Materialise Q2 2020 revenue declines by more than 20 percent despite software growth
MakerOS Webinar: Make the Most Profit from Your 3D Printing Business
Web-based collaboration platform for 3D printing and digital fabrication companies MakerOS assists users in developing their products faster, no matter the stage or size of the company. It was founded by CEO Mike Moceri, who has copious amounts of experience in design, manufacturing, software, and business: he co-founded the very first 3D printing retail service bureau, located in Chicago, back in 2013, and followed this move by founding 3D printing and product design agency Manulith the next year.
MakerOS is sponsoring a free webinar, which 3DPrint.com is organizing, called “How to Make the Most Profit from 3D Printing,” which will be held on Wednesday, September 16th, 2020, from 2-3 pm EDT. Any digital fabrication business owner or 3D printing shop manager looking to run a more successful business should definitely sign up for this webinar.
“If you don’t understand your costs, you don’t understand your business,” Moceri told 3DPrint.com.
Let’s say that you have successfully completed a 3D printing job for a client, but instead of the substantial profit you were expecting, you only barely broke even. If you care about staying afloat, you’ll want to determine the underlying cause of something like this. That’s why this webinar is so important—you’ll learn how to keep this from happening and gain a deeper understanding of all the various expenses and costs that go into running your 3D printing business. This way, you will be able to set accurate, fair prices and maximize your profits.
“So what we’ll do in this webinar is we’ll figure out what are the core and most important points of cost analysis. We’ll go into detail on how to determine margins and profits for your operation, as well as the philosophy and rationale behind those calculations,” Moceri explained to us.
“We’ll provide a framework and how to think about your business starting with the costs and then we’ll talk about the philosophical aspects of determining margins and ultimately profits for your business.”
By attending this MakerOS webinar, you’ll come away with the knowledge of how to successfully run your digital fabrication or 3D printing shop. The insights attendees will gain can help steer thinking towards a cost-specific perspective, leading to higher profits, and you’ll learn how to recognize subtle things that could negatively affect your margins.
Every webinar attendee will receive access to a spreadsheet that they can use to make calculations and projections to, as Moceri explained, “see what the most optimal path to profitability is for their business.” In addition, the participants will have the chance to learn all of this from someone who has consulted with industry experts from all around the world and has successfully started multiple 3D printing services…Moceri himself.
Featured on MSN, NBC, Make Magazine, the Encyclopedia Britannica, and the D-Business Magazine, which once called him the “Face of 3D printing,” Moceri was once a mentor at TechTown Detroit, and currently serves as a mentor at WeWork Labs in NYC and the Stanley+Techstars Additive Manufacturing Accelerator. He is also an author, having recently published an e-book titled How to Survive the COVID-19 Pandemic as a 3D Printing or Fabrication Shop, along with 9 Lessons for Optimizing Your Product Development Service. You can find both of Moceri’s e-books on the recently launched MakerOS Zone of our website.
What else can you expect to see in the MakerOS Zone? Plenty! There are also free video tutorials, such as “How to Price for SLA 3D Printing” and “Why We Made a 3D Printing Pricing Calculator,” along with the aforementioned pricing calculator itself. The MakerOS Zone also includes articles about the company that have been published on our website, as well as MakerOS articles found elsewhere on the web. Finally, you can access the company’s webinars “How to Optimally Price For Your 3D Printing Service Bureau in 2020,” and “How to Make the Most Profit from 3D Printing,” as previously mentioned. You can register here for the latter, which will be held on Wednesday, September 16th, 2020, from 2-3 pm EDT.
The post MakerOS Webinar: Make the Most Profit from Your 3D Printing Business appeared first on 3DPrint.com | The Voice of 3D Printing / Additive Manufacturing.
ExOne reports revenue decline in Q2 2020 despite growth in recurring customers
Nexa3D Acquires NXT Factory, Introduces Eco-Friendly 3D Printing Washing Solvent
While Nexa3D may specialize in manufacturing super-fast stereolithography 3D printers, the company has been branching out recently, and narrowing its focus on the materials side of things. It launched the high-performance polymer xCE-Black in May, followed soon after with the announcement of a partnership with Henkel to commercialize xMED412, a high-impact material for printing biocompatible medical and wearable devices. Now, Nexa3D has announced that xCLEAN, its new eco-friendly washing solvent for resin and photopolymer 3D printers, is commercially available.
“I am very proud of our entire team for stepping-up during this unprecedented pandemic, and quickly pivoting internal developments and external collaborations to adeptly support our growing customer base and communities. “Throughout this challenging period, we’ve continued to expand the range of our high impact, durable photoplastics, and we are rolling out new productivity tools for the additive manufacturing industry,” said Nexa3D’s CEO and Co-Founder Avi Reichental. “Together with our growing partner network, we are committed to helping our customers improve their design agility, and supply chain resiliency by reducing the time required to produce functional prototypes and production parts from hours to just minutes.”
xCLEAN, compatible with most photopolymeric resin printers, including close loop systems, automated cleaners, and washing units currently on the market, and is safer to handle than other popular cleaning solvents, though it’s not been cleared to use in the cleaning of parts 3D printed out of biocompatible resins.
This material is easy to recycle, as well as recover with the help of a vacuum-assist distillation unit, and doesn’t need any of the typical adherence to shipping regulations or special storage that most post-processing photopolymeric parts require.
