3D printing in micro gravity is garnering growing interest from scientists and aerospace engineers—and especially as such activity grows at the International Space Station. German and French researchers explore the topic of printing in microgravity in the recently published, ‘Enabling the 3D Printing of Metal Components in µ‐Gravity.’ Concerned with creating strategies for working and living in space, the research team delves into the possible challenges of additive manufacturing in metal—with little gravity.
Additive manufacturing has been a boon to many different companies and organizations around the world, but especially the aerospace sector and NASA. Because creating spare parts can be so expensive and so challenging, 3D printing and AM processes are enticing with benefits like exponentially greater affordability, speed in production, and more, including the integration of robots.
In this study, the researchers aimed to create metal parts in space from 1 to 500mm. Larger structures could be created too, allowing for almost all parts on a spacecraft to be fabricated via laser beam melting (LBM), and in a wide range of materials—from titanium to nickel-based alloys.
LBM technology is currently being used in many different applications, including:
- Automotive
- Aerospace
- Tool manufacturing
- Medical
“The selection of LBM as a process for fabricating aerospace components was primarily based on the weight ratio between the raw material required for machining a component and the weight of the component itself. For conventional fabrication technologies, this ‘buy‐to‐fly’ ratio can be as high as 15–20 for flying components, adding a lot of cost to the component for material and machining,” state the researchers.
Offering a buy-to-fly ratio of almost 1, LBM processes offer a list of benefits, beginning with the fact that parts can be manufactured in nearly any shape, created from powder that results in little waste, if any. Dealing with spare parts is key—especially today at the ISS, where in the past shipments have been known to fail due to unsuccessful launches.
“Even losing a tool in the station or during a spacewalk may be problematic for astronauts and mission,” state the researchers. “Despite careful tracking, in average roughly two percent of all spare parts in the ISS, summing up to about 2000 components, are at any time lost.”
3D printing is the logical choice as 3D files can be sent via email for parts to be created on demand and on site. With a ‘virtual tool-box’ to work from, as well as relying on files sent from Earth, astronauts could see their jobs more streamlined in the future—and especially if they are living as far away as Mars where resupply missions are rare or impossible. Much of this depends on success in microgravity manufacturing, however, along with the requirements for 3D printers and materials to be sent along with the crew.

Time needed to reach the ISS, Moon, and Mars as function of their distance to Earth. The values for the required travel times to reach a respective object are based on literature values for different flight trajectories and maneuvers. The Earth–Moon distance considered is at the perigee; for the Earth–Mars distance, filled symbols show the average minimum distance, which is reached every ≈26 months. Open symbols show the maximum distance Earth–Mars and hypothetical flight time, although it is to be expected that flight missions are and will be feasible only when Mars is close to its minimum distance.
Currently, the ISS uses an FM 3D printer that was quite famously delivered by Made in Space. The astronauts have also quite famously fabricated numerous 3D printed parts, mainly in the form of tools, with a wrench being their first success. And while that has been an enormous achievement, the FDM printer may be too basic for their expanding needs in the future, with a priority on functionality.

