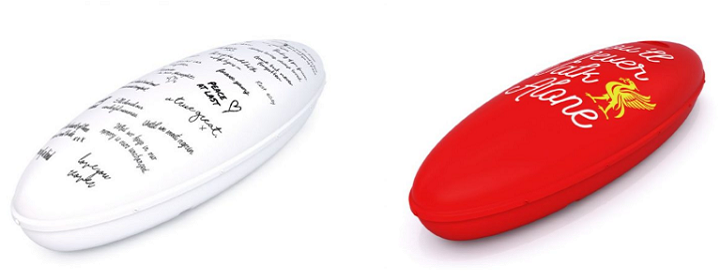
While the way we live is vastly different from the way we did 100, 50, and even 20 years ago, the way we say goodbye to loved ones when they’ve passed away is still pretty much the same. Funerals are not easy for a number of reasons, but the last thing on anyone’s mind should be the cost of these emotional events and ceremonies; unfortunately, that’s not often the case. According to SunLife, funeral costs have shot up over 70% in the last decade.
With this in mind, Koffin, a Liverpool startup founded by artist Gina Czarnecki in 2014, is working with business program LCR 4.0 and using Industry 4.0 technology – specifically 3D printing and advanced material testing – to help cut down on the cost of funerals with customizable, biodegradable eco-coffins.
“Funeral prices are increasing drastically, and people deserve the right to a personalised send-off that isn’t going to break the bank. Planning a funeral can be a difficult time, but we’ve found that having something tangible to take control of and make your own improves people’s wellbeing and peace of mind,” said Czarnecki.
“The work with LCR 4.0 has enabled us to test our design that creates a cost-effective alternative that emits less CO2 emissions than a natural plant.”
Together with brand consultant Clare Barry, Czarnecki set out to redesign the coffin – typically a narrow wooden box. But a KOFFIN, according to the startup’s website, is “a light, eco-friendly capsule made from bioplastic,” which is definitely different from the more traditional, pricey Victorian-style coffins we’re used to seeing.
“The way we currently bury or cremate our loved ones is poisoning the earth,” the Koffin website states.
“Besides… your funeral is your last hurrah, right?
“…So shouldn’t your coffin be as unique as you are?”
The 100% biodegradable KOFFINS were created to help people take back their rights to a personal, affordable funeral. They are made with a lignin-based biopolymer and don’t require any glues or metals to hold them together. They produce less ash residue than other coffins, are leak-proof without having to use wax linings, and will decompose in the earth just like natural tree wood. Additionally, the oval capsules can be completely personalized with different colors, hand-written messages, photographs, and a variety of attachable, 3D printed decorations.
During the development of the KOFFIN prototype, the startup was in need of expert technical support during testing. So Koffin turned to LCR 4.0, partially funded by the European Regional Development Fund, and its partners Sensor City and Liverpool John Moores University to test its inexpensive, sustainable prototype, and use 3D printing for added personalization.
“Koffin is unlike any other start-up that we’ve helped to date,” said Jaime Mora-Fernandez, LCR 4.0 product design engineer at Sensor City. “The work carried out illustrates how new technologies can help businesses in a wide variety of sectors transform the way they approach the design and manufacturing process.”
The LCR 4.0 team at Sensor City helped Koffin complete a finite element analysis (FEA) of the design to find the right material thickness to withhold sufficient pressure. This helps reduce material costs, which will trickle down to lower consumer costs. Then, the partners tested the prototype, and completed a report that concluded the material’s thickness would be robust enough for its purpose.
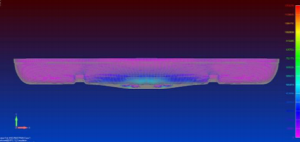

After four long years of development, the startup has officially gone into production with its first run of biodegradable, customizable, eco-friendly KOFFINs.
“Our involvement with the LCR 4.0 scheme has resulted in outputs being produced in a timely and efficient manner, using expert advice and linking disciplines seamlessly,” said Czarnecki.
Starting today, 20 of the KOFFINs, decorated through a national public call-out, will be displayed at the Oratory, next to the Anglican Cathedral, in Liverpool; some of them even bear some interesting 3D printed decorations. Soon, the startup will also launch a Kickstarter campaign in order to raise the necessary funds to take the KOFFINs to market.
This isn’t the first time that 3D printing has been utilized in the death care industry. We’ve seen 3D printed urns, 3D printed busts of the deceased, and even 3D printed jewelry made from the ashes of our loved ones. As 3D printing also comes into play often with sustainability efforts, the KOFFINs seem to be a perfect mix of life and death.
Discuss this story and other 3D printing topics at 3DPrintBoard.com or share your thoughts below.