“xCLEAN’s development is a powerful reminder that necessity is the mother of invention. We were forced to explore alternatives to isopropyl alcohol (IPA) during the initial Covid-19 surge as IPA became extremely scarce and costs skyrocketed,” explained Nexa3D’s Head of Customer Success Brent Zollinger. ” After considering dozens of candidates, we zeroed in on xCLEAN and quickly embraced it as our go-to cleaning solvent. Having processed thousands of serial production parts in our flexible factory with superior results, we decided to share this incredible cleaner with our customers and invite the entire photopolymer 3D printing community to give it a try.”
Made from molecules that are smaller than DPM and TPM, xCLEAN is extremely effective, and doesn’t have any of the gross, greasy residue that you get with these two alternative materials; just rinse it off with water. It’s also sustainable, with three times the saturation limit of IPA, which means that it lasts three times as long and requires fewer changeovers and generates less waste.
xCLEAN can be ordered for immediate delivery here, or from one of Nexa3D’s authorized resellers. A single 5-gallon container will cost you about $320. To see the material in action, check out the video below:
But materials haven’t been the company’s only focus during COVID-19—the company just announced that it has acquired NXT Factory, which manufactures ultra-fast selective laser sintering (SLS) production systems powered by its proprietary Quantum Laser Sintering (QLS) technology.
“We are thrilled to join forces with Nexa3D and together unleash the power and potential of our products. COVID-19 propelled both of our companies to demonstrate the unique capabilities of our complementary additive manufacturing power as we quickly ramped into full production of personal protective equipment for frontline healthcare workers. This crisis has helped showcase the incredibly rapid and flexible nature of our combined additive manufacturing capabilities compared to traditional manufacturing and demonstrates how vulnerable the global manufacturing supply chain is to unexpected disruptions,” stated Kuba Graczyk, the Co-Founder and CEO of NXT Factory. “Together, we are committed to taking additive manufacturing to the next level and realizing its full potential.”
The two companies have entered into an agreement that states Nexa3D will acquire all the outstanding shares of NXT Factory, and the stockholders and boards of directors of both companies have approved the transaction, the details of which were not disclosed publicly.
By combining NXT Factory and Nexa3D’s high-speed technologies, the company is strengthening its capabilities and portfolio of production-grade materials. Nexa3D will now have access to NXT Factory’s range of powder fusion, supply chain-approved plastics, which will essentially double its addressable market and strongly position it for increased growth in the industry.
Leveraging its relationships with other key material suppliers, Nexa3D will be able to diversify its revenue streams by offering access to 100% of currently available polymer applications
“Stereolithography (SLA) and Selective Laser Sintering (SLS) are the cornerstones of additive manufacturing of plastics, so I am honored and proud to be part of the team that is uniting the two companies that are taking both technologies to their full potential. Having worked side by side with the Nexa3D team over the past four years in Ventura, California, sharing facilities, exhibiting jointly at tradeshows, witnessing untold technological breakthroughs and rapid expansion, there is no doubt in my mind that this is the perfect match for both of our companies. I am excited to join this dream team and contribute towards the creation of a leading fourth generation additive manufacturing powerhouse,” said Tomasz Cieszynski, Co-Founder and CTO of NXT Factory.
Subject to customary and other deal-specific closing conditions being met, the transaction should be completed as soon as practically possible.
(Source/Images: Nexa3D)
The post Nexa3D Acquires NXT Factory, Introduces Eco-Friendly 3D Printing Washing Solvent appeared first on 3DPrint.com | The Voice of 3D Printing / Additive Manufacturing.
3D Systems announces strategic refocus and 20% staff cut following Q2 financial results
HP and Dyndrite Partner to Create Next Generation 3D Printing Solutions
Seattle startup Dyndrite announced a strategic new partnership with Hewlett Packard (HP) to license Dyndrite’s geometric kernel technology and power the next generation cloud and edge-based digital manufacturing solutions. By combining HP’s end-to-end manufacturing management expertise with Dyndrite’s cutting edge additive technology, HP is hoping to deliver a software platform capable of powering the additive manufacturing (AM) factories of the future.
In 2019, 26-year old Harshil Goel’s company Dyndrite emerged out of stealth mode to reveal the world’s first GPU-native geometry engine, the Dyndrite Accelerated Geometry Kernel (AGK). Since geometry kernels were first introduced decades ago, they have been a crucial component in advancing 3D CAD/CAM/CAx software. Still, the company claimed this software have not kept pace with changing computational architectures, modern manufacturing technologies, and modern design needs. In order to address this challenge, Goel teamed up with veteran mathematicians, computer scientists, and mechanical engineers to develop a new solution that could level the playing field so that the manufacturing hardware no longer surpassed the software, facilitating the AM industry to reach its potential.
“The promise of 3D printing is to deliver unique parts and tools not possible through traditional methods, and do so on an industrial and global scale. For this to happen the industry must evolve and Dyndrite’s mission is to accelerate this change,” said Goel, now CEO of Dyndrite. “HP is a clear leader in industrial 3D printing and this collaboration speeds the game-changing impact our technology brings to the AM community at large. We applaud HP’s vision and look forward to a long and fruitful partnership for years to come.”
