3D Printing News Briefs: July 27, 2018
We’ve got plenty of awards and other business news for you today in 3D Printing News Briefs. Sinterit and ViscoTec each received awards for their technology, while Arkema announced that it is opening a 3D Printing Center of Excellence at its Pennsylvania facility. Vectary and Sketchfab are integrating, and Xometry is now offering SLA 3D printing. Finally, OPEN MIND Technologies has introduced its latest hyperMILL CAM software.
Sinterit Lisa Receives Award from All3DP
Sinterit, one of the fastest growing manufacturers of SLS 3D printers, just received the “Best Desktop SLS 3D Printer Summer 2018” award for its Lisa 3D printer by All3DP. The award shows that the company is moving in the right direction, and confirms that the Lisa is the perfect choice for 3D printing professionals looking to upgrade to SLS technology without breaking the bank. Even better for Sinterit: the award was announced in the final week of a pre-order period for its upgraded Lisa model, which will feature better hardware, bigger 3D prints, and easier maintenance.
“All3DP is happy to present the Sinterit Lisa with the award for Best Desktop SLS 3D Printer on the market. We recognize the Sinterit team for their tremendous work in making SLS 3D printing technology more affordable and accessible,” said Tyler Koslow, Editor at All3DP. “Additionally, their recent update to the Sinterit Lisa and development of the new Sinterit Lisa 2 PRO suggests that they will remain a market leader for a long time.”
ViscoTec Awarded Special Title Two Years Running
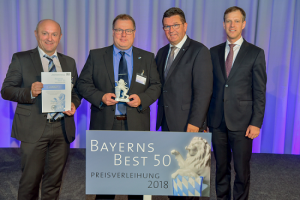
Georg Senftl (holding certificate) and Martin Stadler (holding lion) accepted the award on behalf of all ViscoTec employees.
For the second year in a row, German company ViscoTec, which specializes in pump and dose technology and has 3D printing viscous liquid products for silicone and other materials was awarded the “Bayern’s Best 50” title. For 17 years, the Bavarian Ministry of Economic Affairs has honored the 50 most dynamic, medium-sized companies in Bavaria, and the jury considers criteria such as number of employees, turnover, and social and economic contributions. ViscoTec, and the other 49 winning companies were personally awarded the title, a certificate, and a Bavarian porcelain lion by Bavaria’s Minister of Economic Affairs, Energy and Technology Franz Josef Pschierer at a recent event in Schleißheim Castle.
“Our employees all over the world actively help us to be such a successful company every day and that we will continue to develop very well in the future. Special thanks also go to our partners and customers. Their partnership with ViscoTec is constantly driving us forward. This motivates us not to stand still, to open up new possibilities and to find solutions for the daily challenges,” said Georg Senftl, Commercial Director of ViscoTec Pumpen- u. Dosiertechnik GmbH. “Last but not least, the innovative climate in the Inn-Salzach region contributes to the continuous development of companies like ViscoTec.”
Arkema to Open 3D Printing Center of Excellence
This Monday, July 30th, speciality chemical and advanced materials developer Arkema will be holding the grand opening for its new 3D Printing Center of Excellence. The center will be located at the Exton, Pennsylvania facility of its Sartomer subsidiary, which designs engineered resins for UV-curable additive manufacturing under its N3xtDimension brand. The 3D Printing Center of Excellence will work to advance 3D printing resins technology and be home to most UV-based 3D printing technologies, such as Digital Light Processing (DLP), stereolithography (SLA), and HP’s Multi Jet Fusion (MJF). It will offer a collaborative space for developing custom resins, and complete the company’s worldwide R&D network, which is dedicated to developing advanced 3D printing materials.
“Sartomer is a historic partner for 3D printing pioneers. We’re launching the 3D Printing Center of Excellence to deepen our support of the visionaries working to develop innovative 3D printed materials,” said Sumeet Jain, Global Director, 3D Printing at Sartomer.
