Orthopedic implant device maker Exactech wants to scale up the production of its Equinoxe Stemless Shoulder implant by switching from electron beam metal additive manufacturing to direct metal 3D printing with high precision lasers. In an official statement released on July 21, 2020, the Florida-based company announced plans to transition all US stemless shoulder procedures to its laser-printed devices throughout the rest of the year.
As the latest addition to the company’s extremities product line, the Stemless Shoulder, launched in 2018, is a bone conserving prosthesis designed for anatomic total shoulder arthroplasty. Comprised of a stemless cage, humeral head, and cage glenoid, the device offers intraoperative flexibility which is ideal for conserving the bone, said the company. Furthermore, to enhance the probability of biological fixation, it incorporated a laser 3D printed porous bone cage structure that allows bone-through growth, and without the need for a stem, there is more ease of implantation, reduced operating time, and blood loss. Exactech indicated that the innovative combination of 3D porous material and bone cage technology is what differentiates it from competing products on the market.
Currently, there is a growing trend towards minimally invasive orthopedic surgeries, like stemless shoulder implant procedures mainly led by experts in Germany and France. However, US surgeons also took notice of the benefits of using stemless implants to perform arthroplasties with less bone removal and fewer complications than more conventional anatomic shoulder prosthesis.
Driven by an upsurge in the aging population, longer life expectancy, and rising prevalence of arthritis, the global shoulder arthroplasty market is expected to reach $2.4 billion by 2023, and that includes increased demand for stemless shoulder implants, as forecasted by Koncept Analytics last year. In the US alone, over 53,000 people have shoulder replacement surgery each year, according to the Agency for Healthcare Research and Quality, and with only a handful of stemless shoulder implants cleared by the US Food and Drug Administration (FDA) since 2015 (including the Equinoxe Stemless Shoulder), there is a wide-open market opportunity for medical device manufacturers to exploit. Expecting to become a leading force in the stemless implant market, Exactech is switching technologies to deliver quick solutions for patients and surgeons.
“We have been incredibly pleased with our original EBM [electron beam melting] Stemless Shoulder implant and the early positive clinical feedback we received from our surgeon customers. The new laser-printed device is built on this solid foundation while also giving us the ability to ramp up production to serve even more patients, which drives us and fulfills our mission,” said Exactech Vice President of Extremities, Chris Roche.
Orthopedic surgeons Curtis Noel, of the Crystal Clinic in Akron, Ohio, and Stephanie Muh, of the Henry Ford Health System in Detroit, Michigan, were the first shoulder specialists to perform the surgeries with the Equinoxe Stemless Shoulder implant earlier this month. As a member of the design team, Noel expressed how proud he was to be one of the first to implant the laser-printed Stemless Shoulder, mainly due to the bone conserving design, along with its compatibility to the Equinoxe Shoulder Platform System.

Laser 3D printed porous structure designed to promote bone-through growth (Image courtesy of Exactech)
Muh described that “one of my favorite features of the Stemless implant is its bone cage structure that is designed to provide initial press-fit fixation while also allowing for bone-through growth. That intentional design element, along with the porous structure being designed to mimic the trabecular nature of cancellous bone, differentiates it from competitors.”
In order to design the Stemless Shoulder implant, Exactech engineering researchers collaborated with orthopedic surgeons that combined their knowledge, expertise, and background to come up with a final design structure that could be additively manufactured with optimized pore size, porosity, and count. The design team included Noel; shoulder and elbow surgery expert’s Felix Henry Savoie, from Tulane University, and Joseph Zuckerman from New York University (NYU)’s Langone Orthopaedic Hospital; Pierre-Henri Flurin, from the Clinique du Sport in Bordeaux-Mérignac, in France; Ryan Simovitch, the Director of the Shoulder Division at the Hospital for Special Surgery (HSS) in West Palm Beach, Florida, and Thomas Wright, Director of Interdisciplinary Center for Musculoskeletal Training at the University of Florida.
