Dr. Albert Woo is the Chief of Pediatric Plastic Surgery and Director of the Cleft and Craniofacial Center at Hasbro Children’s Hospital and also an Associate Professor of Surgery, Pediatrics & Neurosurgery at
The Warren Alpert Medical School of Brown University. Albert has done extensive work in
CMF (cranio maxillofacial) and pediatric surgery including a lot of research and significant experience in things such as
Endoscopic Craniosynostosis Surgery and ocular facial surgery. Additionally, he is the Director of the Lifespan 3D Printing Lab. Albert has for a number of years now played a pioneering role in bringing 3D printing into hospitals and in using 3D printing for surgery. The current trend in 3D printing labs in hospitals has partially pioneered by Albert at St. Louis and now at Lifespan. I found it hugely inspirational to meet Albert at
Additive Manufacturing Strategies in Boston. I’d met good Doctors working with 3D printing and good engineers who were trying to get 3D printing into medicine but here was someone who bridges the gap in understanding our technology and how it can be applied. We interviewed him to see how hospitals and surgeons can harness 3D printing today?

Why as a surgeon are you excited about 3D printing?
3D printing is extremely exciting to me because it represents the future of medicine. Particularly in my profession as a plastic surgeon specializing in craniofacial abnormalities, it is well understood that every individual is different and that every face is unique. In that regard, it seems unreasonable to think that while everyone is different, we can still perform the exact same operation on each individual. The promise of 3D printing is that it can help us to understand the nuances that are particular to each person and to design or alter surgical procedures to best fit each person’s needs.
Beyond this, the use of surgical guides and computer designed implants help us as surgeons to provide consistency and accuracy in our operations. Generally, all patients want their doctors to “be experienced”. Why? Because they are hoping for the best possible result, and the idea of experience is a surrogate for accuracy and predictability. One of the advantages of 3D printing is that it can provide an inexperienced surgeon with the tools to plan a procedure down to the millimeter in accuracy — in essence, helping that physician get comparable results to that of a master with decades of experience. Wouldn’t you want your doctor to have this technology available if it could potentially improve your surgical results?
What is holding back 3D printing in surgery?
Every technology has hurdles to adoption. In general, medical 3D printing is largely in its infancy. Most physicians have no idea about this technology to begin with, have no access to 3D printing, and are inherently wary to adopting new, “unproven” or “unconventional” ideas. Many have been doing things the same way for decades and see no need to change. Indeed, when frustrated with hiccups in a procedure, angry surgeons will often yell out, “We do it the same way every time!” 3D Printing threatens change and not everyone likes change.
Beyond this, based on my experience with the additive manufacturing industry, it seems clear that communication barriers exist. 3D printing companies are very used to speaking the language of manufacturers but do not know how to speak to clinicians. Similarly, engineers designing materials do not have a great idea of the challenges facing those performing procedures on patients.
Finally, smooth workflows have yet to be ironed out. You can’t just buy a printer today and start printing medical models or implants in 30 minutes. The printers require specialty software provided by separate companies which frequently do not work with the original vendors. Moreover, there is a dearth of trained professionals to create medical models (and even training opportunities if you want to learn). How many of us feel comfortable building a computer from scratch and purchasing all the parts and software separately? This is where we are in the field now, prior to the advent of companies like Dell which put everything together for us. These issues will need to be ironed out before Medical 3D Printing becomes mainstream.
