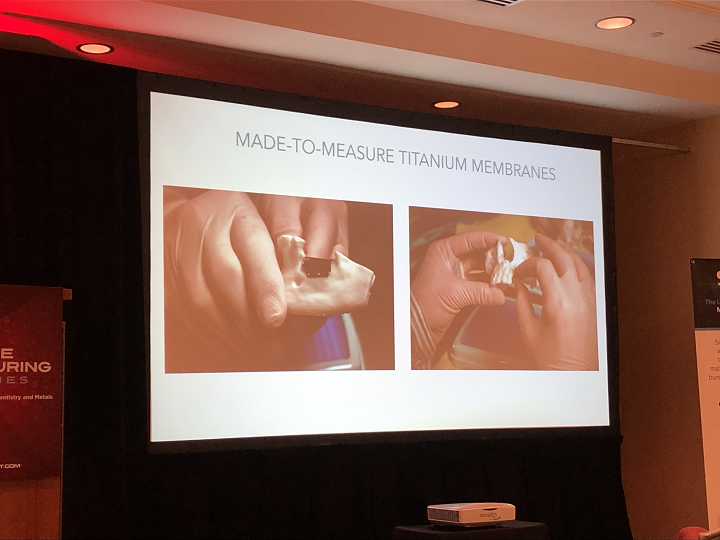
She finished by stating that the company believes FDM printing can “be a good value add for dentists.”
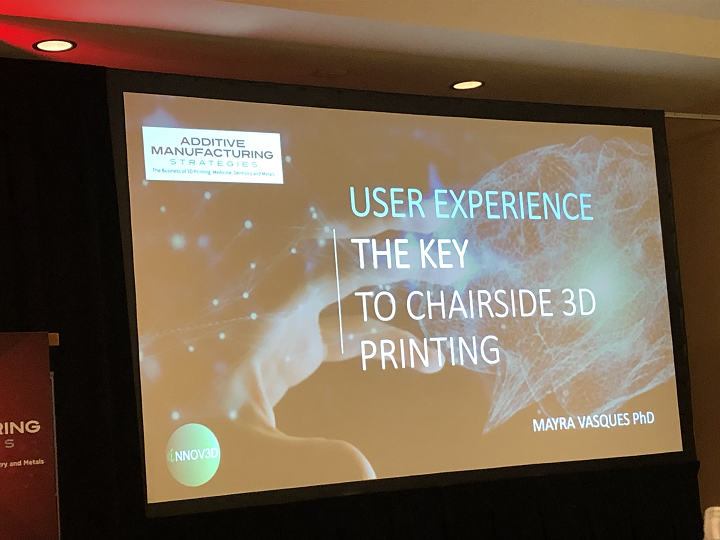
Vasques finished things by sharing her research into how things look, dental 3D printing-wise, from the point of view of clinicians.
“It’s common for most to be scared of using 3D printing,” she explained. “They think it’s plug and play, and it’s not.”

For her research, she divided users into two separate groups – high level experience (seniors), and innovation (early adopters and students).
“We are trying to figure out how these people understand the technology,” she said.
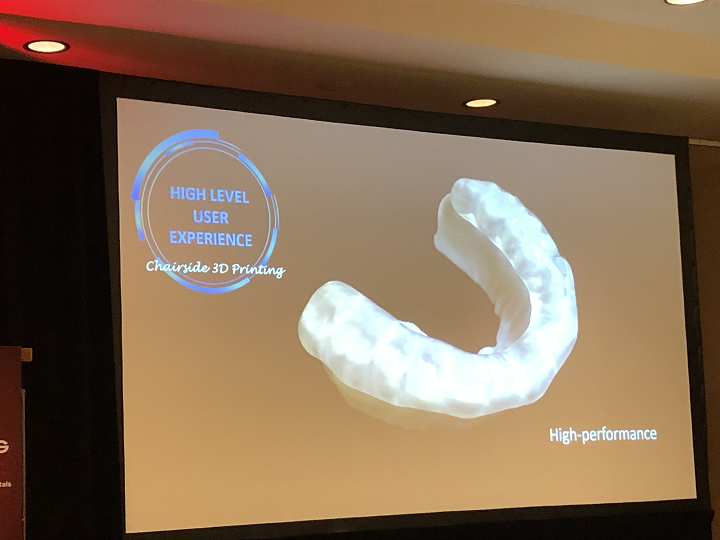
High level users expect accuracy, efficiency, high quality technology, and high-performance materials for the purposes of chairside 3D printing. Vasques said that these users “don’t want to wait 2-3 hours to make products by hand.”
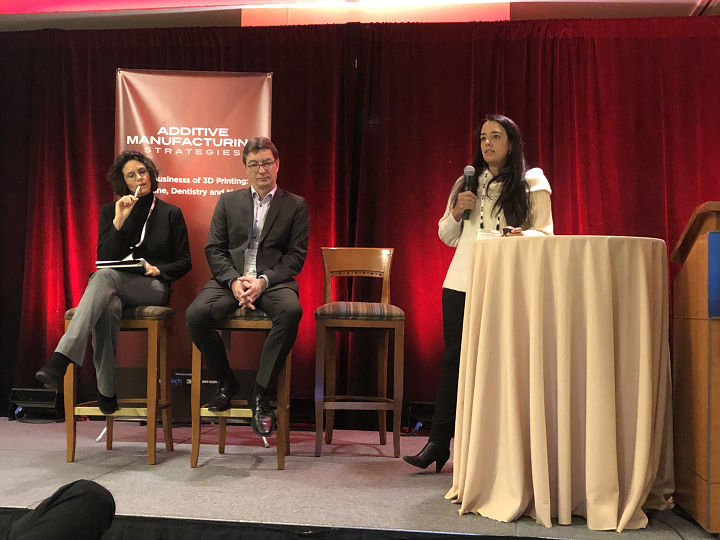
“In university, we’re trying to establish protocols and research to help these people have the results they are expecting.
“We’re trying to solve problems, like mouthguards for sports.”