Vectary Integrates Sketchfab
Online 3D design tool Vectary is giving its users access to thousands of new 3D models, as it has now integrated Sketchfab, the world’s largest platform for interactive 3D content. Vectary users can connect to the Sketchfab library and import hundreds of thousands of 3D models with one click, as well as export, publish, and even sell their own 3D work on Sketchfab. Vectary CEO Michal Koor, who co-founded the tool in 2014 with Pavol Sovis said, “Easily importing Sketchfab 3D models in the Vectary 3D tool can be a great way to create design concepts and bring more inspiration to their work. Exporting their Vectary models to Sketchfab gets them exposure to a larger audience, which can mean an increased customer base and new income possibilities by selling their work on one of the best 3D marketplaces available.”
Xometry Adds SLA 3D Printing to List of Services
3D printing service provider Xometry has added stereolithography (SLA) 3D printing to the list of 3D printing processes it provides. Versatile SLA technology offers higher resolution 3D printing, which will allow Xometry’s customers to achieve prints with good surface finish and fine detail – perfect for production parts and prototypes. The technology also enables you to print large products and parts and can create complex parts, to meet tolerances of +/- 0.004” or +/- 0.001” per inch, in a single operation.
Xometry also offers plenty of SLA-friendly materials, such as the Accura and Somos brands. Try it out today – upload your 3D CAD file to Xometry now to get an instant SLA quote.
New Version of hyperMILL CAM Software Released
Germany CAD/CAM software solutions develop OPEN MIND Technologies AG has released the latest version of its advanced CAM software, hyperMILL 2018.2, which provides more machining efficiency and several new enhancements and features. 3D Z-level Shape Finishing, available in the hyperCAD -S module, now comes with automatic face extension to automatically extend selected milling surfaces during CAM programming, and can now also support conical barrel cutters.
This version also provides a “V sketch” command, which allows users to make easy changes to turning contours and milling boundaries by assigning geometric constraints to 2D contours. Other enhancements to the -S module include being able to measure and record distances between two shapes, like meshes, solids, and face models.
Alan Levine, Managing Director of OPEN MIND Technologies USA, Inc., said, “Keeping the hyperMILL suite at the forefront of CAM technology, we are pleased to offer our customers improved CAM strategies and enhanced CAD tools for even greater machining productivity through our new release of hyperMILL 2018.2.”
Discuss these stories and other 3D printing topics at 3DPrintBoard.com or share your thoughts in the Facebook comments below.
Cloud-Based Simulation and More Among New Features in Netfabb 2019
Netfabb has been a popular software program even since before it was acquired by Autodesk, and each year it offers more and more features to its users as Autodesk brings out new versions. Recently, Autodesk introduced Netfabb 2019, which has several new features in addition to updates to some of its existing features. The new release focuses on improved productivity and updates the simulation and latticing, two of the software’s most significant features.
Simulation is a critical part of the additive manufacturing process, particularly metal additive manufacturing. It saves time and materials by allowing the user to run through a process before running it for real, and to smooth out any issues that the software predicts. Netfabb subscribers beginning at the Premium tier can now take advantage of cloud-based, multi-scale, metal powder bed process simulation.
“With metal additive manufacturing, the stakes are high. Materials are expensive and lead times are continually compressed,” says Autodesk. “The ability to anticipate your outcomes can often save the day, and the project. From additive consultancies to industrial innovation labs and research facilities, industry leaders turn to Netfabb Simulation. Now, this same simulation capability is available in the cloud, allowing you the ability to pay for simulation only when you need it.”
Netfabb simulation uses a multi-scale modelling approach. Users can input machine parameters and material properties to develop their PRM files, then simulate large, complex parts “with a fully predictive part-scale simulation which captures the complex thermal and mechanical interaction between parts during the build process,” says Autodesk. The cloud credit cost for a PRM file is fixed, but part-scale simulation depends on the complexity of the parts being submitted.
