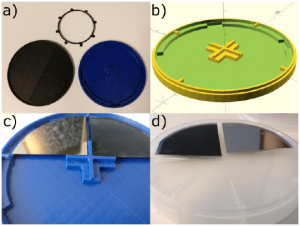
a) Wafer box for four 100 mm wafer quarters 3-D printed out of PLA including top (black), bottom (blue) and holder (black ring). b) Open SCAD model of the customizable single wafer box. c) Wafer quarters stored securely in the 3-D printed box. d) Wafer quarters free to move in a commercial single wafer box.
3D printing has been used by scientists to save money on lab equipment, which is typically quite expensive. Things get a bit complicated, however, when it comes to equipment that is used in clean rooms. There are strict limitations on the types of materials and items that are allowed in cleanrooms, so a good deal of study and experimentation must be done before clearing a new item or material for use. That is the purpose of a study entitled “Compatibility of 3-D Printed Devices in Cleanroom Environments for Semiconductor Processing.”
“As the dimensions of typical semiconductor devices are in the micrometer range, it is essential to fabricate those components in an environment, where the level of contaminants (e.g. dust particles and organic compounds) is accurately controlled,” the researchers explain. “In cleanrooms, the level of contamination is specified by the number of particles per cubic meter at specified particle sizes by the international ISO (the International Organization for Standardization) standards.”
To meet these requirements, air flowing into the cleanroom is filtered and recirculated through HEPA filters, and operators wear protective clothing. Limitations are set on the materials that can be used to make cleanroom equipment and tools, such as wafer boxes and tweezers, since they are only allowed to generate a minimal amount of particles.
“The use of FFF-based 3-D printing in the cleanroom is limited because of the particles generated during fabrication itself, which depend on numerous factors including filament type, filament color, printing parameters and printer design,” the researchers continue.
The study takes a look at the possibility of using 3D printing for some of the least strenuous applications in the cleanroom environment – those that do not require chemical compatibility. The researchers used two objects – a custom single wafer storage box and a wafer positioner for a metrology system – and tested three 3D printing materials: ABS, PLA and PP, 3D printing them on a LulzBot TAZ 6 3D printer.
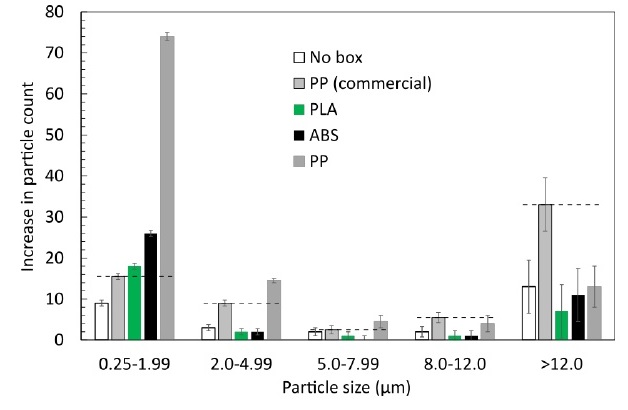
Increase in particle count during 15 days storage in various single wafer boxes. The initial number of particles on all wafers were in the order of 10-20. The dashed lines indicate reference levels set by the commercial PP box, which is commonly used in cleanroom environments. The error bars are determined from the variation in several repeated measurements.
The results of the study show that single wafer boxes 3D printed from PLA and ABS generate as few particles as a commercial equivalent, while slightly more particles were found in the PP box.
“The 3-D wafer positioner seems to cause a negligible particle increase on the manipulated wafer, while abrasion of the mechanical parts generate larger numbers of particles that may disperse in the environment,” the researchers state. “Regular cleaning of those parts is thus recommended, and applicability in a cleanroom environment will depend on the cleanliness constraints.”
Elemental analysis showed that 3D printed objects contained no harmful metal impurities, other than those resulting from colorants, so the researchers recommend that only natural-colored filament be used, especially in applications where metal contamination could be an issue, such as in semiconductor processing.

a) Parts of the positioner modelled in the OpenSCAD software. b) 3-D printed and assembled positioner.
The filaments studied also showed themselves to be resistant to isopropanol and deionized water, which are used for the cleaning of objects in cleanrooms. The researchers conclude that 3D printing is a safe method of creating objects for use in cleanrooms, enabling scientists to take advantage of the cost savings that the technology offers.
Authors of the paper include T.P. Pasanen, G. von Gastrow, I.T.S. Heikkinen, V. Vähänissi, H. Savin and J.M. Pearce.
Discuss this and other 3D printing topics at 3DPrintBoard.com or share your thoughts below.