Soace manufacturing start-up Tethers Unlimited has had a tumultuous time of late. The firm which aims to develop in space manufacturing technologies and has successfully seen its Refabricator put in use on board the ISS space station now. The recycler has been installed and is now being put to use by astronaut Anne McClaine. At the same time, Tethers has had to lay off a fifth of its staff due to cash flow problems stemming from the government shutdown in the US.
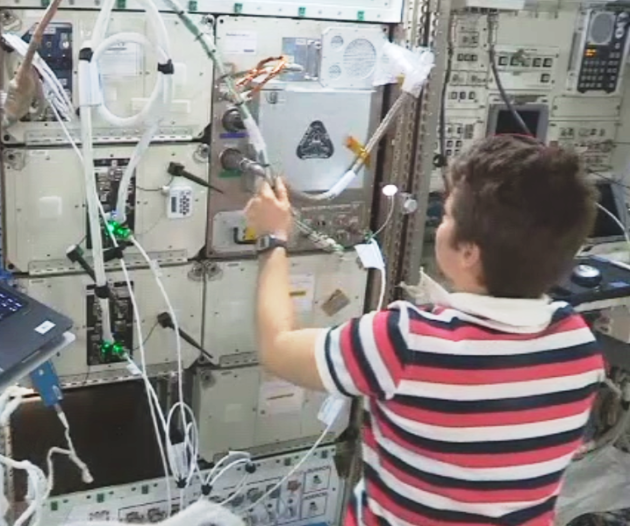
Astronaut Anne McClain installing the Tethers unlimited FDM 3D printer and recycling unit on board the ISS. She appears to be wearing a rugby shirt which would be fitting since she participated in the rugby world cup as well as being a helicopter pilot with 216 missions in Iraq, engineer, a mom and an aerospace engineer.
Tethers as a firm has always been a bit of a wild ride. The company started in 1994 looking to commercialize space tethers. Tethers in space are long (tensile) cables that can be tied to satellites and other space vehicles. Long dreamt about rarely used successfully the idea is that a long tether tied to a satellite could be used for propulsion or power generation in space. An Electrodynamic tether, for example, conducts and by passing through a planet’s magnetic field. This kind of tether can use the Lorentz force (electromagnetic force) of an electrified tether against the magnetic field of a planet to push the spacecraft into a new orbit. This would save on fuel and perhaps let craft slingshot around planets more efficiently. Momentum exchange tethers may actually let the spacecraft slingshot itself into space through spinning. A bolo of a tether tied to a craft may be used to spin and propel other craft onward in their journey.
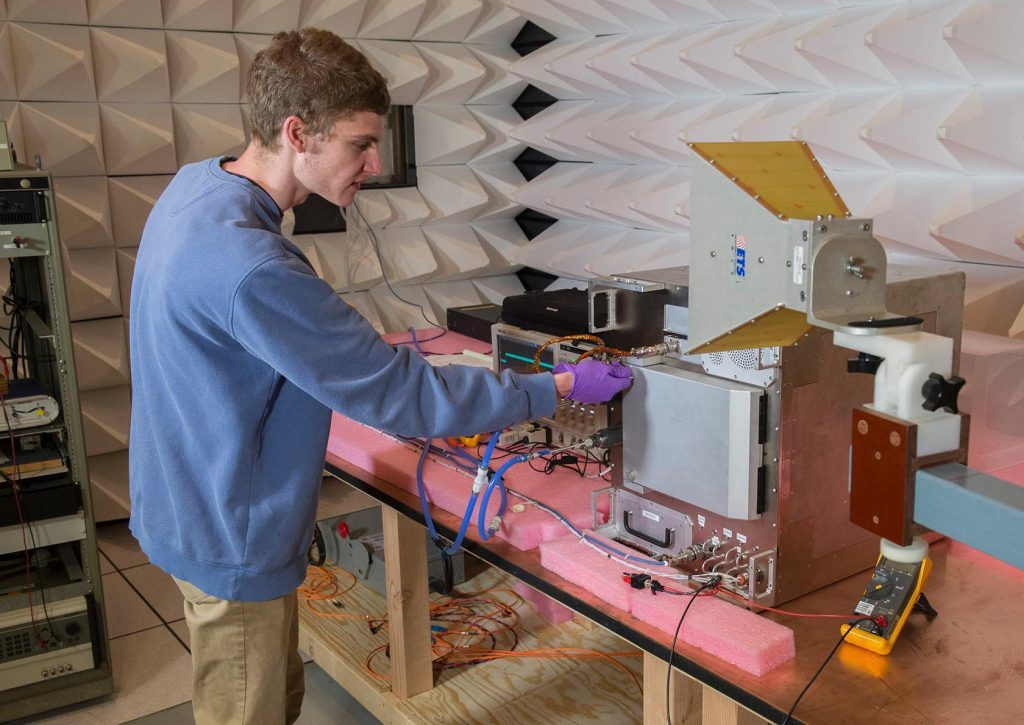
Marko Baricevic of Tethers Unlimited testing the Refabricator
Skyhooks would do the same but at much higher speeds. A space elevator is a tether tied to a craft in geosynchronous orbit above 35,000 KM in altitude which could be used to life payloads potentially inexpensively (once you build the most expensive thing ever which is also the biggest thing ever and also would need advances in material science to even be remotely feasible). Meanwhile, several 20 kilometer long tethers could together form an electric solar wind sail propelled by an electron gun shooting at these tethers to keep them in high potential while the craft spins giving the extended tethers centrifugal force and