Although polymers are still the most popular materials used in 3D printing today, many users find themselves limited due to issues with inferior strength and rigidity. Creating composites is a good way to solve these problems, allowing manufacturers to enjoy the benefits of existing plastics while reinforcing them for better performance. In ‘Modelling and path planning for additive manufacturing of continuous fiber composites,’ Suleman Asif, a thesis student at Sabanci University (Instanbul), examines how the addition of continuous fibers can improve fabrication processes with thermoplastic polymers, and add greater strength in mechanical properties.
FDM 3D printing is mainly explored here. Issues with FDM 3D printing and these materials, however, tend to be centered around a lack of strength and inferior surface finish, build times that take too long, and inconvenient post-processing. In previous studies, researchers have used short fibers to strengthen thermoplastics, along with carbon nanotubes and fiber composites. Iron and copper have been added to ABS, and the addition of graphene fibers have been noted to add conductivity. In most cases, tensile strength increased but there were issues with interfacial bonding and porosity.
The use of short fibers and nanofibers has been explored, but Asif explains that such additions are better for applications like aerospace or automotive. With the use of continuous fiber reinforced thermoplastic (CFRPT) composites, though, both ‘ingredients’ are extruded at the same time from one nozzle and show significant improvement and strengthening.
In a different study, researchers loaded both thermoplastic polymer and continuous fibers into the nozzles for FDM printing, with PLA and continuous fibers (some samples consisted of carbon fibers, and some with jute) added separately to another nozzle. While carbon did offer improvements in strength, the jute was not helpful due to ‘degradation of fiber matrix interactions.’ Other tests showed that PLA reinforced with modified carbon showed higher tensile and flexural strength values, demonstrating how powerful ‘preprocessing’ can be.
“Furthermore, a path control method was developed to print complex geometries including hollow-out aerofoil, a unidirectional flat part, and a circular part,” states Asif.
Previous methods also used ABS and carbon fibers, with two different nozzles and the carbon fibers contained in between the upper and bottom layers of the plastic.
“The process worked in such a way that after printing of lower layers of ABS, carbon fibers [were] thermally bonded using a heating pin before the upper layers of ABS were printed. In addition, some samples were also thermally bonded using a microwave to understand the difference between both methods,” said Asif.
In comparison to pure ABS, the results demonstrated significant strengthening in mechanical properties.
“In addition, it was observed that there was not much difference between the results obtained from test specimen thermally bonded by heating pin and microwave oven. So, it was concluded that microwave could be successfully used for thermal bonding between matrix and other fiber layers.”
Researchers also attempted to reinforce PLA with aramid fibers, showing ‘notable enhancement.’ Another test evaluated a raw material of commingled yarn, containing polypropylene (PP):
“A cutting device was also incorporated in the system, and a novel deposition strategy was developed. The results showed a remarkable increase in flexural modulus as compared to pure PP. However, the void presence in the samples was a major issue in the proposed technique.”
Overall, in reviewing the multitude of studies performed, Asif saw potential for improving mechanical strength, but realizes a need for control of the fiber position within the nozzle to reduce adhesion issues.
“The system also needs to be designed in such a way that the fiber lies directly in the center of the nozzle to ensure that the thermoplastic polymer is properly diffused into the fiber from all sides using a coaxial printing process in which more than one materials are extruded simultaneously through a nozzle along a common axis,” says Asif.
The researcher also began examining various path planning processes for acquiring point locations that guide the extruder in depositing materials for filling layers. Asif discovered that most suggested path planning was limiting as it only worked for specific complex structures—some of which would not be appropriate for fabrication of CFRTP composites. Asif suggests that as the algorithms stand currently, there would be problems due to:
- Under-deposition (typically called underextrusion in FDM)
- Over-deposition
- Movement of the extruder to next layer after filling one layer
“Hence, there is need of a continuous path planning method that can generate a deposition path without any under-deposition and over-deposition, and with better moving strategy from one layer to the next one,” concludes Asif.
“As a future work, a screw-based mechanism can be designed and developed for 3D printing of CFRTP composites. It would allow the continuous input of thermoplastic pallets and, therefore, parts with large dimensions can be printed. In addition, a topology optimization based algorithm can be developed to control the number of layers containing fibers to produce optimized lightweight parts depending upon specific load applications.”
3D printing offers an infinite amount of opportunity for designers and engineers around the world, immersed in creation—whether that is industrial, artistic, or completely scientific. There is an immense amount of energy centered around this technology that just continues to grow in popularity, and especially as users continue to refine the processes and materials. Composites are often used to strengthen existing methods and materials, whether in making structural parts for aerospace, regulating electrical composites, or studying conductivity and different techniques for fabrication. Find out more about the use of continuous fiber composites here.
What do you think of this news? Let us know your thoughts! Join the discussion of this and other 3D printing topics at 3DPrintBoard.com.
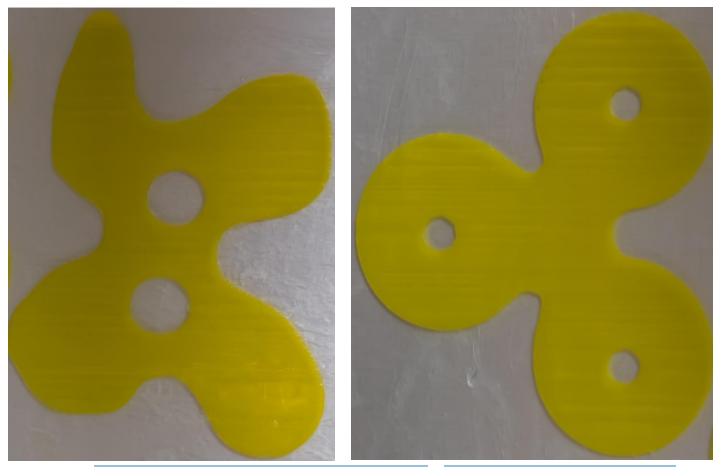
Implementation of the developed algorithm on a commercial printer (a) Complex concave geometry (b) Fidget spinner
[Source / Images: ‘Modelling and path planning for additive manufacturing of continuous fiber composites’]
165 Replies to “Istanbul: Thesis Student Explores Continuous Fiber Composites in FDM 3D Printing”
Comments are closed.