The Netherlands: 3devo to Release AIRID 3D Printing Polymer Dryer in June
Based in the Netherlands, 3devo continues on their mission to bring 3D printing accessories to the rest of the world—offering affordable, accessible products that are also high quality for users at the desktop level. Previously, they brought us the Filament Maker, featuring extrusion of custom 3D printing materials. Along with that is the SHR3D IT, another peripheral 3D printing product that offers a great service in recycling plastic into ‘graduate granulate,’ which can then be used for further fabrication—along with saving the world from more plastic trash.
Now, 3devo is presenting the AIRID Polymer Dryer, for improving 3D printing filament. According to a recent press release sent to 3DPrint.com by 3devo, the AIRID will be available June 28th. The small machine looks like a great accompaniment at the desktop for users seeking better uniformity in their resin base. As slight defects can wreak havoc on the integrity of a 3D print, AIRID is designed to dry plastic filaments before use, thus increasing their performance potential during production.
The drying process is primarily aimed at avoiding polymer hydrolysis as bubbles and holes being to appear in plastic filament, causing problems with materials and 3D printed objects that are lacking stability and strength.
“The AIRID Polymer Dryer is the last piece in our closed loop ecosystem. The user now achieves full control over every step of recycling and extrusion. Unlike a standard oven, AIRID dries batches evenly and makes extrusion even more stable and reliable for consistent filament,” said Louis Rinaldo, Materials Researcher.
Product Specs for the AIRID Polymer Dryer are as follows:
- 1kg / 3hrs
- 5 liters capacity
- Polymer presets to streamline the drying process
- Drying process up to 160C/320F
“Following the company’s accessible philosophy, the portable dryer is a perfect addition to a desktop extrusion system,” states the company in their press release. “The dryer has material presets to promote accuracy and intuitive display settings to easily develop a customized drying environment.”
While a wide range of different and constantly evolving hardware, software, and materials are where it’s at for fabrication of endless innovations in 3D printing, there is also a huge industry today targeting users who love to try out a variety of other gadgets that may help them perfect their products further—and especially at the desktop. Not only that, many of these more peripheral products are fun and aesthetically pleasing as well, from other products repelling moisture damage, recyclers that even turn fishing line into filament, and solutions for recycling solvent waste.
While 3D printing is an extremely creative endeavor, users tend to be hackers, makers, tinkerers, and individuals willing to take the time to perfect not only the items they are making—but also the technology and other associated products.
What do you think of this news? Let us know your thoughts! Join the discussion of this and other 3D printing topics at 3DPrintBoard.com.
[Source / Images: 3devo]
3D Printing News Sliced: Desktop Metal, Sigma Labs, Open Bionics, Cincinnati Incorporated
3D Printing News Briefs: February 6, 2018
We’re talking about business, training, and events on today’s 3D Printing News Briefs. The first European 3D printing incubator will soon be inaugurated in Barcelona, and 3devo is launching training workshops about desktop filament extrusion. nScrypt’s Director of 3D Printing and a surgeon from Belfast will be presenting at upcoming events, and Arburg will display a complete turnkey system at an Italian trade fair. Finally, because we celebrate all accomplishments in our industry, we’re sharing some good news about a Xometry employee.
3D Factory Incubator Inauguration
This coming Monday, February 11th, the inauguration of the first European incubator of 3D printing – 3D Factory Incubator – will take place in Barcelona. The Minister of Science, Innovation and Universities, Pedro Duque, will chair the inauguration’s opening act. This High-Tech Business Incubator, a project led by Fundación LEITAT and El Consorci de Zona Franca de Barcelona (CZFB), is working to promote the adoption of 3D printing by creating a space to incubate related SMEs and micro-SMEs.
The 600 sqm incubator space is located at CZFB’s headquarters, and will include training areas, offices, meeting rooms, laboratories, and co-working zones, in addition to a variety of services. The inauguration will begin promptly at 11 am.
3devo Launching Training Workshops
Dutch technology company 3devo, which creates desktop-based material development and recycling solutions such as SHR3D IT, is launching a series of hands-on training workshops all about desktop filament extrusion for professionals, which will be branded as DevoTraining. The workshops will be held at 3devo’s Utrecht headquarters, and participants can choose one of three programs: a basic, 4-hour module for €499, a 1-day intermediate workshop for €899, and a 2-day advanced level course for €1549.