The new alliance builds on HP’s focus on expanding its software and data platform to help customers fully realize the transformative power of 3D printing technology. Through the development of new solutions that leverage the Dyndrite kernel, HP expects to improve efficiency, enhance performance and quality, enable mass-personalization, automate complex workflows, and create scalability and extensibility for continued partner and customer innovation. The ultimate goal for both companies is to change how the software works in the AM industries, driving new performance and functionality.
In that sense, Dyndrite claims that its fully native GPU Kernel easily handles additive specific computations such as lattice, support, and slice generation, in some cases reducing compute times from hours or days to minutes or seconds. For heavy use cases, the Dyndrite kernel is naturally scalable with access to additional GPU nodes, whether locally or in the cloud and provides both C++ and English-readable Python APIs, making application development accessible to a wide variety of users, including non-programmers such as students, mathematicians, and mechanical engineers. Probably what most interests HP is providing developers and original equipment manufacturer (OEM)s with a tool capable of representing all current geometry types, including higher-order geometries such as splines (NURBs), surface tessellations, volumetric data, tetrahedra, and voxels, allowing the development of next-generation applications and devices.
“Innovations in software, data intelligence, and workflow automation are key to unlocking the full potential of additive manufacturing,” said Ryan Palmer, Global Head of Software, Data and Automation of HP 3D Printing and Digital Manufacturing. “We are committed to advancing our digital manufacturing platform capabilities and this strategic collaboration with Dyndrite is an exciting next step on the journey.”
Building upon HP’s leading position as a behemoth technology firm, the company has acquired and partnered with dozens of companies to broaden its ecosystem and accelerate innovation and speed product development and supply chain efficiencies. HP also supports numerous 3D printing and digital manufacturing open standards to ensure data interoperability and choice for customers.
As a global provider of industrial-grade 3D printing and digital manufacturing solutions, HP offers systems, software, services, and materials science innovation to its customers. These solutions already include numerous software and data innovations, like its HP 3D Process Control and HP 3D Center software offerings.

Dyndrite’s new GPU-powered, python-scriptable, additive manufacturing build processor at work (Image courtesy of Dyndrite Corporation)
The new HP and Dyndrite partnership builds on a relationship that first began when HP became one of the inaugural members of the Dyndrite Developer Council, a group of leading 3D printing systems, software, and solutions providers. Along with Aconity3D, EOS, NVIDIA, Plural Additive Manufacturing, and Renishaw, HP was chartered with steering the future direction of the company’s roadmap. The driving force behind Goel’s venture is advancing the design and manufacturing software tools used today, which he said were built more than 30 years ago and are becoming bottlenecks to today’s creativity and productivity. Especially when compared to the manufacturing hardware that over the past few years has given rise to new design philosophies and a whole new paradigm of manufacturing production.
In this sense, Dyndrite is creating next-generation software for the design, manufacturing and additive marketplace, with the goal to dramatically increase the workflow and efficiency of AM technologies. With Dyndrite joining HP’s global ecosystem, HP advances 3D printing and digital manufacturing solutions, improving the overall experience for its customers and moving the industry forward.
The post HP and Dyndrite Partner to Create Next Generation 3D Printing Solutions appeared first on 3DPrint.com | The Voice of 3D Printing / Additive Manufacturing.
Lubrizol Buys into 3D Printing Parts and Services via Avid Acquisition
The Lubrizol Corporation has purchased Avid Product Development, a 3D printing and engineering services company, marking a significant development for additive materials and the larger industry as a whole.
While it may be best known for its engine oils, Lubrizol is a roughly $6.5 billion specialty chemical company owned by Warren Buffet’s Berkshire Hathaway. As such, it is one of a number of chemical producers that have been increasing their stakes in the 3D printing materials space, the biggest of which is BASF. The Ohio-based firm has already released its own additive feedstocks (specifically thermoplastic polyurethanes for fused filament fabrication and Multi Jet Fusion), but this acquisition marks a strong move for Lubrizol, as it expands from a material manufacturer to an engineering, 3D printing and post-processing service provider.
Based in Loveland, Colorado, Avid offers design for additive manufacturing, as well as prototyping and production using selective laser sintering, Multi Jet Fusion, fused filament fabrication and stereolithography. Additionally, the company provides post-processing for 3D printed parts. The company serves the footwear, consumer goods, industrial and medical segments and won the 2019 Colorado Company to Watch award. According to a press release sent to 3DPrint.com, Lubrizol plans to combine its expertise in materials, applications and testing with the aforementioned offerings from Avid in order to accelerate 3D printing adoption in key industries.
Gert-Jan Nijhuis, General Manager of 3D Printing Solutions at Lubrizol Engineered Materials, said of the deal:
“Lubrizol continues to invest in opportunities that bring new differentiated solutions to our customers. The acquisition of Avid Product Development greatly enhances our ability as a 3D printing solution provider, offering complete product solutions from material development to printing and post processing services, delivering end-use products for our key markets.”
As industrialized nations purportedly strive to shift from fossil fuels to renewable energy sources, oil companies may be looking to supplement demand through petrochemical markets. ExxonMobil admitted as much in a 2018 investor report, stating an expected 30 percent increase in petrochemical demand by 2025.
