
Earlier this week, I arrived back home in chilly Ohio after spending a couple of days in Dallas, Texas. But I wasn’t just visiting the Lone Star State to enjoy the warmer temperatures – I was there to attend one of the biggest events in 3D software, SOLIDWORKS World 2019, which was held in the Kay Bailey Hutchison Convention Center.
This was my first time at the event, which was in Los Angeles the last couple of years, and I’d heard a lot of good things about it, so I was excited.
While I missed the first full day of SWW 19, I was off to the races on Tuesday morning. Three different General Sessions were offered during the same time, and I decided to skip ‘New Horizons’ and ‘Design to Profit’ in favor of ‘R&D Futures,’ which promised attendees a preview of “the cutting-edge technologies taking form at Dassault Systèmes/SOLIDWORKS R&D Labs.”
Manish Kumar, Vice President of R&D for SOLIDWORKS, said that a single global R&D team binds together all of Dassault’s 12 brands, and the 6,700 members of this team, who are spread out across 21 nations, are encouraged to work on their dream projects. Kumar said that design is the starting point at Dassault, but posed two questions – is design still the way we learned it? What is its future?
The 3DEXPERIENCE platform by Dassault Systèmes now includes a portfolio of applications in its new 3DEXPERIENCE.WORKS that will put user experience and simplicity at the core. Kumar likened the platform to a story with three chapters: industry renaissance, knowledge and know-how, and the workforce of the future. He explained that these interconnected chapters “are the themes that drive us.”
Kumar shared a personal story about his father, who once nearly missed a flight because, “like any dad, he refuses to seek any additional help,” such as smartphone airline apps that make traveling more efficient by providing helpful things like notifications of gate changes.
“How many of you face the same problem in your day to day life?” Kumar asked. “When you start your design, when you are extremely busy trying to finalize your design, how many times has it happened where someone who is working on the other design – which your design depends on – changed that design and they forgot to tell you? So you’re working off data which is already out of date.
“How are you gathering information? How are you sharing information, and how are you keeping everything up to date? Is it still like a printed boarding pass, which gets outdated right after it was printed, or is it like an airline app which is connected all the time to a single source of truth?”
Having been notified of more than one gate change this week through my airline app, this analogy really speaks to me…and it’s definitely applicable to additive manufacturing.
“We are in a world where technology enables people from all walks of life to share their knowledge and know-how like never before,” Kumar stated.
“What is your expertise? You are creators, you are designers, you are manufacturers, you are dreamers. If you have to share your expertise with the world, how would you share it?
“Our 3DEXPERIENCE platform is a platform for knowledge and know-how. This quest is also the core of our DNA. We at Dassault Systèmes R&D understand that the world is changing and the future is right now.”
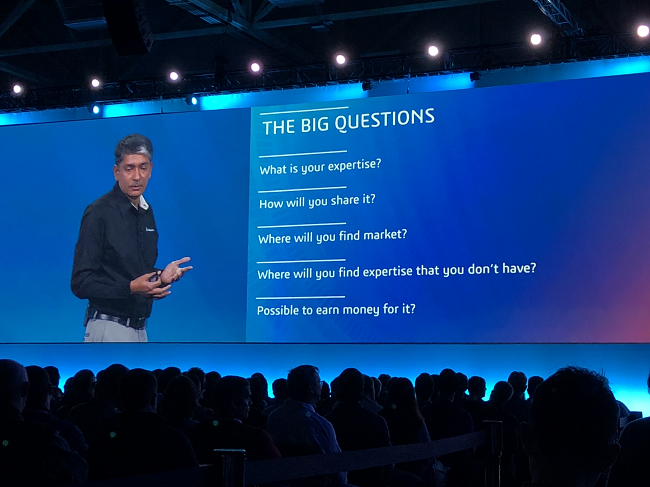
Kumar reminded everyone that the current generation is working with technology in ways we never thought possible. While I was learning how to use Microsoft PowerPoint in eighth grade, students today are making actual robots…and using 3D printing to do it. A few years ago, I was sitting in a local yogurt shop that had an old typewriter on the counter, which patrons were encouraged to use for fun. A man brought his young daughter up to see it, and after running her finger over the keys, she said, “Daddy, where’s the search button?”