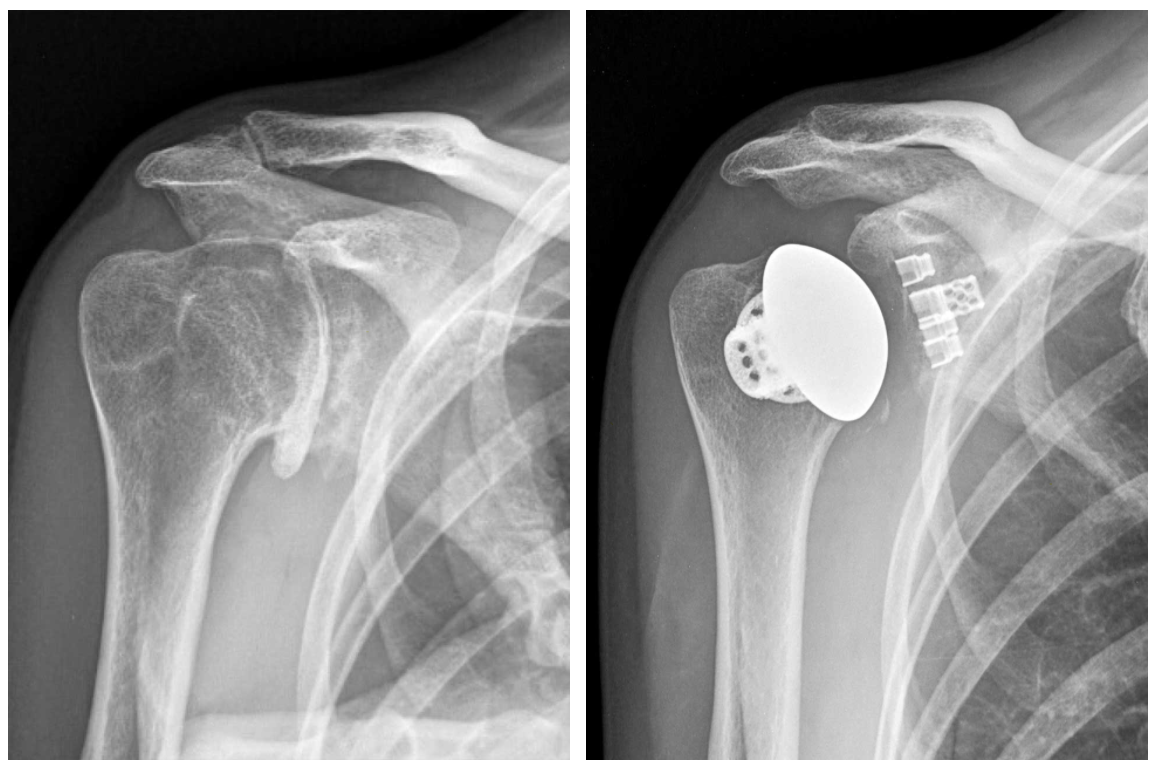
Pre-operative X-ray (left) and postoperative X-ray (right) showing the laser-printed Stemless Shoulder and Equinoxe Cage Glenoid. (Image courtesy of Stephanie Muh)
As a developer, and producer of innovative implants, instrumentation, and computer-assisted technologies for joint replacement surgery, Exactech targeted clinical evaluations of the Stemless Shoulder immediately after release and has been aggressively expanding and upgrading its product ever since. Just like other manufacturers of stemless implants, the goal here is to try to reproduce the native shoulder anatomy and minimize humeral bone removal. Recent studies. have outlined the numerous advantages – as well as a few disadvantages – of stemless shoulder implant arthroplasty, and although its use is still emerging outside of Europe, the implant is gaining ground with surgeons and patients and is expected to surpass stemmed implants by 2025.
The post Exactech Transitions from EBM to Laser 3D Printing Implants for Shoulders appeared first on 3DPrint.com | The Voice of 3D Printing / Additive Manufacturing.