“The demand for unique 3d printing materials is ever-growing, which requires new knowledge on how to process it,” said Tim Wesselink, the CEO of 3devo. “With DevoTraining, we offer the answers to those innovators who seek to take matters into their own hands. Giving them complete guidance to create and customize their own filament – on demand.”
DevoTraining will be officially released next Tuesday, February 12th.
nScrypt Discussing 3D Printed Munitions and Other DoD Applications
Orlando, Florida-based nScrypt, which manufactures micro-dispensing and 3D printing systems, announced the release of its hybrid Factory in a Tool (FiT) integrated system for Direct Digital Manufacturing in October. nScrypt’s Director of 3D Printing, Larry (LJ) R. Holmes, Jr., is in charge of directing the company’s market participation for industrial-level 3D printing hardware, including its work with the US Department of Defense (DoD). This week, Holmes will speak about nScrypt’s 3D printed munitions, as well as its other DoD applications, on the “AM Innovation Panel: Developing the Next Generation of 3D Printing and Processes in Support of the Warfighter” in Tampa at the Military Additive Manufacturing Summit & Technology Showcase.
“Our FiT platform is ideal for DoD’s 3D printing applications because it does next generation Direct Digital Manufacturing, which means no retooling to build a product or to change from printing one product to another. Just change the CAD file. Our FiT’s pick and place tool head adds actives to the prints, making them electrically functional if needed. We just delivered a Factory in a Tool to the Army’s Redstone Arsenal. It has one full meter of travel in the XY plane,” Holmes said.
“nScrypt’s goal is to disrupt how manufacturing happens. Munitions printed on-demand, where and when they are needed; a ruggedized 3D printer for use in forward deployed locations; and printed electronics, like conformal Active Phased Array Antennas for improved performance at lower cost, are a few of the examples of capabilities currently being transitioned from nScrypt to the DoD and the global manufacturing industrial base.”
SXSW 3D Printing Presentation About 3D Printed Kidney Model
SXSW 2019 begins next month in Texas, and in addition to the many other innovations on display at the event, Dr. Tim Brown, Consultant Transplant Surgeon at Belfast City Hospital, will share his experience of using 3D printing to successfully perform a first of its kind, life-saving operation during a presentation titled “Tumours, Transplants and Technology: AI for Life.” His patient needed a life-saving kidney donation, and while her father was willing to donate, his kidney had a tumor on it. Together with UK medical 3D printing company axial3D and Digital Catapult, Dr. Brown used a 3D printed kidney model to safely complete the transplant surgery and save his patient’s life.
“As the cyst was buried deep within the renal cortex and therefore invisible on the back bench, a replica 3D model was used for preoperative planning and intra-operative localization of the lesion,” explained Dr. Brown. “It’s difficult to underestimate how valuable this strategy was in terms of preoperative planning and achieving successful clearance of the lesion.”
axial3D won the Healthcare Application Award at the 2018 TCT Awards for creating the 3D printed model, and the company’s CEO Daniel Crawford and Operations Manager Cathy Coomber will join Dr. Brown for a panel discussion at SXSW, along with Nigel McAlpine, Immersive Technology Lead at Digital Catapult. The session will take place at SXSW on March 12th, at the JW Marriott Salon FG.
Arburg Exhibiting at MECSPE 2019
At next month’s MECSPE 2019 trade fair in Italy, German machine construction company Arburg will be focusing on 3D printing, automation, and digitalization. The company will be displaying a complex turnkey system, built around a Freeformer 200-3X industrial AM system and a hydraulic Allrounder 370 S; both the Freeformer and Allrounder are networked live with the company’s ALS host computer system. In addition to displaying the system at the trade fair, Arburg will also have experts presenting their outlook on the digital future of plastics processing at Stand F49 in Hall 6.
“MECSPE 2019 is the most important trade fair for the manufacturing industry in Italy and, with its focus on Industry 4.0 and automation, it is an ideal match for Arburg. We are not only a machine manufacturer and expert in injection moulding, but we also have our own MES, our own controllers, automation technology and the Freeformer for industrial additive manufacturing as part of our product portfolio,” said Raffaele Abbruzzetti, the new Managing Director of Arburg Srl. “With more than 30 years of experience in networked and flexibly automated production, we offer our customers everything they need in the era of digitalisation to increase their added value, production efficiency and process reliability – from the smart machine to the smart factory and smart services. We will present examples of all of this at MECSPE.”