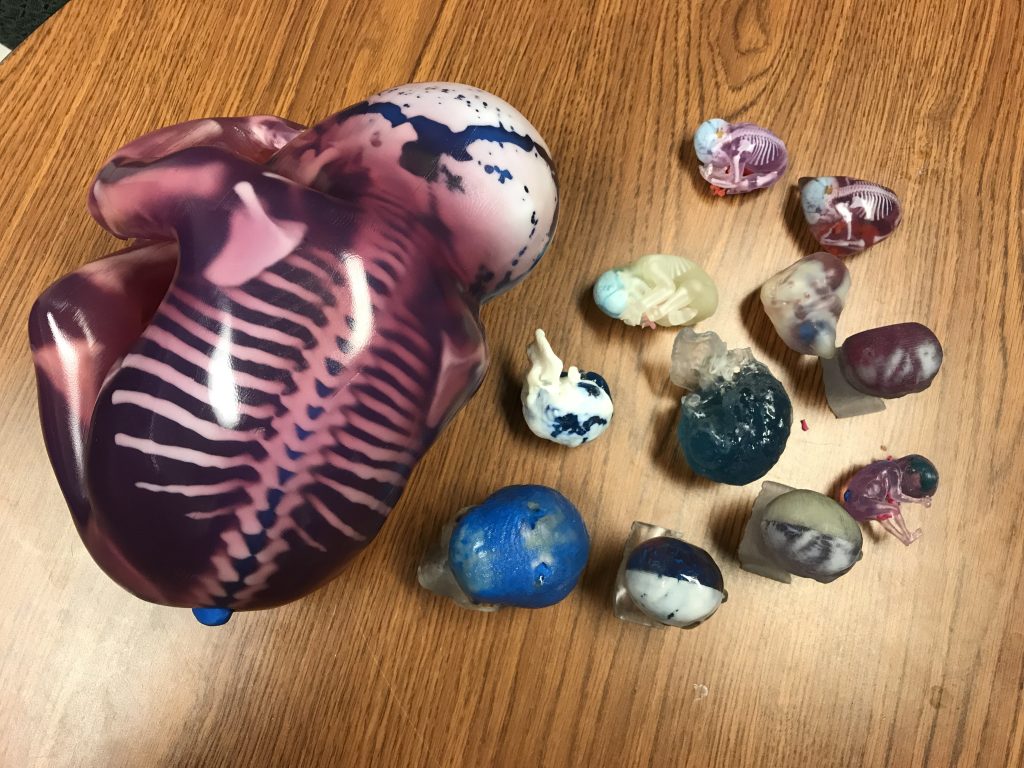
Do you see patient specific procedures as having a bright future or will their applications be more limited?
Eventually, I predict that virtually all procedures will become patient specific. It is only a matter of time as technologies become faster and more ubiquitous. Certainly, today, there are some fields that will require more patient specificity early while others may be delayed in adoption. My field of craniomaxillofacial reconstruction, for instance, is highly specific to each person. This can also be said for pediatric heart abnormalities, each of which are highly variable with very little room for error. On the other hand, hip surgery may be less focused on patient specificity since there is arguably a larger room for error in most of those cases.
What 3D printing materials are would you like to see developed?
Currently, too many 3D printing companies have their own proprietary materials which are the only ones available on some of their high end printers. Unfortunately, proprietary information, while lucrative to individual companies, can limit the growth of the field in general.
We need more work on materials that are FDA approved for use in the body. Silicone is an obvious choice as we have decades of experience implanting this in human beings. A huge number of implants currently incorporate silicone as a component (including artificial joints, facial implants/prostheses and even breast implants used not only for augmentation but to help reconstruct women after breast cancer surgery), allowing for easier adoption versus other proprietary materials.
A 3D printed artificial bone substitute would also be a great material to have. Ideally, we would want materials that would get incorporated into the human body, with tissue in-growth, rather than metals or plastics that are separate. Such “non-autogenous” materials have higher chances of infection and failure than living human tissue. Further, the body has an incredible ability to heal itself. On the other hand, a metal implant has a limited shelf life before it is expected to fail. This is why many people are so excited about the field of bioprinting and regenerative medicine.
How do 3D printed surgical models help you?
I use 3D models for multiple purposes. Anatomical models help us to understand complex 3D geometry far better than anything we can see on the screen. The surgeon is then able to use many more senses to get an intuitive understanding of complex spatial relationships. We can also cut the models and practice our surgeries or use the models to custom design or fit patient-specific implants or prostheses.
These models are also sometimes critical to help patients and their families understand what is going on so that they can make informed medical decisions. Moreover, 3D models have incredible potential for medical education. Sometimes, unique deformities present only once in many years. Obviously, medical students and trainees will not be the ones doing those operations. But imagine if they could – on a model. Wouldn’t that be worth it to train the next generation of doctors?
We often say that a 2D picture is worth a thousand words. If so, how much is a 3D model worth? There is little wonder why virtually every conjoint twin separation and face transplant surgery performed in the last decade has utilized 3D printing in some manner to help with the procedure.
