Formnext 2019: The 3D Printing Industry first look
Preview: DyeMansion launches new post-processing solution Powerfuse S technical specifications
Register for the Third Annual Munich Technology Conference
Why Automated Post Processing Makes Manufacturing With 3D Printers Possible
In Material Extrusion (FDM), we can now use inexpensive machines to make dimensionally accurate & tough parts in various materials at low cost. These parts can fulfill many industrial and manufacturing applications bar one glaring defect. Material Extrusion (FDM) parts are often ugly, and layers can be seen on the rough parts. FDM parts and materials are improving all the time; parts are getting smoother and better looking out of the machine. Clusters of FDM machines bring throughput and versatility and have begun to be used to manufacture parts at scale.
With Selective Laser Sintering (powder bed fusion), one can make thousands of individual parts in many different geometries. Highly detailed polyamide SLS parts have been used for tens of thousands of surgical guides and have found many industrial applications. All parts have to be depowered and cleaned of excess powder, however. Additional steps, such as mechanical finishing are often needed to close the open surface texture of SLS parts.

With Dye Mansion depowdering is combined with surface improvement and coloring to make parts more world proof.
With SLA (stereolithography, vat polymerization) tens of millions of molds have been made for jewels with millions more being used in the dental industry. Additionally, millions of intermediates have been made for aligners. Direct SLA parts in hearing aids have revolutionized the In The Ear hearing aid industry, winning the market in customized fit ITE hearing aids. And yet, every SLA part has to be cut off of supports manually, and most have to be filed down afterward. Parts have to be conveyed to a washing station and a UV flash machine.