Xometry Employee Wins Game Show
This last News Brief has nothing to do with 3D printing itself, but rather an unrelated, but still incredible, accomplishment from one of the industry’s own. On Thursday, January 24th, employees from on-demand manufacturing and 3D printing service provider Xometry gathered to watch one of their colleagues – marketer Aaron Lichtig – compete, and eventually win big, on the popular Jeopardy! game show that night.
Lichtig started off at a steady pace, competing against returning champion and astrophysicist Rachel Paterno-Mahler and sales manager Nancy Rohlen, and was leading the pack with a final score of $12,400 by the end of the Double Jeopardy round. He squared off against Rohlen during Final Jeopardy with the clue, “He was the first U.K. prime minister born after Elizabeth II became queen.” While both correctly guessed the answer as Tony Blair, Lichtig’s steep lead made him the winner that night. Congratulations from your friends at 3DPrint.com!
Discuss this news and other 3D printing topics at 3DPrintBoard.com or share your thoughts below.
Formnext 2018 – the 3D Printing Industry first look
3devo Introduces Two New Series of Filament Extruders
3devo is a young company known for its filament extruders, which include the NEXT 1.0 and the 3devo Advanced. The Dutch company also markets a plastic shredder as part of its mission to simplify the making and recycling of filament. Now 3devo has announced two new series of products, the Precision Series and Composer Series filament makers. According to 3devo, the new filament makers further simplify the material fabrication process.
“Our NEXT filament maker found numerous amounts of applications in industries ranging from education and research to manufacturing and aerospace,” 3devo says. “They brought users a variety of benefits including shorter lead times, reduced material waste, and increased control over material making. Also, they facilitated material research and customization, while introducing the precision of industrial filament making to desktop-based setups. However, we realized that our filament makers could serve these purposes even better – if they focused on specific requirements. Our new Precision and Composer Series filament makers are specialized, result-oriented machines aimed at simplifying the material making process. Each in a different way.”
The Precision Series of filament makers allows mass production of 3D printer filament at faster speed and with improved diameter accuracy. It features a high-flow extruder screw that allows filament to be produced without losing tolerances one the diameter.
The Composer Series is designed for material mixing and experimentation. Users can develop custom filament from a wide variety of polymers and additives. It features a mixing screw that delivers high-quality material mixing and compounding.
Both series have two additional models that address material-specific requirements. The Precision 350 and the Composer 350 can handle temperatures up to 350°C, meaning that they can process materials including PLA, ABS, PC, PS, PETG, TPU, TPE, PPS, PA (6,12,66) and more. The Precision 450 and the Composer 450 can – you guessed it – handle temperatures up to 450ºC, allowing them to process high-performance materials such as PAEK family materials such as PEEK, as well as PSU, PTFE, PVDF and more.
The new filament makers have several upgrades and improvements. Each Precision and Composer model comes with an improved extruder system with a new “swappable” design. The entire extruder system, including screw, barrel, die-head, motor and heaters is designed as an independent, removable unit to simplify cleaning, repair and maintenance. Users can easily disassemble and reattach the system on their own.
In addition, the heating system has been upgraded. All Precision and Composer filament makers contain ceramic band heaters with four controllable heating zones. Each heater is handcrafted in-house. The filament makers also have hoppers with closable caps to prevent material contamination. Finally, the new filament makers each feature upgraded software that improves their thermal stability by up to 35%.
3devo has more in the works as well – the company is working on developing a web app with cloud access, which will allow for active data logging of extrusion tests.
You can learn more about the Precision and Composer filament maker series here.
Discuss this and other 3D printing topics at 3DPrintBoard.com or share your thoughts below.
