In today’s 3D Printing News Briefs, we’re covering a range of topics. First, Digital Alloys is sharing a guide on the cold spray metal 3D printing process. UPM just launched its new GrowInk Bioinks product range. STPL3D offered its 3D printing expertise to help with a complex orthopaedic surgery, and the Smithsonian Institution is using Mimaki’s full-color 3D printer to make virus models for an exhibit. Finally, 3D printing was used to give an ancient mummy a voice…sort of.
Digital Alloys’ Cold Spray Guide
Massachusetts-based Digital Alloys has been publishing a Guide to Metal Additive Manufacturing, and the 16th part is all about Cold Spray technology, which was used as a coating process for many years before it was adapted into a metal 3D printing technology for rapid fabrication of near-net-shape parts. The technology uses pressurized gas to rapidly fire metal powders through a nozzle, aimed at the deposition point, with high enough velocity to create a metallurgical bond on impact but without melting the material. High-pressure Cold Spray systems allow for the processing of heavier materials, like steel and titanium alloys, while low-pressure systems use ambient air as a propellant, making them better for more ductile metals, like copper and aluminum.
“Cold Spray’s advantages include compatibility with heat-sensitive materials, low thermal stresses, and the ability to operate in an open (non-inert) environment. Disadvantages include restrictive part geometry, low density and accuracy, and material embrittlement,” the blog post states. “This post provides an overview of Cold Spray metal AM technology: how it works, geometry capability, material compatibility, economics, applications, and current state of commercialization.”
UPM Launched GrowInk Product Range
Biomaterials company UPM, which introduced the biocomposite 3D printing material Formi 3D two years ago, is now launching a new line of hydrogels. The GrowInk 3D printing product range, which consists of non-animal derived, ready-to-use hydrogels, was introduced at the recent SLAS2020 conference. These bioinks, made up of water and nanofibrillar cellulose, support cell growth and differentiation by mimicking the in vivo environment, and are compatible with a wide range of 3D printers.
GrowInk Bioinks provide excellent imaging quality, and are perfect for many different 3D bioprinting applications, such as scaffold preparation and cell encapsulation for drug discovery, regenerative medicine, and tissue engineering. Additionally, UPM is also expanding its GrowDex product range with the sterile hydrogel GrowDex-A, which was created to debind biotinylated molecules, like antibiotics and peptides.
STPL3D Provides 3D Printing Help in Orthopedic Surgery
In December, 14-year-old Aaska Shah from India sustained multiple fractures to her left elbow while playing, and at her young age, a prosthetic implant would only compromise her natural movements. So doctors were left with no choice but to operate, using clamps to keep the bone pieces in place. Aaska’s surgery was denied because of how complex it would be, but Dr. Jignesh Pandya took on the task, and partnered up with Agam Shah from 3D printing service STPL3D to create a 3D printed resin model of the patient’s fractured elbow bone for surgical planning.
“Dr Pandya and his team first reviewed x-rays and 2D scans of the patient and reviewed their surgical plan. The doctors were a little concerned because there are a frightening amount of things that can go wrong during the operation but refused to give up hope,” an STPL3D blog post states. “The doctors have faced many challenges during the operation like deciding the clamp length and attaching points in the bone but the surgeries were successful largely thanks to the skilled surgeons.”
The doctors said the 3D model gave them “greater confidence,” and the patient was also on the operation table for roughly 25% less time.
Smithsonian Institution 3D Printing Full-Color Virus Models
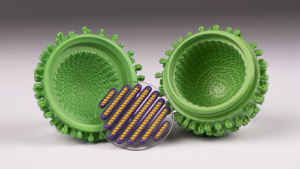
This image shows the Influenza virus model, created using the Mimaki 3DUJ-553 3D printer, in an opened position. The clear disk that contains the eight purple capsids and the eight yellow RNA strands has been removed from the green envelope. Image credit: Carolyn Thome/SIE
The world’s largest museum, education, and research complex, the Smithsonian Institution, is working with Mimaki USA to help with art, cultural, educational, and science exhibits and experiences. The Maryland-based Smithsonian Exhibits’ (SIE) studios works with the Institution’s offices and museums, and the federal government, to help plan engaging exhibits, as well as create models for research and public programs. The SIE team is using the full-color Mimaki 3DUJ-553 3D printer to create detailed, 3D printed models of enlarged viruses for the Smithsonian National Museum of Natural History’s Outbreak: Epidemics in a Connected World exhibition.
“We are pleased to be a part of the Smithsonian Institution’s efforts to engage and inspire audiences through the increase and diffusion of knowledge. This printer will enable the Smithsonian to use new technologies to produce exhibits in new ways, particularly for creating models and tactile elements that help bring exhibits to life for all visitors,” stated Josh Hope, Sr. Manager, 3D Printing & Engineering Projects at Mimaki USA.
3D Printed Vocal Tract for Mummy
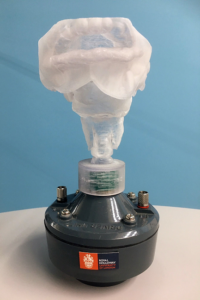
The 3D printed trachea and mouth of Nesyamun. (Credit: David Howard/Royal Holloway, University of London)
We’ve seen 3D printing used multiple times to help bring the mysteries of mummies into the modern world, but here’s a new one: a team of researchers from the UK used 3D printing to help an ancient mummy speak. Together, they published a paper, titled “Synthesis of a Vocal Sound from the 3,000 year old Mummy, Nesyamun ‘True of Voice,’ about their work creating a 3D printed vocal box for the mummy. Nesyamun was an Egyptian priest who lived and died over 3,000 years ago, during the reign of Ramses XI. A scribe and incense-bearer who likely sang and chanted prayers at the temple in Thebes, his sarcophagus features an epithet that translates to “true of voice,” because as a priest, he would have said that he lived a virtuous life; this is the reason the researchers gave for their work being ethical. In 2016, the mummy was sent to a facility for CT scanning, which discovered that, while his soft palate was gone and his tongue was shapeless, his larynx and throat were still in good condition – perfect for an experiment to replicate his vocal tract and help him “speak.”
Egyptologist Joann Fletcher said, “The actual mummification process was key here. The superb quality of preservation achieved by the ancient embalmers meant that Nesyamun’s vocal tract is still in excellent shape.”
The team 3D printed a copy of Nesyamun’s vocal tract between the larynx and lips on a Stratysys Connex 260 system. The horn portion of a loudspeaker was removed and replaced with the artificial vocal box, and then connected to a computer to create an electronic waveform similar to what is used in common speech synthesizers. This setup was able to help produce a single vowel sound, which you can hear for yourself here.
Discuss these stories and other 3D printing topics at 3DPrintBoard.com or share your thoughts below.
The post 3D Printing News Briefs: February 4, 2020 appeared first on 3DPrint.com | The Voice of 3D Printing / Additive Manufacturing.