Because 3D printing can ensure complex structures and geometry, mass production of individualized products seems closer than ever. But, since standards are somewhat lacking across process chains, and automated levels of handling and transport processes are low, it’s only possible to achieve horizontal and vertical AM integration in production lines on a limited basis. Additional obstacles include limited monitoring and a lack of transparency across the process chain, due to a non-continuous digital data chain at lots of interfaces. But the potential benefits of integrating AM into assembly and series production lines in the automotive industry are great, which is why the POLYLINE project was launched.
With 10.7 Mio. Euro in funding by the German Federal Ministry of Education and Research (BMBF), this “lighthouse project” is bringing together 15 industrial, science, and research partners from across Germany with the shared goal of creating a digital production line for 3D printed spare and series automotive parts.
The three-year project officially began at a kick-off meeting of the consortium partners this spring at the Krailling headquarters of industrial 3D printing provider EOS, which is leading the project. The other 14 partners are:
- The BMW Group,
- Grenzebach Maschinenbau GmbH,
- 3YOURMIND,
- Additive Marking GmbH,
- DyeMansion GmbH,
- Bernd Olschner GmbH,
- Optris,
- Krumm-tec,
- Paderborn University,
- Fraunhofer IGCV,
- Fraunhofer IML,
- TU Dortmund University,
- University of Augsburg, and
- University of Duisburg-Essen
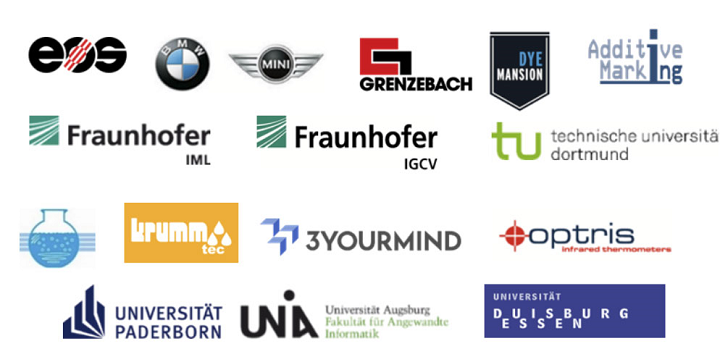
BMBF is funding POLYLINE as part of the “Photonics Research Germany – Light with a Future” program in order to set up AM as a solid alternative for series production. The resulting next-generation digital production line will 3D print plastic automotive parts in an aim to complement more traditional production techniques, like casting and machining, with high-throughput systems.
The project is looking to disrupt the digital and physical production line system, and is using an interesting approach to do so that, according to a press release, “takes a holistic view and implements all required processes.” To succeed, all of the quality criteria and central characteristic values from the CAD model to the printed part need to be recorded and documented, and individual production sub-processes, like the selective laser sintering, cooling, and post-processing, will be automated and added to the production line. For the first time, all technological elements of the SLS production chain will be linked as a result.
Schematic representation of a laser sintering production line
Per the application partner’s requirements, the production line will be realized with “a high degree of maturity,” and uses cases for POLYLINE will include large amounts of both serial and customized components.
Each partner will add its own contribution to the POLYLINE project. Beginning with the leader, the EOS P 500 system will have real-time monitoring and automated loading of exchange frames added to its features; the printer will also be embedded in an automatic powder handling system. Premium automotive manufacturer the BMW Group, already familiar with 3D printing, has a massive production network of 31 plants in 15 countries, and is creating a catalog of requirements for the project to make sure that the new line will meet automotive industry standards. Additionally, the demonstrator line will be set up near its Additive Manufacturing Campus, and cause-and-effect relationships will be jointly researched.
Iterations of a BMW Roof Bracket made with 3D printing. (Image: BMW Group)
Industrial process automation specialist Grenzebach will be responsible for material flow and transport between AM processes, as well as helping to develop automated hardware and software interfaces for these processes. 3YOURMIND is setting up a data-driven operating model, which will include “qualified digital parts inventories, orders processing, jobs and post-processing planning and execution, material management, and quality control,” while software solutions developer Additive Marking is focusing on quality management optimization and resource efficiency.
Post-processing specialist DyeMansion will develop a process for certified, UV-stable automotive colors, create Industry 4.0-ready solutions for cleaning and mechanical surface treatment with its PolyShot Surfacing (PSS) process, and contribute its Print-to-Product platform’s MES connectivity. Bernd Olschner GmbH will offer its customer-specific industrial cleaning solutions, Optris will make fast pyrometers and special thermal imaging cameras adapted for plastic SLS 3D printing, and air filter systems manufacturer Krumm-tec will work to upgrade the manual object unpacking process.
(Image: DyeMansion)
Along with other project partners, Paderborn University is “working on the horizontal process chain for the integration of additive manufacturing in a line process,” while the Fraunhofer Institute for Casting, Composite and Processing-Technology IGCV is developing a concept for POLYLINE production planning and control, which will be tested in a simulation study for scalability. The Fraunhofer Institute for Material Flow and Logistics IML will work on “the physical concatenation of process steps,” paying specific attention to flexibly linking the former manual upstream and downstream AM processes.
TU Dortmund University will help apply deep learning, and implicit geometric modeling, for data preparation and analysis, along with online monitoring and quality management, in order to achieve sustainable automation and efficiency for the project. The University of Augsburg’s Chair of Digital Manufacturing works to integrate AM processes into current production methods, and will apply its expertise in this area to the POLYLINE project, helping to develop strong vertical process chains. Finally, the University of Duisburg-Essen will focus on creating quality assurance for the material system, and its laser sintering process.
The consortium of the POLYLINE project (Image: EOS GmbH)
Discuss this and other 3D printing topics at 3DPrintBoard.com or share your thoughts in the Facebook comments below.
The post POLYLINE Project: Developing Digital Production Line for 3D Printing Spare & Series Automotive Parts appeared first on 3DPrint.com | The Voice of 3D Printing / Additive Manufacturing.