carrying parts around a factory. A woman leans over, looks at a piece of paper, matches the part, carries it to her station and then later puts it on a tray where a colleague takes it to a new station. This is Industry Bore.0, not 4.0. And metal printing? Like all things, it makes the polymer part of our industry look easy. Parts have to be sawed off by hand, and a number of post-processing stations always pay a part: from HIP to EDM to shot peening to destressing to spending a week in a tumbler it often needs to happen to your metal part.
We can not ask industrial manufacturing firms to learn new ways of thinking, master design for additive, change parts in their inventory and take on new unknown risks in return for a future where parts are marched around a “factory.” I say factory partially in jest because currently manufacturing with 3D printing is much closer to a collective of be-dreaded sandal-wearing artisanal vegan soap makers than actual manufacturing.

Rosler’s AM Post Processing Line of machines remove powder, support and structures.
Imagine us, some hippie collective with handcrafted bamboo bowls trying to sell our way to the Six Sigma people? Just change everything; it will be great. Hope is the new one error per ten million. Do you want a Craft aircraft? Do artisanal aero engines sound like a good idea to you? Would you like to take a trip to Mars on a handcrafted rocket? Would you like your next hip to be made with love? Or would you prefer it to have things like quality control? We’re currently selling a dream to manufacturers that for many applications, we can not turn into a reality.
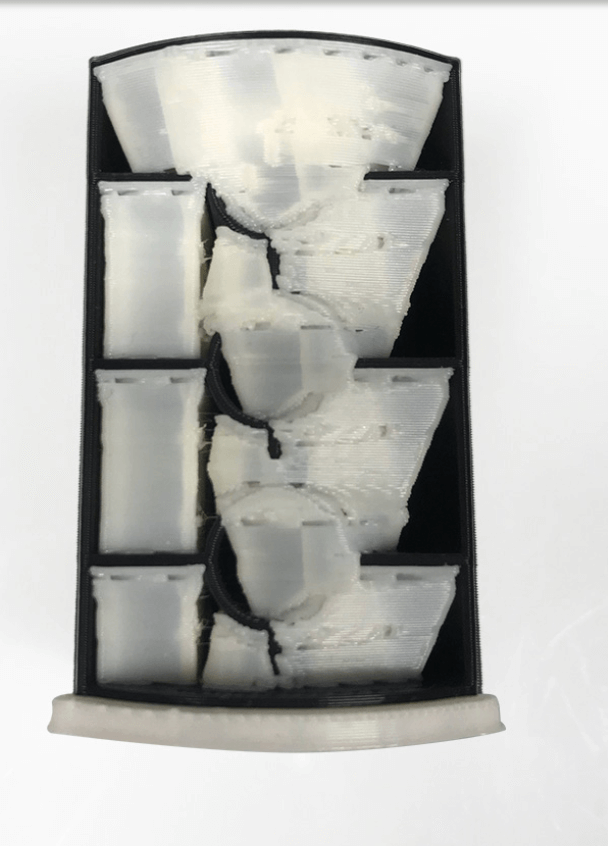
Post Process showing you parts before and after their process.
What can make 3D printing for manufacturing real? Automated Post Processing. By automating the entire post-processing chain, we can dramatically lower the part costs of 3D printed parts. We can make many more business cases worthwhile by making 3D printed parts significantly cheaper. By automating conveyancing throughout the plant, we can dramatically reduce the overall cost at high throughput. By offering post finishing to improve the surface quality of parts, we can make better looking and better-performing parts. Consumer-friendly and industry-friendly parts can ensure that the adoption of 3D printing is more rapid. The combination of automated post-processing with 3D printing will let parts be produced close to the consumer in wealthy countries at a reasonable cost. Improved post finishing processes will improve surface quality and let 3D printed parts be deployable for many more applications. If we integrate automated QC and QA processes into post-processing setups, we can genuinely offer manufactured 3D printed parts to many industries. Many firms are looking into automating the entire post-processing chain. From Post Process to Rosler, Additive Manufacturing Technologies and Dye Mansion, it is these companies that will unlock manufacturing for us all.
The post Why Automated Post Processing Makes Manufacturing With 3D Printers Possible appeared first on 3DPrint.com | The Voice of 3D Printing / Additive Manufacturing.