In turn, not only are we seeing an increasing number of major chemical companies enter the 3D printing industry, but we are seeing them diversify within that space as well. BASF has made the biggest movements, putting money into three different 3D-printed parts makers by partnering with Shapeways, investing in Materialise and acquiring Sculpteo. Mitsubishi Chemicals is also trying its hand at 3D printing parts through a pilot program with AddiFab.
By purchasing Avid, Lubrizol gets out ahead of a number of other chemical companies not described so far, including Dow/DuPont, Eastman, SABIC and more, who seem to be more focused on making materials at this point than using them. However, we have also witnessed a number of investments by companies like DSM and Arkema into new technologies and startups that could greatly expand their foothold in 3D printing once those startups take off.
All of these players are changing the landscape of the 3D printing industry, likely into a more industrially focused space. How that will look in the years to come is anyone’s guess, particularly given the uncertainty of global events at the moment, but the impact will be impossible to overlook.
The post Lubrizol Buys into 3D Printing Parts and Services via Avid Acquisition appeared first on 3DPrint.com | The Voice of 3D Printing / Additive Manufacturing.
3DEXPERIENCE: A Virtual Journey, Part 1
Due to the ongoing COVID-19 crisis, this year’s 3DEXPERIENCE Forum by Dassault Systèmes had to be re-imagined as a virtual event, just like so many other conferences. At 1 pm EDT on July 29th, nearly two months after the in-person event was meant to have taken place in Florida, the company began the live stream of the Plenary Session for “3DEXPERIENCE: A Virtual Journey,” a series of digital programming that replaced the annual North America customer event.
Unfortunately, the webinar seemed to be having issues, which continued on and off over the next two hours of the live stream, so I missed pieces here and there. Technical difficulties happen all the time at live events, too, so the only real difference here was that I couldn’t raise my hand and say, “I’m sorry, the audio and picture cut out, could you repeat that please?” Luckily, Dassault had the webinar up to view on-demand the very next day, so I was able to go back and check out the parts that I had missed.
Erik Swedberg, Managing Director, North America, Dassault Systèmes, got things started with his segment on “Business in the Age of Experience: Challenges and Opportunities for North America,” which focused on manufacturing and supply chains, and why companies looking to transform, some sooner than they’d hoped due to the pandemic, should “invent the industry of tomorrow,” rather than trying to digitize the past or the present.
“Yesterday, businesses focused on automation of the manufacturing system; this is Industry 4.0. Today, many industrials are digitizing the enterprise system. It’s not enough. You need to create experiences. Tomorrow, the game changers will be those with the best developed knowledge and know-how assets. Why? Simple. Because the Industry Renaissance is about new categories of new industrials creating new categories of solutions for new categories of consumers,” Swedberg said.
He mentioned Tesla and Amazon, companies in Silicon Valley working to create autonomous vehicles, and fab labs creating and printing smart, connected objects.
“The 3DEXPERIENCE platform is a platform for knowledge and know-how—a game changer, collaborative environment that empowers businesses and people to innovate in an entirely new way,” he continued. “Digital experience platforms for industry, urban development, and healthcare will become the infrastructure for the 21st century.”
Swedberg explained how 3DEXPERIENCE can allow any business to become social, by connecting employee innovation into the system where the company’s products are designed. This was a common theme today, which you’ll be able to see later.
He also explained that, with Dassault’s 13 brand applications—such as SIMULIA, CATIA, and SOLIDWORKS—the company can serve a wide variety of industries, helping its customers on their journey to invent tomorrow’s industry.
“In summation, we are in the experience economy, the Industry Renaissance is here, and world events are accelerating the need for digital transformation. As the world changes, we will partner with you for success,” Swedberg concluded. “We have the people and the insights to help you on your journey.”
Dassault’s Vice Chairman & CEO Bernard Charlès was up next, speaking about “From Things to Life.” He first said that he hoped no one on the live stream, or their loved ones and colleagues, had been impacted by the COVID-19 crisis.
“We’ve gone through a tough time, all of us. And we are with you, and we are learning a lot also from the crisis,” Charlès said.
Even though I’ve worked from home for nearly four years now, other aspects of my life have been turned upside down in the last few months, and I felt a kind of solidarity whenever the session’s speakers brought up how all of our lives, and our industry, have changed. Charlès also congratulated everyone signed into the live stream on working together, and continuing to innovate, during the pandemic; the continuing health crisis was another theme that threaded throughout the plenary session.
He said that the 3DEXPERIENCE platform is about inclusiveness, “because it means ideas and people connecting.” He shared some of the work that 3DEXPERIENCE users had accomplished during the recent and varied quarantines, such as creating respirators, improving logistics, and working to make the quality of airflow in hospitals better. He said that all of these projects were done on the 3DEXPERIENCE cloud.
“So many of you accelerated the cloud implementation, to be able to work from anywhere, especially from home, during confinement time.”
He mentioned that we are moving from a product economy to an experience economy, and that, in the long run, companies will continue to produce, and maintain ownership of, products and services throughout the life cycle, while their customers will get to enjoy the experience.
“That will accelerate innovation for a sustainable world,” Charlès said.
Next, he talked about a few companies that have been using the 3DEXPERIENCE platform for interesting projects, like California-based Canoo, which dreams about refining urban mobility with an electric vehicle that can be used as a service or subscription, rather than being owned by individuals.
