Seeking solutions for ‘buckling’ in wall structures and failure in parts, Chalmers University of Technology PhD researcher Bharet Mehta turned to additive manufacturing processes for improved performance in production. Mehta recently presented a thesis, “Enhanced performance of magnetic floating devices enabled through metal additive manufacturing,” to Chalmers.
The author focuses on creating a family of floating devices, using 316L stainless steel. With thin shells of sub-millimeter thickness welded together, the metallic floating structures are meant to resist buckling activity. Mehta explains that the ultimate goal of the study was to create stronger parts that are still light in weight, with the thesis focusing only on laser-based powder bed fusion (LPBF).
AM processes were considered beneficial due to reduction of parts during production and less assembly, greater accuracy and less post-processing, flexibility in design, rigidity in materials, and customization. Mehta listed typical limitations: higher surface roughness, few materials available, increased manufacturing times, and lack of consistency in terms of quality.

λ or buckling factor of safety comparison between sections with different stiffeners under hydrostatic loads: a) λ for an empty tube; b) λ for a tube
with longitudinal ribs; c) λ for a tube with only 5 weld rings; d) λ for a tube with
longitudinal ribs and weld rings
During experimentation, the addition of stiffeners enhanced performance of the part. This was especially effective when high buckling strength or less weight was required.
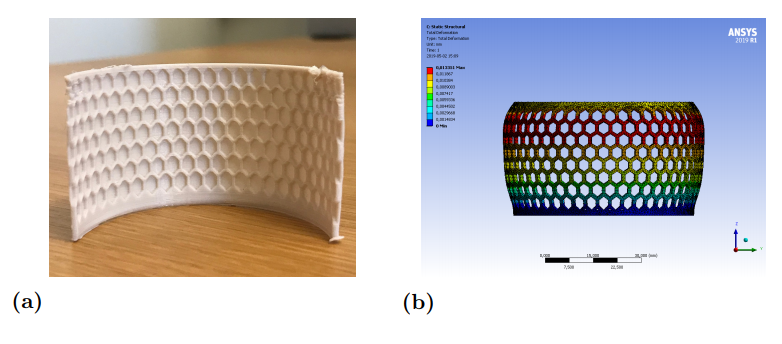
Effect of poisson’s ratio in selection of stiffeners for thin shells: a) representation of modified honeycomb as expected to be printed on the thin shell b) honeycomb loaded with uniaxial compression, as shown
While not all the details regarding the sample part were disclosed, Mehta did describe it as a ‘thin shell cylindrical section which is closed by welding and is supported by some ring stiffeners to make it bear the hydrostatic loads.’
“As a modification to the original part, a slight modification was done based on ANSYS simulation results, producing a simulation-based design to thicken the rings,” said Mehta. “The same was done to avoid the failure at rings and change the load path, in order to get a skin type buckling failure.”
Another customized design was also fabricated but with thicker rings and bigger holes in the rings, allowing for similar weight, and improvement in terms of buckling.

Difference between original ring stiffeners as used by ABB vs a modified ring stiffener: a) the original ring design with 0,5 mm thickness rings ; b) modified ring design with 1 mm thick rings with bigger inner diameter
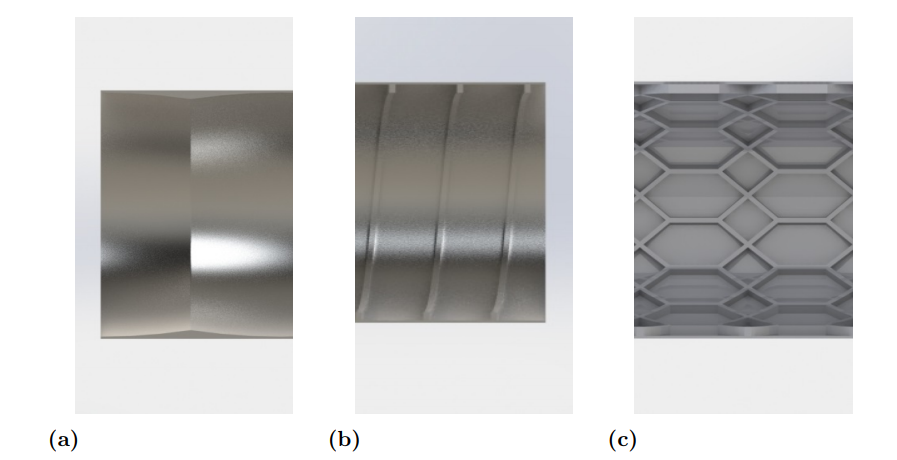
Different design concepts which are suitable for metal AM: a) with some small protrusions as ring stiffeners; b) with helical supports as stiffeners; c) with honeycombs as stiffeners
“As discussed in theory, linear buckling of the part was not the correct representation to what would actually happen when the part fails. This is because hydrostatic buckling represents a plastic failure and the collapse pressure is used to define the maximum loads for the part. Hence, a sturdier design, which incorporated non-linearity, was planned to be tested and prove the design’s performance in real life. Several factors were found to affect the performance while switching to AM, and experimental setups were defined accordingly,” explained Mehta.
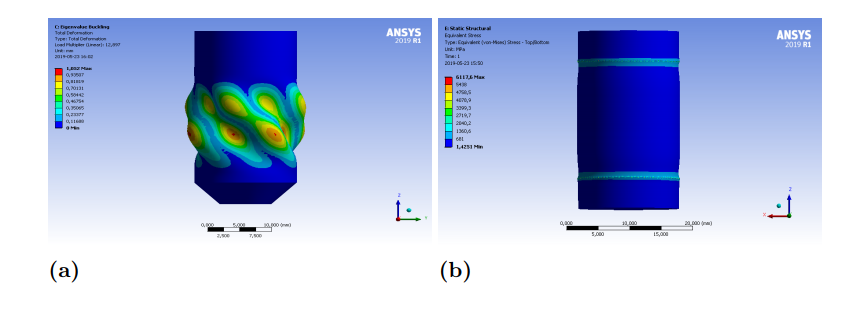
ANSYS results showing Euler buckling test results and static structural testing results: a) Euler buckling showing the theoretical factor of safety to be 12,9 at 8124 N uniaxial load and 0,4 mm thickness at cylindrical section; b) stress generated at 8124 N in the part, showing the average stress value in the range of 401 MPa at the 0,4 mm thickness
Prints were performed at AMEXCI, Sweden, on an EOS M290, and at ABB Corporate on the ReaLizer SLM 50.
“The simulation results showed about 3 times improvement in specific buckling strength in one of the designs – isogrid stiffened AM part with hollow rings, as can be seen in table 6.1 [below]. The stress levels shown were well below the ultimate strength of the material, which means that the idea might work. However, this design concept has to be proven experimentally,” stated Mehta in conclusion.
“These floating devices take modularity to the next level, by giving an opportunity for optimization of lattice based stiffeners and hollow rings to define ‘new materials.’ Hence, strength to weight ratios can be adjusted to become as high as aluminum or as low as some plastics.”
Improvements in metal 3D printing are continually being made by researchers looking into strengthening mechanical properties, investigating the effects of porosity, and testing metal powders and other materials. What do you think of this news? Let us know your thoughts! Join the discussion of this and other 3D printing topics at 3DPrintBoard.com.
Source / Images: ‘Enhanced performance of magnetic floating devices enabled through metal additive manufacturing’]
The post Metal 3D Printing: Enhancing Magnetic Floating Device Systems appeared first on 3DPrint.com | The Voice of 3D Printing / Additive Manufacturing.