Researchers are mixing up the macro- and the micro- in their latest study, designed to expand the limits of 3D printing with glass. In ‘Three-dimensional laser printing of macroscale glass objects at a micro-scale resolution,’ the authors explain how they created macro-scale 3D objects in glass at a micro-scale resolution—hoping for success which has so far never been attained in two decades of research and effort in femtosecond laser induced chemical etching (FLICE).
The researchers were able to 3D print macro-scale glass objects at heights up to ~3.8 cm with a well-balanced (i.e., lateral vs longitudinal) spatial resolution of ~20 μm:
“The remarkable accomplishment is achieved by revealing an unexplored regime in the interaction of ultrafast laser pulses with fused silica which results in aberration free focusing of the laser pulses deeply inside fused silica,” state the researchers.
They began by ‘loosely focusing’ laser pulses into the silica, etching multiple lines organized into two different grids for both X and Y directions.

The fabrication resolution offered by loosely focusing the picosecond laser pulses into fused
silica. (a) Schematic illustration of inscribing lines within a cube of fused silica along X and Y
direction. Cross-sectional optical micrographs of the lines written along (b) Y and (c) X directions.
(d) Cross-sectional micrographs of the hollow channels produced by chemically etching the
inscribed sample in the last column of (c). Scale bar: 25 m.
The research team noted that their cross section of lines showed an almost completely circular shape. The lines were insensitive to all the following: scan speed, focal position depth, laser writing direction.
“The difference is that with an increasing scan speed, the color in the cross section captured under the microscope in a reflective mode becomes lighter, indicating that a weaker modification of fused silica will be generated with the decrease of the irradiation dose at the increasing scan speed,” explained the authors.
After eliminating nanogratings in the fused silica, they could 3D print with worrying about polarizing the writing laser beam ‘in real time.’ The authors states that this allowed them to simply beam steering in the printing system, making the entire process easier and ‘more robust.’
In the images below, you can get a better understanding of the successes in their work as the authors created the Einstein head with all his ‘fine features’ visible—even the eyelids.
“It proves that the entire sculpture is printed with a decent fabrication resolution from top to the bottom,” said the authors.
The statue of Confucius is extremely detailed also, with an impressively smooth appearance, although this could be further improved with post annealing or laser polishing.
The air turbine includes moveable parts that were printed in the glass, eliminating any need for assembly, and illustrated below.

A laser printed sculpture of Albert Einstein’s head in fused silica. (a) The model and the (b)
front, (c) right, (d) back, and (e) left sides of the sculpture. (f) and (g) are the zoom-in images of (b)
and (e), respectively, to highlight the fine details on the face. Scale bar: 5 mm.
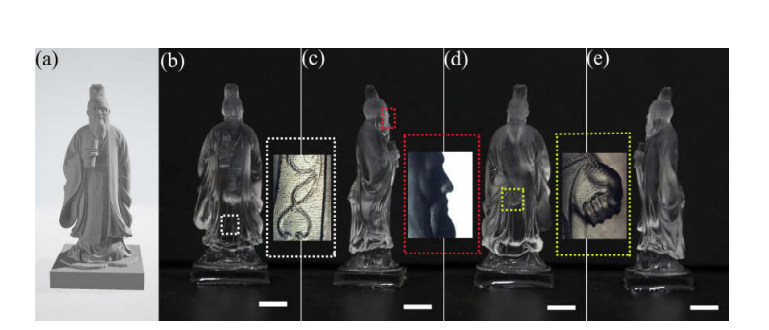
A laser printed sculpture of Confucius in fused silica. (a) The model and the (b) front, (c) left,
(d) back, and (e) right sides of the sculpture. The details of the decorative pattern on the cloth, the
right side of his face, and the left hand hanging behind his body are shown in the insets on the righthand side of the images in (b), (c) and (d), respectively. Scale bar: 5 mm

A laser printed air turbine in fused silica. (a) The whole air turbine model. Inlet and outlet for
air injection are indicated. (b) The interior of the turbine including turbine fan, a driving gear (G3)
and two driven gears (G1 and G2). Each of G1 and G2 is connected with a cam. (c) Digital-camera
captured image of the fabricated turbine. The air direction and the rotation direction of the fan, as
well as the rotation directions of G1, G2 and G3 from a top view are all indicated by the curved
arrows in (c). (d) The initial position of the two cams is pointing to the left as indicated by the two
arrows. (e) Both the cams are rotated in a clockwise direction by 90 as a result of the injected air flow. Scale bar: 5 mm.
“Further improvement on the printing efficiency will be done in the near future by combining a 2D galvo scanner with the 2D motion stage. This design will allow both a high printing speed and a large printing area. The novel 3D glass printing technique is established based on two unconventional characteristics in the interaction of loosely focused picosecond laser pulses with fused silica, namely, the depth-independent aberration-free focusing and the elimination of the self-organized nanograting,” concluded the researchers.
“The physical mechanisms behind these interesting effects have not yet been clarified. We stress that the interaction of ultrafast laser pulses with transparent media under the loose focusing condition is a largely unexplored area of research, which shall inspire significant interest for further investigations. The high-resolution 3D printing of macro-scale objects in glass is expected to have implications in the fields of photonics, microfluidics, and high-precision mechanics.”
The great thing about 3D printing and all the accompanying techniques requiring infinite choices in hardware, software, and materials is that there is always something new to try—and there is always lots to talk about, whether you are a researcher, student, designer, engineer, or one of the many other types of users enthusiastic about 3D design and printing. Fabrication with glass is garnering growing interest, from experimentation with works of art, to metallic glass, to carbohydrate glass. Those are just a few examples, with macro-scale objects taking such studies to a new level of complexity.
What do you think of this news? Let us know your thoughts! Join the discussion of this and other 3D printing topics at 3DPrintBoard.com.
[Source / Images: Three-dimensional laser printing of macroscale glass objects at a micro-scale resolution]