A large group of researchers came together to author Bioprinting in Ophthalmology: Current Advances and Future Pathways, published recently regarding their findings on bioprinting within the field of ophthalmology. While they understand the promise 3D printing with cells has in so many applications, there is serious potential for ‘highly delicate organs’ like the eyes and the heart. Here, they review some of the strides made in bioprinting over the past 20 years, and specifically in ophthalmology.
As the researchers point out, over 30 percent of people around the world have visual impairment issues of some kind. Because the eye presents such an easy access point, however, doctors have excellent access for performing medical procedures and supplying implants. This means that the eyes are also very conducive to treatments with bioprinting.
3D printing so far has been responsible for a wide range of developments in optics, whether for lenses in smart phones, or a variety of different printing systems to include those for fabricating models of the eye for surgeons. Although bioprinting allows for tissue engineering and the potential for transplants, the benefits of 3D medical models alone are enormous as they give medical professionals access to visual aids for more accurate diagnoses, treatment, and education for both patients and their families.
Medical models of the eye also serve as invaluable training devices for procedures for medical students, and for surgeons who may be performing unique surgeries never attempted. They may even use the models in the operating room. Most of these models today are created with the 3D Systems Z650 printer.

(a) Schematic view of the cross-section of our physical model eye; (b) two printed parts provided main structure of the physical model eye; (c) use of the physical eye model for assessing the fundus range of the viewing system; (d–f) pictures of the angle bars photographed under 128D lens, 60D lens, and 60D lens with model eye tilt; (g–i) other three eye models printed and fabricated with different anterior chamber and total axial length.
The authors point out that because there are still so few ‘workable materials’ for ophthalmology in additive manufacturing, there is still substantial room for further innovation:
“The printing of artificial lenses, glaucoma valves and other medical implants developed in customized processes will be a reality in the future,” stated the authors.
“It is believed that printing of artificial lenses, glaucoma valves and other medical implants with customization and on-demand supply will be possible in the coming years. Further, numerous next generations ophthalmological products are likely to be benefited with this technology.”
Smart-phone technology, the impetus for many different applications today, also allows for an interesting ‘alternative use of 3D printing,’ as a variety of different devices can be attached to mobile phones for examination of areas like the ocular anterior segment, giving medical professionals easy access to detect conditions like cataracts, uveitis, ulcers, and other defects.
“These devices are more than ten times cheaper than standard ocular imaging devices,” state the authors.
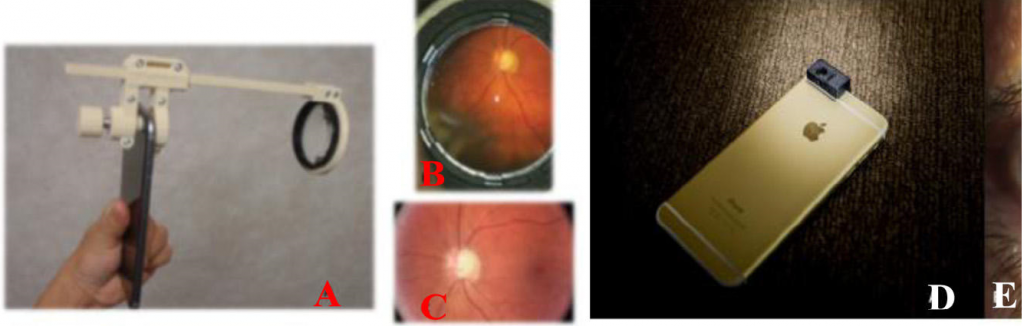
(A) 3D printed retinal imaging adapter on a smartphone; (B) an image of a glaucomatous disc captured with the smartphone retinal imaging adapter; (C) an image of the same glaucomatous disc captured with a standard fundus camera; (D) 3D printed smartphone slit lamp microscope, (E) an image of a patient with a white cataract captured on a smartphone with the 3D printed slit lamp microscope.
Bioprinting systems for ophthalmology are still difficult to come by, due to the lack of suitable materials, mechanical limits, speed in production, and affordability; however, the researchers are convinced that because so many innovations are being continually presented, ‘the development of a fully functional artificial eye’ is imminent.
“Overall, it can be concluded from the research endeavors in 3D printing in ophthalmology that this technology has the potential to improve the treatments of vision impaired patient by helping the doctors in performing risky surgery,” concluded the researchers. “The only need for this is to explore the innovative trends in customization of the medical devices which are highly desirable in-terms of market demand. Ultimately, the printed ophthalmological devices can heal the poor vision and other ocular diseases.”
Bioprinting continues to make steady impacts in the medical field, and while so many fascinating innovations have been made in ophthalmology, from orbital implants to prosthetic eyes, researchers continue to branch out into nearly every area of human health with medical models, and a variety of other implants and devices to change patient’s lives around the globe. Find out more about bioprinting efforts in ophthalmology here.
[Source / Images: Bioprinting in Ophthalmology: Current Advances and Future Pathways]