BASF’s 3D printing unit, Forward AM, has advanced its partnership with Photocentric to develop and launch a materials portfolio specifically tailored for the LCD-screen based daylight 3D printers from Photocentric. The partnership combines the latest materials and 3D printing technology, improves the quality and efficiency in 3D printing components, and aims to further enable the industrialization of the additive manufacturing industry.
“From the very beginning of our cooperation, together we have aimed to extend the possibilities of advanced photopolymer solutions to address the enormous spectrum of applications opened up by the outstanding performance of this Additive Manufacturing technology. We believe the combination of the expertise gained through decades of BASF research into 3D printing materials, our unique material portfolio, and Photocentric’s remarkable printer technology, genuinely has potential to enable cost competitive parts printing and thus make mass-manufacturing of functional end-use parts a reality,” explains François Minec, Managing Director BASF 3D Printing Solutions.
“The new chemistries we have harnessed for our product offering enable us to meet our customers’ very high mechanical performance demands and realize their mass scale applications. At the same time we are intentionally offering industry-disruptive prices on formulated bulk resin to the market: Jointly we want to move the Additive Manufacturing business towards higher productivity and lower prices per printed part,” adds Dr. Piotr Bazula, Global Product and New Business Development Manager Liquid Formulation Solutions, BASF 3D Printing Solutions.
The two companies had been collaborating on optimizing photopolymer resins and printer parameters, and the next step has been to go to market together with a range of high performance photopolymers: ‘Ultracur3D Powered by Photocentric’. For BASF, this is another specialized application for its Ultracur range of materials, which can be applied to DLP, LCD and SLA based 3D printing technologies.
“Photocentric is deepening its partnership with BASF to facilitate the custom mass manufacture of components in a wide variety of industries. Together we have created a unique combination of software, hardware and chemistry that removes obstacles to using Additive Manufacturing in mass production. Working with Forward AM, we have developed a portfolio of products that delivers the required functional properties perfectly, enables high-resolution mass manufacture, and thereby adds real customer value,” says Paul Holt, Managing Director, Photocentric Ltd.
“This extended range of high performance materials now allows our customers to take full advantage of the large build volume, speed and reliability of Photocentric printers, to move towards the cost-effective, large-scale production of end-use parts,” comments Sally Tipping, Sales Director, Photocentric Ltd.
Ultracur3D EPD 1006 Powered by Photocentric will be the first in an initial set of ten products specifically developed for LCD daylight technology, and the partnership will look to expand offerings within the portfolio progressively.
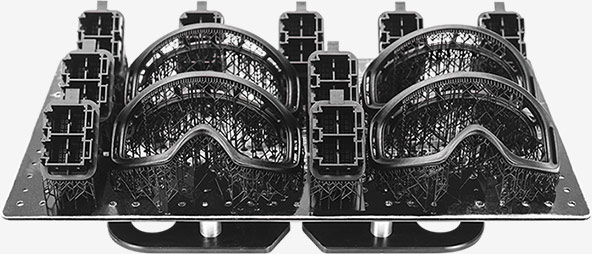
BASF Ultracur material used in the LC Magna. Image Courtesy of Photocentric.
Photocentric, founded in 2002 and headquartered in the UK, has disrupted the vat photopolymerization 3D printing market with its Liquid Crystal 3D printers and material solutions that rely on LCD-screens (using visible or low light spectrum) to cure special photopolymers to print high quality parts, that significantly improve the speed and cost efficiency of 3D printing production, particularly in digital dentistry.
Video courtesy of Photocentric
The polymer market is set to generate $11.7 billion in 2020, as per SmarTech’s “Polymer Additive Manufacturing Markets and Applications: 2020-2029” report, and BASF, a leading polyurethane manufacturer and the world’s largest chemical company (by revenue), has been expanding its presence in the 3D printing industry, to include specialized materials providers, hardware and software providers, as well as service bureaus.
In 2019, BASF had introduced its new 3D printing brand ‘ForwardAM’ and, since then, has engaged in a number of partnerships, investments and acquisitions in the 3D printing ecosystem to expand its presence and offerings in the industrial AM market. The company acquired Sculpteo, partnered with Shapeways to combine the product creation platform’s proprietary technology with the range of additive materials from ForwardAM via a co-branded website; teamed with HP to develop materials for the Multi-Jet Fusion 3D printing platform, with Impossible Objects in its composite sheet layering technology, and with Origin and ECCO for footwear production; invested in Materialise for materials and software; invested in and partnered with PrismLab in the Asian market, with Essentium for Ultrafuse filaments for high-speed extrusion printing, as well as with Owens Corning for glass-fiber reinforced filament materials.
The post BASF and Photocentric Launch Materials for Visible Light 3D Printing appeared first on 3DPrint.com | The Voice of 3D Printing / Additive Manufacturing.