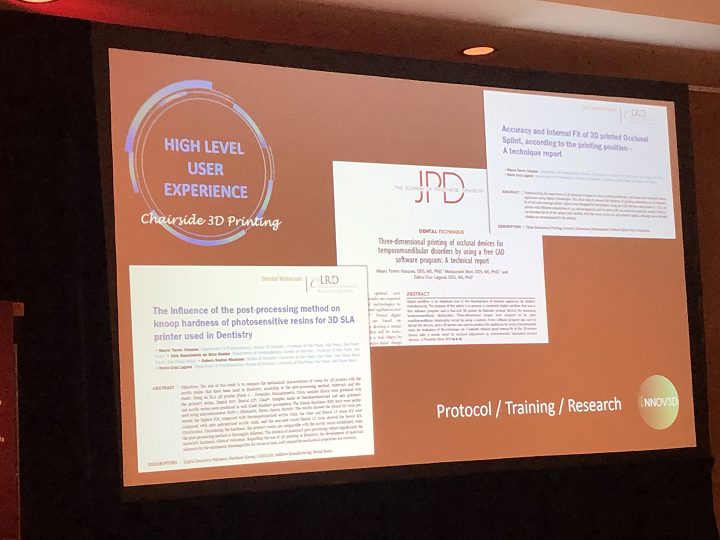
Vasques said that last year, she and her team published three articles about dental 3D printing topics, such as 3D printed occlusal devices and post-processing. She launched INNOV3D the same year, in order to help train professors in using dental 3D printing.
“We have an online training platform, educational materials, and 3D lab,” she stated.
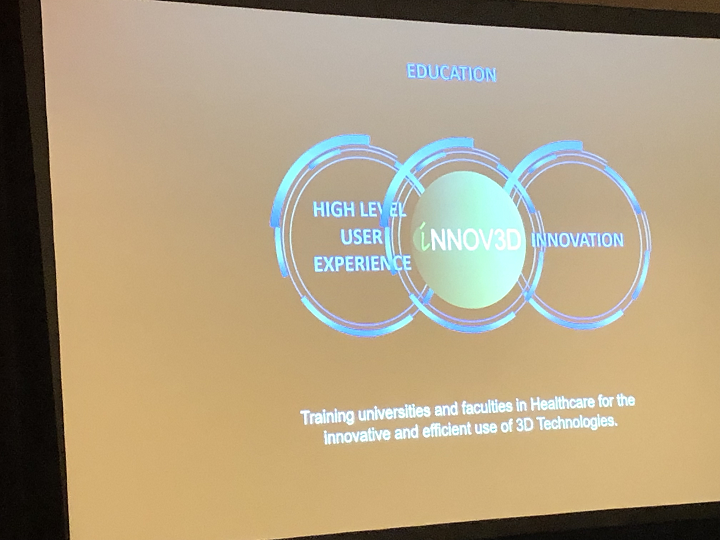
Once she finished and sat back down, Davide Sher, the panel’s moderator, asked the other two panelists how they would address the challenges that Vasques listed, and how they would make dentists understand more about dental 3D printing.
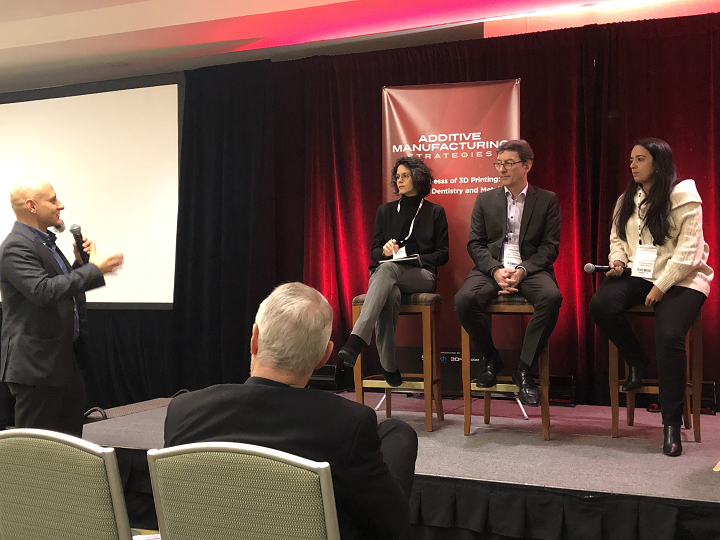
Ferracane answered that most dentists aren’t buying 3D printers today, because they’re initially taught that the systems are really easy to use when they’re not. Once they run into issues with SLA technology, they get frustrated and just start outsourcing the work instead.
“Then they’re really dissatisfied, because they’re complicated and not just plug and play. We need to help them understand that they can bring the technology back to their office.”

Sher noted that dentists don’t really have the time to learn about the more advanced types, and so asked if the companies directed their technology to users in dental labs; Dr. Mayerhofer said yes.
After a short break, the next session, “Dental lab experiences with 3D printing,” began. While Les Kalman, an Assistant Professor for Restorative Dentistry at Western University’s Schulich School of Medicine, was unable to make AMS 2020, Arfona founder and CEO Justin Marks and Sam Wainwright, Dental Product Manager for Formlabs, were both ready to go.
Marks went first, explaining that Arfona, founded in 2017 by dental technicians and 3D printing enthusiasts on “the core belief that thermoplastic dental materials should not be substituted for inferior photopolymers,” has been working to “bring 3D printing into the world of dentistry.” The company’s flagship product is its 3D printed flexible nylon dentures.
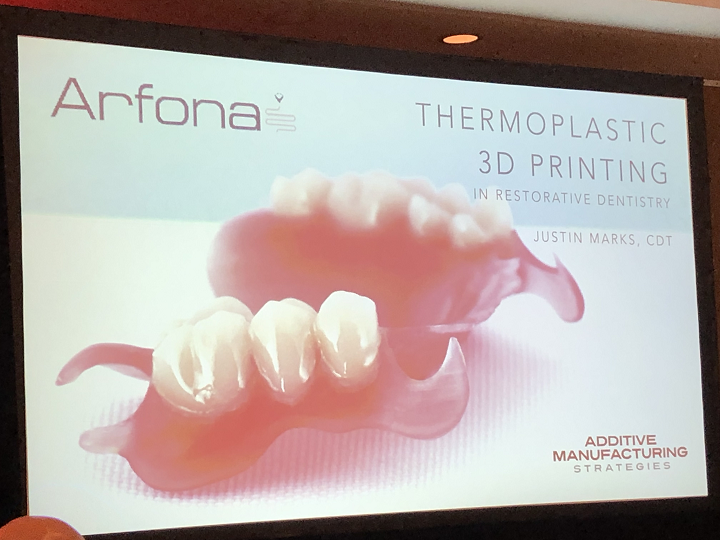
He pulled up a slide that cited research stating that 36 million Americans are completely edentulous, meaning without teeth, and that 178 million are partially edentulous. But even so, Marks said that there’s an “astronomical” number of people who are still not wearing dentures.
