The TCT Asia show began today in Shanghai, and desktop 3D printing leader Ultimaker is one of the attendees. The Dutch company made some important announcements at the event today, including the launch of its future-ready Ultimaker Cloud platform, which was designed to support the professional 3D printing workflow and will help speed up the adoption of 3D printing.
As the world transitions to local digital manufacturing, we need a platform solution that will not only make the user workflow more simple but also hasten this transition, while ensuring compatibility with multiple materials and software applications. Due to Ultimaker’s open strategy, important industry partners, like material manufacturers and CAD providers, can integrate with its new cloud-based platform, which will offer more value to users and make the 3D printing experience seamless and reliable.
“Ultimaker Cloud forms the foundation for future value propositions provided by Ultimaker and key industry partners. This is a crucial next step in our journey to speed up the world’s transition to local digital manufacturing,” said Jos Burger, Ultimaker CEO. “I have no doubt that our enabling platform, formed with our global network of software and material partners, makes Ultimaker the preferred solution in the desktop space.”
The first cloud services the platform offers include remote 3D printing, which will provide monitoring and allow print jobs to sent from anywhere to network-enabled Ultimaker 3D printers. Ultimaker Cloud also provides unlimited access to the Marketplace, where registered users can browse materials thanks to exclusive access to print profiles, as well as give feedback to the community and plugin contributors through a rating option. In addition, optimized settings for ideal print results are automatically populated in Ultimaker’s Cura software through the Marketplace. Finally, Ultimaker Cloud offers a way to backup user settings for easier remote access.
Ultimaker Cloud will be available for download on March 19th, which is also when Ultimaker Cura 4.0, with its updated user interface, will be launched.
This new cloud-based platform isn’t the only news Ultimaker announced at TCT Asia. The company’s Material Alliance Program, which was established last year, has three new members: Polymaker, eSUN, and Essentium.
“The growing importance of 3D printing gives us – as a leader in desktop 3D printing – an important role in ensuring a perfect collaboration between hardware, software and materials. By offering material profiles directly to millions of end users via the Ultimaker Marketplace, we unlock new 3D printing applications for different industries,” said Burger. “Essentium, eSUN, and Polymaker and are well-respected material companies, offering unique material properties that are relevant for engineers working in a wide range of industries. I am proud to recognize their commitment to the Ultimaker Material Alliance during TCT ASIA.”
This means that there will now be more choices for applications and materials in FFF 3D printing, as print profiles for these three companies will now be available for download in the Ultimaker Marketplace. Users can just choose a material profile and quickly begin a print.
“FFF 3D printing remains the most practical and accessible of all 3D printing technologies. The three materials we offer via the Ultimaker Marketplace, including PolyMide PA6-CF, PolyMide CoPA and PolyCast, are among the most unique and advanced materials in our portfolio,” stated Polymaker president Dr. Xiaofan Luo. “I believe they will open up countless new applications for a greater number of engineers.”
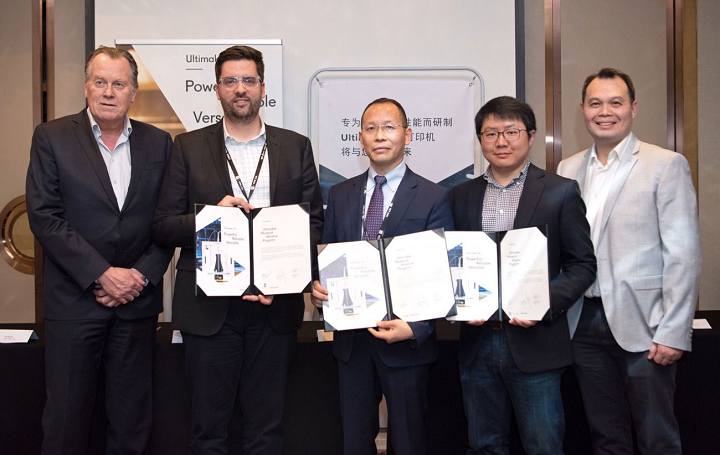
L-R: From Jos Burger, CEO Ultimaker; Dr. Blake Teipel, CEO Essentium; Dr. Yihu Yang, CEO eSUN; Dr. Xiaofan Luo, President Polymaker; Benjamin Tan, VP APAC Ultimaker
Each new member of the alliance brings something important to the table. For instance, recycling is a topic that’s widely discussed around the world, and it seems like helpful initiatives are popping up all over.
“We are specialized in the industrialization of biodegradable polymers. We are delighted to join the Ultimaker Materials Alliance Program with material print profiles of PETG, ePA-CF, and HIPS (High Impact Polystyrene), since it allows us to speed up the development of eco-friendly 3D printed products by using renewable resources,” said eSUN’s CEO Dr. Yihu Yang.
So engineers in the electronics industry can benefit from FFF 3D printing, the materials used must be ESD safe. Now, print profiles in the Ultimaker Marketplace are available with just these properties.
“At Essentium we are committed to creating industrial solutions for the world’s top manufacturers and bridging the gap between 3D printing and machining. We have partnered with BASF, the world’s largest chemical producer, to create the Ultrafuse-Z line, which is a series of ESD safe filaments that are powered by Essentium,” explained Dr. Blake Teipel, CEO of Essentium. “We offer material print profiles for Ultrafuse-Z PCTG in the Ultimaker Marketplace, an industrial grade filament that is specifically formulated to be ESD safe.”
Discuss this news and other 3D printing topics at 3DPrintBoard.com or share your thoughts in the Facebook comments below.
[Source/Images: Ultimaker]