These personal anecdotes popped in my head during Kumar’s talk, both of which prove his point: kids today know that everything is connected.
“Today our kids are growing up in an environment where the global market is accessible to them,” Kumar said. “Our future generation is growing up in an entirely different world…connected to a global world of intelligent machines and computing power.
“So as they become our next generation workforce, we need to be ready for their needs. At Dassault Systèmes R&D, we take all these factors into consideration.”
Kumar then invited six members of the global R&D team onstage to show the audience what the team is working on, and SOLIDWORKS employee Aaron Kelly joined him first.
“24 years ago when I started at the SOLIDWORKS brand, we had the mission to put the power of 3D at every engineer’s desktop,” Kelly said. “We’ve been working on that passionately over that time, but there was one other thing. There was this unwritten promise, and that promise was that we would work together to make products…to build this ecosystem of products that were valuable and got you to get your job done faster and better.
“3DEXPERIENCE.WORKS, to me, is kind of a culmination of that promise.
“I know you’ll work with us together, and I know we’ll continue to make great products, because 3D is not enough – you’ve told us that. 24 years ago, 3D was new, it was exciting, and many of you have adopted it, and you’ve come back to us and said ‘We need more. We need to take our business to the next level, we need more tools.’ And when I think of 3DEXPERIENCE.WORKS…I think of that taking us down a path to smashing down the walls of limitations and gently opening the doors to infinite possibilities.”
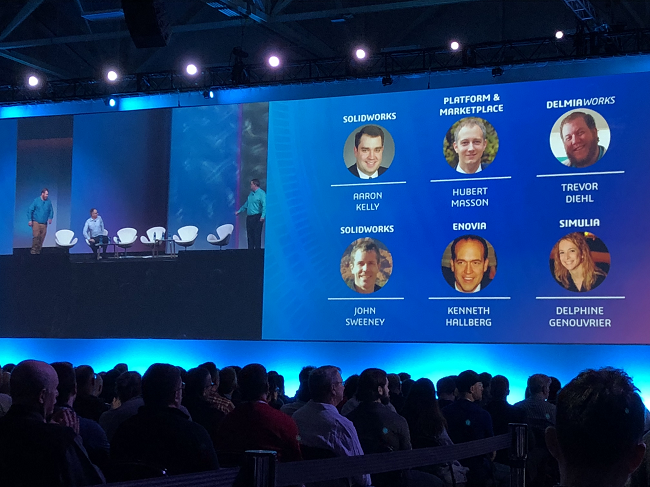
Kelly then introduced the other experts from the SOLIDWORKS R&D team, which, according to John Sweeney, just released several hundred new features in SOLIDWORKS 2019, and is currently working to do the same with SOLIDWORKS 2020.
Sweeney discussed some of the team’s multi-year initiatives, such as Sketch Enhancements, and 3D MarkUp, which can now be completed with a mouse. Mesh Modeling now allows for the addition of textures by grabbing a bitmap, dragging it to the correct place, and actually changing the surface of the mesh right then and there. This means it comes right off the 3D printer with that texture.
He also mentioned some big performance initiatives from last year that are continuing into next year, like a telescope model with huge assemblies that can be opened, and edited, in LDR, or Large Design Review, mode. Sweeney also discussed the new Detailing Mode, which gives users access to all project sheets and the ability to complete edits, like deleting dimensions.
Hubert Masson, who works with the 3DEXPERIENCE Marketplace, talked about how the company helps customers with collaboration, and mentioned two specific applications: 3D Drive, which has to do with file storage and sharing on the cloud, and social media collaboration on the 3D XPoint platform through 3D Swym.
Users can upload files to the cloud with a simple drag and drop from their web browser to 3D Drive.
“In a few seconds, all those files become available and accessible from anywhere – from the web browser as well as right from within SOLIDWORKS,” Masson explained.
