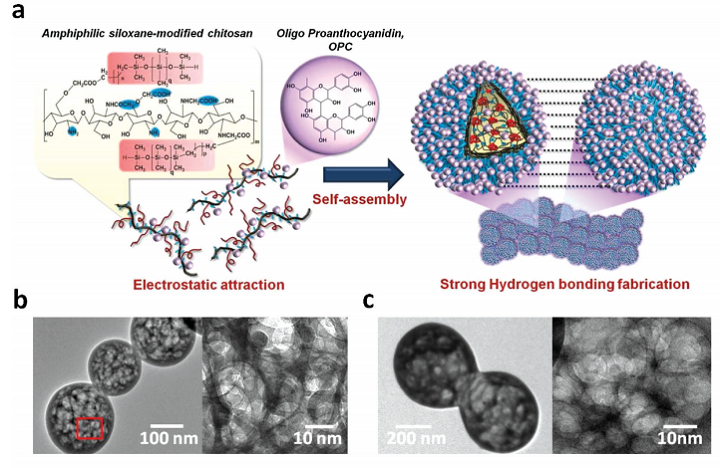
a) Schematic illustration of the mechanism for formation of nanogel-based membrane based on the self-assembly of OPC-incorporated amphiphilic polydimethylsiloxane-modified N, O-carboxylic chitosan (OPMSC), followed by hydrogel-bonding interaction of OPC. The TEM images display the network structure of b) PMSC and c) OPMSC spherical nanogels.
3D printing has been used in the past to help treat degenerative diseases, or at least make it easier to cope with them. In terms of neurodegenerative diseases, implanted prosthetic devices are often used, but adverse biological reactions in host tissues can result in signal failure. it’s important to create tissue that can mimic the mechanical and structural properties of neural implanted devices, and while flexible polymer-based implants have helped to alleviate some injuries, the mechanical stress doesn’t quite match brain tissue. That’s why a lot of research has been conducted about using conductive polymer (CP) composites or conductive hydrogels to coat the devices so the biocompatibility and electrochemical performance of neural electrodes can be improved.
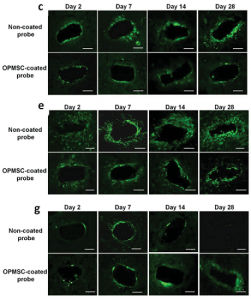
Representative fluorescent images demonstrate tissue responses around the tip of the non-coated probe and the OPMSC-coated probe at days 2, 7, 14, and 28 post-implantation. (c) ED1 staining; (e) GFAP staining; (g) NeuN staining.
But, a team of researchers from China and Taiwan say that it’s more important to design biocompatible coatings for implanted devices that mimic mechanical and structural properties of brain tissues, so tissue responses after long-term utilization can be reduced.
The researchers believe that 3D nanostructural coatings should be developed for the insulated regions, and not the implant electrode sites, so implants can interface with nearby brain tissues with more stability. They explained their findings in a recently published paper, titled “Multifunctional 3D Patternable Drug-Embedded Nanocarrier-Based Interfaces to Enhance Signal Recording and Reduce Neuron Degeneration in Neural Implantation.”
“Although the nanomaterial-based substrate coatings incorporated into drug delivery systems such as poly(lactic-co-glycolic acid) (PLGA) nanoparticles, pHEMA, or PLGA nanoparticles-embedded matrix have been developed, these systems lack stable physical and chemical properties for reducing tissue responses, including an appropriate nanostructural interface, mechanical properties, and biofouling ability,” the researchers wrote. “Multifunctional drug-embedded coatings must be developed and integrated into the nanostructural neural interfaces to allow sustained release of bioactive molecules (anti-inflammatory drugs) and simultaneous construction of a brain tissue-mimic but bioinert microenvironment for reducing both acute and chronic inflammation reactions during long-term implantation.”
The researchers used aerosol jet 3D printing to develop a neuronal interface with prolonged anti-inflammatory ability, structural and mechanical properties that mimicked brain tissue, and a sustained nonfouling property in order to inhibit tissue encapsulation.

Using aerosol jet printing, the OPMSC suspensions were directly patterned on a neural probe to create an anti-inflammatory neural interface.
“With the integration of nanomanufacturing technology and multifunctional nanomaterials into the neural implants, we can extensively reduce the reactive tissue responses, provide continuous protection of surviving neurons, and ensure long-term performance reliability of implants,” the researchers explained.
They created a new 3D nanocarrier-based neural interface that could possibly be used to support long-term neural implantation, as well as achieve better therapy for chronic and degenerative diseases. The researchers used a “novel combination of antioxidative zwitterionic nanocarriers and nanomanufacturing technology” to make the interface. The team developed a new type of anti-inflammatory nanogel, based on the amphiphilic polydimethylsiloxane-modified N, O-carboxylic chitosan (PMSC) incorporated with oligo-proanthocyanidin (OPC), called OPMSC.
![]()
a) Optical microscopy image showing patterning morphology of PMSC and OPMSC arrays with a thickness of ≈30 µm obtained by aerosol jet printing. The red arrows indicate the patterned location. Comparison of PC12 cell patterning on b) PMSC and c) OPMSC arrays demonstrates that OPMSC can maintain structural stability in a biological microenvironment. d) An overview and SEM images of the flexible OPMSC-coated polyimide probe. e) SEM image showing a cross-sectional view of OPMSC-coated probe after washing with water.
“The natural OPC can be used as an anti-inflammatory drug due to its multipotent therapeutic effects on neurodegenerative diseases,” the researchers explained. “Furthermore, given the abundance of hydroxyl groups and the aromatic architecture, the semi-hydrophilic OPC can act as a structural stabilizer to help the self-adhesion of nanogels, making the structure evolve into a biostable 3D anti-inflammatory neural interface.”
The team directly fabricated OPMSC nanogels onto a membrane using aerosol jet printing technology, because it is a low-temperature technology. When developing neural implants, mechanical properties are the main concern, which is why the researchers conducted a tensile test, among other experiments, on their new 3D nanocarrier-based neural interface, which was also implanted into rodents.
“After short-term and long-term in vivo implantation, the OPMSC-coated neural probe displayed a relatively lower impedance value and much higher signal stability compared to noncoated probe,” the researchers concluded. “The ADC obtained by magnetic resonance imaging (MRI) demonstrated that the OPMCS-coated probe alleviated edema at the acute phase, and further reduced tissue trauma in the chronic phase. Immunostaining of anti-NeuN, anti-ED1, and anti-GFAP around the implanted site further demonstrated that the OPMSC-coated probe significantly reduced the population of activated microglia and astrocytes for all durations, resulting in increased survival 28 d after implantation. Such multifunctional nanostructured OPMSC-coated neural probes can provide a long-lasting functional neural interface for long-term neural implantation.”
Co-authors of the paper are Wei-Chen Huang, Hsin-Yi Lai, Li-Wei Kuo, Chia-Hsin Liao, Po-Hsieh Chang,Ta-Chung Liu, San-Yuan Chen, and You-Yin Chen.
Discuss this and other 3D printing topics at 3DPrintBoard.com or share your thoughts below.