The 2020 Additive Manufacturing Strategies (AMS) event ended earlier this week in Boston. The summit was focused on the business of 3D printing in medical, dental, and metals, so it makes sense that Scott Dunham, the Vice President of Research at SmarTech Analysis, was on hand to give everyone a sense of where we are in these industries, just like at last year’s AMS. SmarTech provides the additive manufacturing industry with industry analysis reports and consulting services, and Dunham began with the company’s metal additive quarterly advisory services. These reports are compiled using data from 10-12 consecutive quarters.

Dunham noted that the messaging and adoption rates have changed for metal AM, and that while we’re all still “working towards the same goals,” we are “drilling down to specific solutions and challenges.”
“Metal additive manufacturing is in a strange place right now,” he said. “From 2016 to 2018, there was lots of hype, lots of investments and growth and attention paid, and the growth was aggressive and accelerated. But now, the past couple of years, we’re in this period where people are saying, ‘What’s happening? We though this technology was supposed to revolutionize things.’ Growth rates don’t always line up with perceptions.”

He got into some of the specific factors that are going into the challenges the metal AM market is facing. There’s a large disparity between metal AM hardware and metal powder sales, which Dunham said tells us that metal 3D printers are viewed much differently than the machine tool systems to which people compare them.
“Right now, the machines are not viewed or utilized in the same way that other popular manufacturing tools are, so people are still looking at this as a longer-term opportunity that still needs development work and may not necessarily always be the right tool for high-volume serial production,” he explained. ” Users now understand they can’t just drop it on the shop floor like a CNC machine. This in some ways is a barrier to growth. There are still plenty of investments being made, though, but maybe we don’t expect those days to last forever now. We may be ending the phase of early adopters and innovators who want to make these investments.”

In the years 2014-2016, the sale of metal machines was averaging just below 30%, then climbed up closer to even, but are now dropping again a bit. According to SmarTech, non-metal 3D printers are still generating most of the hardware sales, but Dunham said we should see more of a 50/50 split into the mid 2020s.

SmarTech has a theory that this leapfrog effect is due to the current two-tiered market scenario. The advanced market focuses on serial applications and high-volume production, while the legacy market consists of applications that have around for a long time, maybe resembling a factory floor, such as injection molding and tool inserts, jigs and fixtures, prototyping or limited series, medical and dental models, and one-off high volume components. Dunham said these markets are both important, but that they each have a “different set of considerations.”

He pointed out that this advanced market will soon grow to over $4 billion worth of AM hardware sold.
“We consider this side of things a little bit further ahead of polymer machine sales,” Dunham explained. “That’s why there’s so much focus on metals.”

So, where is all this growth in the metal AM market coming from? Dunham said that hardware sales is a “good indicator of the pulse of the industry,” and that SmarTech is seeing a lot of growth on what Dunham called “the fringes,” like some of the new companies coming up over the last few years, as well as the legacy manufacturing companies adopting the technology for the first time. He referred to the newer companies, such as Desktop Metal, HP, Markforged, Trumpf, and VELO3D, as “challengers,” while the legacy companies were called “incumbents.”

Next, he talked about metal 3D printing service bureaus, which see a global market of a little over $2 million.
“It’s a pretty big opportunity on the metals side, but not as big as we think it should be, or as big as polymer service bureaus,” Dunham said. “But the footprint of metal additive manufacturing in the healthcare industry is very important, and will continue to be so.”
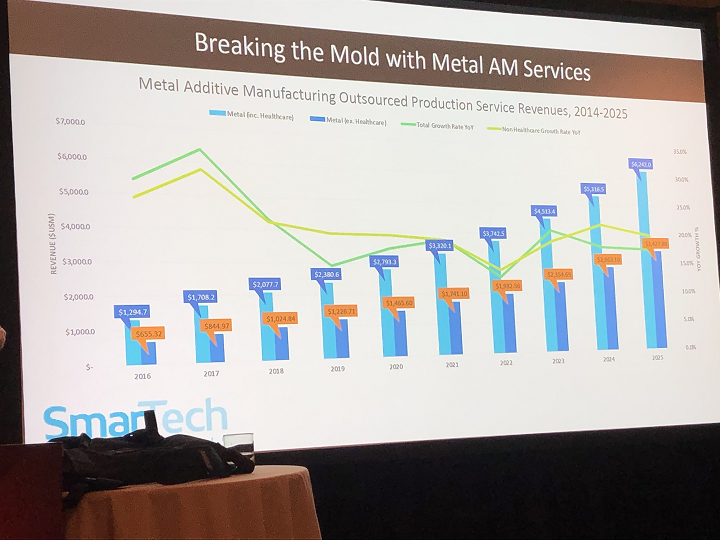
Dunham pulled up a slide about powder bed fusion technology, noting that because the dental industry was so mature in terms of AM adoption, it actually skews the production data in the top two graphs