In addition, the PRM library has been redesigned to give the user visibility into process parameters. PRM files can now be edited directly from the library.
Manual latticing is now available to customers at the Premium tier, and all Netfabb lattice functionality is now available from a single location. Additional updates allow for better productivity, such as:
- A replay function that allows regeneration of manual or script-based supports after a change in geometry is made, even after the support strategy has been finalized.
- Supports can be deleted by criteria
- Shared viewing and cloud storage
- A new My Machines workspace that streamlines the process by allowing the user to define only the machines they have access to. The user can also categorize machines by functions and assign repair or support scripts accordingly.
Netfabb 2019 also includes a new workspace for the DMG Mori Lasertec 30 and features updated Form2 integration, giving the user direct access to Form2 from Netfabb.
That’s only a few of the new and updated features that Netfabb 2019 offers – for a full list, you can find out more here.
Discuss this and other 3D printing topics at 3DPrintBoard.com or share your thoughts below.
[Source/Images: Autodesk]
KAIST develops VR platform for 3D sketching in thin air
3D Printing News Briefs: July 20, 2018
We’re starting out with some construction news in today’s 3D Printing News Briefs, then following that with a little business, a little metal, and a little 3D design. Russian firm AMT-SPETSAVIA has updated two of its construction 3D printers, and the University of New Brunswick has chosen a Concept Laser 3D printer to use for its upcoming research. Mass Portal’s software team went through a reorganization, and attendees learned all about lightweight aluminum material at the recent AMAP forum. Finally, users of browser-based SelfCAD 3D software can access the MyMiniFactory design library…and share their own work there as well.
Spetsavia Completes Updates on Large Construction 3D Printers
Three years ago, Russian firm Spetsavia presented its home construction methods and 3D printers at the 3D Print Expo. Now, the group of machining and 3D printing companies collectively known as AMT-SPECAVIA has updated its range of construction 3D printers (Construction Objects Printing or COP) to introduce two new large-format models. The S-300, with a “working field” of 11.5 x 11 x 5.4 m, is able to print directly on the foundation of buildings up to two stories and 120 square meters, while the S-500 features an 11.5 x 11 x 15 m field and can 3D print buildings up to five, or even six, floors. However, the latter can be increased to a working field of 40 x 11 x 80 m, which Spetsavia says makes it “the largest 3D construction printer in the world.”
“New models of the S series are essentially the next generation of building printers. We’ve always been asked for a solution for multi-storey construction,” said Alexander Maslov, the General Director of AMT-SPETSAVIA. “Now we declare with confidence that such a solution exists! The AMT S300 and S500 printers are high-performance equipment with unprecedented capabilities and competitive price. During the development we’ve taken into account the wishes of the developing companies, at the same time maintaining the inherent reliability of our equipment, ease of management and maintenance.”
Both the S-300 and the S-500 have a direct flow print head for increased productivity, in addition to a new feed station that prepares the concrete mixture. The first shipment of the S-500 is scheduled for this fall, and a team of engineers will accompany the 3D printer to the customer for training.
University of New Brunswick to Use Concept Laser M2 Cusing
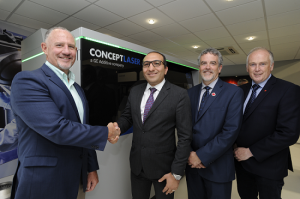
L-R: Keith Campbell, Senior Sales Director, GE Additive; Dr. Mohsen Mohammadi, Director of Research and Development for the Marine Additive Manufacturing Centre of Excellence; Hart Devitt, Director of Industry and Government Services; Duncan McSporran, Director, Programs and Innovation, Office of Research Services, University of New Brunswick
GE Additive has announced that the University of New Brunswick (UNB) in Canada, together with commercialization partner Custom Fabricators & Machinists and training partners Nova Scotia Community College (NSCC), New Brunswick Community College (NBCC), and the College communautaire du Nouveau-Brunswick (CCNB), has chosen its Concept Laser M2 Cusing metal 3D printer to use in its latest research.
