Local Motors burst onto the scene in 2007 using crowdsourcing and cooperative design to develop cars. Their visionary and bold approach lead them to become a nexus for designers, engineers, and gearheads who wish to work together on making vehicles. The Local Motors team has made the Strati, Olli, and Swim, which all use 3D printing heavily in their designs. Local Motors has been trying to usher in a paradigm of collaborative engineering and local production in a very complicated class of product with lots of safety and regulatory issues. It is not often that you find a company that wants to juggle and ride a unicycle at the same time. What’s more Local Motors has been using several 3D printing technologies to make some of the largest functional parts now being used. Local Motors is a very inspiring company for many of us and we decided to interview Greg Haye, their Vice President of Product Management, to find out more.
What is Local Motors?
Local Motors is actually one of two subsidiaries under the parent company, LM Industries. LM Industries is noted as the first digital vehicle manufacturer. A digital vehicle manufacturer means that we can build large, complex cyber-mechanical products from concept to deployment in under a year on our digital thread. This speed lets us bring products to market in a whole new way, designing with a global community of experts, and applying technology such as 3D printing to create and assemble products in small batches at our agile microfactories. We fulfill every step of the creation process from design to production in-house, the result being more stakeholder centric products, built at a lower costs, using fewer resources and taking less production time.
We start with “co-creation,” where we source design ideas using challenges on Launch Forth, our global community of designers and engineers. Once a winning design has been well received by users as a minimum viable product (MVP) it moves immediately into manufacturing, using one of our microfactories powered by robotic, additive and subtractive manufacturing capabilities, which often includes using the world’s largest 3D printer, the Thermwood Large Scale Additive Manufacturing (LSAM) for production. From this process, we’ve made the world’s first co-created car, the Rally Fighter; the world’s first 3D-printed car, Strati; and the world’s first co-created, self-driving, cognitive, electric shuttle, Olli. We also created our own subtractive process and composite materials for use in our vehicles.
Is 3D printing a natural fit for your business model?
The major revolution in direct digital manufacturing is that 3D printing is becoming a manufacturing tool rather than a modeling tool. It’s a huge shift in application fueled by changes in material, machine and processing science.
This shift towards using 3D printing as a manufacturing tool makes 3D printing a critical piece of our digital vehicle manufacturer model. 3D printing enables us to produce products that can quickly evolve to changing consumer demands or shifts in the product’s purpose.
How is 3D printing limited?
The current limitations are solely tied to the relative immaturity of the technology and materials ecosystem as compared to more conventional mass manufacturing processes. While we see ourselves as subject matter experts on the process and its entire ecosystem, we cannot do it alone and have enlisted the industries best partners to move the technology forward together in all areas. The largest limitations exist in the ability to accurately and easily simulate the 3D printed structures in existing CAD and simulations softwares. We have regularly developed our own simulation models to verify our designs performance and efficiency, but it is still a time consuming process.
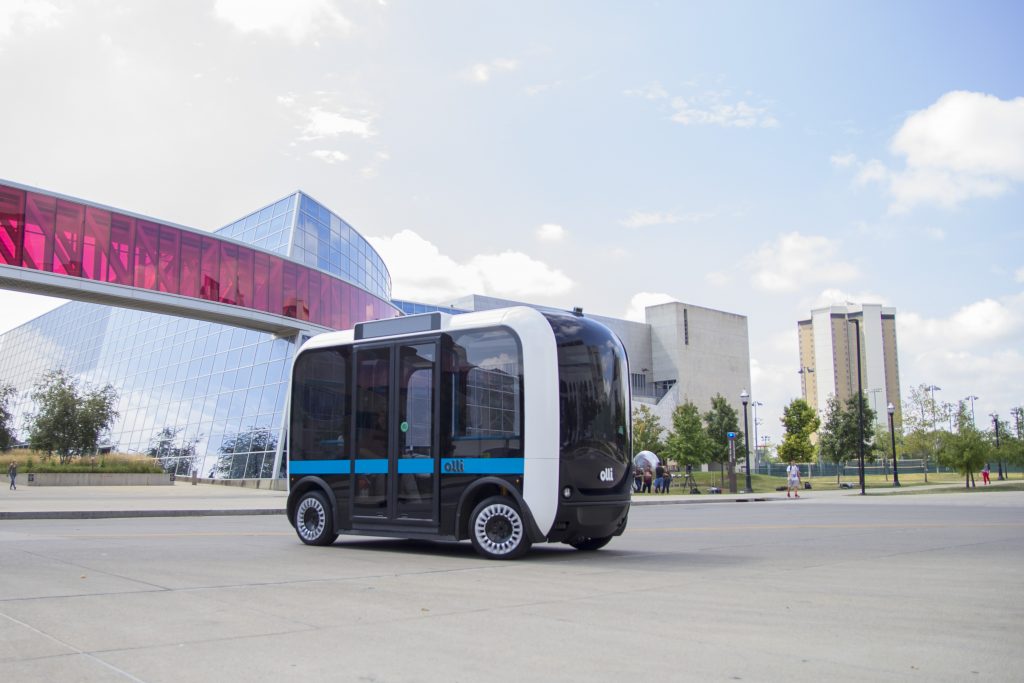
What needs to change to make 3D printing a more viable production technology?