Bound metal processes, like binder jetting, are currently used often for tooling, and SmarTech forecasts that applications for this technology in prototyping and end-use components will rise. Dunham said that powder-based DED 3D printing is currently “heavily skewed” towards end-use components, in addition to prototyping, and that the “vision of this will likely not change much in the future.

Moving on to the market value of metal parts produced with 3D printing, Dunham said that this number is “hard to assign,” but that investments by end users are likely just south of $5 billion. However, there are lots of high-value parts to consider, which contributes to that number.
“By 2025, we expect that all metal 3D printed parts will exceed 20 billion,” he stated.
In terms of project applications for metal AM, healthcare leads the pack, with crown and bridge substructures and hip implant components at the top of the list. If you remove medical applications from the equation, we’re looking at using the technology to repair high-value turbine blades and aircraft parts, valves and pumps in the oil & gas & energy sector, and more medium-sized industrial components.

“If you’re a supplier in the industry, these are what will succeed,” Dunham said. “The incentive here is to invest in different approaches to metal additive manufacturing.”
Dunham summed everything up by saying that while metal AM is still demonstrating value, entry barriers, such as financial reasons, are also high, which does deter growth somewhat, and that a multidisciplinary approach to it is necessary for growth to continue.

Then I followed Dunham out and into the next room for the SmarTech medical 3D printing forecast, which was wisely titled “Healthcare – the Backbone of Additive Manufacturing.”
“Within the healthcare segment, there are many ways that AM has been and will continue to be leveraged,” he stated. “There are some very industrialized serial, serious manufacturing applications in healthcare, so emphasis is put on the customization of these devices.”
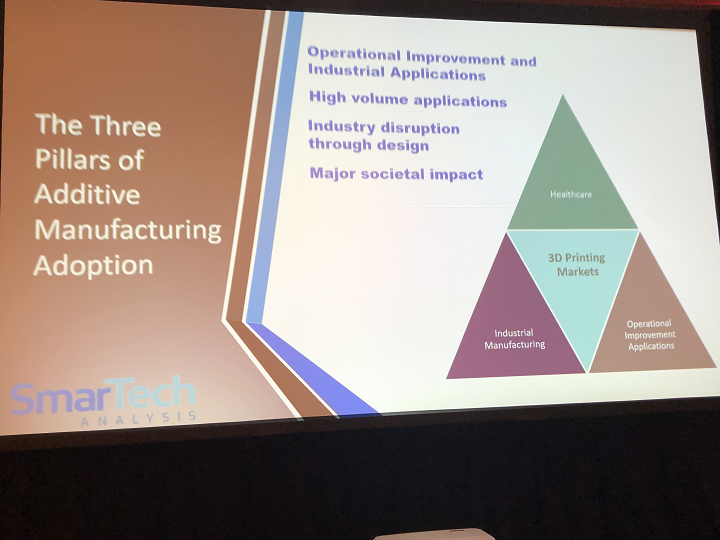
He noted AMS 2020 has a theme of looking at business cases, which is why it’s so heavily focused on dental and orthopedic 3D printing applications.
“We don’t think these are more impactful or important, but these are areas that we’re seeing more challenges and work here,” Dunham explained.