letting them stay extended enough for them to harvest force from solar wind plasma. Tethers could also be used to generate power. Tethers are amazing dream mayonnaise for making any insane space idea palatable. Tether dreams are way beyond Elon Musk’s comparatively quotidian dreams of cities of Mars and reusable rockets without Elon’s magical capital sourcing ability and media presence.
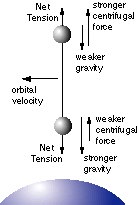
A momentum exchange tether courtesy of Tethers Unlimited
So for Tethers, the firm, going since 1994 a 3D printer and recycler onboard ISS may seem like a bit of a climb down and limited technical challenge compared to what they want to be doing. Nonetheless, for us, it is a great leap. If we conceive of astronauts spending many years in space and journeying through the solar system we know now that many unforeseen things will go wrong. Accidents will happen and valves not opening properly and nonfunctional O rings have killed astronauts. Just a few years ago a design flaw nearly caused an Italian astronaut to drown in space. If we extend our proposed space journeys to years then we know things we will not have foreseen will go wrong beyond any imaginary tolerance for failure that we can engineer away through redundancy. The perfect spacecraft may exist on the platform but it will not exist underway.
In essence, we need a magic satchel with stuff that could repair all the things in ways that we could not imagine them breaking. A combination of a 3D printer and a recycler is that magic satchel. A recycling unit can take food packaging, waste and things no longer need it and turn it into 3D printer filament which then can be printed into solutions for problems. Nonworking solutions can be recycled into iterations of better ones and all of those failures and the winner can be recycled into future solutions waiting to happen. We commonly refer to those as 3D printer filament. A spool of filament is really a seem of ideas not made yet or a roll of problems unsolved. The reason I love 3D printing and am completely obsessed with it is this idea of a recycler and 3D printer combo remaking our world forever letting us consumer while we reuse so please excuse the much more than efficient stream of words. NASA itself says that 95% of spare parts in space will never be used but they don’t know which 95% and that on the 13 tonne ISS they predict 450 Kilograms of failures each year. This in itself makes for a very compelling case for 3D printing spares.
