Authors Henry Giddens and Yang Hao seek expanded and improved ways to manufacture antennas, releasing the findings of their study in the recently published ‘Multi-Beam Graded Dielectric Lens Antenna from Multi-Material 3D Printing.’
With important applications like mobile networks relying on powerful, directive antennas, there is ongoing interest in refining them further, broadening the potential for performance. In this study, the authors 3D printed a new lens with multiple materials. Able to function omnidirectionally, their final lens radiated with a gain of 8.5 dBi during the excitement of a single sector, and with a maximum gain of 5.9 dBi in multi-beam mode.
The authors point out that while ceramic composites have been used to create graded-index (GRIN) materials, that method is not always considered suitable for prototyping purposes. The use of effective-medium theory, adding sub-wavelength airgap intrusions, has also been used with better luck; however, as 3D printing has begun to make its way into the mainstream and offer considerable impacts within nearly every industry from automotive and racing to medicine to aerospace—and with numerous different projects focusing on the fabrication of antennas.
“3D printing also offers the possibility to achieve effective graded-index profiles, where a unit cell volume is only partially filled with the 3D filament, the rest of the volume occupied by air,” stated the researchers. “In such a case, the overall permittivity of the unit cell is lower than that of the 3D filament and by increasing the filling factor of the air gap within the unit cell, 3-dimensional GRIN materials can easily be realized.”
The antenna is meant to change the propagation path, emanating from the source found at the focal point, allowing the front of the electromagnetic wave to align. The GRIN lens was created with a quasi-conformal coordinate transformation, converting the lens onto a flat surface, further modified to lie ‘within a single sector of an octagon.’ The chosen parameters were critical to ensure that the lens was suitably illuminated, as well as offering the best performance level.

(a) Hyperbolic lens. (b) Permittivity map of transformed GRIN lens
overlaid with outline of octagonal sector. (c) Discretized permittivity values of
lens sector. (d) Radiation patterns from original hyperbolic lens, GRIN lens,
and waveguide port on its own
The researchers rotated the GRIN lens segment through 45°. It was copied seven times, allowing the team to create a comprehensive octagonal lens—alternating between beams spanning the whole 360° azimuth plane.

(a) The full octagonal graded dielectric lens with 8 individual segments – the feed points are shown in green. (b) The 2D radiation patterns from each segment at 5.8 GHz.
The octagonal lens featured eight directive beams, with crossover points displayed at a 22.5° offset from the center of each segment.
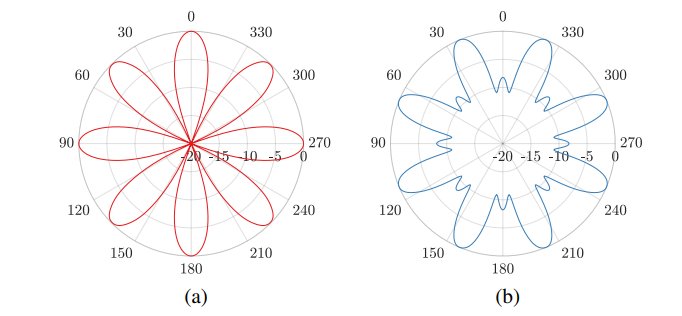
Radiation patterns of the 2D 8-sector lens with multi-port excitation. (a) Anti-phase excitation. (b) Equal-phase excitation.
“One of the drawbacks of phased antenna arrays is achieving the required phase and amplitude weightings required to each of the antenna elements, due to complexity, cost, power consumption and system losses,” explained the researchers. “Here however, the different radiation pattern combinations presented can be achieved through simple switched feeding networks.”
For 3D printing, the research team used a standard white ABS, along with ABS-400—both required to achieve necessary permittivity’s of the discretized lens.
A 3D printed model of an antenna was fabricated via two different printing jobs, with the interior part of the lens made with standard ABS and six different sectors—and the second part made with ABS400.

Full 3D antenna structure. (a) CAD model of 3D lens. (b) Photograph of 3D printed lens prototype with embedded feeding structure positioned on a metallic ground plane.
The GRIN lens was 3D printed on an Original Prusa i3 MK3 3D printer, with SMA connectors soldered to the side in feed point areas.
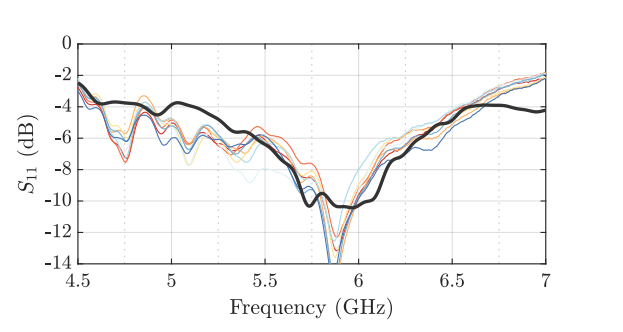
Input response of each of the feeding monopoles of the octagonal GRIN lens. The dark grey line shows the simulated data and coloured lines represent measured data of each port.
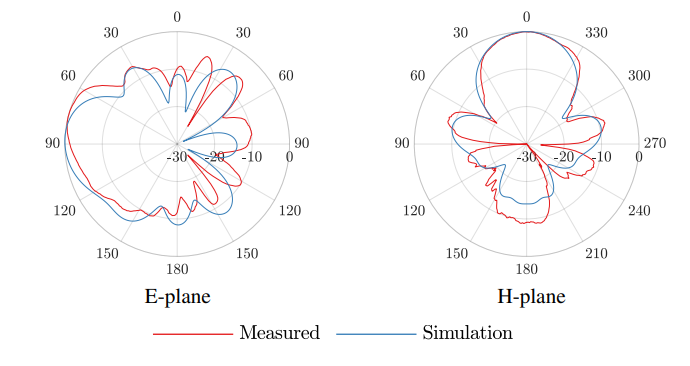
Measured and simulated E and H plane radiation patterns of a single
sector of the octagonal GRIN lens at 5.8 GHz.
“The lens was also able to radiate with an omnidirectional pattern, despite the directive nature of each individual sector,” concluded the researchers.
“The proposed antenna would be suitable for application in a MANET radio to be mounted on a mobile terminal when directive beams are required for interference mitigation and targeted communications.”
What do you think of this news? Let us know your thoughts! Join the discussion of this and other 3D printing topics at 3DPrintBoard.com.
[Source / Images: ‘Multi-Beam Graded Dielectric Lens Antenna from Multi-Material 3D Printing’]
The post Multi-Material 3D Printing for the Dielectric Lens Antenna appeared first on 3DPrint.com | The Voice of 3D Printing / Additive Manufacturing.