UNB is in charge of the country’s first Marine Additive Manufacturing Center of Excellence, which will be the very first in Canada to fabricate certified parts for the marine industry with metal 3D printing. The M2 Cusing will mostly be used by UNB’s Dr. Mohsen Mohammadi, who will be the Director of Research and Development for the new center, and his team for multiple R&D areas, including bast resistance, enhanced corrosion protection, and hybrid 3D printing processes.
Mass Portal Announces Reorganization of Software Team
Latvian 3D printer manufacturer Mass Portal has reorganized, and appointed new leadership for, its software team, which is now an independent company called FabControl. The company will be building an open, next-generation software platform for managing 3D printers and AM workflows, and Mass Portal’s current CEO and co-founder Janis Grinhofs, the founder of FabControl and in charge of developing Mass Portal’s flagship Pharaoh 3D printers, will now serve as the CEO of the new company. Imants Treidis has been named the new CEO of Mass Portal.
“We will continue to serve our existing customers and industrial partners, in the same time striving for excellence in supplying the industry with highest quality machines and tailor built solutions for additive manufacturing needs,” Treidis said.
All About Aluminum at AMAP Forum
Not too long ago in Aachen, scientific and industry experts gathered at the AMAP Forum (Advanced Metals and Processes) to demonstrate the continuing potential of researching non-ferrous metals, like aluminum, for the purposes of lightweight automotive design. 14 entrepreneurs from industry and five of the RWTH Aachen University institutions formed the AMAP Open Innovation Research cluster at the forum, and discussed topics ranging from new production technologies and materials development to modeling and metallurgic process technology. Some of the specifics included using aluminum hollow castings to create structural components with functional integration, additive manufacturing, and new design and calculation methods for high-strength aluminum alloys.
Dr. Klaus Vieregge, Chairman of the AMAP Advisory Board and Head of the Hydro Aluminium Research and Development Center in Bonn, said, “We are an efficient network. New members are always welcome, but a high number of members is not the focus of the AMAP cluster, we want to convince people by the efficiency of the work and the research results.”
SelfCAD Partners with MyMiniFactory
Online 3D design platform SelfCAD, founded in 2015, combines 3D modeling, slicing, and several other tools and functions in one easy program. Earlier this year, the platform announced a partnership with popular 3D printable model marketplace MyMiniFactory.
This partnership makes it easy for SelfCAD users to access the design library in MyMiniFactory, and also gives them the ability to download their 3D models directly from the marketplace while still in the SelfCAD program. In addition, it’s also possible for users to upload their models directly to MyMiniFactory for maximum exposure.
To learn more, check out this helpful video:
Discuss these stories and other 3D printing topics at 3DPrintBoard.com or share your thoughts in the Facebook comments below.
Renishaw launches InfiniAM Spectral additive manufacturing monitoring software
3D Printing News Briefs: July 17, 2018
In Today’s 3D Printing News Briefs, we’re covering a lot of business and a little medical news. AMFG is partnering with a top UK bearings manufacturer to help automate its digital manufacturing workflows, while Segula Technologies has begun an industrial 3D printing partnership with digital manufacturing company Multistation. Techniplas has completed a deployment of Sharebot 3D printers to its 14 manufacturing facilities around the world, and the winners of the SkillsUSA Additive Manufacturing Competition have been announced. Finally, a pediatric cardiologist used the Sinterit Lisa to create a 3D printed model of a newborn boy’s heart to plan his risky surgery.
Bowman International Announces Partnership with AMFG
Automation software specialist AMFG, which recently launched a new AI software platform, has partnered with Bowman International, one of the top bearings manufacturers in the UK, as it works to grow its 3D printing capabilities through its Bowman Additive Production (AP) division. Bowman AP has several MJF and SLS 3D printers available for its use, and uses 3D printing to design and produce its end-part bearings, which has helped increase their load bearing capacity by up to 70%.
