Researchers from the University of California delve into a very important area of 3D printing for the medical field, experimenting with how sterilization processes affect materials. They released their findings in the recently published ‘Identifying a commercially-available 3D printing process that minimizes model distortion after annealing and autoclaving and the effect of steam sterilization on mechanical strength.’
3D printed models are currently changing the face of medicine in terms of patient-specific treatment, allowing for better diagnosis, education for patients and their families (and medical students), along with acting as pre-planning tools and surgical guides.
In relation to FDM 3D printing in medicine, the authors refer back to previous studies concluding that PLA was weakened by sterilization yet strengthened in annealing, explaining that the next viable step would be to find a 3D printing material that can withstand heat treatment and steam sterilization.
The team fabricated four 30 mm cubes as samples for the study, each featuring different infill—designed in Tinkercad and then 3D printed on a LulzBot Mini 3D printer.
Samples were printed all at once, using 0.38 mm layer height and a 0.5 mm printhead nozzle. Materials tested included:
- ColorFabb Woodfill
- Dragons Metallic PLA in All That Glitters Gold
- Essentium PLA in Gray
- Maker Series PLA in Food Safe FDA OK Clear
- Maker Series PLA in White HOT White
- Proto-Pasta HTPLA in White
- Raptor Series PLA in HD Vivid Blue

a) Infill geometries clockwise beginning from top-left: tetrahedral, triangles, grid, zig-zag and b) 3D printed cubes
Each sample was bathed in hot water, with the annealing treatment performed via an 800 W Strata Home sous vide circulating precision cooker.
“The cubes were removed from the hot water-bath and allowed to cool to room temperature without interference. The X, Y, and Z dimensions of the cubes were measured again to quantify deformation and calculate percent changes, a positive percent change indicating expansion and a negative percent change indicating shrinkage,” explained the researchers.
“In order to quantify distortion in either direction, we took the absolute value of these percentages. Subjective observations were noted such as spherical ‘balloon-like’ expansion. We also analyzed whether certain materials consistently expanded or contracted in every axes.”
Samples were then placed in autoclave sterilization pouches and deposited into a Tuttnauer 2540 M autoclave for 45 minutes at 134 °C and a pressure of 375 PSI. Afterward, the samples were cooled to room temperature and then examined for any signs of deformation.

a) Standard Army-Navy retractor and b) strength-optimized Army-Navy retractor designs in inches created in AutoDesk Fusion 360 obtained from Chen et al. c Retractor orientation on the build plate to eliminate need for support material
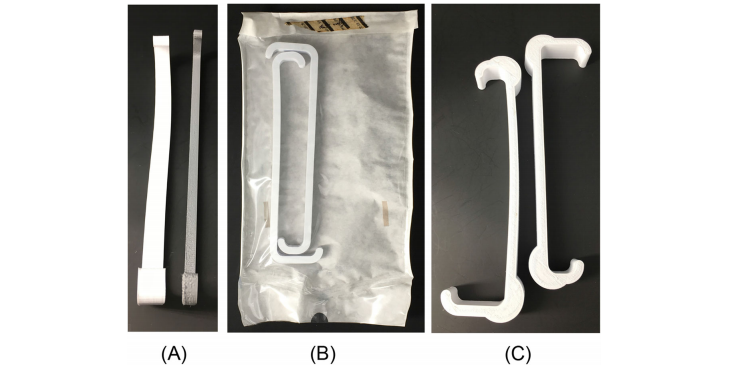
a) Standard retractors warping after hot water-bath annealing and b) after autoclaving. c) Strength-optimized retractor without intervention (right) and warping after hot water-bath annealing (left)
The material exhibiting the least amount of deformation was Essentium PLA Gray. The highest deformation was noted in Maker Series PLA White HOT White.
“After hot water-bath annealing for 30 mm cubes, the infill that deformed the least was ‘grid,’ and the infill pattern that deformed the most was ‘zig-zag.’ After both annealing then autoclaving for 30 mm cubes, the material that deformed the least was Essentium PLA Gray. The material that deformed the most was Maker Series PLA White HOT White. After both annealing then autoclaving for 30 mm cubes, the infill pattern that deformed the least was ‘grid,’ and the infill pattern that deformed the most was ‘tetrahedral.’”
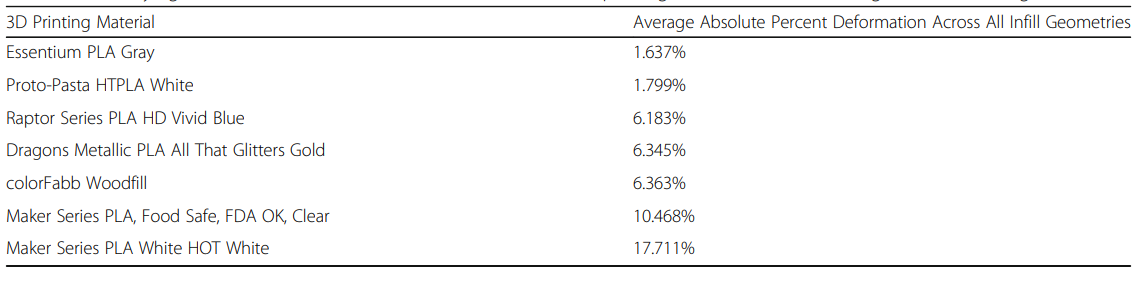
Quantifying absolute deformation in 30 mm cubes across 3D printing materials after annealing then autoclaving

Quantifying absolute deformation in 30 mm cubes across infill geometries after annealing then autoclaving
Maker Series PLA White HOT White was the only material noted to expand in every axis—despite the infill geometry or intervention. Every other material showed variances due to infill. Expansion after annealing usually seemed to suggest ‘direction of distortion’ after autoclaving.
“We acknowledge that dimensional changes and strength limitations may not be a challenge at a lower autoclave cycle, which would require further testing. We have also yet to understand the mechanical behavior of the 3D printed models in this study when they are subjected to multiple cycles of autoclaving and whether they will continue to undergo dimensional change. However, regardless of whether 3D printed PLA surgical instruments are determined to be single or multi-use, these instruments may still be valuable in fields such as aerospace medicine where space limitations exist, or in resource-limited situations where additional instruments are needed,” stated the researchers.
“This study is intended as a pre-clinical evaluation of the mechanical behavior of FDM 3D printing materials following hot water-bath annealing treatment and autoclave sterilization. For FDM 3D printed Army-Navy retractors, further sterilization and biocompatibility validation will be necessary for it to be applied clinically.”
What do you think of this news? Let us know your thoughts! Join the discussion of this and other 3D printing topics at 3DPrintBoard.com.
[Source / Images: ‘Identifying a commercially-available 3D printing process that minimizes model distortion after annealing and autoclaving and the effect of steam sterilization on mechanical strength’]
The post PLA: The Effects of Annealing & Autoclaving on Mechanical Behavior of Desktop FDM Parts appeared first on 3DPrint.com | The Voice of 3D Printing / Additive Manufacturing.