Advances in speed and efficiency in design processes and manufacturing equipment will accelerate its viability for mass commercial usage. This will be driven primarily by advancements in design and simulation software as well as faster, more accurate manufacturing equipment.
What materials are you excited about?
We are excited to work with more and more “green” materials coming into the market such as reclaimed carbon fiber from aerospace industry waste streams as well as bio based materials such as algae based polymers and bamboo fibers. Innovative solutions like these ensure that we can continue to push the bounds of energy efficiency and sustainability.
Do you think that your approach will be suited to a whole host of other products as well?
This is the beauty of the digital vehicle manufacturer business model. Our goal is to produce other products from design to production in-house. We as a company are currently working on mobility solutions, but we’re always exploring the depth and range of mobility products whether its off-roading vehicles, autonomous vehicles or a better wheelchair.
We recognize the massive opportunity to conceptualize, design, prototype and manufacture other products, especially in the realm of complex machinery or products that evolve rapidly due to shifting consumer demands.
Why would I help co-create your products? What the reward for me?
There are a few reasons. The first is the driving force behind many of Launch Forth’s 200,000 community members: following a passion. Launch Forth gives the hobbyist engineer, designer or critical thinker, the opportunity to create out a completely original idea to solve real world problems. It’s an opportunity for our community members to take their passion or side-hustle to the next level by testing their skills and potentially earn recognition for their work.
Another incentive for community members is the access to a community of thousands of like-minded people and the potential to bridge a critical skills gap. Many Launch Forth Challenge submissions are from groups or pairs of community members as Launch Forth creates an infrastructure and network for designers, engineers and innovators to connect and collaborate.
We also, of course, offer cash rewards and the potential to earn a commission for your designs or ideas (if the product is prototyped and produced by Local Motors or one of our industry partners like Airbus, Allianz or the US Marine Corps).
Why is Olli important?
Olli is our 8-person, low-speed, 3D-printed, autonomous, electric shuttle. It’s perfect for things like urban centers in cities, business campuses, hospitals or other large spaces where people need to get around.
This product exemplifies how LM Industries’ digital vehicle manufacturing is capable of creating real solutions for mobility challenges like sustainability and traffic congestion. Designed by a Launch Forth community member and now being manufactured and deployed across the country by Local Motors, Olli was designed and built specifically so that it could be constantly iterated on and easily customized to fit the needs of wherever it was being used. Also Olli was made from tire to roof with true autonomy and safety in mind, unlike other AVs, which are really minivans with mounted sensors and added software.
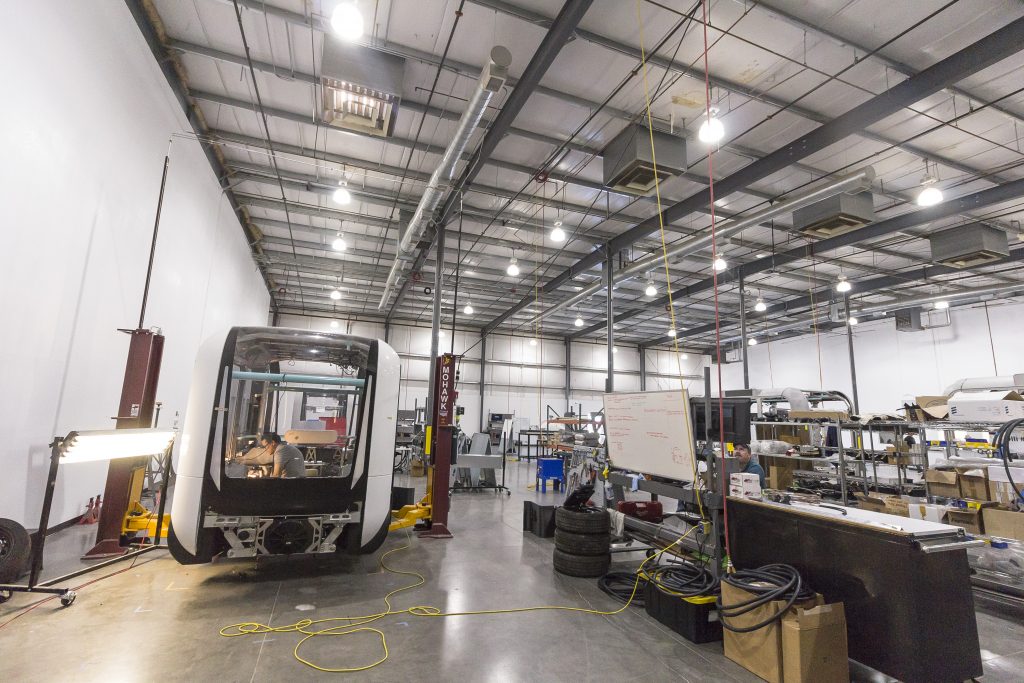
Is there actually an economic advantage to local microfactories?
