3D printing construction today can build more than just walls, structural shells or components. It can build the entire house, as Mighty Buildings has shown, including floors, ceiling, roofs and overhangs. Completed this month, the Mighty Duo B model is a 700-sq-ft ADU with one bedroom, one bath, and a kitchenette. As Slava Solonitsyn, CEO and Cofounder of Mighty Buildings points out,
“As soon as you are able to produce not only the walls but also floor and ceiling, that saves a huge amount of hours, and specifically labor hours, which are very expensive,”.
Additive construction has been increasingly expanding beyond proof-of-concept or research projects, and into commercial applications over the last few years. Increasing urbanization, rising costs of construction, and the need for affordable housing is driving the development of 3D printing applications in real-world construction. In addition, McKinsey reports estimated that California would need 3.5 million homes by 2025, and that improvements in productivity in the global construction industry could add $1.6 trillion (2% of the global economy) to the sector’s value—both areas that construction 3D printing technology is positioned to address.
The company, based out of California, U.S., has received $30 million to date (from Khosla Ventures, Y Combinator, and others), and has just announced its launch out of stealth. Mighty Buildings uses a 20-foot tall 3D printer, the Big-G, which can output at speeds of 120 millimeters per second, to construct a 350-square-foot studio in under 24 hours.
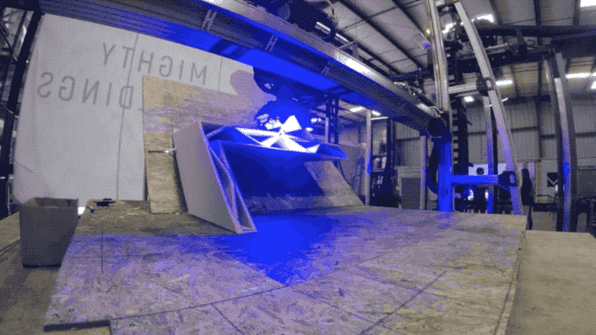
Image Courtesy of Mighty Buildings
The material used is a low-priced Light Stone Material (LSM), a thermal composite that hardens when exposed to UV light. Similar to Corian, a typical kitchen countertop material, LSM “freezes in air” on exposure to the light. While traditional walls are traditionally made from several materials, Mighty Buildings relies on a single material to print a monolithic shell (that improves its insulating properties, thermal and energy efficiency to the highest existing standards) with channels built in for electrical and plumbing requirements.
Chief Sustainability Officer at Mighty Buildings, Sam Ruben explained,
“From a sustainability standpoint, by being able to print the roof and the floors as well as the walls, it allows us to create monolithic shells that increase the airtightness, reduce the thermal leakage, and increase the overall energy efficiency of the structure, making it really easy to meet California zero net energy standards. We can even go past that into Passive House and other standards that are on the cutting edge of what energy efficiency can do.”
Compared to traditional construction methods, Mighty Building’s production platform saves 95% on labor hours, doubles the rate of traditional construction, and produces ten times less waste. The automated 3D printing construction process also automates up to 80% and saves a further 20-30% in costs compared to traditional prefab process, as the machine prints the entire structural shell of the home, as opposed to 3D printing sections for on-site assembly.
Mighty Buildings initially focused on Accessory Dwelling Units (ADUs) or backyard homes, since these were easier to obtain permits for than for empty lot construction. The Mighty Duo B unit took a total of five weeks to complete from construction to installation. The company says it is now ready to scale production having obtained certification and building code compliance for its advanced technology and material solutions. The company was the first to be certified under California’s UL3401 standard for 3D-printed building structures under the state’s Factory Built Housing program.
The offering from Might Buildings also has other advantages, in that their customers do not have to be dependent on multiple subcontractors (for roofing, electrical, HVAC, plumbing and more) with unpredictable schedules for construction. The 3D printing construction company claims its turnkey solution simplifies the process “by being the only entity that you need to work with from start to finish.”
The company has since installed units in San Ramon, and San Diego, and has fifteen more such ADUs under contract. These units can cost up to 45% less than comparable homes built traditionally. Their production as a service platform also allows for custom floor plans for each unit, using optimized software and low-cost printing materials in their design-to-production solution. Unlike concrete, typically used in 3D printed housing, Mighty Building’s material is lighter, has better thermal insulation properties, and can be tailored by robotic arms, in a production system that is 80% automated. The company is expanding its offerings in ADUs with six customizable options available (with the cost of the unit is roughly $314 per square foot) from 350 square foot studios priced from $115,000 to three-bedroom housing priced up to $285,000.
The company is now looking to develop a fiber-reinforced material comparable to steel, that would allow the 3D printing of multi-story, multifamily homes for dense, urban housing. Developers will be the primary customers for Mighty Buildings, as opposed to one-off customers, and the company will look to mass produce affordable, customizable housing from small factories setup in urban markets.
ICON, another company in this emerging sector, is bringing cutting edge 3D printing construction technology in an affordable, accessible way to low-income or homeless populations. Partnering with a non-profit called New Story, ICON is looking to build low-cost houses, the world’s first 3D printed neighborhood, in Mexico for rural populations. The company was the first company to obtain a building permit in the US to construct a 350 square foot 3D printed house in the Austin, Texas. The second version of its 3D printing system, the Vulcan II, can 3D print a 800-square-foot house in 24 hours for less than $4000. In New York, AISpaceFactory, that won the NASA 3D Printed Habitat Challenge expanded on its MARSHA design to build TERA, a Mars-inspired future of home concept house.
Winsun from China has already built multi-storied apartment buildings, and has claimed to build 10 houses in 24 hours, while HuaShang Tengda has created two-storied earthquake resistant buildings, over 4000 square feet, in just 45 days. Apis Cor, a pioneering Russian company in 3D printing construction, built a 400 square foot house in 24 hours that costs just over $10,000 to make. The firm also built the “world’s largest” 3D printed building in Dubai, UAE, a country that has pledged to use 3D printing construction technologies for at least 25% of all buildings made by 2030.
In Europe, Italian firm WASP has built one of the largest concrete 3D printers currently in the market, BigDelta, and has built an ‘ecosustainable’ 323 square foot house, Gaia, made using soil, straw and lime. A few weeks ago, one of Europe’s biggest 3D printers from COBOD (Denmark) was used to build a two-story house, Kamp C, in Antwerp, Belgium which saved at lest sixty percent on project materials, time and costs compared to traditional construction methods. In early July this year, a floating home, named ‘Prvok’ was completed, 3D printed in 22 hours using concrete in the Czech Republic. University of Eindhoven is constructing five, one story and multi-story, 3D printed houses, under Project Milestone, in the Netherlands, which will later be available through real estate agencies for customers to purchase and live in.
The advantages of 3D printing are beginning to be realized in residential and commercial-scale construction. In combination with automation and software, the 3D printing approach fundamentally reduces cost, time and improves efficiency in construction. It can be used to build entire houses now, as well as build components (tiles, slabs, and more) or tools (molds and support structures) in construction. These components and materials, from steel, basalt-based materials and improved concrete to straw and soil, may have better structural properties, improve energy efficiency and sustainability, and can be customized or personalized at the unit level. 3D printed construction can happen on-site or off-site and allows for flexibility in deployment and supply chain. 3D printed houses have already proven to meet certification or compliance requirements, to be earthquake resistant, and may be able to withstand extreme conditions or temperatures.
The post Mighty Buildings’ Commercial House 3D Printing Automates Construction by 80 Percent appeared first on 3DPrint.com | The Voice of 3D Printing / Additive Manufacturing.