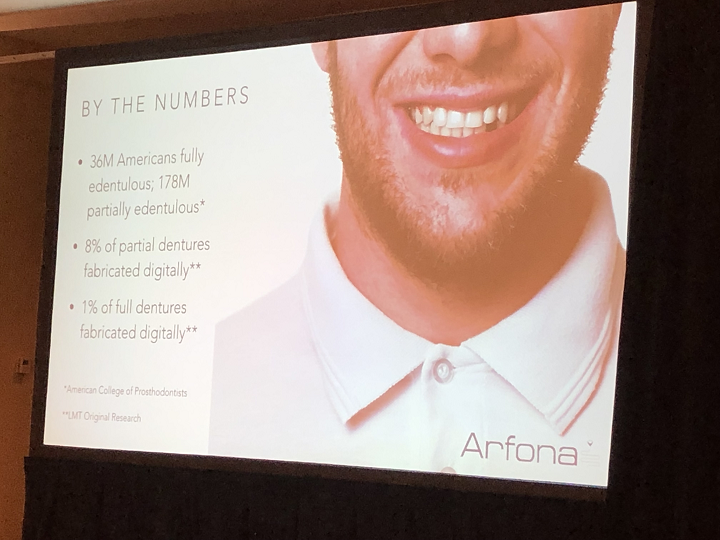
“Most people don’t think about this until it happens to you or someone you know,” he said about missing a tooth. “It’s not always that easy or cheap to fix this with implants.”
According to a survey, only 8% of dentures are digitally fabricated, which means most are still made by hand using analog methods.

Marks said that even though 3D printing is “becoming more of a buzzword” in the dental industry, most of the materials “have largely stayed the same,” and based on the same technologies and principles. Extrusion-based AM is not used often in dentistry, and powder bed fusion (PBF) is mostly limited to metals, not polymers.
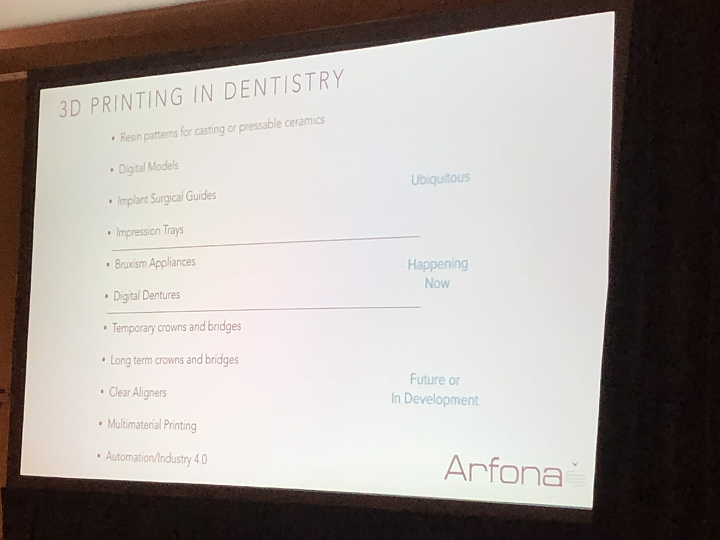
Marks went through a brief history of 3D printing in dentistry. Ubiquitous applications include impression trays, digital models, and resin patterns for casting, while digital dentures are currently happening and things like clear aligners, temporary and long-term crowns and bridges, and multimaterial printing are in development for use in the future.
He said that the ubiquitous ones have one thing in common – they’re used once and then thrown away.
“We’re still not doing much with crowns and bridges,” Marks said. “Clear aligners are the holy grail, and direct printing of the aligner is still a ways off, though all companies are probably working on it.”
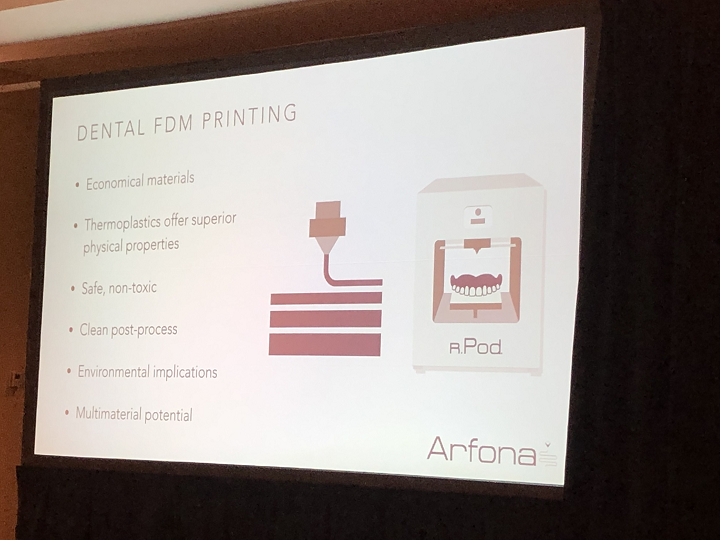
Aronfa’s dental 3D printer is the r.Pod, which is a modified version of a Makerbot clone. The dual extrusion filament system is optimized for all of the company’s thermoplastic materials.
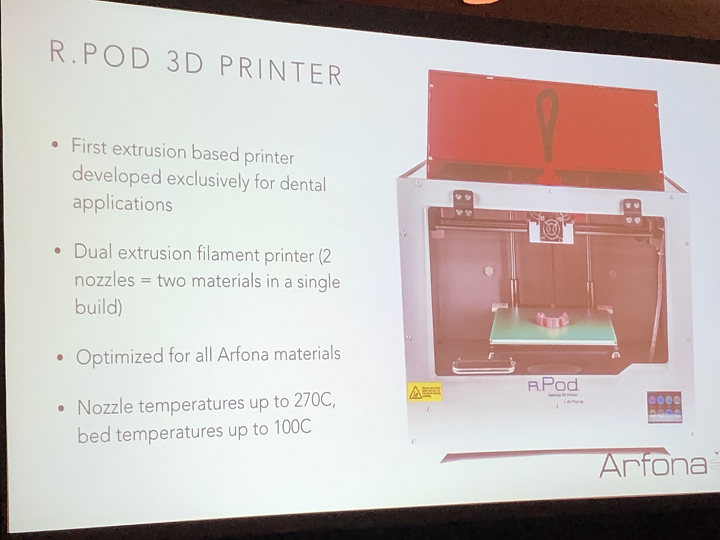
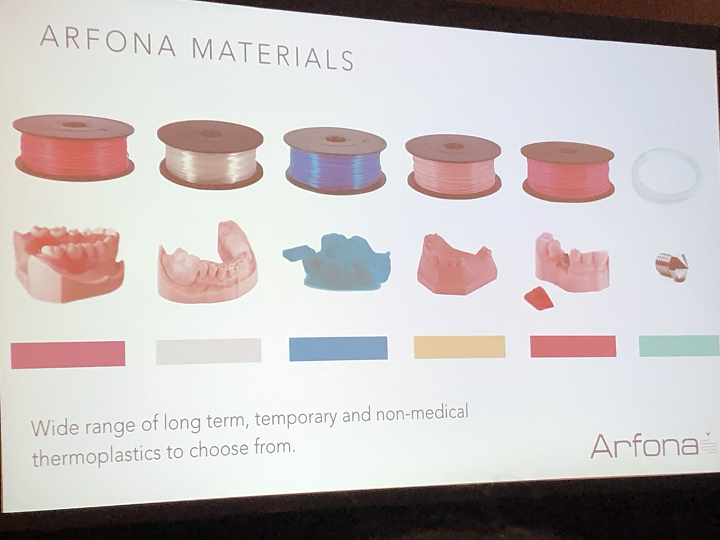
Then it was Wainwright’s turn to talk about dental 3D printing at Formlabs. He agreed with Marks that “FDM and thermoplastics have an incredible place” in the dental industry.
