What started out as an exploration into the flexible properties of different materials soon became a revolutionary product for Boston-based industrial designer Evan Gant. His design, the Twist Light, is a pendant light that transforms to adjust the brightness with a simple twist. At the start of his design process, Gant was making prototypes simply out of paper towel rolls. Then, seeing the product’s potential, he moved into using 3D printing to prototype the Twist Light.
“I started out trying to find a way to get some of my ideas out of my sketchbook and into a physical form,” Gant told Shapeways. “My first project was a printed ring for my wife as an anniversary present. Then I made a few items to use around the house before I decided to start selling some of my projects.”
From Paper Towel Rolls to 3D Printing
While using paper towel rolls was of help in the very beginning stages of the design process, Gant has now seen the many benefits to prototyping with 3D printing. In fact, he notes that using companies like Shapeways over traditional manufacturing methods — like injection molding — has proved to have many more benefits than expected.
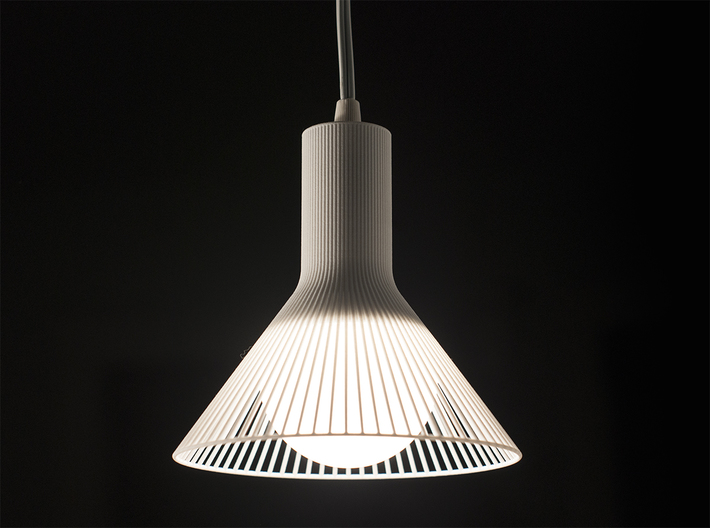
Array by OliveBird
“It gives me an opportunity to try ideas out and get them in people’s hands rather than committing to a larger scale production. I also love that I can test out people’s interest in an idea and see what feedback I get from selling/sharing the ideas. It is very easy to make changes, or even scrap the idea and move on without feeling like I am too invested. My favorite part of the design process is iterating and seeing the reaction to ideas. In a traditional process (like injection molding), a large portion of your time is spent optimizing from a mold, finding a vender that will make you parts, doing quality control, etc. You often need to make a lot of compromises to your design in the end.”
Choosing 3D Printing Over Desktop Printing
On the flip side, Gant notes the benefits of using Shapeways over other 3D printing methods like desktop printing, saying, “I love having access to the variety of printing methods. I can switch between materials, colors build volumes, etc. If I had a home machine, I would have to stock the materials, maintain the machine and probably deal with a small build volume, or have a very expensive machine. Also, most of the affordable home machines are FDM, which is a great process but has limitations in terms of surface finish and level of detail.”
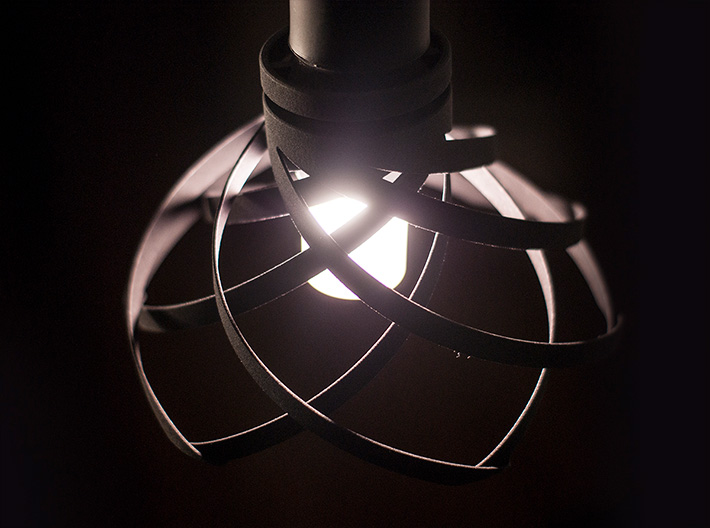
Twist by OliveBird
The Twist Light is now in its 4th iteration and only getting better. Gant explains the constant need for it to be dimensionally accurate, as well as for it to have good aesthetics.
“Given that I would like to sell the ideas with no secondary finishes, I need the parts to look good when they come out of the printer, which is why I really like the durable and flexible plastics. It is cleaner than an FDM while being flexible and durable (obviously), and the cost per square inch is reasonable.”
As he moves forward with his product, Gant is excited to see it come to fruition. He applauds Shapeways for our customer service and low costs, among other benefits.
“I think that Shapeways is a very customer friendly service, easy to understand the costs and build limitations. The best part for me is the ease of which I can turn ideas around into something I can sell, which I can use to fund my next project. I have appreciated Shapeways sharing my projects in the past and driving more sales.”
Interested in 3D Printing for Your Business?
Interested in manufacturing with 3D printing? Contact us to learn about all the ways Shapeways can aid your business.
The post Twist Light Reinvents the Lighting Industry appeared first on Shapeways Magazine.