[Images: 3devo]
Interview with Alessandro Severini of the Felfil Filament Extrusion Machine to Make Your Own Filament at Home
The main thing that attracted me to 3D printing initially was this technology’s promise to let anyone make anything. On top of that once we’re bored with it we could then recycle it and make new things. With 3D printing, we could in a sustainable way have our cake and eat it too. We could grind up and extrude new filament made of old 3D prints or old PET bottles. At the same time this would make 3D printing energy efficient and very low cost. Many companies and projects have tried to make low cost, open source, and easy filament extruders. Most of these extruders are the kind of things that would take pleasure at burning your house down. Rickety, dangerous and difficult to use they’ve been nice representations of the idea but I shudder at the thought of using them again. Some are exceptions such as the high-end 3Devo device which is fine for your lab but too expensive for many of us. There really isn’t a product between the 3Devo and the rickety cheap extruders. The Felfill purports to be just such a device combining ease of use and desktop filament making inside of a relatively inexpensive device. An assembled Felfill costs 719 euros and promises to make a filament manufacturer out of you. We spoke to Alessandro Severini of Felfill to find out more.
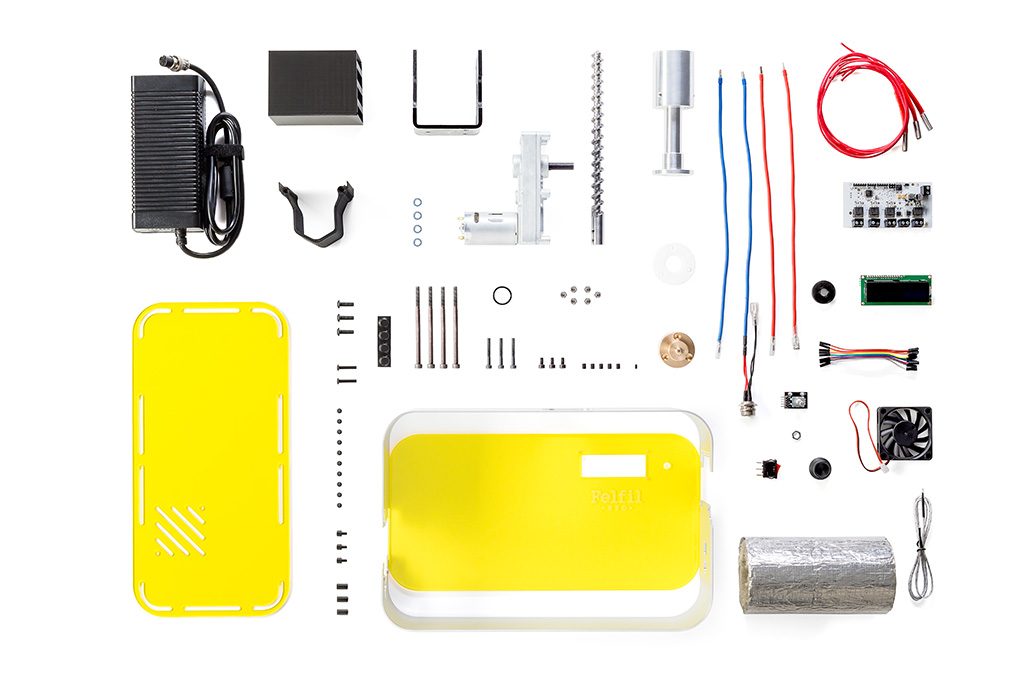
“Felfil is a 3d printer plastic extruder machine which allows anyone to make custom 3D printing filaments at home, starting from industrial pellet or chopping up wrong 3D prints, old models and plastic waste.
Using our desktop filament maker you will be able to choose your filament color, diameter and material, day by day, according to your creativity and your curiosity. In this way you can save over 80% of the price of filaments spools and help to protect the environment.”
What kinds of customers do you have?
“Our customers are many and really different from each other. However we can divide it in three different groups: those who are focused on recycling, those who are focused on research on new material types, such as medical applications, and those who just print a lot and want to save some money buying pellets instead of filament. We are seeking all of them in order to help them to reach their goals.”
What kind of materials can the Felfill make?
“We have tested the Felfil Evo with a wide range of materials, at the moment we can say that It can successfully process: PLA, ABS, HIPS, TPU, PA12, LDPE and HDPE, PETG, PP, PC/ABS, PCL and PMMA, and this list is in continuously updated.”
If I process HIPS and ABS won’t harmful fumes come from this?
“Ye,s It could happen. For this reason we strongly suggest our customers take every possible precaution about their own safety such as using it in a well ventilated area and under a fume hood.”
How well are you doing as a company?
“Never good enough! We are working hard in order to increase our business an improve our products quality, we are also developing some new interesting things and we will show them in next few months.”