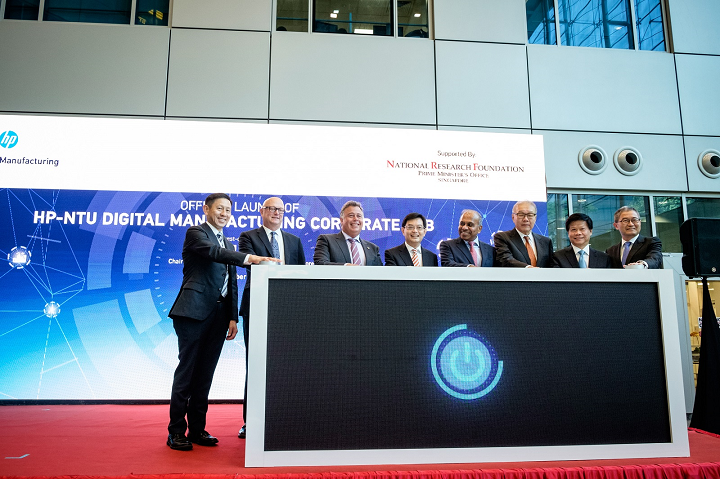
Launch of the HP-NTU Digital Manufacturing Corporate Lab. L-R: Ng Tian Chong, President of HP Asia Pacific and Japan; HP CTO Shane Wall; HP CEO Dion Weisler; Minister for Finance and Chairman of the NRF Heng Swee Keat; NTU President Prof Subra Suresh; NRF CEO Prof Low Teck Seng; NTU Vice President (Research) Prof Lam Khin Yong; and NTU Provost and Vice President (Academic) Prof Ling San.
HP Inc. has a solid presence in Asia, with expansions in recent years into Japan and China. But it’s been in Singapore since 1970, and the country is home to its Asia Pacific & Japan Regional Headquarters, global supply chain control towers, and print manufacturing. Now, the company is partnering with Nanyang Technological University (NTU Singapore) to open Singapore’s newest corporate research laboratory.
The HP-NTU Digital Manufacturing Corporate Lab, which is HP’s largest university research collaboration worldwide and first in Asia, is meant to help advance digital manufacturing and drive the economic development, innovation, skills, and technology necessary to advance the Fourth Industrial Revolution.
![]()
(Clockwise from bottom right) NTU Vice President (Research) Prof Lam Khin Yong and HP CTO Shane Wall signing the corporate lab partnership agreement, witnessed by HP CEO Dion Weisler; Minister for Finance and Chairman of the NRF Heng Swee Keat; NTU President Prof Subra Suresh; and NRF CEO Prof Low Teck Seng.
“The World Economic Forum estimates more than $100 trillion in value will be created by digital transformation across all industries in the next 10 years. HP is helping lead the development of the underlying technologies, like 3D printing, that will enable the benefits of this transformation,” said Dion Weisler, CEO and President, HP Inc. “Singapore is one of our key worldwide technology development and manufacturing centres in Print technology. The HP-NTU Digital Manufacturing Corporate Lab will significantly deepen our involvement here and serve as a nucleus for this ecosystem. We are proud to collaborate with NTU and we are looking forward to this becoming a blueprint for innovation, collaboration and economic progress.”
The $84 million lab is located at NTU and launched by Heng Swee Keat, Minister for Finance and Chairman of the National Research Foundation (NRF), which is a department within the Prime Minister’s Office. The NRF facilitates corporate labs setups through public-private partnerships, and its 13th lab, the HP-NTU Digital Manufacturing Corporate Lab, is the 7th located at NTU.
“Corporate laboratories are an integral part of our strategy to anchor joint R&D partnerships between our universities and companies in areas that have direct relevance to the growth of industries in Singapore,” said NRF CEO Professor Low Teck Seng. “The HP-NTU Digital Manufacturing Corporate Laboratory is significant to our long-term competitiveness in the advanced manufacturing sector, and ensures that we stay relevant in the Fourth Industrial Revolution that is evolving and growing rapidly world-wide. It will also strengthen our capabilities to support multinational companies for expansion from Singapore into the region.”