Meanwhile, in the SLS world, the future of manufacturing consists of a man with a brush brushing off powder from a part. It won’t surprise you that a third of part costs are perhaps due to finishing and post finishing parts. We boast of machines that can, in a day, make a new part, only to casually leave out that this part may spend another day in a tumbler. We jump on the gleeful subsidy bandwagon that is Industry 4.0 while a lot of the cost of 3D printed parts is in conveyancing.
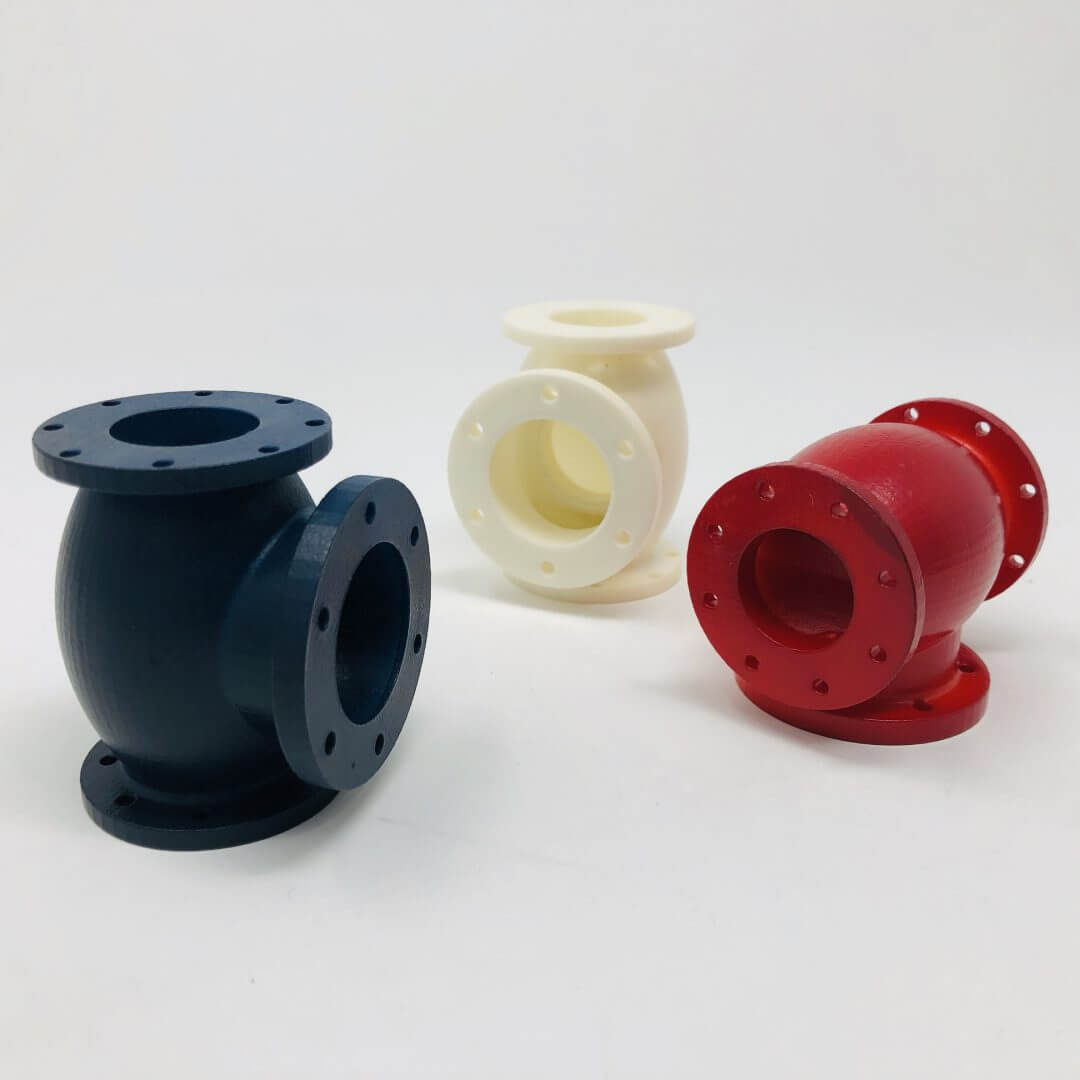
Additive Manufacturing Technologies‘ automated surface finishing colors and finishes in one step.
Significant part costs comprise of people carrying parts around a factory. A woman leans over, looks at a piece of paper, matches the part, carries it to her station and then later puts it on a tray where a colleague takes it to a new station. This is Industry Bore.0, not 4.0. And metal printing? Like all things, it makes the polymer part of our industry look easy. Parts have to be sawed off by hand, and a number of post-processing stations always pay a part: from HIP to EDM to shot peening to destressing to spending a week in a tumbler it often needs to happen to your metal part.
We can not ask industrial manufacturing firms to learn new ways of thinking, master design for additive, change parts in their inventory and take on new unknown risks in return for a future where parts are marched around a “factory.” I say factory partially in jest because currently manufacturing with 3D printing is much closer to a collective of be-dreaded sandal-wearing artisanal vegan soap makers than actual manufacturing.

Rosler’s AM Post Processing Line of machines remove powder, support and structures.
Imagine us, some hippie collective with handcrafted bamboo bowls trying to sell our way to the Six Sigma people? Just change everything; it will be great. Hope is the new one error per ten million. Do you want a Craft aircraft? Do artisanal aero engines sound like a good idea to you? Would you like to take a trip to Mars on a handcrafted rocket? Would you like your next hip to be made with love? Or would you prefer it to have things like quality control? We’re currently selling a dream to manufacturers that for many applications, we can not turn into a reality.
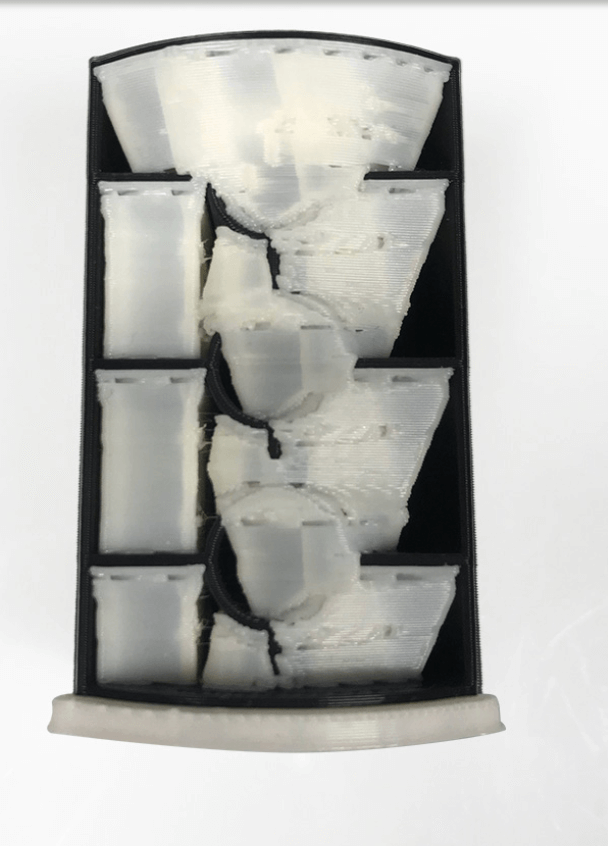
Post Process showing you parts before and after their process.