When the company was founded in 2012, its goal was to make professional-scale 3D printing accessible and affordable for everyone. Now Formlabs employs over 500 people at its multiple locations around the world, and has sold more than 50,000 3D printers.
Wainwright explained that the Form 3B desktop printer, optimized for biocompatible materials, has many dental-specific features, materials, and software, in addition to automated washing and post-curing systems “to help tie in end-to-end dental workflows.”

In addition, Formlabs offers dental materials, and launched its dental service plan (DSP) along with the Form 3B in 2019. Because there are high demands, the 3D printing process is complex, and the DSP offers support.
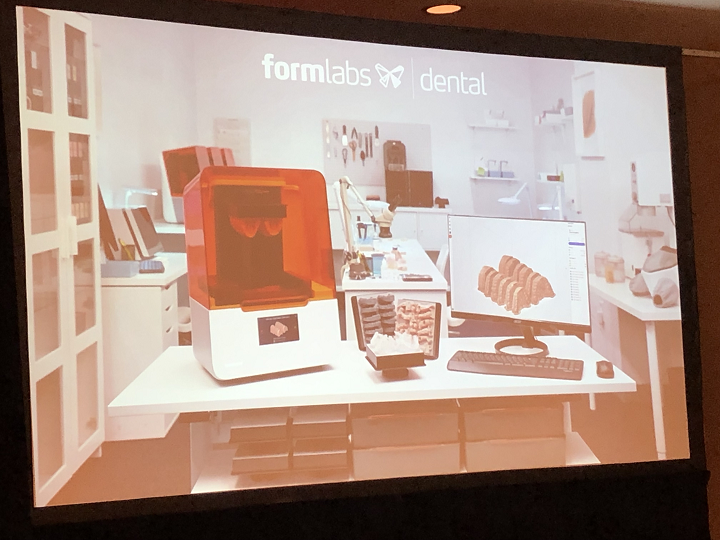
“We are committed to 3D printing for dental,” Wainwright stated. “We have over 20 people in the dental business unit. But we have the resources of a 500 person-plus company.”
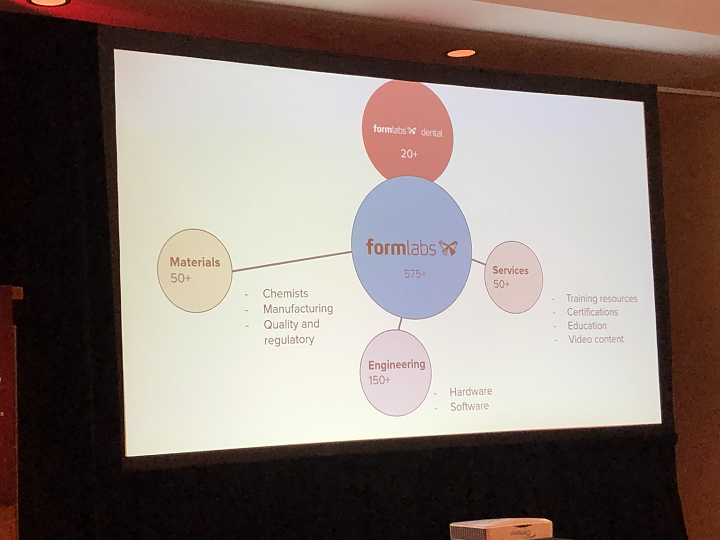
While most are made overseas, Formlabs Dental is now developing photopolymers in my home state, since the company acquired its main material supplier, Ohio-based Spectra Photopolymers, last year. Formlabs’ biocompatible Surgical Guide Resin is the company’s first material made in an ISO-certified facility.
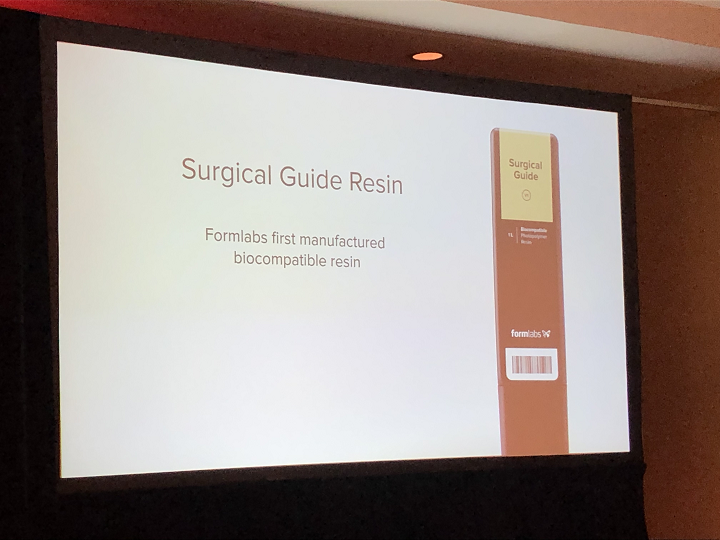
“It’s exciting to have intimate control over design aspects,” Wainwright said.
