In today’s 3D Printing News Briefs, Fraunhofer will soon discuss adoption of Industry 4.0-related technologies in a webinar, and we’ve learned that Formnext 2020 is still planned for this November. Moving on, Visagio and DiManEx have announced a partnership. Finally, BCN3D’s technology was used to make an interesting event installation.
Fraunhofer’s Industry 4.0 Webinar
Tomorrow, May 19th, the Fraunhofer Project Center (FPC) at the University of Twente will be holding a free webinar called “The Road to Digitalisation” that explains some of the challenges in adopting technologies related to Industry 4.0, such as 3D printing, as well as the solutions. Industry 4.0 is about optimization, and can offer companies many benefits, such as increased revenue, better quality, and reduced cycle times and costs. But, it can be a tough journey to start, and companies looking to start could use some help.
“Industry 4.0 is all about optimization; from managing big data to efficiency in the production line. All this aims at enabling businesses to make quicker, smarter decisions while minimizing costs. This webinar sets out to explain the challenges and to offer solutions in the adoption of I4.0 related technologies.”
The webinar, featuring Join Biba Visnjicki, Managing Director of FPC, and Thomas Vollmer, Head of Production Quality Dept. from Fraunhofer IPT, will last 60 minutes; register for free here.
Formnext 2020 Still a Go in Frankfurt
As many places in the world are cautiously reopening after recent mass shutdowns due to the COVID-19 pandemic, we need to look to the future. In that vein, Mesago Messe Frankfurt GmbH is still planning to hold the AM industry’s biggest event, formnext 2020, this November 10-13. Recently, the Federal Government and the Federal States of Germany ruled that trade shows are no longer under the ‘major events’ category for health risks, but the health of all the employees, exhibitors, and visitors are still considered the highest priority if the event does indeed take place this fall. That’s why the exhibition organizer is working around the clock to develop an updated health concept, such as introducing contact tracing and decreasing visitor density, along with a supplementary digital/virtual program.
“We remain convinced of the unique value and advantages of a physical exhibition. And although digital interaction will never be able to replace face-to-face contact, it does offer more scope than previously thought possible only a few weeks ago,” stated Sascha F. Wenzler, Vice President of Formnext, Mesago Messe Frankfurt GmbH.
“Ultimately, even in these challenging times, we want to organize a trade show that is as responsive as possible to the current situation and the needs of participants and the market.”
Visagio and DiManEx Partnering to Improve AM Supply Chains
Management consultancy Visagio Ltd and DiManEx BV are partnering to strengthen end-to-end 3D printing usage in supply chains. Companies are looking to conquer supply base disruptions, and by pairing Visagio’s supply chain services with DiManEx’s end-to-end 3D printing platform, they can do so by digitizing their inventory and 3D printing parts on demand, which can delivered all over the world. The collaboration is a representation of how both companies address market needs, especially in these challenging times as COVID-19 disrupts the global supply and demand process.
“Companies are increasingly looking for ways to optimize their supply chains and mitigate risks, such as those brought about by pandemics or geo-political tensions. Our platform embeds 3D printing in supply chains easily, realising the concept of ‘Digital Inventory at your Fingertips, Ordered at a Click of a Button’. Coupled with Visagio’s industry and management expertise, this is a winning combination for supply chain optimization,” said Tibor van Melsem Kocsis, the Founder and CEO of DiManEx.
3D Printed Cisco Live 2020 Installation
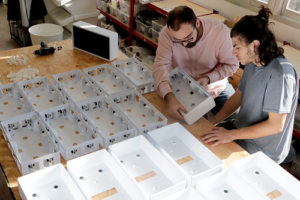
Thanks to 3D printing, it was possible to quickly iterate not only the main design, but also all the smaller parts of the internal mechanisms.
Speaking of collaborations, Barcelona data interpretation firm and design studio Domestic Data Streamers pairs data and arts with storytelling to develop “participatory projects” for community building and education. Its workshop has long used 3D printers from BCN3D Technologies, and recently turned to the technology again to create an installation for the Cisco Live 2020 event. The studio wanted to give attendees “a better experience” by displaying the event schedule on an interactive Recommendation Wall of clickable screens; once clicked, the animated image turned into a QR code, which visitors could scan for more information. The screens had to be custom-made, and so Domestic Data Streamers turned to its in-house printer farm, and the BCN3D Epsilon 3D printer. They used PETG to print over 40 of the main covers in just four weeks, which equaled major cost savings.
“The printers work very well, we count on a very high success ratio, and the support from the team is always quick and helpful,” said Pol Trias, the Head of Design at Domestic Data Streamers.
“It gave us great agility when it comes to functionally and aesthetically validating the designs at a very low cost…our processes were more efficient and much faster thanks to our BCN3D Epsilon.
“This could not have happened without 3D printing. For a project like this one, where you want high-quality results in a short time and within a limited budget, there is no better option than 3D printing.”
You can learn more about the project here, or check out the video below.
Discuss these stories and other 3D printing topics at 3DPrintBoard.com or share your thoughts in the Facebook comments below.
The post 3D Printing News Briefs, May 18, 2020: Fraunhofer, Formnext, Visagio & DiManEx, BCN3D Technologies appeared first on 3DPrint.com | The Voice of 3D Printing / Additive Manufacturing.