What can make 3D printing for manufacturing real? Automated Post Processing. By automating the entire post-processing chain, we can dramatically lower the part costs of 3D printed parts. We can make many more business cases worthwhile by making 3D printed parts significantly cheaper. By automating conveyancing throughout the plant, we can dramatically reduce the overall cost at high throughput. By offering post finishing to improve the surface quality of parts, we can make better looking and better-performing parts. Consumer-friendly and industry-friendly parts can ensure that the adoption of 3D printing is more rapid. The combination of automated post-processing with 3D printing will let parts be produced close to the consumer in wealthy countries at a reasonable cost. Improved post finishing processes will improve surface quality and let 3D printed parts be deployable for many more applications. If we integrate automated QC and QA processes into post-processing setups, we can genuinely offer manufactured 3D printed parts to many industries. Many firms are looking into automating the entire post-processing chain. From Post Process to Rosler, Additive Manufacturing Technologies and Dye Mansion, it is these companies that will unlock manufacturing for us all.
The post Why Automated Post Processing Makes Manufacturing With 3D Printers Possible appeared first on 3DPrint.com | The Voice of 3D Printing / Additive Manufacturing.
DyeMansion expands its reach of post processing technology to China
3D Printing Industry jobs, career moves & facility openings update: DyeMansion, PostProcess Technologies, Massivit 3D, ExOne, iGo3D, Sintavia, Voxeljet
What happened in 3D printing at RAPID & TCT 2019?
3D Printing News Briefs: May 26, 2019
This year’s RAPID + TCT ended late last week at the Cobo Center in Detroit, so we’re again starting off today’s 3D Printing News Briefs with more news from the busy show floor. DyeMansion launched a new extended color series at RAPID, while 3D Systems made the announcement that its Figure 4 Modular is now available. Moving on, SLM Solutions just celebrated the grand opening of its new Shanghai application center. Finally, a Reddit user made an adorable miniature 3D printer.
RAPID 2019: DyeMansion’s New Colors
Munich startup DyeMansion, a leader in finishing and coloring solutions for 3D printing, launched its new ColorsX extended color series for end-use products at RAPID last week, in order to continue helping its customers achieve the perfect finish for all of their applications. Automotive ColorsX and Neon ColorsX are the first solutions under the startup’s X Colors for X Industries premise, with more to follow in the future. The automotive color line has improved light and heat resistance for better 3D printed polyamide components and interior car parts, and features Automotive BlackX, which has a less saturated black tone than DyeMansion’s basic DM Black 01 and was created according to ISO EN 105 B06 method 3’s hot irradiation standards. The luminous neon color line includes GreenX, YellowX, OrangeX and PinkX to help create striking end-use products. Both of these new color lines are compatible with DyeMansion’s PolyShot Surfacing (PSS) and VaporFuse Surfacing (VFS).
“Some of our earliest customers who made use of DyeMansion Print-to-Product technologies for serial production are from the Automotive and Lifestyle industries,” explained Kai Witter, DyeMansion’s Chief Customer Officer. “While working closely with our customers, joint strategies are always about creating even more value to their businesses. So, I feel very delighted to now offer additional value creating products. Automotive and Neon ColorsX are only the beginning of providing more specific industry offers.”
Once DyeMansion decided to launch its ColorsX series, it also named the coloring process it established back in 2015: DeepDye Coloring (DDC), which can be easily controlled and traced through integrated RFID technology and offers a limitless choice of custom colors.