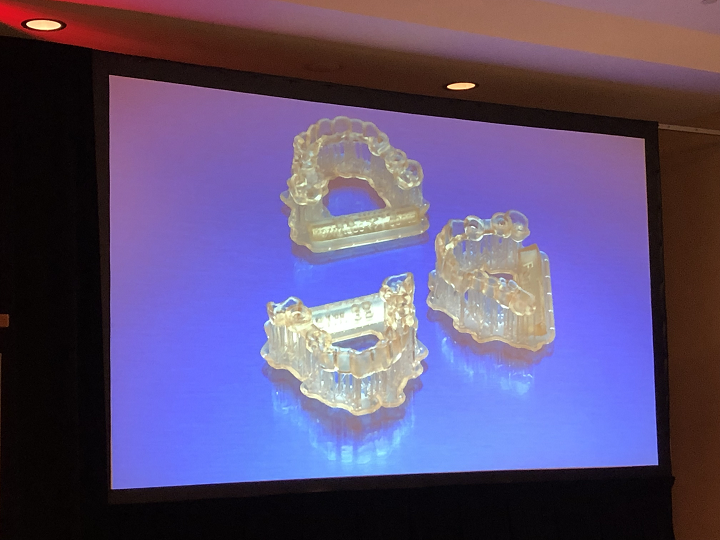
The image above is an example of the Surgical Guide material. Wainright explained that the light touch supports are very easy to remove, which means that there isn’t a lot of time wasted in post-processing.
He said that 36% of dental labs in the US use 3D printing technology, which makes them very “cutting edge.”
“There’s a ton of market opportunity for dental to go digital,” he said. “We have 30% of this market – we’re the biggest player in dental laboratories and will continue to grow, but compared to Invisalign, it’s not really that much.”
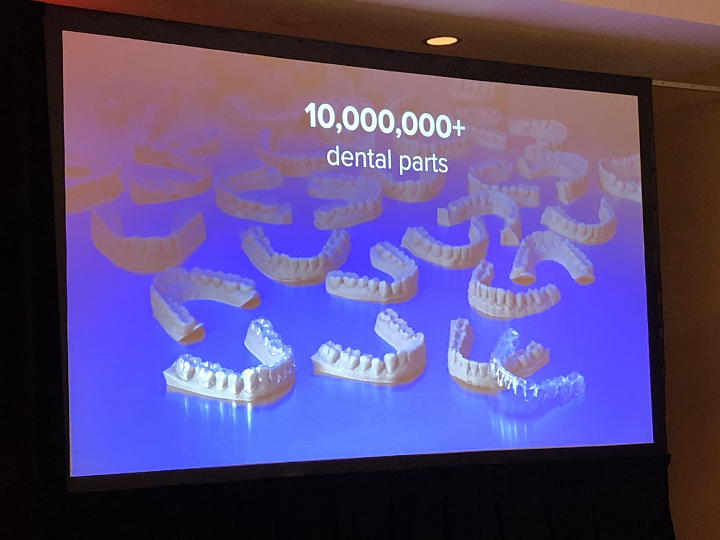
So far, Formlabs has 3D printed more than 10,000,000 parts for the dental industry. Wainwright predicts that in ten years or less, “everything in dental will be 3D printed.”
He reiterated to the room that Formlabs has “a whole host of materials” for dental applications, four of which are solely for fabricating models, which are “really critical to dentists.” As dental offices adopt intraoral scanning technology, it’s helpful to take the scan data and turn it into something physical. Wainwright mentioned that Formlabs’ Grey Resin can achieve fast, accurate prints, and that it’s good for thermoforming as well.

The company’s Draft material is “accurate enough to create models in less than 20 minutes,” which makes it perfect for creating retainers on the same day as a patient’s appointment. Model Resin is good for accurately restoring dental models, while the biocompatible Dental LT Clear Resin can be used to print occlusal splints in addition to models.

Formlabs’ Digital Dentures solution comes in multiple shades to match a patient’s teeth, and a full set can be 3D printed for less than $10, which Wainwright says is “really a game-changer.”
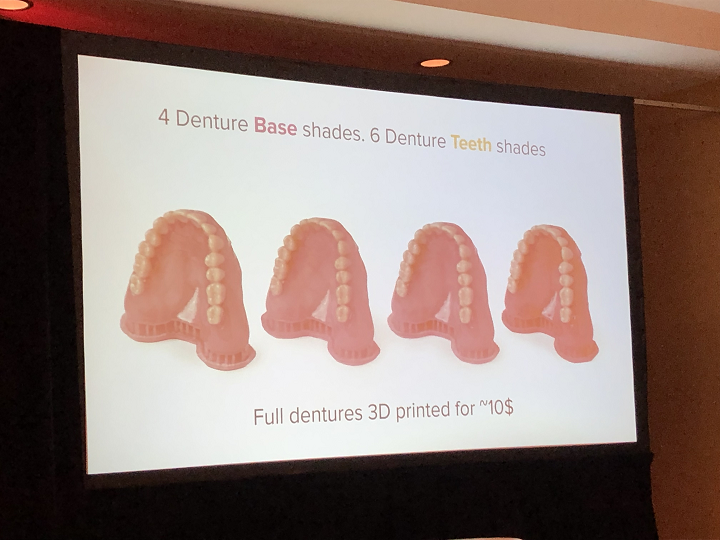
“We want to make treatments easier, better, and faster,” he said in conclusion.
“3D printing is still very early in dental, this is just the beginning. The materials will just keep getting better, it’s an exciting place to be.”
Then it was time to eat lunch and chat with other attendees…or, as I did, inhale food and then find a spot in the hallway near an outlet and get a little work done.
After the lunch break, I sat in on my last panel at AMS 2020, “3D materials for dental applications.” It was a panel of one – Gabi Janssen, Business Development Manager and Global Leader, Healthcare Segment Additive Manufacturing, for DSM Additive Manufacturing. She presented on digitalization in healthcare and dentistry.
She tried to play a short movie about what the company does, but due to technical difficulties there was no sound, so she narrated instead, explaining that DSM is “a material company” that also does a lot with nutrition – a brand behind the brands.

The company also has a biomedical department, which helps deliver advanced healing solutions for AM applications, including bioceramics, collagen, polyethylenes, polyurethanes, and hydrophilic coating.
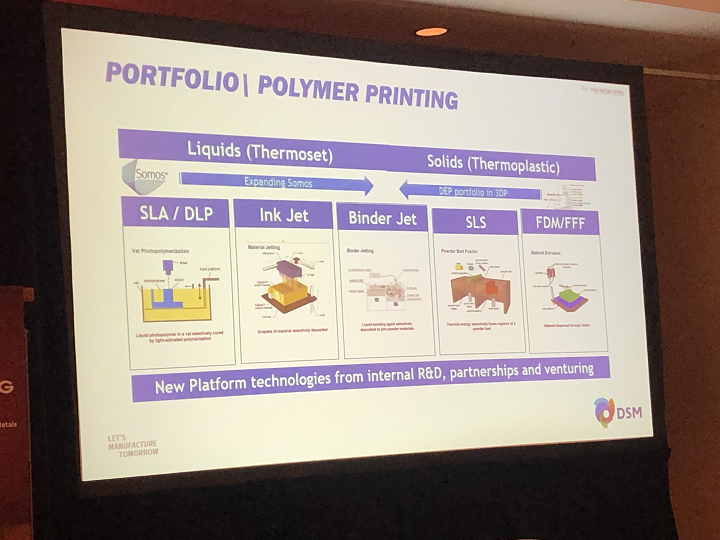
“What we have on the market is filaments,” Janssen said, pulling up a list of the dental materials DSM offers.