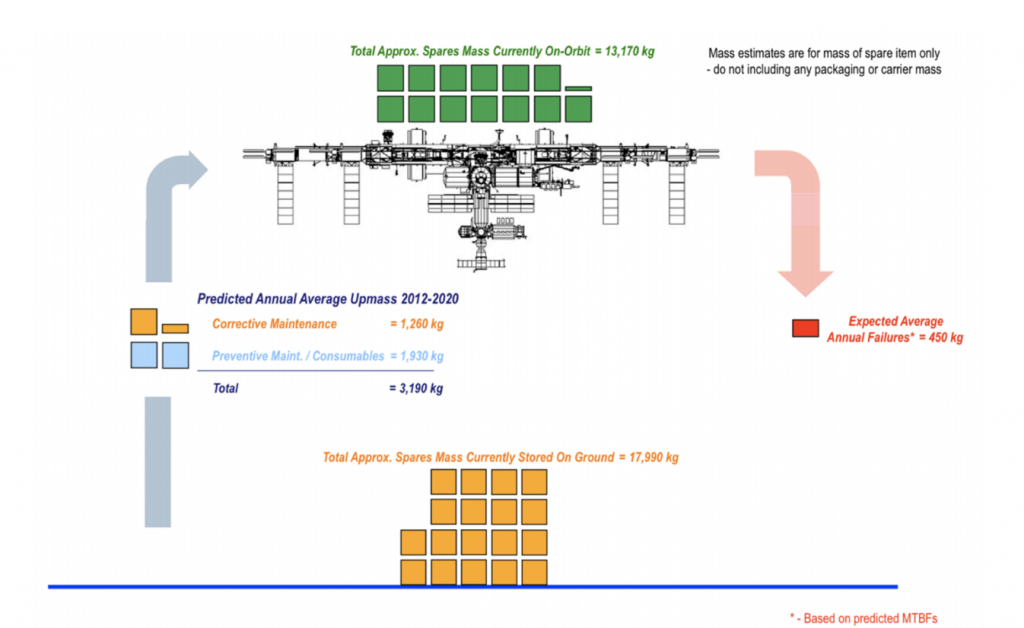
Graphical representation of ISS logistics.
Tethers has now made an Express rack compatible recycler that is being used on board the ISS as we speak. The Refabricators objective is to,
“The Refabricator demonstrates a unique process for repeatable, closed-loop recycling plastic materials for additive manufacturing in the microgravity environment of the ISS a minimum of seven times. Samples consisting of sections of filament and standardized material testing specimens are collected from each cycle in order to quantify any degradation of material that occurs during the recycling and printing process, and enhance the understanding of the recycling process in space.”
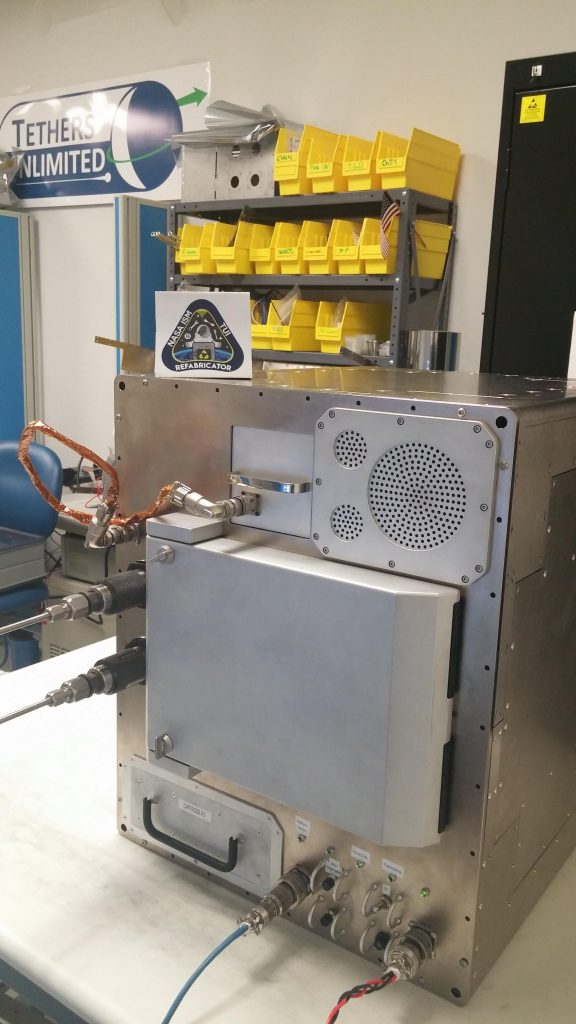
The Refabricator
This would be quite the polymer 3D printing challenge here on earth but at least NASA is being realistic on the number of recycling cycles and material degradation of plastics which a lot of people don’t seem to know. The Refabricator is meant to show,
“Integrated recycling/3D printing capability thus provides significant cost savings by reducing the launch mass and volume required for printer feedstock while decreasing Earth reliance.”
