AFRL and University Partners Used 3D Printed Composite Materials to Make Structural Parts
The Air Force Research Laboratory (AFRL), located at Wright-Patterson Air Force Base (WPAFB) near my hometown of Dayton, Ohio, has long been interested in using 3D printing and composite materials for the purposes of aerospace applications. Last year, AFRL’s Composites Branch at the Materials and Manufacturing Directorate partnered up with researchers from the University of Arkansas, the University of Miami in Florida, Louisiana Tech University, and the University of Texas at El Paso (UTEP) to work on advancing 3D printable composite materials.
The Composites Branch works on the research and development of organic and ceramic matrix composite technologies for legacy, developmental, and future Air Force system components. Together with its university partners, the AFRL branch demonstrated 3D printed composite materials, made from a combination of carbon fiber and epoxy, which had been successfully fabricated and used to make structural parts on both air and space craft. The results of this 3D printed composite material effort will soon be published in a special issue of the Journal of Experimental Mechanics that’s dedicated to the mechanics of 3D printed materials.
Dr. Jeffery Baur, leader of the Composite Performance Research Team, said, “The potential to quickly print high-strength composite parts and fixtures for the warfighter could be a tremendous asset both in the field and for accelerating weapon system development.”
Composite materials are made up of two, or sometimes more, constituent materials that have very different chemical or physical properties. When combined, these components produce a new material that has characteristics which are different from the originals. The individual components that make up the composite will remain distinctly separated within the final material structure.
When compared to the more low-quality polymers that are typically used in 3D printers, the composite materials demonstrated by AFRL and its partners are the same type that are already being used to make Air Force system components. These materials are very strong, while also lightweight, and have higher thermal and environmental durability than most.
Most traditional epoxy and carbon fiber composites are made by layering carbon fiber sheets, coated with epoxy resin, on top of each other. Then, the whole thing is cooked for hours in a costly pressure cooker to finish. The major downside to this method is that it’s more difficult to create parts that have complex shapes when sheets are being used.
This is where additive manufacturing comes in. Composite materials that are 3D printed are able to create parts with those complex shapes, and additionally don’t require the use of long heating cycles or expensive pressure cookers. On a materials level, there aren’t a whole lot of downsides to using composites for the purposes of producing, assembling, or repairing parts for the Air Force, whether at the depot or out in the field.
Military branches in other countries are also seeing the benefit of 3D printable composite materials. For example, engineers in India are manufacturing complex core structures using the composite 3D printing process; when combined with top and bottom face sheets, these structures will create lightweight sandwich structures that have properties tailored specifically to, as AFRL put it, “the physical forces that need to be carried.”
Conventionally fabricated sandwich structures use the same core geometries over the entire area of an aircraft skin, but a 3D printed version would be able to stand up under heavier forces when necessary, while also remaining lightweight in other parts of the skin.
Discuss this story and other 3D printing topics at 3DPrintBoard.com or share your thoughts in the Facebook comments below.
[Source: Dayton Daily News]
3D Printing News Briefs: December 19, 2018
In today’s 3D Printing News Briefs, a maker has published a free 3D print management app in the Play Store, while Formlabs works to continue accelerating its growth in the Asia Pacific region. America Makes has announced the winners of two Directed Project Opportunities, and a chemist employed by Sinterit has won a prestigious award. Finally, an engineer with a thirst for vengeance used 3D printing and a lot of glitter to get back at the people who steal packages from his porch.
Free 3D Printing App for Filament Management
A new app, simply called 3D Print, is now available to download for free on the Google Play Store. The app was published by a maker who goes by paratiDev on Google Play, and was developed to help other makers better manage their filament.
“It has happened to all of us, you want to print a piece and not to know for sure if you have enough filament in the coil to print it. If you have only one coil of that filament, you have only two options; you can use another filament that has more quantity or risk and print it,” paratiDev writes.
“In the first case it forces you to use another filament different from the one you wanted while in the second case you run the risk that there is not enough filament and the piece remains halfway, assuming a loss of money, filament and time.”
The app allows users to visualize how much filament they have left, view the history of 3D printed pieces they’ve made, and can also generate invoices and quotations for 3D prints. The free 3D Print app also allows you to create projects that group together several pieces, and will visualize the wight and total cost of the project.
Formlabs Continues to Grow in APAC Region
Today, Formlabs announced that its growth in the APAC region is continuing to speed up. The company, which first entered the China market in 2015, is planning to open its new APAC headquarters in Singapore soon, and has also completed a new warehouse in Shenzhen, China for more efficient processing and shipping. While its physical presence in the region is growing, so too is its headcount: Formlabs also announced that David Tan, previously the APAC director of strategy and programs for Oracle Cloud Platform, Alliances & Channels, has been hired on as a new general manager for its own APAC team.
“Formlabs has long set its sights on making 3D printing processes more accessible. Part of this strategy has been completely rethinking 3D printing technologies from the ground up. The second is bringing the technology to market,” explained Max Lobovsky, Co-Founder and CEO of Formlabs. “There is an immense amount of opportunity in Asia Pacific, we’re looking forward to what David and these new locations can do to improve our growing success in the region.”
