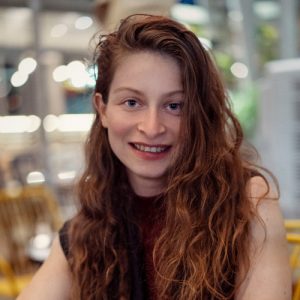
Ganit Goldstein
Ganit Goldstein is a Designer whose interest lies in the intersection between Craft and Technology. Ganit studied Jewelry and Fashion. She received the Excellence Award from Bezalel Academy of Arts and Design, Jerusalem, Israel. Her work is focusing on new methods of incorporating 3D Printing into the world of Textiles, Shoes and Fashion. In her Collection ‘Between The Layers’, she created garments and shoes, inspired by her study of ‘IKAT’ weaving in Tokyo, Japan. Her collection received great interest and immediate press recognition, and was presented at Exhibitions and Museums around the world including Milan Design week, New York Textile Month, Asian Art Musuem – San Francisco, Holon Design Museum, ‘TALENTE’ exhibition in Munich and more. Ganit Goldstein believes in an interdisciplinary approach to design- mixing Tradition with Futuristic techniques – 3D printing & 3D body scanning.
Give us some background on your experiences so far.
I studied at Bezalel Academy of Arts in Design and majored in the department of Fashion and Jewelry. Since my first year of study, I was fascinated by using 3D design software, especially because of the design-freedom it allowed me. During my studies, I have often incorporated tools from other disciplines into my work, whether it is CNC, laser cutting, 3D scanning and 3D printing. The use of different tools and mindsets helped me discover my own desig language.
During my third year of study, I was expected to participate in an exchange student program. My decision was to apply for the opposite direction of what I was used to. Meaning, the opposite of the cutting-edge technology field. I found my way to the Craft Department ’Textile Art’ program at Tokyo University of the Arts – GEIDAI. During this time, every single process of my designs was made using traditional handmade techniques. Meaning, I turned completely low-tech, changing my entire thinking structures and patterns. That was very significant for me in terms of expanding my horizons and changing my view on design. Talk about stepping out of your comfort zone! When I finished my studies in Tokyo, I went back to Jerusalem to finish my final project. That’s when I decided to combine the traditional methods I recently learned, with the latest technology I was working on before. This was translating both worlds of the past and future into one design language.
Since my graduation, I was lucky to participate as a finalist in four international competitions, presented my projects in New York Textile Month, Hong Kong Fashion Week, Asian Art Museum- San Francisco and ‘Talente’ exhibition in Munich. These competitions helped me a lot to reach my goals, discover possibilities, and meet great people that influence my work until this day.
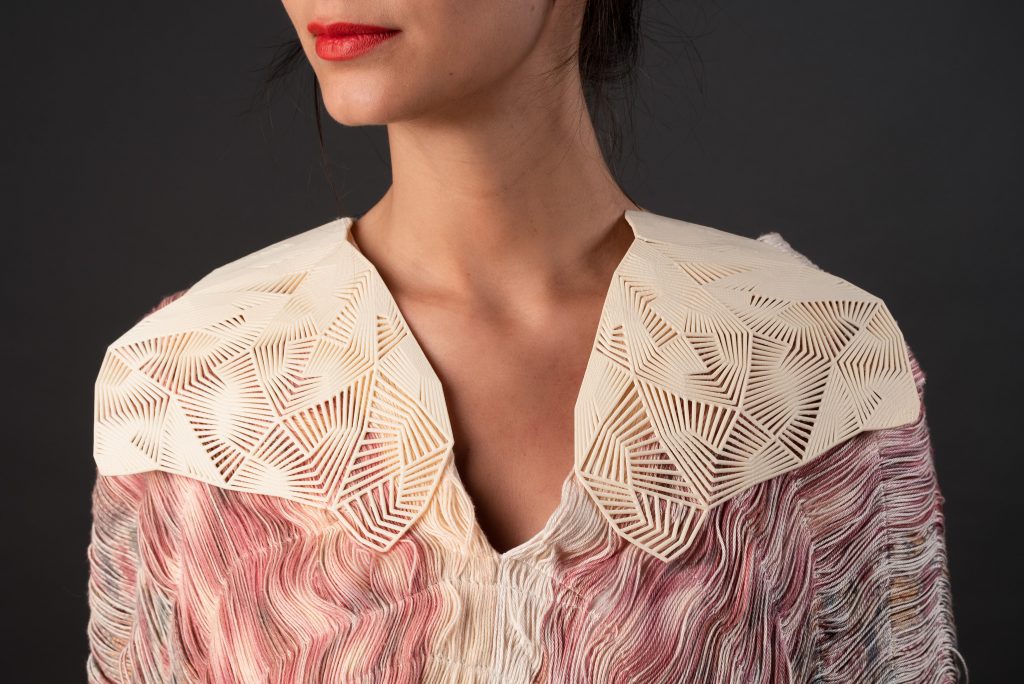
Craft and Technology Outfit
When did you first get excited about fashion and design?
I was excited to mix the borders between art and fashion, back in high school, when my project consisted of dresses made from broken glass and metal wires. I was looking at garments as a platform to make art pieces, that aren’t necessarily meant to be worn, but rather a manifestation of aesthetics, culture, language, and design.
One exhibition that is very powerful in my memory is a solo exhibition (2014) of Iris Van Herpen at the Design Museum Holon. The exhibition was very special and it featured beautiful outfits, that crossed borders between art, fashion, and futuristic techniques. It was influential for me because it dealt, or perhaps answered the question of whether fashion can be presented at museums as art pieces.