Tethers CEO Rob Hoyt said,
“It will provide future astronauts the ability to manufacture tools, replacement parts, utensils and medical implements when they need them, and greatly reduce the logistics costs for manned space missions by reusing waste materials and minimizing the amount of replacement parts that must be launched from Earth,”
The printer was made for $2.5 million so that’s a good amount to spend on engineering a printer that works well in space and can also recycle. Tethers has additional expertise via a $10 million FabLab project to make a fab lab in space but this is separate from Made In Space‘s own 3D printer initiative. Tethers Refabricator is meant to recycle ABS and they will do it through a process that they’ve called positrusion.
As well the Positrusion effort by Tethers NASA is also developing the CRISSP both as apart of NASA’s ISP (In Space Manufacturing) program. CRISSP is focused on recycling packaging but is also being carried out by Tethers while Cornerstone Research Group is doing a similar effort (but with creating reversible copolymers that can take antistatic bags and turn them into parts) and Resonetics has been tasked with making a sensor and monitoring package. Meanwhile Made in Space is working on its printer and 3D printed metal printing for NASA. Ultratech Machinery (with ultrasonic 3D printing), Techshot and Tethers again are also working on metal parts. With Tethers opting to use its Positrusion system for metals and then combine it with a robot arm and CNC. In metals Techshot wants to use low powered lasers with metal wire in its SIMPLE technology (which is far from it). Techshot’s SIMPLE will use an induction coil around an FDM nozzle to extrude a metal filament which is then sintered by a low power laser. Techshot itself is also working on recycling and separately biofabrication. whats better than astronauts? 3D printed astronauts. Weirdly GE isn’t apparently working for NASA on metal even though its EBM process has been evaluated thoroughly by NASA. Tethers is also working on medical printing in space while the Marshall Space Flight Center itself is trying to print electronics and circuits. NASA also has efforts underway to print structures in space outside of the vehicle which Made in Space, Loral, Orbital ATK and Tethers are working on. NASA also 3D printing structures on MARS so Elon has a place to live. This MARS effort has a contest element as well as a cooperation with the US Army Corps of Engineers here on earth with the ACES initiative which we’ve covered extensively. Additionally, NASA is printing engines and more parts for space systems themselves.
Positrusion is a new filament extrusion technology that Tethers came up with specifically for space based recycling. The system can accept “miscellaneous ABS parts, it will dry and degas the input material before melting and extruding it through a die, and the cross-sectional dimensions and feed-rate of the cooling extrudate will be tightly controlled in a continuous analog of closed-die molding.”
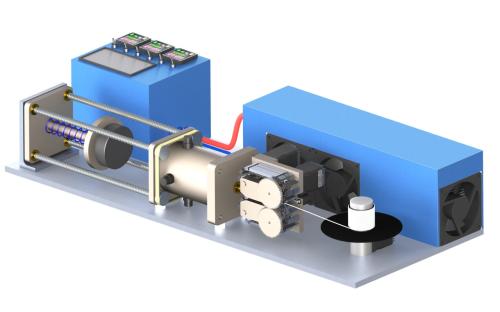
NASA diagram of the Positrusion recycling system
In closed die molding, material is injected into a closed cold mold at high velocity while degassing removes material and creates voids that must be filled while the build material is often quickly cooled. If the Refabricator can control the gas removal and make the filament free of voids while at the same time making sure that there is no bubbling on the surface then they could have a very small form factor recycling process. Tight control of that process could give them high-quality polymer parts as well. If they could tightly collapse the system they make have a really amazing nozzle based print head that can dose and deposit accurately at one point in the future.