America Makes Announces Directed Project Opportunities Winners
America Makes has announced the award winners of two Directed Project Opportunities, both of which were funded by the Air Force Research Laboratory (AFRL), Materials and Manufacturing Directorate, Manufacturing and Industrial Base Technology Division. The first is the acceleration of large scale additive manufacturing (ALSAM) project, with the objective of getting past the shortcomings of SLM 3D printing, and America Makes awarded $2.1 million to GE Global Research, in conjunction with GE Additive and the Applied Research Laboratory (ARL) at Penn State. With at least $525,000 in matching funds from the team, the total funding for the ALSAM Directed Project to develop an open source, multi-laser manufacturing research platform will be about $2.6 million.
The second is the advancing AM post-processing techniques (AAPT) project, with a goal of improving process control and lowering costs for qualifying complex parts made with SLM technology. The first awardee is Arizona State University, in conjunction with Quintus Technologies, Phoenix Heat Treating, Inc., and Phoenix Analysis & Design Technologies, Inc., and the second is led by the ASTM International AM Center of Excellence collaborative, in conjunction with Quintus Technologies, Carpenter Technologies Corporation, Aerojet Rocketdyne, Rolls Royce Corporation, Honeywell Aerospace, GE Aviation, and Raytheon. America Makes awarded a total of $1.6 million to the two teams, which will also contribute at least $800,000 in matching funds. Both projects are expected to begin next month.
Sinterit Chemist Makes Forbes List of ’25 Under 25′ Poland
Desktop SLS 3D printer manufacturer Sinterit is proud to announce that its chemist, Paweł Piszko, has been selected by Forbes and the Warsaw office of McKinsey & Company as one of the prestigious “25 Under 25” in Poland. There are five categories in the awards, with five winners in each, and the jury appreciated Piszko’s work on increasing the efficiency of energy collection from renewable sources. When asked by his employers what his goal was, he answered that he wanted to have “an impact on the architecture of society.”
“We are delighted that Paweł chose Sinterit as a place where he can develop his skills and check the results of his scientific activities in practice,” Sinterit wrote in a blog post. “As part of his work, he researches the chemical processes that occur during the sintering of polymers, which allows us to improve the materials that Lisa and Lisa Pro, our flagship SLS 3D printers, print from.”
3DPrint.com congratulates Paweł on this exciting achievement!
Engineer Uses 3D Printed Component to Make Glitter Bomb
Revenge is a dish best served with glitter and fart spray…at least according to a mechanical engineer and evil genius Mark Rober. He spent nine years working at NASA’s JPL – mostly on the Curiosity Rover – and later founded a company called Digital Dudz. He was upset when someone stole a delivered package right off of his porch, and decided to employ all kinds of technology to take revenge.
“I just felt like something needs to be done to take a stand against dishonest punks like this,” Rober said in his YouTube video.
“I spent nine years designing hardware that’s currently roving around on another freaking planet. If anyone was going to make a revenge bait package and over-engineer the crap out of it, it was going to be me.”
Over the course of several months, Rober sketched his idea out, then finished it in CAD before getting to work on the physical prototypes. The package contains a 3D printed component that’s contoured in such a way that four hidden phones inside can capture package thieves opening the box and getting hit with a giant cloud of colorful glitter and continuous blasts of fart spray. Check out his video below to see how things turned out, though be warned that there is some bleeped out profanity. To learn more about the details of his build, check out his friend Sean’s video as well.
Discuss these stories and other 3D printing topics at 3DPrintBoard.com or share your thoughts below.
Proper 3D Printing Orientation and Technique Can Introduce Dielectric Strength Anisotropy into Insulator Components
3D printing has been applied to multiple projects across the various branches of the US military. However, before the technology can be used for more critical applications, some of its issues and imperfections still need to be better understood and conquered. The Air Force Research Lab (AFRL), headquartered at Wright-Patterson Air Force Base (WPAFB) near Dayton, Ohio, works to demystify the technology, and figure out how to apply it to various projects, such as cost-efficient solar cells and silicon chips.
The 3D printing industry has seen plenty of advancement over the last ten years, and allows for the manufacturing of dielectric insulators with highly complex geometries. But, something that causes problems with high voltage electrical generation and distribution systems is stress from the electric field on the dielectric insulating components, like bushings, which can cause dielectric breakdown events that damage those components and reduce the system lifetime.
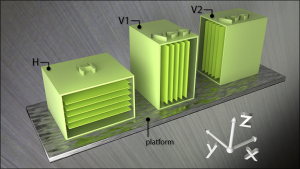
Schematic representation of sample coupon assemblies 3D printed in the H, V1, and V2 configurations.
