As the applications of drones varies and grows, it becomes more and more important to develop specific designs that are based on its particular function. A drone built for delivery requires different specifications than a drone built for surveying or image capture. 3D printing is driving this evolution of drone technology by providing access to affordable rapid prototyping and customization and allowing faster innovation to occur. Whether it’s for disaster relief, mapping, or carrying heavy payloads, a drone can better serve its function with the time and cost efficiency and attention to detail that 3D printing provides.
Here are 5 drone projects that have pushed the
boundaries with the help of 3D printing:
Disaster
Relief X VEIN Drone by Team ROK
After the Great East Japan earthquake and tsunami brought disaster on a massive scale in 2011, Yuki Ogasawara and Ryo Kumeda of Team ROK were inspired to create a drone built especially for disaster relief and search and rescue. A few years later they used 3D printing and generative design to create their x-shaped X VEIN drone. Because disaster aid presents its own specific set of challenges, the team used 3D printing to be able to customize their drone based on their exact needs.
The design features freeform curves, and a 3D printed lattice-patterned body for maintaining minimal weight while still giving it the strength required to operate in difficult conditions. X VEIN is able to fly within a 500 meter range and can be equipped with thermographic and infrared-imaging and capture images that can be viewed in real time to access remote or obstructed areas and help locate survivors. Because many of its parts are 3D printed, if they are damaged on a mission they can be re-printed and replaced on site. 3D Printing was a crucial tool to be able to have the level of design freedom necessary to build a drone with these specific needs and it ensures that the drone can be further customized in the future depending on the situation at hand.
CargoCopter
by KU Leuven Researchers
Built to deliver payloads over long distances, KU Leuven research team created the 3D printed CargoCopter, a hybrid drone that combines fixed wings and multi-rotors so that it can take off vertically, hover and then fly horizontally. It was designed to expand the range and speed of traditional multi-rotor drones and thanks to its hybrid nature can efficiently transition from take-off to long-distance flight. It can carry up to 5kg, has a range of 60km and can fly up to 100km/hour. The team used 3D printing to rapidly prototype over 3 years to arrive at this model and their designs were able to quickly evolve. Thanks to the customization flexibility of 3D printing they are able to optimize each new CargoCopter design based on the needs of its particular mission.
BLUEROV2
Submarine Drone by Blue Robotics
Aerial drones are not the only ones making use of 3D printing. When Blue Robotics set out to build their underwater drones, they needed parts that could withstand the harsh conditions of the ocean and had trouble sourcing ones that were durable enough and weren’t overly expensive. They then turned to 3D printing to be able to prototype their own parts at a much more affordable rate. Using 3D printing to prototype also led them to customize parts to fit their exact needs. The BLUEROV2 comes with a high definition, wide-angle low-light camera with two or four lights to illuminate the ocean around it. It can travel to a depth of up to 100 meters and is built to withstand currents. The ROV is designed with expansion and modification in mind, and is fitted with a customizable frame to accommodate a range of functions.
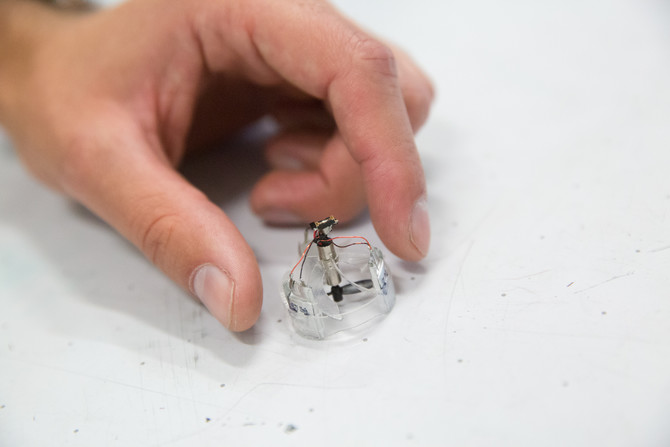
Piccolissimo
The Tiny Drone by Matt Piccoli from UPenn
In 2016, Matt Piccoli from UPenn’s School of Engineering and Applied Science designed the world’s smallest steerable drone “Piccolissimo”. The tiny drone comes in two sizes: one weighs 2.5 grams and is the size of a quarter, and the other steerable version is 2 grams heavier and a centimeter wider. It was 3D printed using lightweight plastic. It has two moving parts, the robot’s body and motor, which spins one way 40 times per second, and its propeller spinning 800 per second in the opposite direction. Its motion is determined by how quickly the propeller and body are spinning, which can be controlled by infrared signals. The drone can carry a load of up to one gram, like a small camera or sensor. Its size suggests that it would be a fitting model for surveying or search and rescue missions, as a few hundred could be used to cover more ground than a single larger sized drone.
The
Int-Ball by the Japan Aerospace Exploration Agency (JAXA)
The Int-Ball, or JEM Internal Ball Camera was built using 3D printing to float aboard the International Space Station taking video and photo documentation. The spherical drone arrived on the ISS in June of 2017 and weighs 1kg, has a 15cm diameter and moves with 12 propellers. The Int-Ball features both internal and external components produced using 3D printing and is designed to float in a zero-gravity environment with the ability to move autonomously or be maneuvered by operators on Earth. It is set to reduce the crew’s workload by 10% by taking on image capturing duties.
3D printing helps to redefine what is possible when it comes to exploring and achieving innovation in drone technology. Its efficiency in prototyping and customization make room for a higher level of productivity and imagination, improving the way drones are designed and manufactured. If you are looking to create the next innovative drone, 3D printing is essential to facilitating the most efficient and flexible production process.
See how Shapeways can help your drone business transition to 3D printing!
The post 5 Next-Level 3D Printed Drones That Are Pushing the Industry Forward appeared first on Shapeways Blog.