Ten years or so ago I worked for a company and we were making thousands of colored sintered parts per day. We were doing this by using large heated soup pots and Dylon dye which was used for T-shirts. People spent shift after shift stirring these pots to move around the 3D Printed parts. One of our biggest problems was that different geometries, wall thicknesses or stirring tempo influenced how far and how much the dye penetrated parts. This meant that some parts were darker than others overall or just on one side. The global press was writing about 3D Printing as the Revolution in Manufacturing. We on the front lines were not so sure. Now more than a decade later many sintered parts are still colored in those soup pots with Dylon and similar materials. If you’d like to skip the dyeing and change the colored powder in your printer be prepared to spend some quality time with your vacuum cleaner of choice.
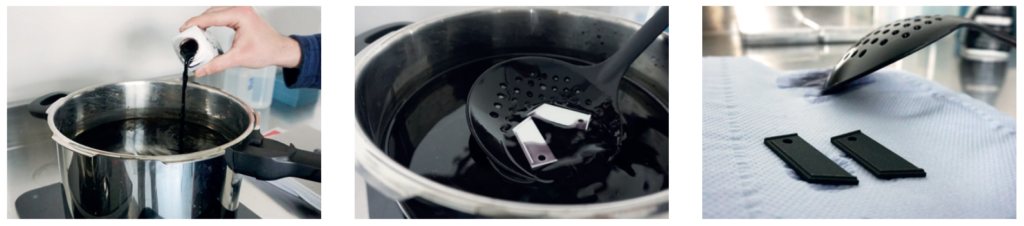
Artisanal pot dyeing as now practiced by certain locally owned establishments still serving up hand-colored 3D prints.
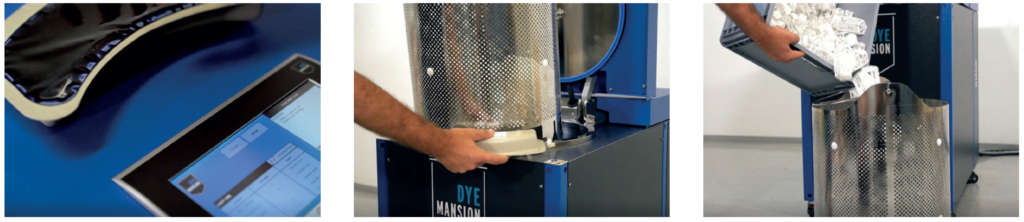
Repeatable processes for industry.
Sintering (SLS, Selective Laser Sintering, Powder bed fusion) is a highly productive 3D printing technology, but color is still somewhat problematic. Yes we can make thousands of shapes per day but can we make thousands of products each day? The gulf between a shape and a product is what we’re trying to collectively bridge at the moment. One way we can add value to our current activities and, with little in the way of marginal cost, sell much more expensive high volume goods is through post-processing. Post-processing is 3D Printing’s dirty little secret. Around a third of final part costs are from manual labor and even with a high labor component we lag in part quality and finish. A whole industry has sprung up that simultaneously wishes to give us lower part costs, higher yields, and better finished products. One of the companies leading the charge is Dye Mansion. We’ve talked of the German EOS offshoot’s vapor fuse technology, looked at how the costs add up, their funding round in 2018 and launch in the US before.
;
The company now wants to banish artisanal pot coloring entirely through automation and workflows. I’m shocked that they wish to make hand-colored 3D prints a thing of the past. Won’t it be so soulless without the wooden spoons? In a white paper which you can download here, the firm lists why pot dyeing is to be a thing of the past.
They say that “DyeMansion supplies their customers with exact color recipes down to the microgram. This enables an industrial and traceable process that could not be easier for the user and can be reproduced any time.” Their process delivers “certified and proven colors for high-end manufacturing” and is “traceable and fully automated “plug & play” process.”
They do bring up some salient points such as the UV degradation seen in pot dyed colors and the ability to color match. But, where is the human element? Dream killer, Sterling Logan, Owner of 3D Logics mentions that “Traditional pot dyeing was messy, inconsistent, and resulted in a lot of scrapped parts.” Yes, sure but…what about, creativity? The human touch? I know that we’re making progress here but I can’t help but think that along with progress, something is lost.
The post The End of the Road for Pot Dyeing in 3D Printing? appeared first on 3DPrint.com | The Voice of 3D Printing / Additive Manufacturing.