You can also drag and drop files in order to add more components to a model, and send the files to other users, who can then work on them from their own devices and send suggestions back and forth, which will remain forever in the cloud as searchable comments. In 3D Swym, groups of people can create and publish social contact, react to it, and share existing content. The application was recently enhanced in order to increase user engagement, so people can now have private conversations on 3D Swym.
[Image: Dassault Systèmes]
Both 3D Drive and 3D Swym are available through iPhone apps, and 3D Drive also offers an augmented reality feature that allows users to get an even closer look at models from their phones. Additionally, you can even make video calls, which Masson demonstrated by calling a colleague in the front row.
Sweeney took center stage again to discuss design applications, and mentioned the recently announced xShape, which allows freeform design on the 3DEXPERIENCE platform. Then Kenneth Hallberg talked about Dassault’s ENOVIA PLM software, which works to keep things more product-based.
“We’re kind of taking a giant leap with 3DEXPERIENCE PLM Collaboration Services, and next to our 3D Drive solution, which is file-centric, we are delivering an all-embracing environment that supports everything from innovation processes to design and engineering work that spans over and across enterprises,” Hallberg explained.
“3DEXPERIENCE PLM Collaboration Services is connecting not only the SOLIDWORKS desktop users but all of the product stakeholders in a company, no matter what function you have or applications that you’re using.
“In addition to this, we are leveraging the ENOVIA portfolio and we’re providing really strong applications and capabilities for planning work…development work…and finally release activities, like engineering and comprehensive change management.”
Delphine Genouvrier has helped SOLIDWORKS create many simulation products over the years and is currently working with its SIMULIA team.
[Image: Dassault Systèmes]
“Lots of great things are coming for the SOLIDWORKS community, with a strong focus on power, robustness, and intuitiveness, ” she said.
To help customers increase efficiency and innovation, Genouvrier noted that it was imperative to assess product performance early on, with the highest possible fidelity. She explained that now through SIMULIA, users can test out projects with any physics through SOLIDWORKS, which is “completely new” for the community and can be accessed in the cloud through a “unique engineering workflow.” The 3DEXPERIENCE platform makes it easy to share simulation results during design, which can then be reviewed on any device anywhere.
Finally, Trever Diehl introduced the room to DELMIAWORKS, which is the rebranded version of IQMS – a recent acquisition of Dassault’s. Diehl described it as the bridge between designing and executing a product, as it provides all sorts of helpful features:
- part quoting
- process monitoring
- scheduling, order processing, & shipping
- shop floor integration
- accounting suite
This helps ensure that your product is actually profitable.

“Think about making cookies,” Diehl said. “You get the dough together, you batch it out onto a baking sheet, you put it in the oven, you take out a batch of cookies.”
The R&D team members also talked about the 3DEXPERIENCE Marketplace, which makes it easy to collaborate between partner companies to “get your parts made in record time.”
Before the session ended, we got a surprise – the next morning, on the last day of SWW 19 and before the last General Session, the entertaining (and only slightly corny) SOLIDWORKS News Network team, or SNN, would perform a “What’s New” skit to provide attendees with a sneak peak at some of the latest features and platform updates “that even Wikileaks wouldn’t report” coming in SOLIDWORKS 2020.
After a day of interviews and a press conference, both of which I will talk about in more detail later, I spent the evening attending the SWW 19 special event, which was held nearby at a giant entertainment venue called Gilley’s and included everything from horseshoes, trivia, and a photo booth to hearty snacks and drinks, lots of live music and opportunities to meet new people, and armadillo racing…yes, you read that correctly.
The special session the next morning began with Dassault’s Mark Schneider announcing the winners of the Lenovo-sponsored Model Mania Challenge, which pitted users against users and resellers against resellers to see who could model and analyze a part most efficiently, accurately, and quickly.