In order to create innovation, Charlès said, you need to be sure that your digital platform will work, and Canoo stated that 3DEXPERIENCE hit the mark here, helping to speed things up in the product development process.
He then talked about Arup, a company that’s using the 3DEXPERIENCE platform to create a virtual Hong Kong for city planning purposes. Arup is working to make Hong Kong a smart city, and the platform is helping the company in this endeavor; for example, Arup and Dassault just completed a project called the Common Spatial Data Infrastructure Built Environment Application platform…say that three times fast.
Finally, Charlès explained that the role of life sciences is to “protect what we care about,” and said that industry pioneers are coming up with new and different ways to diagnose and care for people. He stated that creating new healthcare experiences is a complex project, because it means converting big data into smart data and simulating real world situations in a virtual world. Luckily, 3DEXPERIENCE can help with this.
“3DEXPERIENCE…is a system of operation, because the platform can help you run your business, and the platform should also help you invent a new business model,” Charlès concluded. “The common values across all the industries we serve is putting the human at the center of everything we do.”
Next, Renee Pasman, Director of Integrated Systems at Skunk Works for Lockheed Martin, provided an overview of using the digital thread, and the 3DEXPERIENCE platform, for the product lifecycle, “and how Lockheed Martin is leveraging it to drive increased affordability, efficiency and collaboration throughout the lifecycle.”
“…Our projects cover the entire product life cycle that you might imagine from an aerospace and defense type of program, all the way from conceptual design through modeling and simulation, manufacturing, to sustainment and end of life,” she explained. “And one key part of the Skunk Works culture in the last 75 years has been very close collaboration across all of those areas. What we’ve learned as we have started this digital thread initiative is that by giving our workforce these latest tools, we’ve been able to make that collaboration easier, to be able to make it go faster, to be able to bring data in sooner, make better decisions, see what the impacts are of those decisions, and use that to guide where we are going.”
She explained that the product lifecycle “really starts with design,” and said that by starting this new Near Term Digital Thread/Affordability initiative and giving its workforce the 3DEXPERIENCE tools, Skunk Works has learned that collaboration is faster and stronger, and that we “make better decisions to guide where we’re going.”
We’ve all heard about this issue before—there are two versions of an important product document, and some people update one, while others update the other, and no one has a clear idea of which version is correct and most up-to-date. It’s frustrating to say the least. But Pasman noted that by using the 3DEXPERIENCE product lifecycle management platform, “we’re starting to see efficiency benefits now.”
Pasman also said that the Skunk Works team has learned something “unexpected” with the platform, and that’s the social collaboration it provides, which allows users to “make changes with a level of certainty.”
“We hadn’t necessarily focused on this area, but our teams really used this environment to collaborate better, and found it to be very useful to have all information in that single source of truth.”
Pasman also noted the usefulness of having a life cycle digital twin, as it “allows us to tie it all the way back not just to manufacturing but actually back into design, and making sure the data flows in the digital twin seamlessly.”
“I think if you talk to maintainers or sustainment and users, there’s a lot of time spent putting data into different systems. By making it easier to do that, it allows people to focus on the hard parts of their job, and not just the data entry parts,” she explained. “Collaboration between different areas and getting data flowing is where we see a lot of the benefit from 3DEXPERIENCE, from affordability and product quality perspectives. We’re focused now on how to take the next step in this journey and improve schedule and affordability to fit into the market space that we are working in today. That’s where a lot of the work from our digital thread initiatives have been focused.”
Next up, Craig Maxwell, the Vice President and Chief Technology and Innovation Officer for Ohio-based motion and control technologies leader Parker Hannifin, spoke about “Simple By Design.” The multinational company has been integrating some of the tools that Dassault has been developing over the past few years, which has been valuable to the company.
“When we look at any enterprise or business, we saw these as opportunities that would manifest themselves as complexity,” he said in reference to the image below. “An average customer experience, which might be the ability to ship on time, with high and consistent quality. Of course, inconsistent delivery would manifest itself as complexity. High cost would be complexity…and then all of this would beget complexity in its many forms.”
He said that all of these complexities can add up to new opportunities to take the company on the path to high performance. Maxwell also explained that the company’s traditional simplification efforts had revolved around design and organizational structure, explaining that 80% of any business’s profits and sales come from 20% of its portfolio.
“So by slicing and dicing that, could we eliminate complexity? The answer is a resounding yes,” Maxwell said.
He explained that 70% of a product’s cost is design, while 30% is labor and overhead, like lean manufacturing and the supply chain. The key is to spend less time on L&O, or conventional simplification, and work harder to reduce business complexity in that 70% design range. He said there are hundreds and thousands of decisions made on the L&O side, which, while easier to change, had a more limited impact on the long life cycles of their products.
“There were processes in place that we felt could address that reactively, not proactively,” he said.
With design, the decisions made were “relatively few and quick,” even though they could make a significant impact, because they would be difficult to change, mainly due to expensive tooling.
“We believe that if we can address design complexity, it would enable us to move faster and to grow by taking market share,” Maxwell said.
He explained that the cross-functional team Parker Hannifin set up to address “new” product complexity in a proactive way knew early on that there are two different value streams of Simple by Design.
“New products, for sure, but also core products,” he said. “If you look at where the money is, new products get a lot of attention, but our business is core products…they’re undergoing revisions constantly because our customers are asking for things that are different.”