At the moment, there isn’t a lot of bulk dielectric strength data available for many 3D printing materials, which can limit their use when it may not be necessary to do so. We need to learn more about the limitations of 3D printed parts that result specifically from the given printing method before widespread use of 3D printed dielectric insulators in high field environments can commence. Further research will also help guide development of new 3D printing systems and materials that are well-suited for creating parts for these applications.
AFRL set out to do just that, and together with researchers from the AFRL located at New Mexico’s Kirtland AFB, the Aramco Research Center in Boston, and UES, Inc., published a paper, titled “Dielectric strength heterogeneity associated with printing orientation in additively manufacturing polymer materials,” in the Additive Manufacturing journal.
The abstract reads, “Anisotropy in dielectric properties can have deleterious effects in structures intended for use in high-field environments. We show that dielectric anisotropy is introduced into parts fabricated using additive manufacturing techniques based on the orientation in which the part is printed. Dielectric strength testing data, based on the ASTM D149 standard, are presented for samples fabricated using the polymer jetting (PolyJet), stereolithography(SLA), fused deposition modeling (FDM), and selective laser sintering (SLS) additive manufacturing techniques. Each unique printing direction available, based on the printing method, was examined in turn. Each printing technique was found to introduce anisotropic dielectric properties within the sample coupons that were a function of the original orientation in which the part was printed, and the direction of structural susceptibility was found to be print-method dependent. Differences in dielectric strength for coupons printed in different orientations were found to exceed 70% for some combinations of printing technique and polymer.”
The researchers explained that the durability and size of insulators can be better optimized, which increases the reliability of the high voltage system and lowers component costs, by being careful in choosing their geometry. The data they collected in their study illustrates that dielectric strength anisotropy can be introduced into a 3D printed structure by picking the correct print orientation in respect to the build platform.
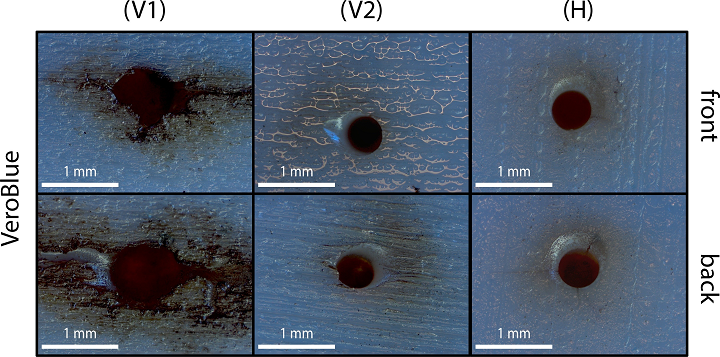
Post-failure microscopy images of VeroBlue samples showing the location of high voltage dielectric failure. The image set contains front and back photos from a failed (V1), (V2), and (H) coupon, tested according to the ASTM D149 Standard. Damage observable in this image set is representative of damage present after dielectric failure in all VeroBlue PolyJet sample coupons.
According to the paper, “The source of dielectric strength anisotropy is largely a consequence of the printing technique employed. Some printing techniques impart susceptibility to dielectric failure based on incomplete curing of starting materials and others through the introduction of structural microdomains or voids that can impart susceptibility to dielectric breakdown to the printed part.”
For their study, the team discussed dielectric failure mechanisms, and also examined the dielectric breakdown of model test structures (coupons) manufactured using four of the most common methods of 3D printing: PolyJet, SLA, SLS, and FDM.
The results showed that the test coupons 3D printed using SLA technology degree of dielectric strength heterogeneity was found to be smallest in the SLA coupons. The “(V) orientation yielding the highest dielectric strength and the (H) orientations exhibiting dielectric strength reductions of 8.3 and 16.1% for WaterShed 11122 and ProtoGen.” As expected with FDM the difference “in dielectric strength between structures printed in the (H) and (V1/V2) orientations was found to be greater than 73% in the ABS-M30 samples and greater than 23% in the ABS-M30i samples.” SLS coupons, had reduced dialectic strength in “(V) orientation, compared to (H) oriented samples. This difference was approximately 31% for the DuraForm HST structures and 16% for the Nylon EX structures.” Polyjet, “showed a dramatic reduction in dielectric strength in the (V1) orientation, compared to the (V2) and (H) orientations. For structures printed using the VeroBlue photopolymer, this difference was greater than 50%; the difference exceeded 70% for samples printed using the VeroAmber photopolymer.”
Non uniform curing was attributed to cause these issues in Polyjet due to printhead placement vis a vis laser, while in SLA the issue was anisotropic curing with different laser pathways occurring in different areas of the part. In SLS, ” Pore networks formed as an artifact of the printing process are likely the strongest contributor to observed differences” while in FDM a Void Layergaps are a probable cause.
Co-authors of the paper are Brad W. Hoff, Sabrina S. Maestas, Steven C. Hayden, Daniel J. Harrigan, Rachael O. Grudt, Michele L. Ostraat, John C. Horwath, and Serhiy Leontsev.
Discuss this story and other 3D printing topics at 3DPrintBoard.com or share your thoughts in the Facebook comments below.