Spanish researchers Juan Barrios and Pablo Romero experiment with different techniques in FDM 3D printing in the recently published, Decision Tree Methods for Predicting Surface Roughness in Fused Deposition Modeling Parts.’
Examining control parameters for achieving finishes, the researchers created PETG parts to compare models from three different tree algorithms—C4.5, random forest, and random tree. Working with 27 different models, the team examined:
- Layer height
- Extrusion temperature
- Print speed
- Print acceleration
- Flow rate
In addition, a dataset has been created to evaluate the models, consisting of 15 additional instances. The models generated by the random tree algorithm achieve the best results for predicting the surface roughness in FDM parts. Data mining can be used to improve 3D printed products based on prior information, demonstrating which methods and parameters are most effective in surface finishing as well as other manufacturing methods like tooling and machining.
Data mining is either supervised and consists of classification and regression, or is unsupervised, consisting of clustering, association rules, and correlations.
“To use these techniques, different classes must be established in which each instance in the database must belong to a class; the rest of the attributes of the instance are used to predict that class. The objective of these algorithms is to maximize the accuracy ratio of the classification of new instances,” stated the researchers.
Decision trees are extremely useful for classifying data, with tree nodes acting as conditions for attributes—with each leaf representing the instances belonging to a class. Researchers rely on these algorithms for engineering predictive models.
The 27 samples were designed in SolidWorks and then 3D printed on an Ender 3 using PETG filament, each with a dimension of 25.0 mm × 25.0 mm × 2.4 mm.
Surface roughness was measured using a Mitutoyo perthometer model SJ-201.
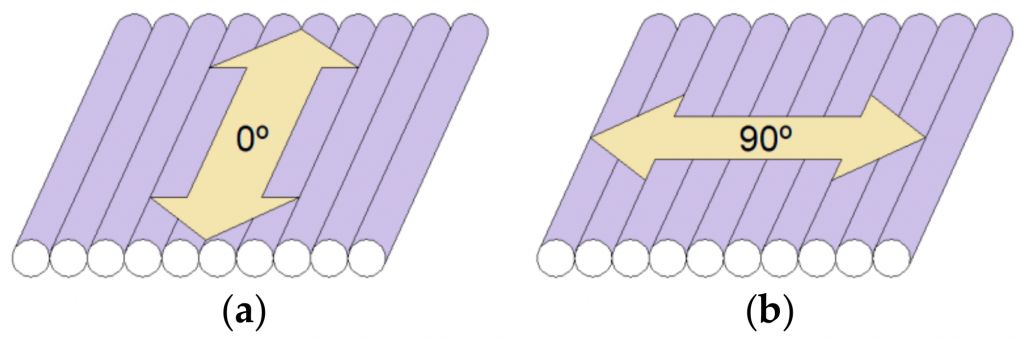
Measurement of surface roughness in the direction parallel to the direction of extrusion (a) and in the direction perpendicular to the direction of extrusion (b).
The J48 algorithm was relied on in this research to plot trees that are not only comprehensive, but according to the research team are also ‘easily understood’ as well as predicting parameters for roughness, to include PA, LH, and F for Ra,0; F, PS, and LH for Ra,90.
“PA is the parameter with the greatest influence on Ra,0; F, PS, and LH are the parameters with the greatest influence on Ra,90. However, in this case, the models created with J48 algorithm were not able to predict the data used in the test. This may be related to overfitting problems,” concluded the researchers. “In the problem addressed, the random forest algorithm obtained better results than J48, as could be expected from the literature.”
“In future works, we intend to study whether the decision trees can be used to generate models that allow for the prediction of a better dimensional accuracy of the parts manufactured by FDM. The impact of other print factors on the surface properties of printed parts, such as nozzle diameter, will also be studied.”
Study of topologies and issues like surface roughness and finishing continue to be critical to 3D printing enterprises as users explore issues with complex internal structures, antibacterial surfaces, hydrophobic and hydrophilic surfaces, and more.
What do you think of this news? Let us know your thoughts! Join the discussion of this and other 3D printing topics at 3DPrintBoard.com.
The post University of Cordoba: Predicting Surface Roughness in FDM 3D Printing appeared first on 3DPrint.com | The Voice of 3D Printing / Additive Manufacturing.