Xaar is a Cambridge based company that makes many different kinds of inkjet head. It is also has invested in High Speed Sintering (HSS), the Factum machine both pioneered by Neil Hopkinson to increase throughput in 3D printing. What may come as a surprise to many is that apart from HSS, Xaar is looking to partner with more 3D printing businesses. The company is actively seeing to develop applications with OEMs and industrial partners through which new inkjet-based 3D printing technologies are commercialized. The company’s business development manager Mike Seal explained Xaar’s position, capabilities and vision to 3DPrint.com at the TCT Show. With new inkjet technologies ramping up to be the next area to be commercialized and inkjet in metals one of the hottest areas for investment currently inkjet is a very exciting technology now. Inkjet piggybacks on billions and decades of investment in new and interesting ways to get lots of different inks to stick in a coherent way to lots of different things. If we just make that a 3D technology then we can expand the space of the makable significantly. Uniquely Xaar is open about its inkjet heads letting you play with them and have settings information so you can actually develop a new technology. The company is also open to working directly with you in making a material or substrate work in inkjet.
A HSS part
Why is Xaar interested in 3D printing?
“It’s a rapidly growing, exciting digital industry and plays to Xaar’s strengths. Inkjet technology is very suited to the requirements of the 3D printing industry as it transitions from prototyping to volume manufacturing. Inkjet printheads are capable of accurately ejecting droplets of fluid thousands of times per second, whilst the capability of using multiple printheads on a single system enables scale and volume production.
The digital inkjet market has been established for decades, and the technology has been used across a wide range of applications, such as for printing graphics, ceramic tiles, packaging and labels. Digital inkjet has already proven itself in a number of harsh environments where high volume is critical. Systems and components continue to be prohibitively expensive to potential adopters. In comparison to systems that use lasers or similar, inkjet printheads have a significantly lower purchase price and prove much more cost-effective over the lifetime of machines. Xaar in particular has a number of advantages that are especially useful for this market. Xaar’s unique printhead architecture and two key technologies enable more choice for the end user – specifically, access to a wider range of materials which is growing as the inkjet technology itself advances.

-
Hybrid side shooter architecture delivers a higher fluid viscosity capability and awider fluid viscosity range than other inkjet printheads
-
High Laydown Technology enables the printhead to jet even higher viscosityfluids
-
TF Technology – enables higher particle loading fluids such as metals andpolymer additives
-
Improved productivity enabled by High Laydown Technology, TF Technologyenables part uniformity as well as low production maintenance and reducedproduction downtime.”
3. What is HSS?
“High Speed Sintering works by depositing a fine layer of powder onto the surface of a powder bed. An inkjet printhead then selectively prints an infrared (IR) absorbing fluid directly onto the powder surface. The entire surface is irradiated with IR energy, causing only the printed areas to melt/sinter; the unprinted areas remain as powder. This process is repeated layer by layer until the build is complete. Un-sintered powder is then removed to reveal the final part(s). Parts can be produced using a wide range of polymers from elastomers to engineering grade polyamides. Strength and stiffness are comparable to other
polymer powder-based approaches while ductility (Elongation at Break) is often significantly higher. The process requires no support structure and features as small as 0.5 mm can be easily reproduced.
High Speed Sintering for 3D Printing applications does not require tooling, driving down set-up time and costs by replacing multiple processes. It also allows for faster product design and modification, improves manufacturing efficiency, and enables the creation of on-demand, high-value parts with geometry freedom. All this contributes to a faster time-to-market and increase in ROI compared to traditional additive manufacturing processes.”
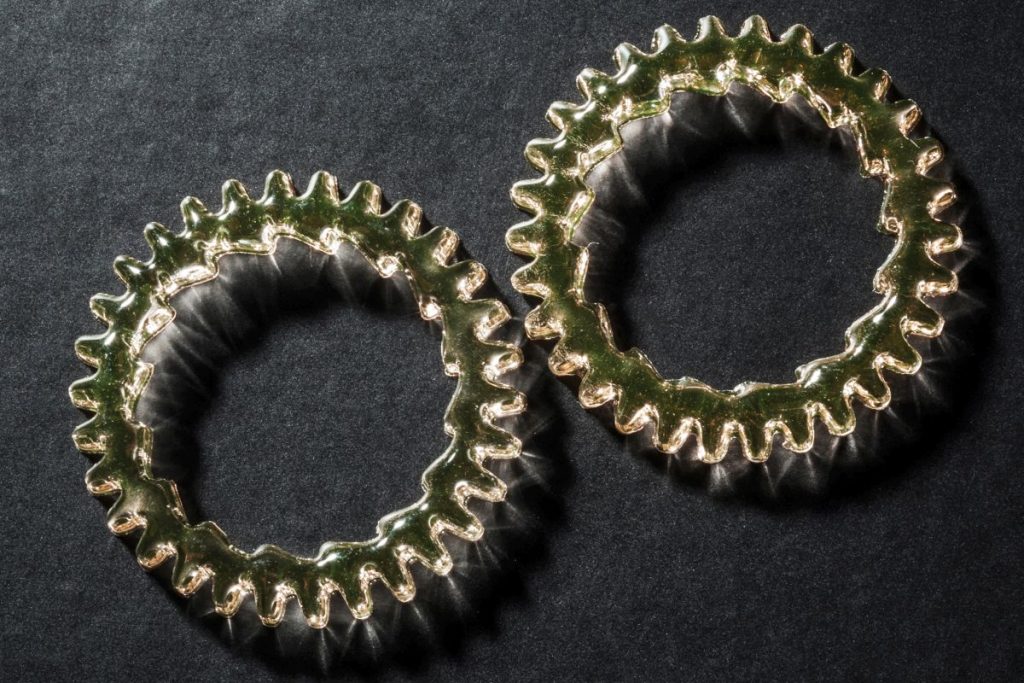
4. So separately from HSS, Xaar would like to engage with the 3D printing
community?