In the meantime, Bowman International’s goal is to use AMFG’s AI-powered production automation software to oversee production of said bearings, by automating production job scheduling, optimizing digital CAD files for production with printability analyses, and creating a custom digital part catalog.
“We’re very pleased to be partnering with AMFG and using their automation software to scale our already expanding AM facility,” said Jacob Turner, the Head of Additive Production at Bowman International. “Additive manufacturing is transforming the way bearings are manufactured, and we aim to continue to be at the forefront of innovating the production of bearings using AM. AMFG’s automation software will enable us to achieve this by significantly increasing the efficiency of our production processes.”
Multistation Partners with Segula Technologies
Another newly announced 3D printing partnership is the one between international engineering group Segula Technologies and Paris-based 3D printing company Multistation. The two are working together to further develop the potential of 3D printing in the industrial sector, which will allow both companies to increase their offerings and provide customers with excellent services along the AM value chain. Segula will bring its design, product-process qualification, and technology integration in industrial environments to the table, while Multistation will share and apply its expertise in AM design and simulation by determining any potential parts that could be 3D printed instead of fabricated with a more traditional method of manufacturing.
“Additive manufacturing is an integral part of a value chain within which Multistation provides a comprehensive offering; Segula Technologies was an obvious partner of choice to enable our Additive Consulting division to address manufacturers’ concerns more effectively,” said Yannick Loisance, the CEO of Multistation. “We will thus be able to supply them not just with software packages, machines and materials, but also with a more comprehensive range of high-quality engineering services that are suited to a host of different business sectors.”
Techniplas Adds Sharebot 3D Printers to Its Manufacturing Facilities
This fall, Italian professional-grade 3D printer manufacturer Sharebot joined the open innovation program at Techniplas, a top automotive design and manufacturing provider. Now, as part of its own continuing digital transformation, Techniplas has deployed Sharebot 3D printers to all of its 14 manufacturing facilities across five continents. This move will allow the company to 3D print the majority of the manufacturing products it uses every day on-site, which will equal major cost and time savings as Techniplas previously used only third-party providers for this task.
“With Sharebot 3D printers installed in all of our manufacturing facilities worldwide, we are taking decisive steps toward fabricating the majority of our manufacturing line assembly tools, jigs, fixtures, gauges and even robotic arm attachments in-house. Based on our experience with Sharebot printers thus far, we expect to significantly reduce our development time and annual assembly line tooling costs in each manufacturing facility over time,” said Techniplas COO Manfred Kwade.
Winners of the SkillsUSA Additive Manufacturing Competition Announced
For the fourth year running, advanced manufacturing technology industry organization SME and Stratasys have co-sponsored the SkillsUSA Additive Manufacturing Contest, held during the annual SkillsUSA National Leadership and Skills Conference in Louisville. The winners of this year’s student contest, which asks contestants to solve real world problems with 3D printing, were just announced. This year, entrants had to design an adaptive device for a veteran, who had endured a traumatic thumb amputation, so he could keep playing his PlayStation 3. Prizes include RAPID + TCT conference passes, SOLIDWORKS’ 3D-CAD design software, SME Education Foundation scholarships (for high school participants), a one-year Tooling U-SME subscription, and a MakerBot Mini 3D printer.
“The SkillsUSA contest is designed to help students and educators realize the power of additive manufacturing to drive innovation. This year’s competition was particularly meaningful as it directly resulted in enhancing a veteran’s life with a custom solution not possible without additive manufacturing,” said Gina Scala, the Director of Marketing, Global Education at Stratasys.