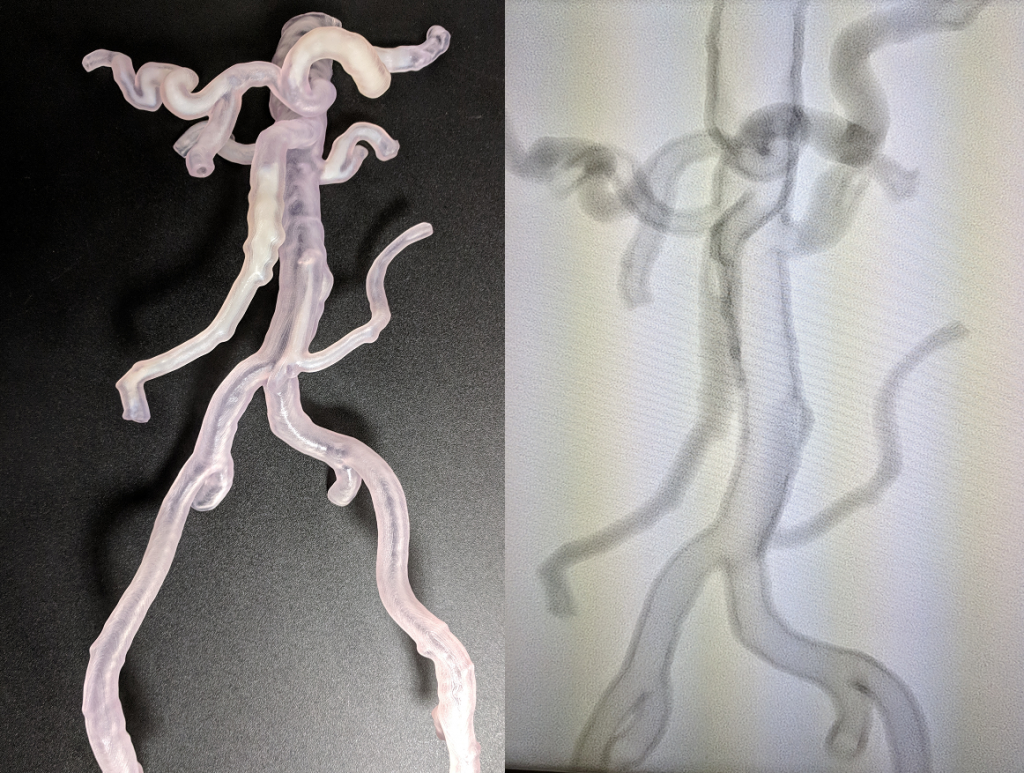
This is going to sound crazy but seriously, let’s arm surgeons with 3D printing pens? They’re really good at cutting things away how about letting them add material to patients?
This is certainly worth a discussion. To be honest, I would say that we are still a ways out from this just yet. But I’d be happy to chat further about it with people who see the value of it.
We’ve seen comparatively little work on custom post-operative braces and things like that?
Yes, this is largely due to cost and materials. While there has been huge interest and advancements in 3D printed “robotic” hands, notably less work has been done with lower extremity prostheses. This is because of the extreme load that artificial legs put onto the 3D printed structures. While standard consumer FDM materials can handle the load on a hand, they cannot provide reasonable support for legs. As a result, the pool of those with the resources to help in this arena is dramatically smaller. This will likely not improve until accessibility to metal printers or higher grade materials has been democratized.
We also see few developments in 3D printed surgical tools. For many kinds it wouldn’t make sense but would you see a need for more custom surgical tools?
It is funny that you mention this as I have worked with industry to help develop some of these tools. One of my projects is a custom bone bending instrument and multiple iterations were printed on an FDM machine before a functional instrument was created out of stainless steel. Unfortunately, there is little market for creation of speciality tools as these instruments do not make companies money. You buy one tool and have it for a decade. Implants, however, are put in every single day. As a result, many companies do not see a great ROI on development of specialty tools and only do so if they feel that it is critical to keeping their current business of selling the implants themselves.
How do we best educate hospitals on what 3D printing can and can not do?
This is an interesting question. I would suggest that it is critical for 3D printing companies to get physicians who actually perform the procedures involved. I have seen numerous efforts fail when companies have not done this as there is frequently no one to translate the world of 3D printing into the medical environment. On the flip side, physicians are notoriously wary of speaking to company reps or salespeople. Personally, I equate them somewhere on the level of used car salesmen. No one can understand the unique hospital environment and the challenges facing surgeons than another surgeon. As a result, I would posit that physician champions will be critical to the further adoption of 3D printing in medicine.
If I’m a doctor and want to learn how to use 3D printing in my practice where and how can I learn about this?
Ahh, there’s the rub. This can be an exceedingly difficult and frustrating endeavor. While extensive resources exist for companies and individuals who have the wherewithal to invest tens of thousands of dollars a year in custom software licenses, few options are available for an enthusiast or those who simply want to learn more with limited resources. Thankfully, one standout software package is 3D Slicer, a free and open-source platform for analyzing medical image data developed in part through funding from the National Institutes of Health (NIH). Training is also extremely difficult to come by. Regarding development of 3D printing programs, the best I can suggest would be to contact those who have successfully done so to ask for advice. Unfortunately, the activation energy to do this remains fairly high.