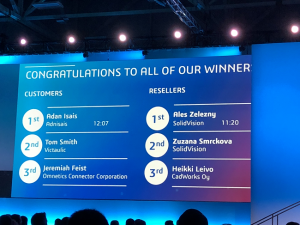
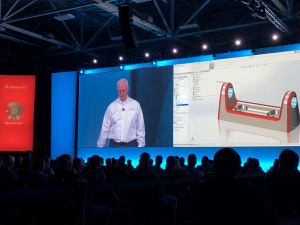
Then, the six members of the SNN team – Schneider, Mark Barrow, Megan Duane, Michael Steeves, Jeremy Regnerus, and Yan Killy – went into full Anchorman mode, complete with plenty of groan-worthy jokes, to bring the room the latest SOLIDWORKS 2020 updates.
For instance, weatherman Schneider said that a massive approaching deadline could “lead to elevated stress levels” across the entire design ecosystem, and mentioned enhanced features for the Sketch Relations application, which allows users to control curves and will soon be able to make models even smoother with the new G3 Curvature constraint.
Another new assembly function coming is Envelope Publisher, as SW 2020 will include the ability to fill in mass properties for wires and cables; thanks to another new feature, the mass can also be calculated automatically. The team’s sportscaster brought up March Feature Madness, and explained some of the features of the 3DEXPERIENCE platform that would make up his top 10 list, including new tools that he was able to use to fix the remote he broke out of excitement over the Patriots’ recent Superbowl win.
One example is the ability to drag freeform primitive surfaces in order to easily customize geometry onscreen. In addition, users can select the Cage manipulator to achieve an alternate perspective for making detailed changes to freeform surfaces, and selection filters offer multiple ways to work with geometry. xDesign is a new browser tool that can use a merge function to knit freeform shapes into solid bodies, Flexible Parts can make any component dynamic, and SW 2020 will also allow you to run simulations and share design data more easily with other team members.

Killy, the team’s undercover reporter, tracked down a major developer to determine their favorite new features. Detailing Mode, which Sweeney mentioned the day before during R&D Futures, was brought up – it lets users quickly open drawings, no matter the complexity or size, without losing any detail, and also allows for annotation. While SW 2019 lets users add markups to past assemblies, SW 2020 takes it a step further with the new Markup view, which lets you choose a writing utensil and add markups directly to the screen of your device, then save, send, and post as a PDF.
Stay tuned for more news from SOLIDWORKS World 2019 – in the meantime, enjoy some of the pictures I took at the event:
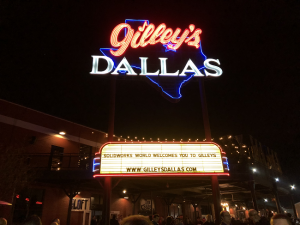
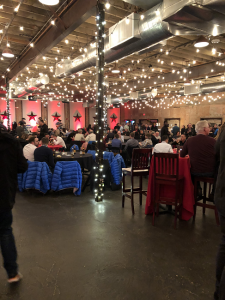
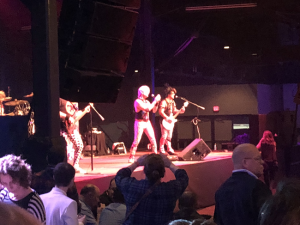
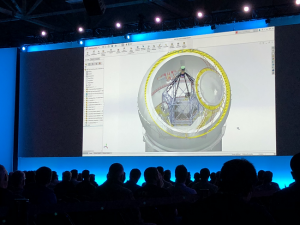
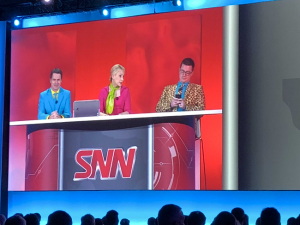
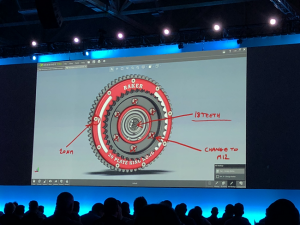
Discuss this news and other 3D printing topics at 3DPrintBoard.com or share your thoughts below.
[Images: Sarah Saunders, unless otherwise noted]