The high school winners include:
- Gold medal: Getty George and Sam Green, Martin Luther King High School, Riverside, California
- Silver medal: Noah Logan and Johnathan Urbani, Stafford Tech Center, Rutland, Vermont
- Bronze medal: Andrew Daddone and Layke Martin, Frederick County Career & Tech Center, Frederick, Maryland
The college winners include:
- Gold medal: Adolfo Vargas and Alexander Kemnitz, Central Community College-Hastings, Hastings, Nebraska
- Silver medal: Deema Al Namee and Aric Donerkiel, Vermont Technical College, Randolph Center, Vermont
- Bronze medal: William Swaner and Ashton DeZwarte, Tenneseee College of Applied Tech-Nashville, Nashville, Tennessee
Watch a video about the 2018 competition here, and check out the winning designs here; you can also view SME’s Flickr album for more competition photos.
Surgeon 3D Prints Pediatric Heart Model with Sinterit Lisa
Desktop SLS 3D printer manufacturing Sinterit has seen its flagship Lisa 3D printer, which went through a recent upgrade, used to save lives in multiple ways, from fighting wildfires and protecting the faces of children to providing assistance in a tough pediatric cardiac surgery.
“Delivering desktop SLS 3D printer for more than three years caused that our clients send us tonnes of useful and exciting cases. Writing about all of them is hard, if not impossible, but when 3D printing helps saving lives, especially those most fragile, we feel proud, and also a duty to share it with you,” Michał Krzak, Sinterit’s Marketing Communication Manager, told 3DPrint.com.
A newborn’s heart can weigh barely 20 grams, and fits in the palm of an adult’s hand, so you can imagine that surgeries on such a delicate organ are exceedingly difficult. Jarosław Meyer-Szary, MD, from the Department of Pediatric Cardiology and Congenital Heart Defects at the University Clinical Center in Poland recently turned to Sinterit’s Lisa 3D printer to save the life of Kordian, an infant less than one month old suffering from a potentially fatal heart disease called interrupted aortic arch.
Meyer-Szary created 3D printed, life-size model of Kordian’s tiny heart, and SLS technology was able to recreate each intricate artery and vein. The model not only helped him plan the surgery ahead of time, but also helped Kordian’s mother gain a more thorough understanding of her son’s condition. Kordian is now a thriving and happy 18 month-old, thanks to Sinterit’s SLS technology.
Discuss these stories and other 3D printing topics at 3DPrintBoard.com or share your thoughts in the comments below.
NIAID Scientists Use 3D Tech to Better Understand the 1918 Influenza Virus

The H1N1 virus. [Image via Wikipedia]
The flu pandemic of 1918, also known as the Spanish flu, was the first of two flu pandemics involving the H1N1 virus. It affected approximately 500 million people worldwide, reaching even remote islands and the Arctic, and resulted in the deaths of somewhere between 50 and 100 million people, fully 3-5% of the world’s population at the time, making it the deadliest natural disaster in recorded history. As the flu wave spread around the world, wartime censors tried to minimize reporting on it so as to not adversely affect morale; however; countries such as Spain, which was neutral during WWII, freely reported on the disease. This gave the impression that the flu had hit Spain particularly hard, thus giving rise to the name Spanish flu, despite its heavy hitting consequences around the world.
This flu was particularly shocking not only because of its scale but because of the fact that rather than resulting in the deaths of the young, old, and sick as is normally the case during flu outbreaks, it killed primarily healthy young adults. There are a number of theories as to why this flu was so particularly deadly and samples of it that were preserved in the bodies of victims who were found frozen were subjected to study at the time in order to attempt to unravel its secrets. While some investigation has proposed that the virus itself was particularly aggressive, other research has suggested that rather than a difference in the virus itself, it was a change in global circumstances as a result of WWI, such as malnutrition and crowding in prison camps, that allowed the normal flu virus to wreak such deadly havoc. A recent theory suggests the possibility that aspirin poisoning contributed to the high number of deaths, as there was a distinct spike after the surgeon general recommended large doses of aspirin as treatment and in the wake of the expiration of Bayer’s patent on the drug in which a multitude of other companies rushed in to produce, and profit from, the production of aspirin.
