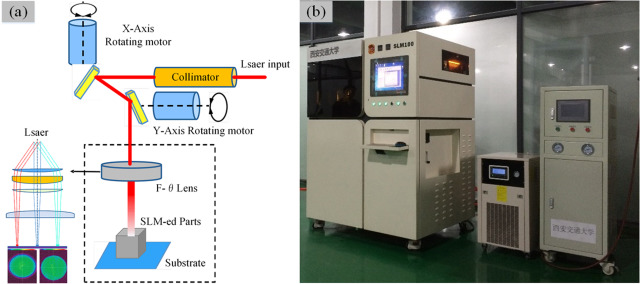
3D printing materials don’t just suddenly appear and get put to use without further thought – there is a great deal of study that goes into them, particularly metal materials. Their behaviors and properties must be known in order to make sure they perform. Especially now that our technology is being used in high-value applications such as aero-engines and medcine research about material properties and performance is growing in both volume and importance. In a new study entitled “Anisotropy of nickel-based superalloy K418 fabricated by selective laser melting,” a group of researchers used 3D printed samples to study the anisotropic mechanical behavior of one particular material – K418, a nickel-based superalloy.
K418 was developed in the 1960s and has been used on a widespread basis in aerospace engines, hot end turbocharger impellers, turbine blades the automotive industry, and more. It has excellent mechanical properties, excellent ductility and fatigue strength, good oxidation resistance at high temperatures, making it a stable and reliable material. It is difficult to machine by conventional methods at room temperature, however, due to excessive tool wearing, high cutting temperature, and other issues. Components made from K418 are often complex, with inner chambers, thin walls, and overhangs, making them difficult to fabricate through one single method such as machining. This alloy is also known as 713C Alloy, 713C,or Inconel 713C Alloy and many derivatives thereof. Inconel is actually a superalloy that was developed in the 60″s but became a catch-all name for the many superalloys developed around the same time frame. Inconel 713LC was a proprietary alloy made by the INCO (INCO was a global Canadian mining company that was the world’s largest producer of nickel, bought by Vale in 2006) and this term plus all of the derivatives are used interchangeably. 713C or as it is also known K418 has been used extensively in rocket engines, turbo stages and in the space and defense industries since the 60’s. SpaceX, NASA, Rocketdyne and others are all using this material to 3D print rocket engines.
Selective laser melting (SLM, also called powder bed fusion, DMLS, Direct Metal Laser Sintering, PBF) has shown itself to be more effective than conventional techniques like machining at manufacturing complex metal components. Thanks to its high temperature and rapid cooling, it also offers better mechanical properties than casting.
In this study, the researchers looked at the anisotropic properties of the K418 alloy. Anisotropy is defined as a difference in physical or mechanical properties when measured along different axes – in other words, a material’s properties could be different along the vertical axis than along the horizontal axis. In FDM (material extrusion) printed parts for example parts are weaker in between layers than laterally.
The researchers used a self-developed SLM 3D printer to produce several cylinders from the K418 material. The samples were manufactured both horizontally and vertically, or transverse and longitudinal. Microstructural anisotropy analysis was performed on both the horizontal and vertical samples.

“The microstructural anisotropy analysis was performed by optical microscopy (OM) and scanning electron microscopy (SEM),” the researchers explain. “Electron backscatter diffraction (EBSD) analysis was used to identify their crystallographic preferred orientation (texture) and to correlate the anisotropy of the mechanical strength with the texture of the material. The results showed that the transverse specimens had slightly higher yield strength, but much significantly higher ductility than that of the transverse specimens with the elongated columnar grains along the building direction.”
SEM micrographs of (a and b) the horizontal samples and (b and c) the vertical samples.
The extremely high thermal gradient and rapid cooling rate during the SLM process led to strong non-equilibrium solidification of the molten pool and the formation of ultrafine grain structure, which resulted in anisotropic microstructures and mechanical properties in different directions.
“The presence of textures renders the SLM processed K418 samples anisotropic in their mechanical properties, indicating that the transverse specimens display a ductile-brittle hybrid fracture mode with a slightly higher yield strength, while the vertical specimens show a ductile fracture mode with a significant increase in ductility,” the researchers continue.
The fact that SLM-produced K418 has anisotropic properties is an interesting finding. The finding may mean that engineers will feel more comfortable using and designing K418 parts using 3D printing. Metal 3D printing is an extremely effective method for producing components from this material, particularly complex structures. Given the performance envelope of this material and its space applications, this is sure to be an article that many will take an interest in. For some more reading on Inconel this article discusses cooling rates and their effects on Inconel 718 and in this article, we look at how Inconel 718 is being used by Launcher.
Authors of the paper include Zhen Chen, Shenggui Chen, Zhengying Wei, Lijuan Zhang, Pei Wei, Bingheng Lu, Shuzhe Zhang, and Yu Xiang.
Discuss this and other 3D printing topics at 3DPrintBoard.com or share your thoughts below.