In ‘Success Factors for 3D Printing Technology Adoption in Construction,” thesis student Pankhuri Pimpley at the University of Maryland, College Park, explores not only the history and benefits of 3D printing but also its effectiveness overall in a competitive, demanding market.
While 3D printing was created in the 1980s and introduced to the construction industry in the 90s, its purpose in that application was mainly for rapid prototyping. Such a process offers huge benefits to industrial users, but as with so many other industries and applications, it wasn’t long before ambitious users wanted to use digital fabrication to make real parts.
As further advances in automation are still needed for the construction industry, 3D printing has become a very attractive option. The advantages abound too—from more savings on the bottom line to greater efficiency and less need for labor, to a continually expanding array of available materials. The author’s discussion as to why 3D printing is needed in construction is compelling:
“The construction industry has been slow in adopting new methods and innovations due to deep confidence in the efficiency of traditional processes, materials and codes. Since no change or innovation proposes growth of the sector, the construction industry has one of the lowest productivity increases compared to other industries. It is even more important to automate construction activities given the risks associated with it,” states the author.
“About 400,000 people are injured or killed every year in the USA during construction. These injuries and fatalities eventually translate to costs for society. Construction is also prone to corruption and political feuds. Hence the primary need for 3DP in construction is to reduce or eliminate human involvement in the design and development of the structure. It is also important that 3D printing be considered a standard construction practice by code bodies. Accepting the innovation can help set a common standard for global construction and solve the problem of labor skill variation from demographics and experience.”
Large-scale mobile printers are popular in the construction industry, and we have followed many of them such as the WASP 3D printer, which has been used for the beginnings of creating an entire community, along with tiny houses, and more. Pimpley points out numerous other examples too of companies with ambitious plans also, many of them eager to build small structures in record time—including Eindhoven University of Technology in the Netherlands, planning to print five single-story, two-bedroom residences.
Pimpley also gave great attention to how socioeconomics might affect 3D printing, along with considering how to manage such factors in the future. One of the most important items that Pimpley points out, however, is that within the construction industry overall, the actual usefulness of 3D printing is ‘still limited.’ The author explains to us that this is due to certain issues related to society, the general market, and other business-related reasons.
“Nine success factors and forty-two corresponding measurement items have been identified and analyzed through literature review, case studies, surveys, interviews and correspondence with worldwide construction 3D printing experts and professionals. All factors are finally determined important to consider for the success of a construction 3DP project at its current phase. Relative significance of the factors and measurement items have been determined based on 82 questionnaire survey responses,” concluded the researcher.
“Altogether, the findings can help achieve an understanding of 3DP and increase the likelihood of successful adoption in various sectors within construction.”
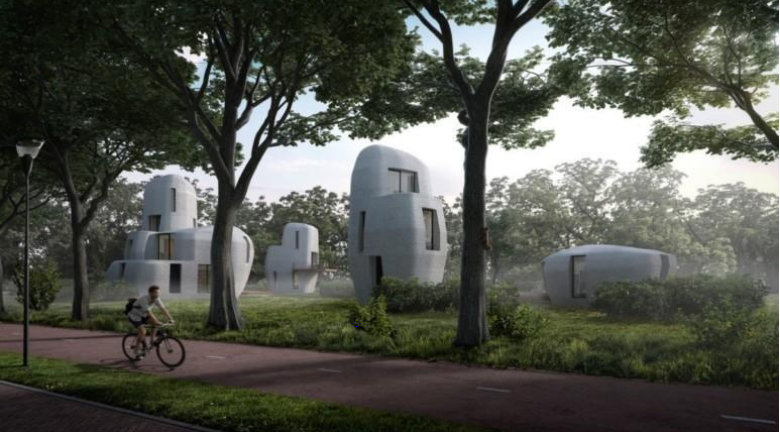
Eindhoven’s proposed home design (“3D Printed Homes – 4 Most Fascinating Projects in 2019”, 2019, February 20).
What do you think of this news? Let us know your thoughts! Join the discussion of this and other 3D printing topics at 3DPrintBoard.com.
The post 3D Printing in the Construction Industry: Still Evolving appeared first on 3DPrint.com | The Voice of 3D Printing / Additive Manufacturing.