Excluding software numbers, the healthcare portion of the AM market – combining medical and dental applications – is a little over $3 billion dollars; truly, “the backbone of the industry.” These revenue numbers have gone down a bit, because there’s a lot of attention being paid to industrial markets, but Dunham said that SmarTech forecasts a stabilization, stating that healthcare will “continue to be important to overall industry structure for at least the next several years, and into decades.”
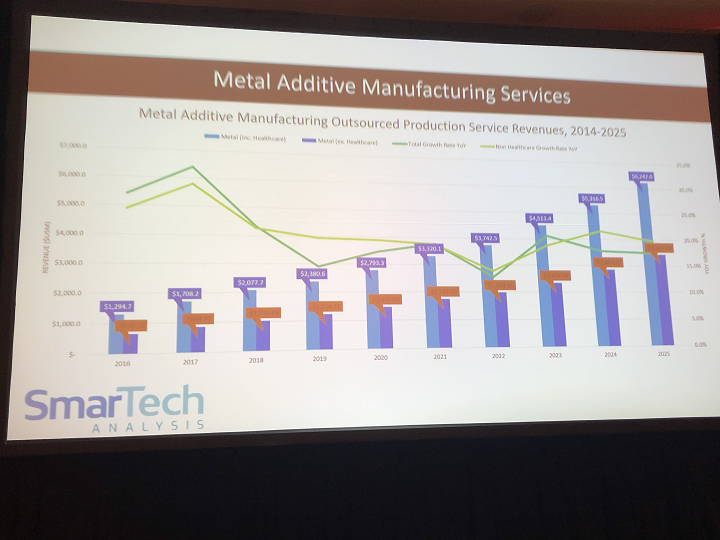
As has been previously mentioned, in comparison to other industries, dental is “fairly mature overall in its adoption of additive manufacturing.” If you’re looking at metal AM used in healthcare, you get into the orthopedic sector, which means you’re looking at implants.

“The longer that we can gather clinical evidence for these implants the better,” Dunham said, noting that this will help ‘build confidence’ with metal 3D printing in the medical field.
Some OEMs are bringing AM in-house, so that they can better control the process to try and ensure a good outcome. A lot of factors go into making medical implants, and if something goes wrong, “clinical efficacy is damaged.”

As of yet, there isn’t a huge push by OEMs for non-metal 3D printed implants, but SmarTech believes this is coming later, for materials like ceramics, and especially for craniomaxillofacial (CMF) implants.
There are plenty of business use cases for metal orthopedic 3D printed implants, and while the hip is still in the lead, about a third of 3D printed implants made now are are spinal. But Dunham said that hip implants won’t dominate the production numbers forever, as the 2025 forecast shows more diversification coming.

Moving to the dental side of things, companies are seeing a lot of success with high speed vat photopolymerization technologies, which Dunham said was expected. But what they didn’t count on was the aligner segment looking to get into powder bed fusion.
“No one process has everything locked down, and we can all benefit from more competition to push the technology forward,” he said.
Dunham said we should expect that 3D printing will ultimately follow the “trend of machines in dentist offices.”
“We expect a pretty healthy growth in investment by dental offices and clinics, though dental labs are still where it’s at from a hardware perspective.”

Dunham pulled up a slide that showed numbers from 2018, and forecast out to 2027, that show specifically what’s going to keep driving the sale of materials and hardware for dental applications. Looking at things like direct aligners and aligner tools, models, surgical guides, and denture bases and trays, it’s clear that he’s correct when he said that there is a lot of “diversification going on out there.”

Stay tuned to 3DPrint.com as we continue to bring you the news from our third annual AMS Summit.
Discuss this and other 3D printing topics at 3DPrintBoard.com or share your thoughts below.
[Photos: Sarah Saunders]
The post Scott Dunham: SmarTech Industry Forecasts for Metal and Medical/Dental 3D Printing appeared first on 3DPrint.com | The Voice of 3D Printing / Additive Manufacturing.