Schematic of the powder deposition unit. The area of the porous building platform for the powder deposition was 106.5 × 85.5 mm2.
“Laser‐based AM in particular would enable the fabrication of high‐performance metals and thermoplastic polymers in space,” state the researchers.
While powder has previously been eschewed as too difficult for production in space, the research team explains that new advances could make LBM processes suitable for the in µ‐g environment now, using a technique that could stabilize powder in space by creating a flow of gas throughout the powder bed. A porous building platform is used as a filter for ‘fixation of metal particles in a gas flow.’
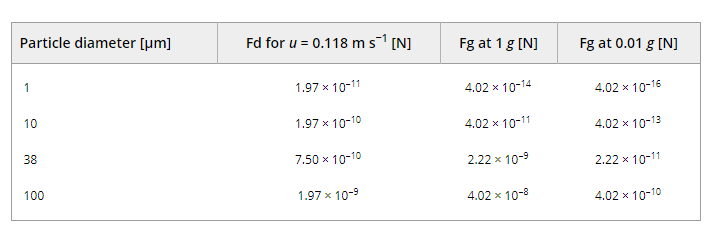
Drag force Fd and gravitational force Fg compared for stainless steel spheres at different acceleration values and for different particle sizes
“It could be shown, that the drag forces provided by the gas flow are comparable or even exceeding the forces acting on the particles in µ‐g acceleration conditions (<0.01 g) for particles with a diameter of 38 µm (which is the D50 of the powder used in this work),” concluded the researchers.
“In this study, the worldwide first metallic tool, a 12 mm wrench has been manufactured by LBM at µ‐g conditions. Moreover, other parts have been manufactured at different accelerations provided by a parabolic flight, that is, hyper gravity (1.8 g), µ‐g (<0.01 g), and 1 g. In a first survey of the parts microstructure, no significant deviations from a part manufactured at 1 g conditions have been found. Hence, the current work has presented the first results on the feasibility of an LBM process for additively manufactured ready to use metal parts in space.”
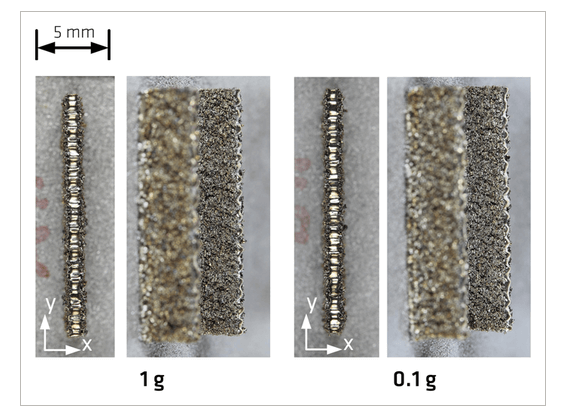
Specimens manufactured in different g conditions, top view, and inclined side‐view; left: 1 g; right: µ‐g.
Metal 3D printing encompasses many different techniques today aside from that of space, and for a wide variety of different industrial purposes—and with many different types of powders and materials that are being continually still being experimented with here on Earth, from ceramic to nanocomposites to copper.
What do you think of this news? Let us know your thoughts! Join the discussion of this and other 3D printing topics at 3DPrintBoard.com.
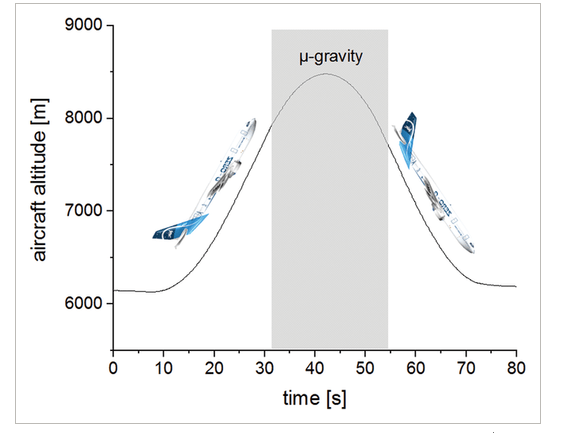
Schematic of an airplane flying a maneuver defined as “parabola.” The airplane image is courtesy of Novespace.

a) Top view of the deposition chamber, showing the laser scanner and optics, two oxygen sensors, two pressure gauges, and two overpressure safety valves b) view of the deposition unit during cleaning after a parabolic flight, showing the wrenches produced by LBM still partially embedded in the powder bed c) top view of the porous metal base plate and of the wrenches manufactured in µ‐gravity d) 12 mm wrench manufactured in µ‐gravity, after separation from the base plate. The base plate has a size of 106.5 × 85.5 mm2.
[Source / Images: ‘Enabling the 3D Printing of Metal Components in µ‐Gravity’]
The post 3D Printing in Space: Metal Printing in µ‐Gravity Shows Promise appeared first on 3DPrint.com | The Voice of 3D Printing / Additive Manufacturing.