Several of the company’s products are geared toward the healthcare market, such as Somos BioClear for dental guides and anatomical models.
“So how do we develop a new material?” Janssen asked. “We’ve discussed 510(k) clearance materials, and you have to work all together. We look at the application, and determine what we need – printer, software, material – to fit what the end user needs.”
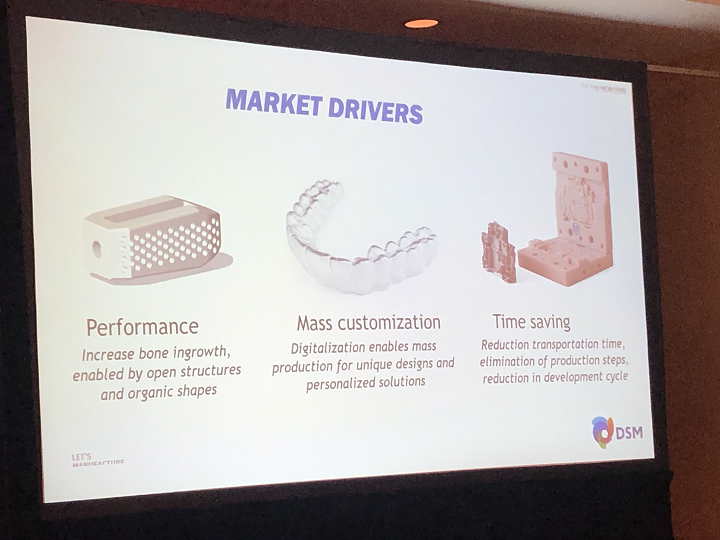
She pulled up a slide of the major market drivers in 3D dental printing – performance, mass customization, and time-saving.
“What kind of applications do we have in dentistry?” she asked.
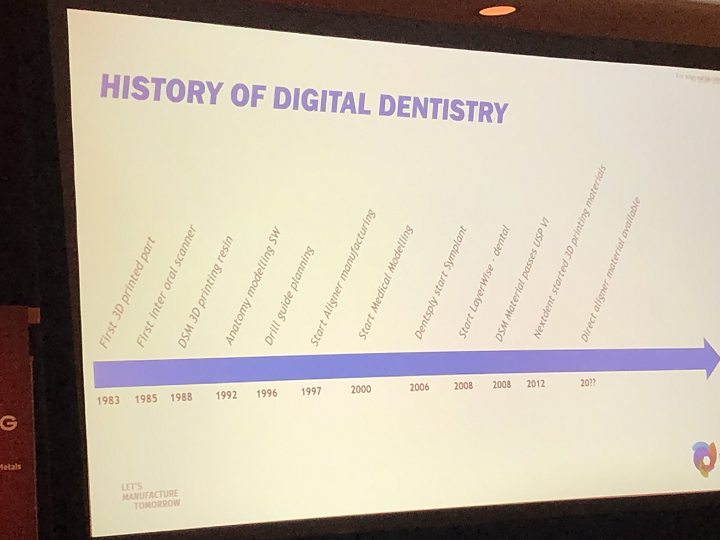
To answer her own question, she showed a brief history of digital dentistry, starting with the first 3D printed part in 1983, moving on to DSM’s 3D printing resin in 1988, the beginning of aligner manufacturing in 1997 and medical modeling in 2000, and DSM’s dental materials passing USP VI in 2008. For 2020 and beyond, hopefully we’ll see the availability of direct aligner materials.
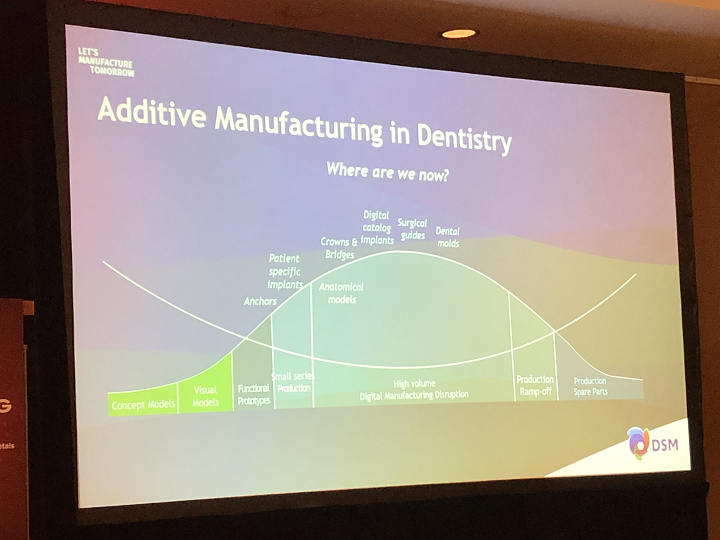
“I think there’s still a lot of data needed to show it’s good,” Janssen said about where the industry currently stands. “Reimbursement is difficult, we need this data to back it up.”
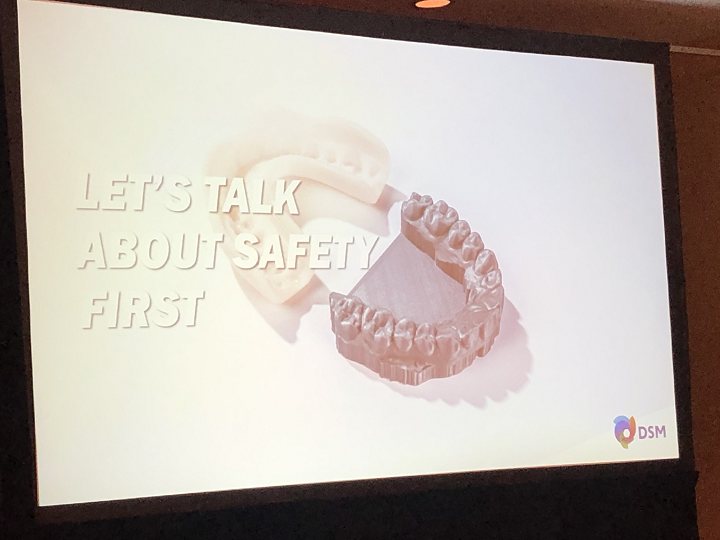
The topic of FDA clearance obviously came up a lot at AMS 2020. Janssen said that DSM has a resin that’s certified for use in dental bite guards, and a general purpose resin that isn’t certified but can be used to make FDA-cleared aligners.