The team decided to tackle new products first, and spent a lot of time working on design-related objectives, which is where they thought “a lot of the complexity and cost was being created.” He explained that the team wanted to keep the customer at the center of their attention, figure out what their pain points were and what they wanted, and get rid of the things that didn’t add value.
“The first principle of Simple by Design is design with Forward Thinking. With that deep customer engagement, anticipate what your customers are going to ask for in the future,” he explained. “Are there things we can do to the design of the product that, without increasing cost, that will allow us to make changes to it at a later date? The second principle is Design to Reduce, so to reduce complexity, can we reduce the number of new parts that we have, can we reduce the number of new suppliers we have? Can we eliminate proprietary materials that might be hard to come by?
“Design to Reuse – can we reuse parts that already exist? Why do we need to invent new when we’ve already got very similar or exactly what we need released into the system…and then finally, if we do the first three, we should see flow in the factory. We should not see the kind of bottlenecks that we experience today.”
Maxwell said that Dassault comes in with software tools that provide access to data, which “is the big game changer.” He talked about all of the many books and catalogs that were in his office at the beginning of his career, noting that engineers today just can look at all of this information online, because they have access to data. Parker Hannifin estimates that it has about 26 million active part numbers, which is a lot to keep track of, and Maxwell said that roughly 45% of a typical design engineer’s time is spent searching for information.
“So if I had access to the data behind that 26 million part numbers, what would happen? And today, I’m not embarrassed to say that generally we don’t. There’s a lot of things that we do many many times, we’re a very diversified company, we’re global, ” Maxwell said. “It’s not unusual for people to spend their entire career here in the company and not talk to a lot of other operating divisions…outside of the one they work in. So what if I could connect them and give them access to information, what kind of leverage might I enjoy?”
He brought up the company’s usage of Dassault’s EXALEAD OnePart, which can give multiple division access to this kind of information. Maxwell said that this software was used “early on in testing and in value creation,” which was very helpful in finding duplicate parts or component-level parts that already exist in the system, so no one had to create a new part.
Below is a test case he showed of Parker successfully using Dassault tools. FET is an industry-standard 6000 PSI thread to connect couplings, and there are a lot of competitors for parts like this. The company was working to design a new series that was more of a premium product than the original FET.
“We applied simplified design principles,” he explained. “There’s four different sizes, it was bespoke, very distinct from the FET series that was standard. It was fully validated and ready for launch. But it added 147 component parts to the value stream.”
The team focused here, and used the simplified design principles to make the decision to recycle the validated part, and go back to the drawing board.
“Is there an opportunity for us to reuse some of the parts that already exist in the FET series in the new 59 series, but still maintaining the 59 series’ premium features and benefits?”
You can see the results of keeping things simplified above—123 parts were eliminated, while keeping the series at 100% function. The new 59 series shares 90% of its components with the original FET series, and no additional capital was spent on equipment. Costs and inventory went down, and delivery went up, which Maxwell called a “great example of flow.”
Swedberg then introduced Florence Verzelen, Executive Vice President, Industry, Marketing, Global Affairs and Workforce of the Future for Dassault Systèmes, who would discuss “How to Transform the New Normal into an Opportunity.”
She opened by discussing how the COVID-19 crisis has changed everything, such as having to stay home and social distancing, and I’m sure we all agreed with this statement. But now we’re entering a new phase of building back after the pandemic, and building back better, as businesses reopen.
“How do you think you managed during COVID?” she asked. “Are you ready to transform, to perform better in the new normal world? Do you know how to become more resilient and therefore be prepared for the next crisis?”
Verzelen discussed some of the stark numbers coming out of the pandemic, such as 53 million—the number of jobs considered to be “at risk” during confinement and quarantine.
“In the 21st century, we have never seen a crisis of this amplitude,” she said. “And when it happens, as industry leaders, there are really two things, two imperatives, we should consider. Ensure the survival of our company, and contribute to the safeguard of the economy.”
There are five actions to take here, and the first priority is to protect employees and make sure they can safely do their jobs.
Verzelen explained that the 3DEXPERIENCE tool SIMULIA can help with this in many ways, such as simulating the airflow in a building’s corridors. She also said that companies can “implore their employees to work from home” without disruption, which is possible thanks to Dassault’s cloud solution.
The second thing necessary to keep your company surviving is maintaining its financial health.
“COVID-19 has affected the liquidity of many companies,” she said. “Less revenue, more costs…and in order to make decisions, you need to be able to build a scenario.”
Online sales can help keep companies afloat during a crisis, and also help maintain the connection to customers. Dassault can help with these as well through its data analytics solutions and digital tools. Adapting your company’s marketing and sales for an online experience is the third way to ensure its survival.
The fourth thing is to safeguard the supply chain. The disruption of one supplier can decimate production all the way down the whole chain, which can include suppliers in locations all over the world.
“During a crisis, it becomes essential to know where the weak points are,” Verzelen said. “This again we can do thanks to digitalization and thanks to data analytics.”
Finally, companies need to help the ecosystem, otherwise it will not survive. Dassault made sure that all of its solutions and tools were readily available on the cloud so that all customers could continue to work to keep the ecosystem going.
But, even though the world is slowly coming out of confinement, Verzelen warns that “it’s not over yet.” The use of automation will likely increase, and e-commerce is skyrocketing in Italy.