“Yes, definitely. We are looking to engage with users of the full range of 3D printing technologies and with partners from all aspects of the process, including OEMs, end- users, 3D print bureaus, materials suppliers and fluids manufacturers.”
5. What kind of companies and people would you like to work with?
“All kinds – anyone with the drive to innovate and collaborate. We offer an open model for fluids and electronics which means we do not insist our partners develop with prescribed fluids and electronics.”
6. When developing new materials for inkjet how does Xaar work with people?
“We follow a five-step process which could start with a very open question such as “Can you jet this fluid?” and then continue with a straightforward dialogue. We then look to evaluate the fluid using fluids physicals measurement, complex rheology and materials compatibility testing. After that we’ll look at jetting optimisation through things like waveform configuration and in-flight droplet visualization followed by sample production. The final two stages are where we look at the details of the specific application and transfer the knowledge and capability over to the partner we are working with. So our five step process goes from conversation right through to commercialisation.”
7. Do you want to work with OEMs to make new inkjet 3D printing technologies?
“Yes, we do, and it is certainly something we have done in the past. For example, developing customised printheads for a specific application by way of a funded programme.We offer an ‘open’ model whereby our partners are able work with the
fluids and electronics of their choice with our printhead technology.”
11. What types of inkjet 3D printing technologies could there be?
“Drop-on-Demand is a hugely flexible inkjet technology that continues to reach new
heights – it has lots more to give!”
13. Batteries?
“Technically yes, provided that fluids are correctly formulated. We have jetted fluids used in the manufacture of batteries, fuel cells and photovoltaics. Inkjet lends itself very well to layer, coating and lamination based applications.”
14. How about coatings for parts?
“Yes, it is possible to use inkjet as a more controlled method of spray coating. Currently, inkjet is used for product printing and direct-to-shape applications whereby a graphical image, text or a coating is applied to the outside of a three dimensional
shape.”
15. What are some cutting-edge inkjet applications being developed now?
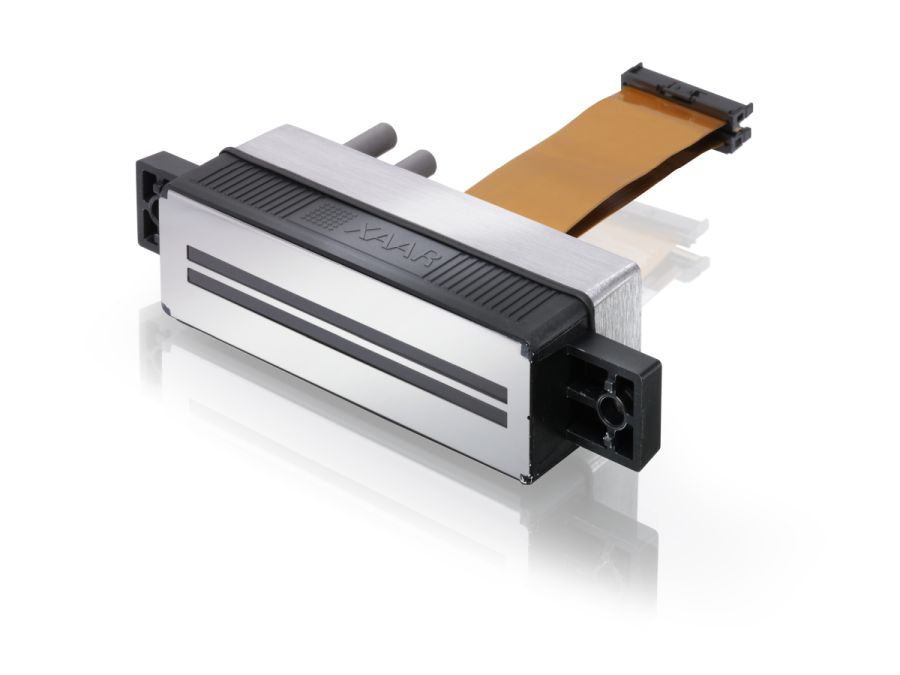
“We are unable to talk about specific applications due to reasons of confidentiality. However, there is significant focus on Flat Panel Display technology, and also on applications in the pharmaceuticals, biomedical and semiconductorindustries.”