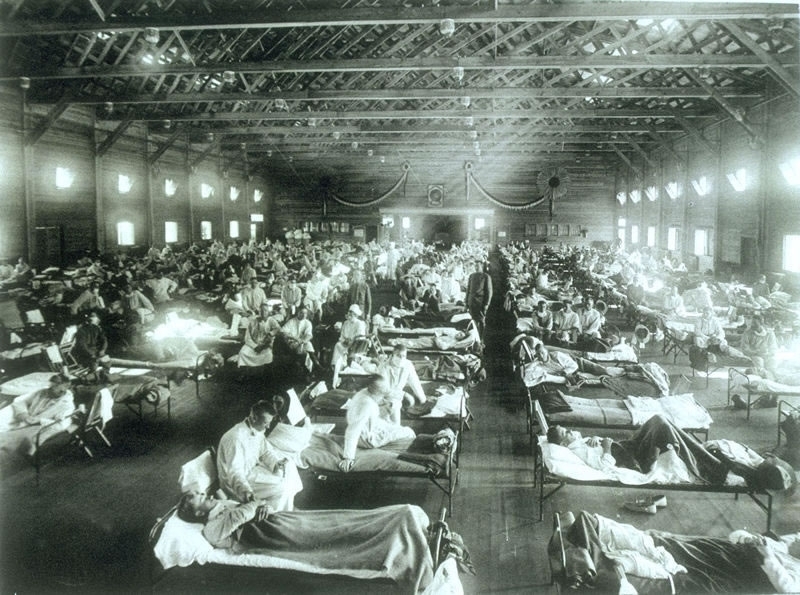
Soldiers from Fort Riley, Kansas, ill with Spanish influenza at a hospital ward at Camp Funston. [Image: US Military via Wikipedia]
Efforts to understand everything we can about such a deadly disease have not been shelved in the 100 years since its dramatic outbreak. New research being undertaken by scientists at the National Institute of Allergy and Infectious Diseases (NIAID), part of the National Institutes of Health, is working to better understand the H1N1 flu virus as part of a program to develop improved vaccine platforms using virus-like particles (VLPs). A virus-like particle is a protein-based structures that mimics a virus and binds to antibodies, with the important distinction of itself being non-infectious. This combination makes it the idea delivery platform for vaccines not only for the flu but potentially for diseases such as Ebola, SARS, and HIV.

On the left is a 1918 H1 influenza virus-like particle (VLP) as seen by cryo-electron microscopy. On the right is the same VLP rendered in 3D with structural components computationally segmented and colored; hemagglutinin and membrane are light blue and internal components (molecular cargo) are red. [Image: NIAID]
In order to better understand how this might occur, an expert in 3D modeling was called in to create a rendition of the 1918 H1 pandemic influenza virus to help the researchers visualize the molecular structure. The data for the visualization was compiled through a process of collecting hundreds of VLP samples which were then quick frozen and sliced into layers, providing a view of their internal layers. Computers were used to track their key molecules and the the aggregate data was used to generate a full model of the molecular structure from the frozen samples.
While it has been possible to get close up imagery of the VLPs before, never has it been presented with the kind of clarity made possible using 3D modeling techniques. This has enabled the researchers to understand the unique arrangement of hemagglutinin (HA) proteins and it is believed that the number and location of HA molecules may influence the efficacy of VLP vaccines. The hope is that with this increased understanding they will not only be able to create a potential platform for vaccines against other diseases, but also more efficacious vaccines against the flu itself, even when it’s just the regular seasonal bug.
The results of their preliminary research have been published in Scientific Reports, and will no doubt encourage others to understand the value that 3D modeling holds for medical research on this micro level. “Structural analysis of influenza vaccine virus-like particles reveals a multicomponent organization” was authored by Dustin M. McCraw, John R. Gallagher, Udana Torian, Mallory L. Myers, Michael T. Conlon, Neetu M. Gulati, and Audray K. Harris.
What do you think of this news? Let us know your thoughts; join the discussion of this and other 3D printing topics at 3DPrintBoard.com.
[Source: NIAID]