“It’s the beginning of a new phase. It’s the beginning of what we call the new normal.”
A lot of decisions need to be made when you’re restarting a business. Again, Dassault can help with this by building scenarios, so companies know the right steps to take, and in what order, to successfully reopen.
“We all have to change,” Verzelen said. “We’re developing new capabilities for employees, and making learning experiences available online to make sure your teams are ready. Returning to business probably means we need to rethink our supply chain, and we know that a contact-limited economy is here to stay. So you should push for e-commerce, and be prepared to work in contact-limited economy.”
She stated that the 3DEXPERIENCE allows companies to “unlock unlimited value,” and help us cope during this new normal.
“There are many ways to be resilient, and all of those ways are linked to innovation and sustainability.”
The paradigm has changed, and we need to be realistic going forward, and focus on sustainability in operations and business models, such as turning to additive manufacturing if your usual supplier can’t get you what you need in time.
“With the 3DEXPERIENCE platform you can create this kind of business model…create more efficiently, design more quickly,” she said.
“In a nutshell, we are going through very difficult times right now…But this crisis can also be seen as an opportunity to rethink what we do, and build back better.”
Finally, Swedberg introduced three additional Dassault panelists for the final discussion: Dr. Ales Alajbegovic, Vice President, SIMULIA Industry Process Success & Services; Garth Coleman, Vice President, ENOVIA Advocacy Marketing; and Eric Green, DELMIA’s Brand Marketing Vice President. These three are in charge of the content for the rest of 3DEXPERIENCE: A Virtual Journey, as it continues on:
- “Fueling Innovation for the New Agile Enterprise,” August 26th
- “Modeling & Simulation, Additive Manufacturing,” September 23rd
- “Enabling Business Continuity Using the Cloud,” October 14th
Green said that three themes would be articulated in these upcoming sessions, all of which will fall under the “sustainable operations” umbrella: data-driven decision-making, leveraging agile success and being agile for success, and business resiliency. Coleman mentioned that the many customer references and testimonials found on the 3DEXPERIENCE site provide many examples of how the platform has helped customers innovate across every industry…even wine-making! Dr. Alajbegovic said that they are “very excited” about the upcoming modeling and simulation sessions and additive manufacturing panels.
“In our sessions, we will look at ways to enable the marriage between modeling and simulation, thus revolutionizing design,” Dr. Alajbegovic said.
It’s not too late to register for 3DEXPERIENCE: A Virtual Journey, so sign up today to enjoy access to further digital programming from Dassault Systèmes.
The post 3DEXPERIENCE: A Virtual Journey, Part 1 appeared first on 3DPrint.com | The Voice of 3D Printing / Additive Manufacturing.
3D Printing Webinar and Virtual Event Roundup, August 2, 2020
It’s another busy week in the 3D printing industry that’s packed full of webinars and virtual events, ranging in topics from medical materials and flexible electronics to polypropylene and market costs. There are four on Tuesday, August 4th, two on Wednesday, August 5th, and the week will end with the last KEX webinar on Thursday, August 6th.
ASTM’s AM General Personnel Certificate Program
Last week, the ASTM International Additive Manufacturing Center of Excellence (AM CoE) training course all about additive manufacturing safety. Now, the AM CoE is starting its AM General Personnel Certificate course, which will begin August 4th and run through the 27th. One of its key focus areas is promoting AM adoption, and helping to fill the knowledge gap with training for the future AM workforce is a major way that the AM CoE is doing this. The online course is made up of eight modules covering all the general concepts of the AM process chain, and attendees will learn important technical knowledge that will allow them to earn a General AM Certificate after completing a multiple-choice exam.
“This course will feature 17 experts across the field of additive manufacturing to provide a comprehensive course covering all of the general concepts of the AM process chain to its attendees. The course will occur over the month of August consisting of two modules per week for four weeks. More information can be found in the course flyer.”
Online registration will open soon. This is not a free course—you can learn about the fees here.
Nexa3D & Henkel: Medical Materials Webinar
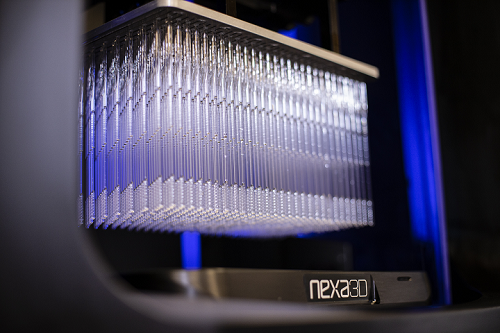
Recently, SLA 3D printer manufacturer Nexa3D and functional additive materials supplier Henkel announced that they were partnering up to commercialize the polypropylene-like xMED412, a durable, high-impact material that can be used to 3D print biocompatible medical and wearable devices; in fact, it’s already been cleared to print nasal swabs. Now, the two are holding a virtual leadership forum on “Advances and Breakthroughs in 3D Printed Medical Equipment and Device Materials,” like xMED412. Topics to be discussed will include new possibilities for 3D printing medical equipment and devices, the benefits of using AM to fabricate these products, and the advantages additive manufacturing has over medical materials made with traditional manufacturing. Panelists will engage with attendees after the discussion in a live Q&A session.