RAPID 2019: 3D Systems Announces General Availability of Figure 4 Modular
Also at RAPID last week, 3D Systems announced the general availability of its scalable Figure 4 Modular production platform. The flexible digital light printing (DLP) system has multiple configurations that can print parts with high surface quality, and allows manufacturers to iterate designs more quickly, as well as produce end-use parts without having to worry about a minimum order quantity. Three models make up the Figure 4 – Standalone, Production, and Modular – and several customers, such as D&K Engineering and Midwest Prototyping, are reaping the benefits. Additionally, 3D Systems also announced five new DLP and SLS materials, the first of which is the immediately available Figure 4 FLEX-BLK 10. The other new Figure 4 materials, such as TOUGH-BLK 20, MED-AMB 10, MED-WHT 10, and HI-TEMP-AMB 250, are expected to be available in Q3 and Q4 of 2019.
“The newest additions to our plastic 3D printing portfolio demonstrate our commitment to driving the adoption of digital manufacturing. With the industry’s first, truly scalable plastic production platform and our robust selection of materials, 3D Systems enables customers to rethink manufacturing and realize improved agility, reduced complexity, and lower overall total cost of operation,” said Vyomesh Joshi, the President and CEO of 3D Systems.
3D Systems also announced that its customers Rodin Cars (based in New Zealand) and North Carolina-based Stewart-Haas Racing are using its plastic and metal 3D printing solutions to improve the speed and performance of their cars.
SLM Solutions Celebrates Opening of New Shanghai Application Center
The same year that SLM Solutions opened an applications and demonstration center in Germany, it also established Chinese operations in Shanghai. Earlier this week, the selective laser melting experts celebrated the grand opening of their expanded office facilities and application center in Shanghai, which will help the company continue to grow its presence on the Asian market. The new center has installed four SLM systems: one SLM 125, one SLM 500, and two SLM 280 printers. Additionally, the facility also has equipment to represent an SLM build’s supporting process chain, such as a metallurgical lab and post-processing capabilities. The grand opening included a tour through the new new customer service and application engineering center.
“As we continue to grow our Chinese team, the opening of our Shanghai Application Center is an important milestone in SLM Solutions’ development and indicates the confidence in the Chinese market,” stated Jerry Ma, General Manager of SLM Solutions (Shanghai) Co., Ltd. “As part of the global strategy for growth we have the capacity to more than double our number of employees and the equipment to support all Chinese users with the technological resources shared by our applications centers around the world. We can also provide high-quality, fast technical services to better promote the development of selective laser melting and create more value for customers.”
Mini 3D Printed 3D Printer
A reddit and imgur user by the name of “Mega Andy” used 3D printed parts and DVD drive motors to make his own miniature 3D printer. And by miniature, I mean that he used a banana for scale, which was taller than the 3D printed 3D printer itself! It’s a really interesting project – the device runs Marlin, and features a glass bed and an E3D V6 hotend. The black and gold parts of the mini 3D printer were made out of PLA material, while PETG was used to make teeth for the leadscrews. Speaking of this, Mega Andy said that the printer is “fairly unreliable” because it easily ruins the teeth that guide the device on the leadscrew. Additionally, he’s also working to improve and lengthen the Z axis due to binding problems. Mega Andy released the STLs onto Thingiverse so others could try to make their own versions of the miniature 3D printed 3D printer…say that five times fast.
“So this project is nothing new, people have made 3d printers, CNC, engravers before using this hardware. What I wanted to do differently with this is have a designed 3D printed frame to hopefully fit standard parts. Instead of mounting full metal dvd drive assembly’s together and look like a DIY project I wanted a something that could be more compact and neat,” Mega Andy wrote on Thingiverse.
“This project is not for everyone and would only recommend to someone with a decent knowledge of 3d printers, basic soldering and lots of patience. Also some fiddling was needed to get the right amount of tension on the leadscrew, this bit is a massive pain but hopefully no one else needs to go through quite as much issues as i did with this bit. They will wear out though and a 3d printer will be needed to print new parts for it when they inevitable wear out.”
Discuss these stories and other 3D printing topics at 3DPrintBoard.com or share your thoughts in the Facebook comments below.