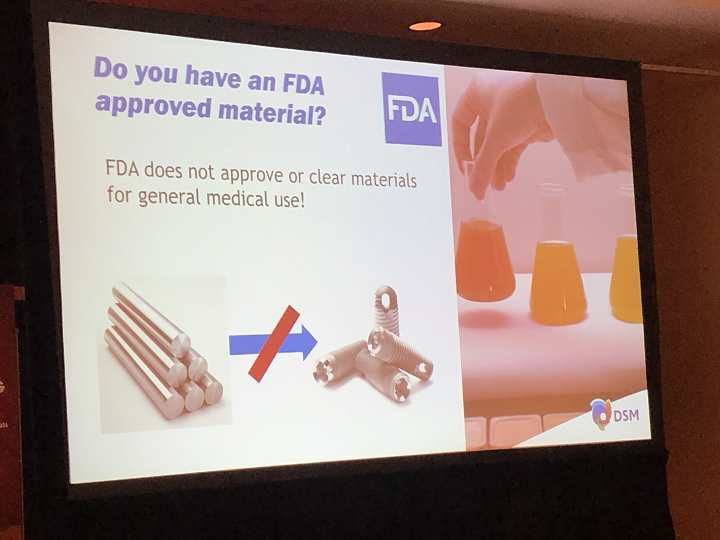
“The end device needs the clearance,” she reminded the room.
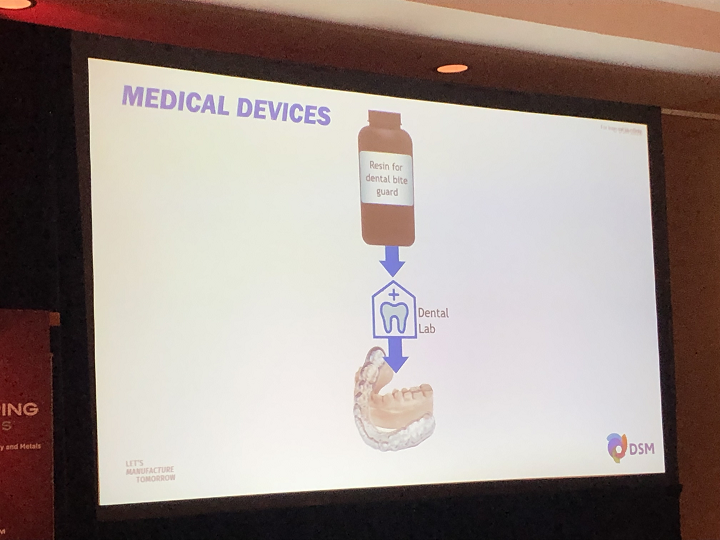
She brought up how Materialise was the first company to receive FDA clearance for software about 3D printing anatomical models for diagnostic use. Materialise Mimics inPrint translates the data for the model to the 3D printer. Then, combined with a specific printer and material, it’s possible to fabricate “the model they actually want within a certain safety margin.”
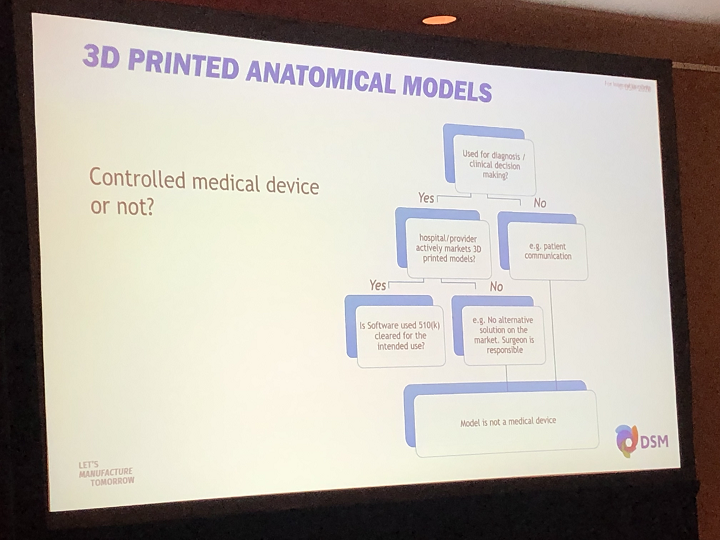
“But, if you want to print medical models, just for patient communication, it does not need to be cleared, because it’s not a medical device,” she explained.
The slide above explains what makes a medical device controlled, i.e. needs clearance, while the below slide lists some very useful definitions, including biocompatibility and risk.
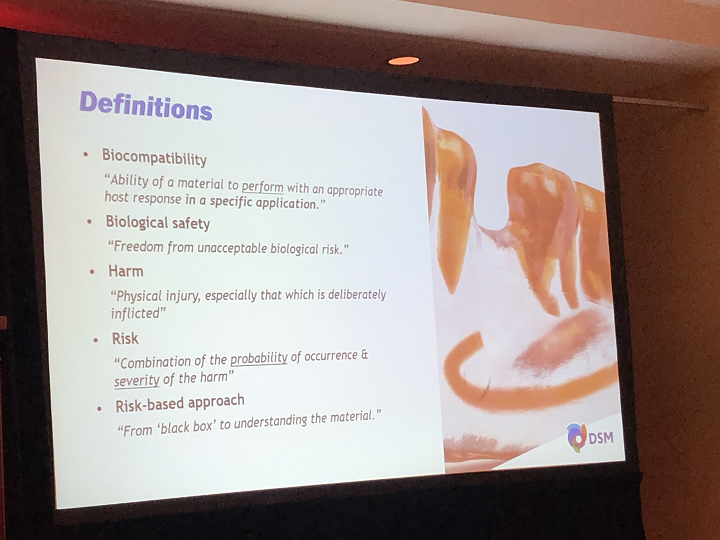
Janssen then brought up the “sometimes confusing standards,” such as ISO standards.
“Depending on what we do with the material, and how long it goes in the mouth, there are different risk associations,” she explained.
In terms of product classification, Class I is the least risky. But, the higher you go up in class, the more research is required to show that the 3D printable material won’t harm patients.
She said that the regulatory industry is changing to have more focus on software, with higher regulations for that software, because it “needs to be validated in combination with the material and equipment.” Additionally, there is more of a focus these days on understanding and managing risks, as well as reducing animal testing…always good news!