“3D printing has introduced all kinds of new possibilities for developing stronger and lightweighted equipment but we’ve only scratched the surface of what’s possible. These past few months have driven the industry to new realms of creativity with the need to quickly deliver medical supplies, devices and materials. With new lightweight, sturdy materials designed to withstand impact, moisture and vibration, access to lower cost medical equipment is becoming more widely available thanks to 3D printing.”
Register here for the 45-minute virtual forum, which will take place on Tuesday, August 4th, at 1:30 pm EST.
SOLIDWORKS Design Solution Demonstration
Also on August 4th, at 11 am EST, Dassault Systèmes will be holding a brief demonstration of its 3DEXPERIENCE SOLIDWORKS design solution. This demonstration of the platform’s capabilities will last just 22 minutes, and will teach attendees how to collaborate and stay connected to data while creating new designs with SOLIDWORKS when connected to the 3DEXPERIENCE platform, exploring the latest tools available on the platform, and design a model using both parametric (3D Creator) and Sub-D modeling (3D Sculptor) tools with the help of complementary workflows.
“SOLIDWORKS is the design tool that has been trusted by engineers and designers around the world for decades. Part of the 3DEXPERIENCE WORKS portfolio, SOLIDWORKS is now connected to the 3DEXPERIENCE platform with cloud-based tools that enable everyone involved in product development to collaborate on real-time data. Doing so enables you to efficiently gain the insight needed to create revolutionary new products.”
You can register for the demonstration here.
NextFlex Innovation Days
The last August 4th event in this week’s roundup is NextFlex Innovation Days, the flagship showcase event for the consortium of academic institutions, companies, non-profits, and local and federal governments that make up NextFlex and are working to advance US manufacturing of flexible hybrid electronics (FHE). The event will run through Thursday, August 6th, and will include panel discussions on how FHEs are continuing to transform the world, including a panel featuring a special guest speaker from the US Senate. FHE innovations that will be highlighted during the event include a wearable biometrics monitor from Stretch Med, Inc., flexible skin-like sensors from Georgia Tech, a flexible UV sensor out of the NASA Ames Research Center, miniaturized gas sensors that GE Research integrated into wearables and drone formats, and Brewer Science’s integrated FHE solutions in a brewery application.
“This multi-day virtual event will feature over 50 customer, partner and member company presentations online available at no cost. If you watch live, you’ll have the chance to interact with presenters and flexible hybrid electronic (FHE) experts from the comfort of home via webinars and virtual labs, or you can watch video demonstrations at your availability.”
Register for NextFlex Innovation Days here.
Additive America & HP AM Webinar
HP is currently sponsoring a webinar series highlighting business in the AM industry that worked to transition their production processes in order to help fill the supply chain gap that’s been caused by the COVID-19 pandemic. This week’s episode, which will take place at 1:30 pm EST on Wednesday, August 5th, will feature a discussion with Additive America on “the lasting impact of COVID-19 on additive manufacturing.”
“Listen in on conversations with our customers to learn how they have adapted to the change in business climate, whether it be a shift in production workflow to address supply chain gaps, enabling a faster product development cycle to support changing customers’ needs, or bridge production.”
You can register for this webinar here.
Prodways, BASF, & Peridot Talk Polypropylene
Also on August 5th, Prodways, BASF, and full-service product development company Peridot Inc. will be holding a free webinar together called “Rethink Additive Manufacturing with Polypropylene.” Led by Lee Barbiasz from Prodways, Jeremy Vos from BASF, and Peridot owner Dave Hockemeyer, the webinar will focus on how PP 1200, a tough, chemically resistant, low density polypropylene enabled by BASF for selective laser sintering (SLS) 3D printing, is being used to bridge the gap between additive manufacturing and injection molding, as well as growing opportunities and applications in short run manufacturing. Hockemeyer was an early adopter of the material, and will share a variety of use cases for PP 1200. There will also be a chance for attendees to ask questions about the material.
“3D Printing with Polypropylene is here! After more than three decades, 3D printing technology has evolved the ability to 3D print polypropylene material. Polypropylene enables scalability in manufacturing, reduces barriers to entry in 3D printing and reduces manufacturing costs by 25-50%!”
You can register for the webinar, held on Wednesday, August 5th, from 1-1:45 pm EST, here.
KEX Knowledge Exchange on Market, Costs & Innovation
The last entry in this week’s roundup will take place on Thursday, August 6th. KEX Knowledge Exchange AG, a former spinoff of Fraunhofer IPT, held webinars in July about powder bed fusion technology and post-processing, and the last in its series will be an online seminar on Market, Costs & Innovation. Sebastian Pfestorf from KEX and Lea Eilert, the project and technology manager for the ACAM Aachen Center for Additive Manufacturing, will be the speakers for this webinar.
“In this online seminar, you will learn:
-
Current AM market and industrial trends
-
What markets the technology has penetrated the most and why
-
How to go about implementing AM, including risks and uncertainties
You can register for the hour-long webinar here. It will take place on Thursday, August 6th, at 8 am EST.
Will you attend any of these events and webinars, or have news to share about future ones? Let us know!
The post 3D Printing Webinar and Virtual Event Roundup, August 2, 2020 appeared first on 3DPrint.com | The Voice of 3D Printing / Additive Manufacturing.