BEGO, headquartered in Germany, has been a leader in the dental field for 130 years—and as pioneers in 3D printing for the last two decades, they now specialize in all types of dental fabrication techniques for prosthodontics and implant dentistry. Today, they have announced a partnership with Formlabs, the US-based designer and manufacturer of 3D printing systems—along with a wide-ranging product line and other strong partnerships around the world.
This alliance, just announced, means that Formlabs dental customers will be able to make on-demand dental products for their patients–using BEGO’s dental materials to 3D print both temporary and permanent crowns and bridges.
Formlabs customers who are already using the Form 3B and Form 2 3D printers will have access to fabricating permanent single crowns, inlays, onlays and veneers, and temporary crowns and bridges. Appreciating many of the benefits of 3D printing, they will be able to save on the bottom line, while making customized products, faster—and better.
“Directly printing temporary crowns and bridges are one of the most sought-after applications from Formlabs customers. By partnering with BEGO and leveraging their 130 years of dental experience, we will be able to not only address this need but take it a step further by offering materials for permanent crowns. We are excited to see how this partnership can continue to advance the dental industry and overcome the major challenges labs and dentists face as digital dentistry becomes a standard for patient care,” said Dávid Lakatos, Chief Product Officer at Formlabs.
Patients will enjoy:
- Excellent aesthetics
- Less tendency for dental work to age and discolor
- Low-plaque accumulation
- More comfort, thanks to less cold and heat sensitivity
“The ability to use completely digital dental workflows with 3D printed temporary restorations will enable a rapid, low cost, iterative process that improves patient care and case acceptance rates,” states the BEGO team in a press release sent to 3DPrint.com.
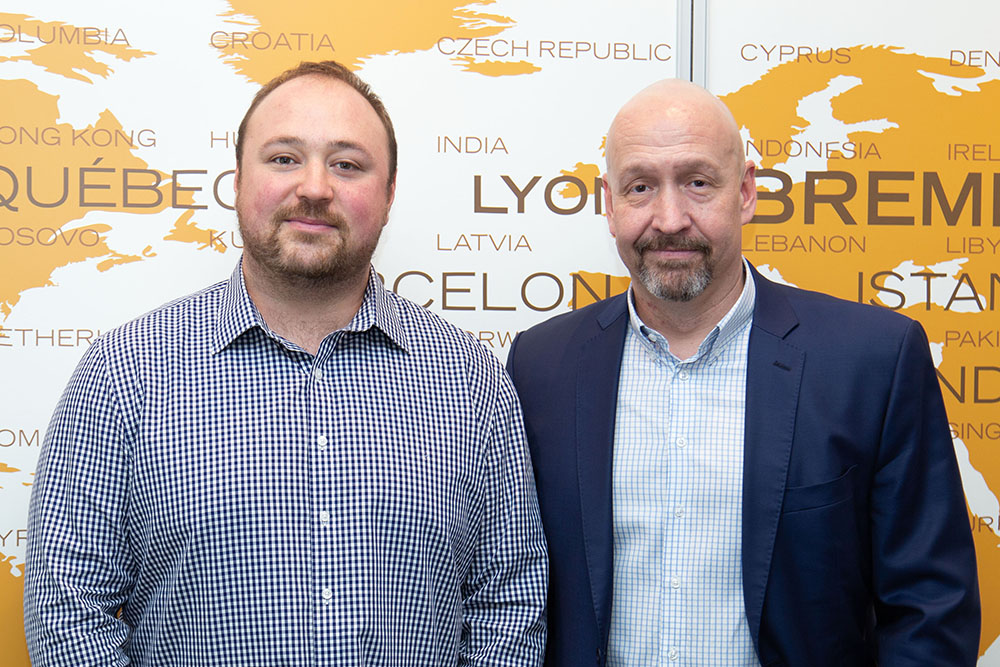
Dávid Lakatos, Chief Product Officer at Formlabs with Axel Klarmeyer, Chief Executive Officer of BEGO Dental
The two companies will be in attendance at LMT Lab Day in Chicago from February 21-22, presenting materials for attendees to see and feel, as well as showcasing their new partnership, which is also part of the ‘natural evolution’ of the also recently announced Dental Business Unit and Form 3B, meant to ensure that dentists are able to offer their patients the best in care.
“We could not be happier to partner with Formlabs, especially at this time, where digital dentistry is reaching a breakthrough. It took some time and a lot of effort and commitment of all involved people to be able to offer to the market a fully validated workflow for final restorations. This partnership underlines BEGO’s leading position in the dental 3D printing materials market,” said Axel Klarmeyer, Chief Executive Officer of BEGO Dental.
Find out more about these products here, and please visit BEGO and Formlabs at LMT Lab Day at Formlabs booth (#P-1) and BEGO booth (#H-13).
Both BEGO and Formlabs stay in the news with continue product development and successes from BEGO’s recent launch of the Varseo XL to new resins and other recent acquisitions by Formlabs.
What do you think of this news? Let us know your thoughts! Join the discussion of this and other 3D printing topics at 3DPrintBoard.com.
[Source / Images: BEGO]
The post New Partnership: BEGO’s Dental Materials Allow Formlabs Customers to 3D Print Crowns & Bridges appeared first on 3DPrint.com | The Voice of 3D Printing / Additive Manufacturing.