A number of small companies are attempting to support the supply shortages being faced by hospitals in the face of the COVID-19 outbreak and provide new devices that can reduce the potential risk of contamination for medical professionals. Meanwhile, some large manufacturers that might be deployed for a massive World War Two-style production effort are not stepping up or being government mandated to provide production capacity. In fact, they are even laying off staff in the midst of a health crisis that has also become an economic crisis. (See our comments about GE worker protests in a previous article for an example.)
One such small firm lending a hand to the supply shortages is 3D LifePrints UK, an additive medical device manufacture specialist that makes such items as implants for craniofacial surgery, surgical guides and pre-surgical models for National Health Service trusts, medical device companies, research institutions and others in the U.K., Europe and around the world.
3D LifePrints has been asked by a number of medical institutions to investigate and provide prototype designs for personal protection equipment (PPE) such as Facial mask connectors, mounts for ICU devices that are being moved into other venues, and a simple 3D printable device called the “Distancer.” This last item makes it possible for healthcare professionals to open a door or swipe an ID card without the need to touch potentially contaminated surfaces.
“A doctor goes through a door up to 150 times a day in a hospital. The phrase we hear all the time is ‘the doors are like lava.’ The surface retention of COVID-19 is quite high on stainless steel and plastic,” founder and CTO Paul Fotheringham said.
Fotheringham explained that, in addition to the regular protocol for which hospital employees use their IDs, presenting proper identification in healthcare facilities is necessary to prevent the theft of supplies by hospital staff.
To ensure the maintenance of proper protocol and prevent the spread of the virus, 3D LifePrints UK and the Alder Hey NHS Foundation Trust designed a 3D printed device that can hang off a keychain or lanyard and allow for the slide insert of a user’s electronic ID card. The Distancer features a handle so that the user does not have to touch the actual card, a hook that allows users to open a door, and a flat end for pushing doors closed.
The company is 3D printing the items from materials that will not deteriorate during the cleaning process, which is essential for items that have exposure to COVID-19: nylon PA 12, ABS or anti-microbial PLA that includes an embedded nano-copper additive. It is available in two designs, either flat-packed with living hinges and one-click assembly, which could be mass produced with injection molding, or a 3D printed version.
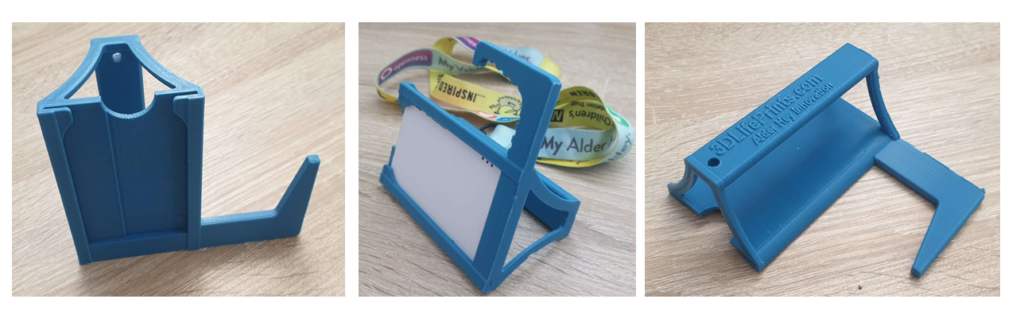
The 3D printed Distancer from 3D LifePrints UK. The file is available for download on the company website. Image courtesy of 3D LifePrints UK.
3D LifePrints is in the process of producing and delivering 4,000 Distancers to NHS hospitals at the moment, while it designs and evaluates other items. The firm is also working with the NHS to develop a specialty connector that can join an off-the-shelf scuba mask to an anesthesia filter that results in a respirator-style device for clinicians (not patients). This is in contrast to the CPAP-type device being developed in Italy using masks from Decathlon. The device is currently being evaluated with the NHS, but it is promising due to the fact that the scuba mask is form fitting and sealed against the face with rubber in a way that is required for the safety of clinicians.
Fotheringham stressed that 3D LifePrints didn’t simply begin making supplies for the U.K.’s medical facilities out of the blue, but is acting on specific requests from the NHS and British hospitals and is working with medical partners to ensure the safety of the devices, while it is his firm’s job to design, iterate and produce the parts to the needs and specifications of the medical professionals.
Typically, these devices would require significant clinical testing and approval from the proper regulatory bodies, but due to the emergency nature of the current public health crisis, devices that have not yet received certification are being fast-tracked for approval.
Other considerations being taken into account are the specific production technologies and materials used to produce parts. More common and less expensive material extrusion printers, for instance, are known to make items that are more porous and have rougher surface finish than those made with selective laser sintering and other polymer powder bed fusion technologies. This reduces the chance for bacteria developing in hidden crevices and makes the parts easier to clean.
As for materials, the company is focusing on the ability of plastics to withstand the use of chemical disinfectants to minimize the degradation of the part over time. In this case, PLA (the most common polymer used in desktop machines and made from corn starch), is not ideal. However, polypropylene, from which 3D LifePrints intends to injection mold its Distancer, is more durable and can sustain repeated cleanings.
Fotheringham urged 3D printing enthusiasts and experts to use caution and proper time management when volunteering to combat the COVID-19 supply crisis. He suggested that these devices should be made in conjunction with medical professionals to ensure proper protocol is followed. One way would be to use official channels such as the FDA in the U.S., who we have reached out to in order to learn more about the safety of 3D printed medical devices made in response to the public health crisis. We will cover this topic in greater depth in a follow-up article.
The post 3D Printing for COVID-19: ID Badge/Door Opener from 3D LifePrints UK appeared first on 3DPrint.com | The Voice of 3D Printing / Additive Manufacturing.