A Geneva drive is a gear that will turn a continuous rotation mechanism into an intermittent rotary motion mechanism by adding a driven wheel to the gear with multiple slots. It then advances a single 90° step each time the drive wheel rotates. Named for its frequent use in Swiss-made watches, it’s still used today in things like movie projectors, and even in 3D printed applications such as novelty items and drug delivery systems.
A team of researchers from the Politehnica of Bucharest University in Romania published a paper, titled “Study behavior of Geneva mechanism using 3D printing technology,” where they considered the use of a variety of materials and technologies for developing, and studying the behavior of, these gears.
The abstract states, “In this paper the authors considered external Geneva mechanism. The design and machining of a conventional Geneva mechanism are generally well known, but there are some particularities, if we consider 3D printing technologies. Conventional, Geneva mechanisms are used to low-speed applications, or to those in which noise and vibration are of no importance. Using PLA+Copper or ABS materials noise and vibrations are reduced considerably. Also, the entire mechanism has a reduced weight. There were considered different fill factors for 3D printed parts. The experimental setup allows fast changing of mechanism parts. This research aims the study of behaviour of 3D Printed machine elements like: springs, bearings, clutches gears, bellows, diaphragms, bushes, brakes, sliders, etc developed by authors.”
A Geneva mechanism is a type of indexing mechanism with a fairly simple design – just a driving crank and wheel, with straight slots. This is known as a Maltese Cross mechanism. Conventional Geneva mechanisms are used for more low-speed applications, where the amount of vibration or noise made doesn’t matter.
The researchers 3D printed five Geneva mechanisms – each with five Maltese crosses and five driving cranks with pins – out of five different materials:
- Plexiglass
- PLA
- ABS
- PLA + copper
- PLA + bronze
“The Geneva mechanism translates continuous motion to intermittent motion through the driving wheel whose crank pin is shown in figure 1,” the researchers explained. “It drives the Geneva wheel as it slides into and out of the slot of the Geneva wheel. It thus advances it – one step at a time when engaged. The driver wheel usually consists of both the crank and a raised circular blocking disk that locks the Geneva wheel in position between steps to avoid excessive vibration while rotating.”
Each cross had six slots, but a Matlab environment was used to develop a theoretical study that considered different Geneva mechanisms with z = 3, 4 and 6 slots; you can see these results in Figure 2.
The team also created experimental setups for five mechanisms so they could “determine cinematic parameters of Geneva mechanisms.” They used reflective sensors to find the time between two successive slots.
“When the slot of the Maltese cross is in front of the reflective sensor the reflected beam is interrupted,” the researchers wrote. “Then, the cross is rotating with an angle of 60°. The cross passes in front of the reflective sensor and the time is recorded until the next (successive) slot is reached. When the cross is in front of the reflective sensor the beam is reflected.”
Different angular rotation speeds for the driver crank were also tested for the paper, in order to study the Geneva mechanisms’ cinematic and dynamic behaviors.
The experimental setups with Geneva mechanisms are connected to PC through a USB interface.
“The models obtained are used as demonstration stands used in didactic applications,” the researchers concluded. “Of the five investigated materials, ABS and PLA + Copper have been proved to have properties and characteristics close to mechanical engineering applications and these results are demonstrated by graphs. ABS also has the advantage of lighter weight, which makes it suitable for applications where low mass is needed. It can also be concluded that the angular speed of the drive element is inversely proportional to the difference between the angular speeds of the Malta crosses.”
Co-authors of the paper are D. Rizescu, D. Besnea, C.I. Rizescu, and E. Moraru.
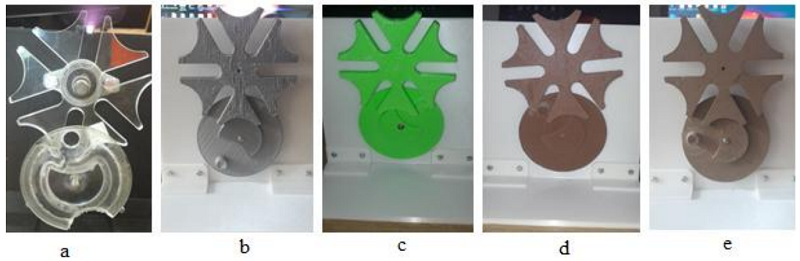
Figure 7. Geneva mechanisms from different materials: a) PMMA b) PLA c) ABS d) PLA + copper e) PLA + bronze
Discuss this story and other 3D printing topics at 3DPrintBoard.com or share your thoughts in the Facebook comments below.
The post Researchers Study Behavior of 3D Printed Geneva Mechanisms appeared first on 3DPrint.com | The Voice of 3D Printing / Additive Manufacturing.