Absolutely! Our vision for the local microfactories is for them to be as advantageous for the communities as possible. Ideally, the microfactories will employ the community, pushing the local economy forward, and only produce customized products that are really in-demand for the community’s needs.
For LM Industries, the local microfactories improve our digital vehicle manufacturing model because microfactories reduce the minimum efficient scale at which innovative products can be brought to market, by employing a workforce with a high mix of vehicle design, development and marketing capabilities. They are a distributed network of flexible production capacity designed around the low volume local products in production at any given time.
And more generally, microfactories are better for everyone ast they benefit the world as a more sustainable option. Microfactories are more sustainable as they theoretically reduce the environmental impacts of transport emission while they also promote less waste and higher recyclability. By producing more adaptable batches of product using more sustainable materials, and leveraging tech like 3D printing, our microfactories and our digital manufacturer model outpaces others in environmental benefits.
What other products are you working on?
We’re always working with multiple partners to figure out solutions to specific problems by developing new products through Launch Forth challenges. For example, Launch Forth recently completed the co-creation phase of the Island Electric Vehicle (EV) challenge, which called for designs to make a low-speed, rugged, electric vehicle particularly designed for island economies. A winning submission has also already be selected – Isla.
We also recently worked with the US Marine Corps to develop a modular logistics vehicle. This challenge, the first of many, asked for design submissions for a modular logistics vehicles that serve a multitude of operations as well as an unmanned cargo delivery system to improve the operations and well-being of servicemen and women.
What it Launch Forth?
As one of the imperative LM Industries’ subsidiaries, Launch Forth is a SaaS (software as a service) platform for product design powered by a robust community of designers, engineers and solvers. Launch Forth harnesses the speed and potential of crowdsourcing and co-creation to bring breakthrough products to market quickly with a shared community of over 200,000 innovators from around the globe who collaborate on ideas, solve problems and create solutions for challenges both large and small. This community-powered platform pairs design thinking with open innovation and accelerates the product development process for well-respected global giants like HP Inc., Local Motors, General Electric Co. and Airbus.
Local Motors wants to collectively design cars whose bodies are printed out locally.
Can I buy a Strati?
The Strati, the world’s first 3D-printed car is not available for commercial sales at this time.
For additional context, the Strati was the winning design entry among more than 200 received from 30+ countries around the globe during a six-week challenge led by Local Motors in Spring 2014. Designed by the company’s global community and built using the available technology at the Manufacturing Demonstration Facility (MDF) at Oak Ridge National Laboratory (ORNL), Local Motors will produce the Strati, designed specially for urban transportation needs of Chicago.
What do you think the potential is for Large Scale Polymer Composite Additive Manufacturing?
This process is unique in that we can use recyclable materials that can be deposited at a very rapid rate consuming low amounts of energy to build items of size and mass. This has huge potential in manufacturing items of scale such as vehicles, aircraft, ships, architectural building components, and tooling or molds. Most of these things take massive capital, resources, and time to execute. With Large scale additive processes applied this can drastically reduce the cost and foot print needed to manufacture.
Will open innovation outpace internalized innovation?
We view co-creation as the future. It will likely start being utilized by more companies in conjunction with their internalized innovation efforts because the internet gives everyone the basic infrastructure to access and connect with open innovation participants. While open innovation is not the solution for every problem, there is a massive opportunity to develop solutions to pressing problems through mass innovation and idea sourcing.
Why should I as a company partake in open innovation?
Open innovation forces a company to step out of its organization biases since the community of co-creators provide fresh ideas, built out of a diversity of perspectives. New ideas and even reevaluating on how to think about a challenge is invaluable to innovation.
What is holding companies back from co-creation?
For some companies, their infrastructure could be the barrier to utilizing co-creation. Co-creation requires the internal organization to establish a platform to curate, facilitate and sift the ideas coming out of a co-creation community. Also co-creation can be a seemingly intimidating process because a company has to develop a community and the infrastructure to handle the influx of innovation. It’s not easy, but it is mangable and can be an incredibly lucrative opportunity for businesses looking to find a solution.