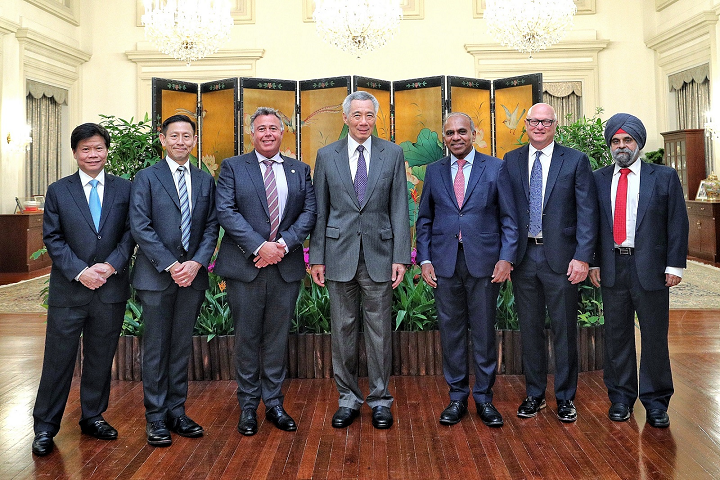
Senior leadership from NTU and HP paid a courtesy call on Prime Minister Lee Hsien Loong, at the Istana, where they spoke about the new partnership between NTU and HP. L-R: NTU Vice President (Research) Prof Lam Khin Yong; Ng Tian Chong, President of HP Asia Pacific and Japan; HP CEO Dion Weisler; Prime Minister of Singapore Lee Hsien Loong; NTU President Prof Subra Suresh; HP CTO Shane Wall; and NTU Board of Trustee member Inderjit Singh. [Image: MCI]
The partnership between HP and NTU was signed today by HP’s CTO and Head of HP Labs Mr Shane Wall and NTU Vice President (Research) Professor Lam Khin Yong. Weisler, NTU President Professor Subra Suresh, and Guest-of-Honour Minister Keat. The 100 researchers and staff at the new lab will focus on digital manufacturing technologies, particularly 3D printing, artificial intelligence, cybersecurity and customization, machine learning, and new materials and applications.
According to Professor Suresh, NTU’s partnership with HP is “a significant milestone.”
“NTU has established deep capabilities and is a recognised leader in the areas of machine learning, data science and additive manufacturing,” said Professor Suresh. “These cutting-edge technologies are now an integral part of NTU’s education and research ecosystem, and the NTU Smart Campus serves as a test bed for them. This is aligned with Singapore’s vision of transforming into a Smart Nation.
“Together with HP Inc., a renowned innovator and leader in the tech industry, NTU seeks to address today’s fundamental challenges with solutions that will benefit both industry and society in Singapore and the world, such as developing automation that is capable of boosting manufacturing productivity.”
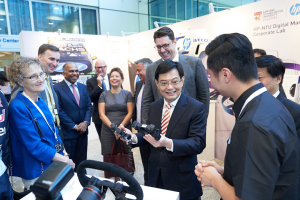
Minister Heng Swee Keat (center) looking at 3D printed automotive parts at the NTU-HP Digital Manufacturing Corporate Lab launch showcase.
The new lab, an important pillar of the university’s Smart Campus initiative, supports the country’s continuing drive toward industry transformation in 3D printing and digital manufacturing. The national strategy to develop a knowledge-based, innovation-driven economy and society, known as the Research, Innovation and Enterprise (RIE) 2020 Plan, lists Advanced Manufacturing and Engineering as one of its four technology domains, and the corporate lab will build on HP’s strong manufacturing and research capabilities to keep driving Singapore’s innovation.
“One out of every three jobs worldwide, more than 30% of global GDP, and nearly one-third of carbon emissions are related to manufacturing. We are committed to innovating with purpose, not only driving the technology breakthroughs that improve HP’s business but also contribute to creating economic opportunity and improving people’s lives,” said Weisler.
Included in the collaboration between HP and NTU Singapore is the development of educational curriculum covering design for additive manufacturing, which will cover such areas as user experience, security, data management, and business models.
Once formally launched, the HP-NTU Digital Manufacturing Corporate Lab will prioritize 15 separate projects in order to gain a better understanding of AI and machine learning, so that the 3D printers in the lab can autonomously predict and fix any issues. The projects also seek to better understand cybersecurity, as a way to improve end-to-end point security infrastructure and malware mitigation, and new materials and applications, like 4D printed, shape-changing smart systems, advanced polymers for manufacturing, and bioprinting models for fabricating tissues.
Discuss this story and other 3D printing topics at 3DPrintBoard.com or share your thoughts below.
[Images: NTU Singapore unless otherwise noted]