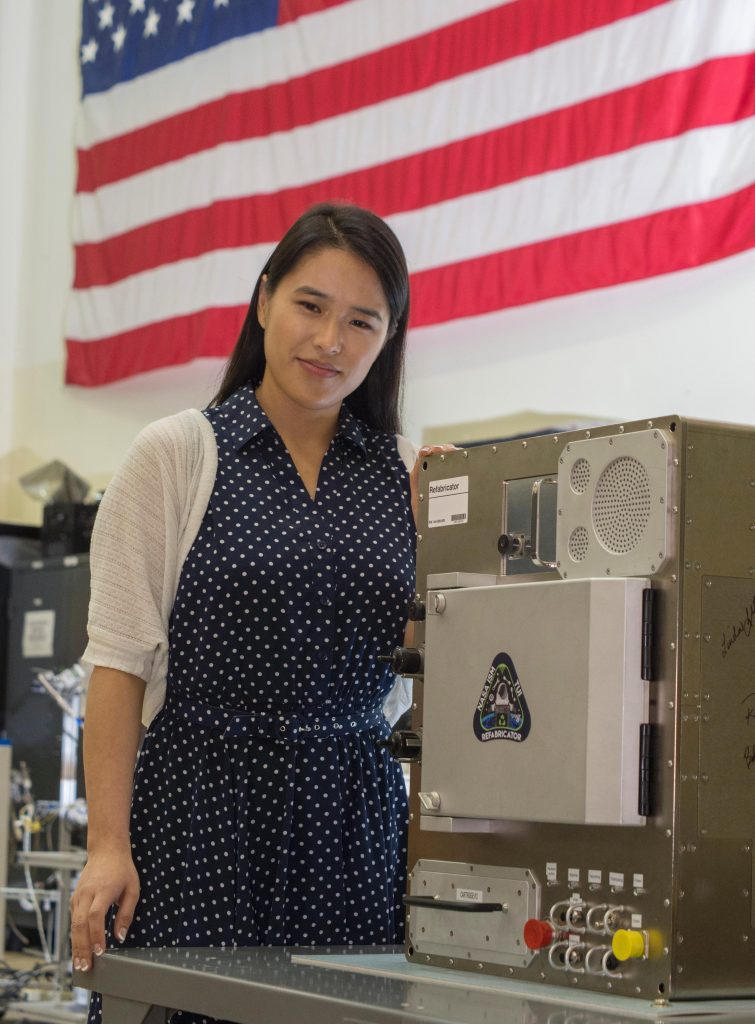
Dr. Allison Porter Missions Manager at Tethers Unlimited with the Refabricator
As well as ABS the system is being tested for use with Ultem 9085 this SABIC material is a UL 94-V0 rated low flame, toxicity and smoke high-performance polymer which you can here on earth get on your Stratasys system and is used widely in aerospace. For space use the Ultem would be significantly safer than ABS and a better bet going forward I should hope. Would this mean that NASA would be inclined to increase its use as build material across the space craft or in other material applications? Ultem Tang packaging anyone?
Developments as the Refabricator would seem to be absolutely essential for the future of space exploration and travel. By recycling what is on board and what is no longer used astronauts could develop solutions for many of the problems that they can encounter and extend the life of the craft that they are traveling on. Here on earth, refabricator-like devices could extend all of the things that surround us. What do you think will homes see refabricators or will this just be a tool for spacefarers? In the meantime here on Earth Tethers has just shed some very experienced people and is hoping to avoid another shutdown, a rather humdrum problem for a company that wishes to conquer the stars.