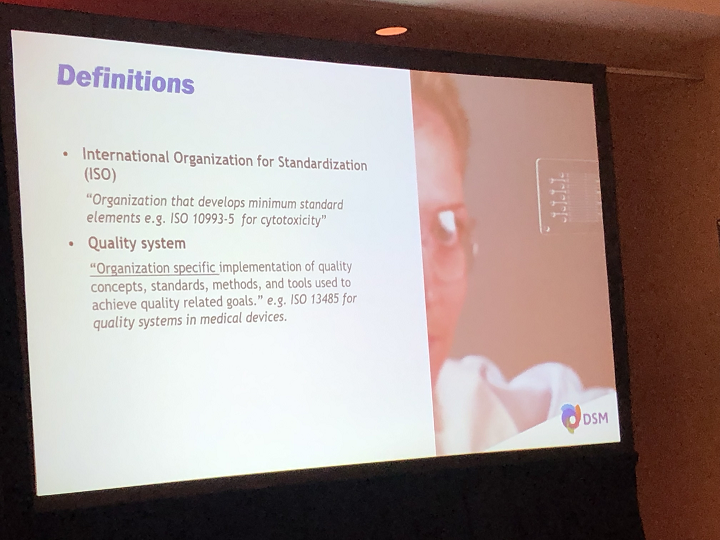
When choosing the proper filaments for your workflow, you should start by working with the dentist on treatment planning. Then, once the patient’s mouth has been scanned, you can create the design in the software. Then the build has to be prepared, which takes some patience and precision – you need to enter the optimal print parameters, and add supports if they’re needed. Then, after the print is complete, it needs to be removed from the bed, supports (if there are any) need to be taken off, and there may even be grinding and painting involved before the final quality check.
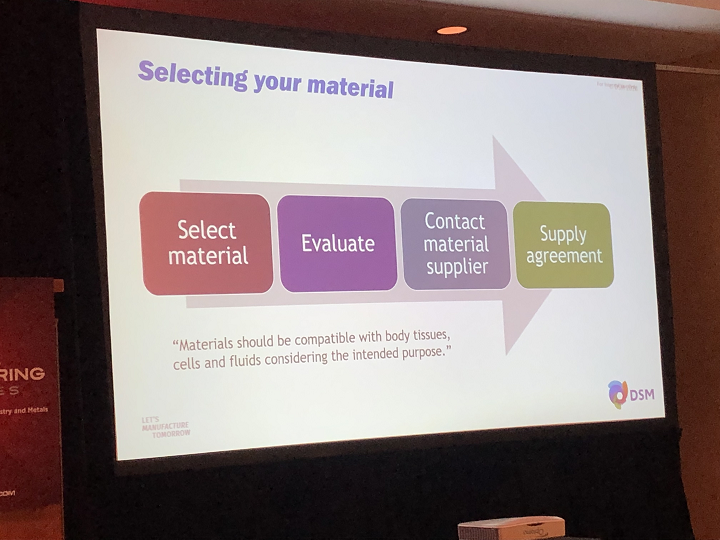
“Many process variables can impact the safety of the final end product,” Janssen noted. “So you need to understand the effect the material can have on patients.”
Finally, there are also plenty of steps to follow to ensure material safety in development, so it’s important to follow the instructions your supplier gives you.
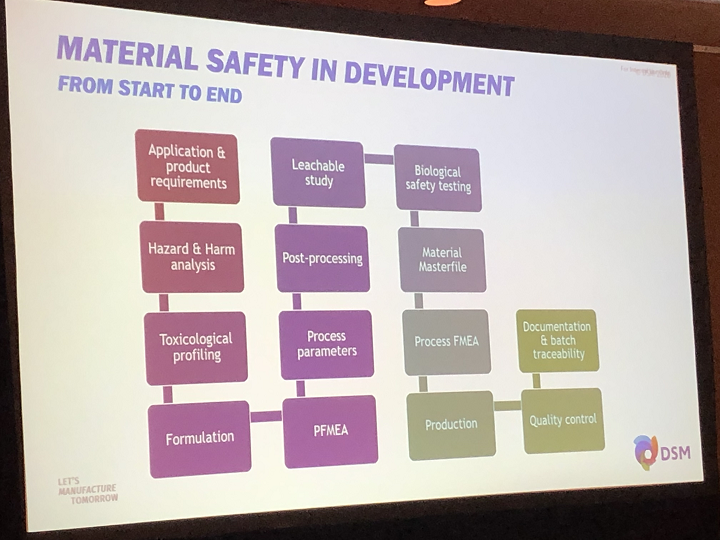
Then it was time for some questions. One attendee asked why dentists aren’t all adopting AM, since some products, like mouthguards, look pretty easy to make in the back office.
“This may look easy, but it’s actually not,” Janssen explained.
She went on to say that the product or device may not always “come out right the first time.” There are a lot of parameters to look at, and potentially tweak, in order to achieve the desired result. A lot of people can get frustrated if it doesn’t work right the first time.
“What we’re doing now – if you bring your design to us, we’ll do the tweaking for you, as our software has all of the maximum and minimum numbers needed for parameters,” she said.
3D printing thought leader and author John Hornick offered his take on the question, as he has some experience with the matter. He explained that most dental offices are private, though many dentists are consolidating their practices into larger ones, “and their appetite for spending money on these machines may go up.” But, SmarTech doesn’t think the average dentist will spend that much for larger, more expensive 3D printers. That’s why some companies, like Arfona, are working on simpler material extrusion systems.
Another attendee said that it seems like 3D printing companies are just throwing technology at various markets and praying that it sticks. Dentists want to be dentists, and not spend their time dealing with issues like print parameters and melted filament.
“We, as technology providers, need to raise our game and make this work for these people,” Janssen stated.
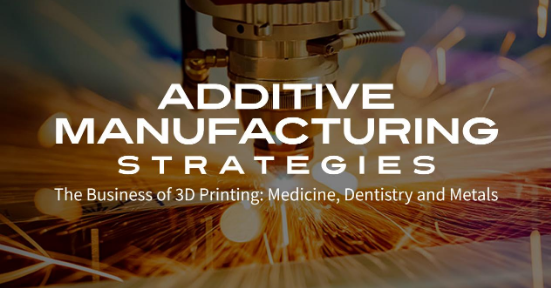
I think that’s a great note on which to end my AMS 2020 coverage – we, the AM technology providers, need to show the rest of the world how 3D printing can work for their industries.
We hope to see you next winter for Additive Manufacturing Strategies 2021!
Discuss this and other 3D printing topics at 3DPrintBoard.com or share your thoughts below.