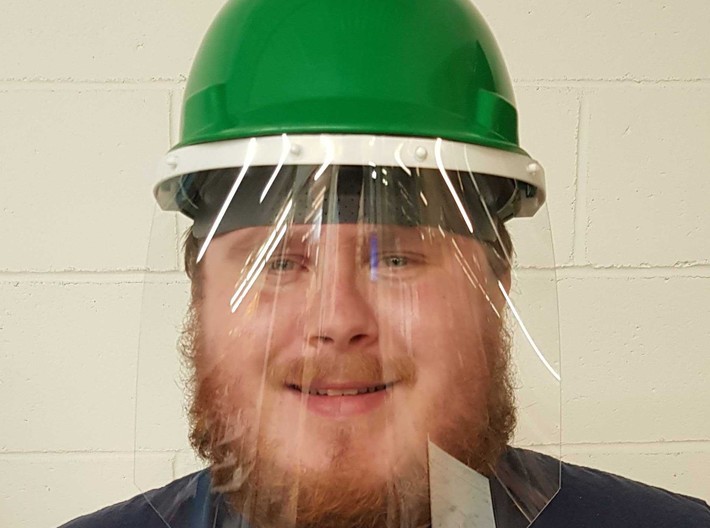
The spread of COVID-19 has led to closures all over the country, but meat and vegetable processing plants have been ordered to remain open and the CDC has made wearing face shields mandatory for plant workers. Since they haven’t had to source these face shields in the past, many don’t know where to turn when their usual PPE suppliers are out of stock. The medical face shields could be made to work in some instances but were not ideal, as plant workers must wear hard hats and the medical shields’ band makes for an uncomfortable and awkward fit. The food production plants then put out a request for a better fitting shield solution that could work with a hard hat or a bump cap. We reached out directly to the plants to supplement this sudden need for more suitable protection in their work environment during a global pandemic.
Hard Hat Shield Design Conception
The hard hat face shield was designed by our Shapeways team that includes Thomas Brown, 3D printing engineer in the SLS department, Kyle Jaworowski, 3D Printing Engineer, and Juan Mercedes, Production Manager.
“The three of us collaborated on the design of the face shield,” said Thomas. “Kyle designed the fasteners to integrate a more comfortable strap to replace the rubber bands that were originally used, while Juan and I focused on material and machine volume usage to optimize the end price.” Using the Shapeways Face Shield v2, a modification of the Prusa RC2 Face Shield developed by Prusa Research, the team modified the previous face shield design to integrate with existing hard hats.
Our team used the MSA VGuard hard hat as the basis for the design because, based on our conversations with plant managers, this is the more universal option in the industry. Using the hard hat has worked out better than a traditional bump cap, because of the ability to clip the face shield frame to the sides of the hard hat.
The Prototypes
We designed and produced the first hard hat shield prototype in two days. We then made adjustments to the measurements to achieve a more uniform fit and to the attachment pegs to keep the visor more securely in place. After no more than three revisions the hard hat shield’s final design was complete.
The Finished Hard Hat Shield
The final iteration consists of a plastic band with protruding pegs for the attachment of a clear visor. The assembled face shield can then be clipped onto the bottom of the hard hat’s brim on the sides. We printed the hard hat shields using SLS plastic for affordability and versatility. The entire designing, prototyping, and printing process took two weeks.
Available for On-Demand Orders
These hard hat shields are made to suit the unexpected and immediate needs of essential plant workers during the COVID-19 pandemic. The hard hat shields can be printed as needed and fulfill a more functional alternative to typical face masks in the food production environment. 3D printing offers immediate solutions to urgent needs for PPE during the COVID-19 crisis and can fulfill that need until the regular sources are able to provide the necessary supplies again.
These hard hat shields can be used as additional protection for workers in any environment where hard hats are worn. To place an order for these face shields please contact our Shapeways sales team directly at bizdev@shapeways.com.
The post Solving An Urgent Need: Shapeways Produces Hard Hat Shields for Plant Workers appeared first on Shapeways Blog.