In ‘Innovative Modeling Techniques and 3D Printing in Patients with Left Ventricular Assist Devices: A Bridge from Bench to Clinical Practice,’ US researchers examine new techniques for better monitoring of left ventricular assist devices (LVAD) and troubleshooting alarms. The need is there due to altered flow dynamics caused by LVADs, which have been a developing technology for the last 30 years.
The authors examine new development methods that are not yet in use clinically but may have significant bearing in the future as they are able to improve treatment of cardiac patients who may have low cardiac output or even be in end-stage heart failure. As LVADs offer a ‘bridge’ to transplants or further therapy, some models may cause issues such as:
- High thrombosis
- Valve failure rates
- Flow augmentation
- Bleeding complications
- Stroke
Even with superior design, issues may arise due to how the LVAD is placed in the body. Here, the researchers look further into techniques predicting LVAD flow. Not only can these techniques lead to better troubleshooting, but also better surgical planning, often with the help of 3D printed guides.
Computational fluid dynamics are used to create LVAD prototypes as well as test them:
“Prior to running a computer simulation, the accurate 3D geometry of the object needs to be defined, usually from cardiac CT or 3D echocardiography,” state the researchers. “The physical characteristics of the fluid, in this case blood, and the surrounding boundaries are defined. In these computer simulations, blood is assumed to act as an ideal fluid.”
“The quantity of blood flow through the ‘inlet’ (the left ventricle) and the ‘outlet’ (the aorta) can be derived from cardiac catheterization or echocardiography. These geometric and boundary conditions are inputs to a computer simulation that essentially functions as a virtual flow lab. The information can then be used to generate information on shear stress, heat dissipation, and wall pressure. Models for hemolysis and platelet activation can also be generated to test a device for hemocompatibility.”
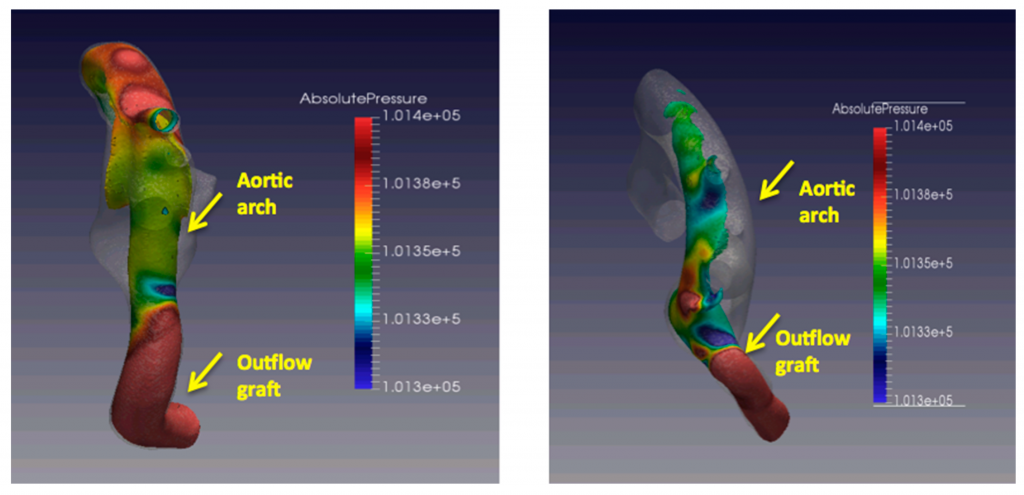
CFD simulations with varying outflow cannula angles relative to the aortic arch and variations in absolute pressure (in Pascals) and distribution on the aortic arch and great vessels.
Fluid structure interaction (FSI) allows researchers to examine fluid flow around a ‘deformable structure,’ with CFD simulations allowing assessment of the following hemodynamic parameters:
- Pressure
- Velocity
- Wall shear stress
- Displacement
Simulations allow researchers to observe disturbed flow, which may be in connection to issues with atherosclerosis and thrombogenesis. The authors point out that most CFD studies are deficient in the specific patient geometry required, along with long-term outcomes.
“CFD can prove to be a useful technique that could potentially be used clinically for LVAD implant planning, surveillance and troubleshooting of complications of patient with LVAD,” state the researchers. “Assessment of adverse fluid characteristics in relation to adverse long-term clinical outcomes may provide important insight into surgical implant techniques.”
In particle image velocimetry (PIV), researchers look at rapid sequential imaging for computing velocity vectors as well as fluid dynamics. PIV modeling involves setting up:
- A transparent phantom organ
- Laser
- Camera
- Seeding particles
- Image processing software
The authors see potential for PIV in understanding LVAD placement and fluid dynamics.
3D printed models are also being used now so that researchers can understand more about heart disease. They may be helpful in surgical planning, as well helping in the placement of ventricular assist devices (VADs). Heart models have also helped with virtual implantations, along with VADS in children too. The researchers point out that 3D printed heart models do improve anatomical positioning and surgical techniques, they are inferior to continuous flow pump simulation. They recommend better simulation models with either CFD or PIV modeling.
“As 3D printing technology evolves, there is hope to develop patient-specific models that replicate the anatomic and physiological features to be used in LVAD surgical planning,” conclude the researchers.
“In the long run, improved fluid dynamics may help improve implant techniques and lessen the burden of significant adverse events.”

An example of a flow circulatory flow loop with LVAD connected to compliance chambers and flow meters
Because there are so many heart conditions affecting so many around the world—and they can be deadly—researchers are constantly looking for better ways to treat patients. With 3D printed models and devices, patient-specific care is much more accessible, meaning that medical professionals have an easier time diagnosing heart conditions, treating them, and explaining what is going on to not only patients, but their families too. Medical students also have much more expanded training mechanisms with advanced 3D printed heart models and surgical guides.
[Source / Images: Innovative Modeling Techniques and 3D Printing in Patients with Left Ventricular Assist Devices: A Bridge from Bench to Clinical Practice]