When you did your first 3D printing project with fashion?
As part of my second-year curriculum study, we were asked to reconstruct costumes from the 18th- 19th centuries. I was asked to build an entire costume, made up of 7 different layers, just as it was made back in the history of fashion. The dress I was assigned to reconstruct is held by The Metropolitan Museum of Art (Costume Institute collections) – from the year 1870. This decade was a “golden decade” for lace dresses. In the next semester, we were asked to think about the outfit in a modern perspective, and I was focusing on the lace. I decided to design and create a 3D lace of our times, based on algorithms printed with hard material, combining flexible properties inside the printed part. This was the first time I used 3D printing as an integral working method in my designs, and that’s when I discovered the huge potential in using algorithms, software and parametric design in the process of my work.
During my studies, and especially due to this project, I began working closely with the Institute of Chemistry – Casali Center at the Hebrew University, for innovative research in 3D printing. The research group, led by Prof. S. Magdassi, focuses on materials science, nanotechnology and their applications in a variety of fields such as 3D and functional printing.
This collaboration gave me the opportunity to work with great researchers, and thus better understand the different approach for material research studies, working on innovations in the field of 3D printing.
How important is the differentiation of fully created 3D printed items vs hybridized fashion products from textiles and 3D printed material?
The harmony of putting together two different worlds makes the innovation approach, and bring forward a new way of thinking about design. I believe in taking the essence of the traditional techniques from our past and translate those methods to the new technology- a different point of view from the traditional technique inside the process of the newest technology.
I feel it is important to make the hybrid of textiles and 3D printing together because it has the power to bring 3D printing to a much more wearable level. I also understand that fully 3D printed fashion is still in a building stage, and the combination of traditional textile methods helps this method is growing quicker. Hybridized craft methods in 3D printing are important in my opinion because we should not lose sight of the traditional processes. Technology will always move forward, but craft methods can disappear easily. I believe it is important for the designers also to remember the traditional working processes, not to lose the history of crafts. Bridging the craft methods and technology to move forward with the latest technology.
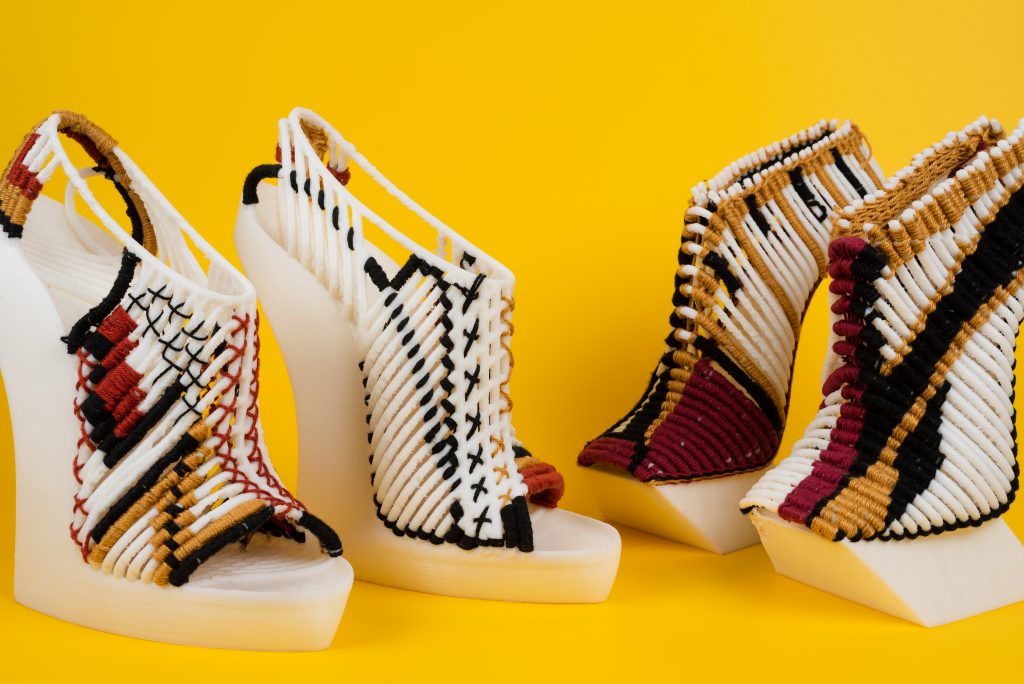
Craft and Technology Shoe
What are some of your favorite projects that you have worked on in 3D printing?
Seeing the first 3D printed multi-color shoes that were made in collaboration with Stratasys was an extremely exciting moment. In these shoes, my aim was to create a fabric-like texture inside the printing process. I couldn’t hope for better results. Since my graduation presentation, the shoes were presented in exhibitions worldwide (the last exhibition was in Milan Design Week 2019). Most of the people I have met during the exhibitions were sure the shoes are made from fabric and not from 3D printing. The shoes are now part of the Holon Design Museum permanent collection, they were the first pair I made together with Stratasys. We made a few more designs, but nothing compares to the success and joy that was brought by my first pair.
One of the most exciting projects that has had a huge impact on my projects so far, was working in collaboration with Intel ‘RealSense’ studio in Jerusalem. We incorporated their technology into the design process by 3D scanning an entire body thus allowing to create customized fashion and accessories, designed for a specific person. We also launched together an AR App (made together with Yoav from RealSense Studio) that demonstrates the 3D printing process using a hologram featured on the reality).
Another very exciting collection will be soon launched together in collaboration with Prusa Research company for FDM processes of wearable shoes. I worked closely with their maker-lab, and we made huge progress, the shoes are 100% wearable with multi-color and flexible materials!
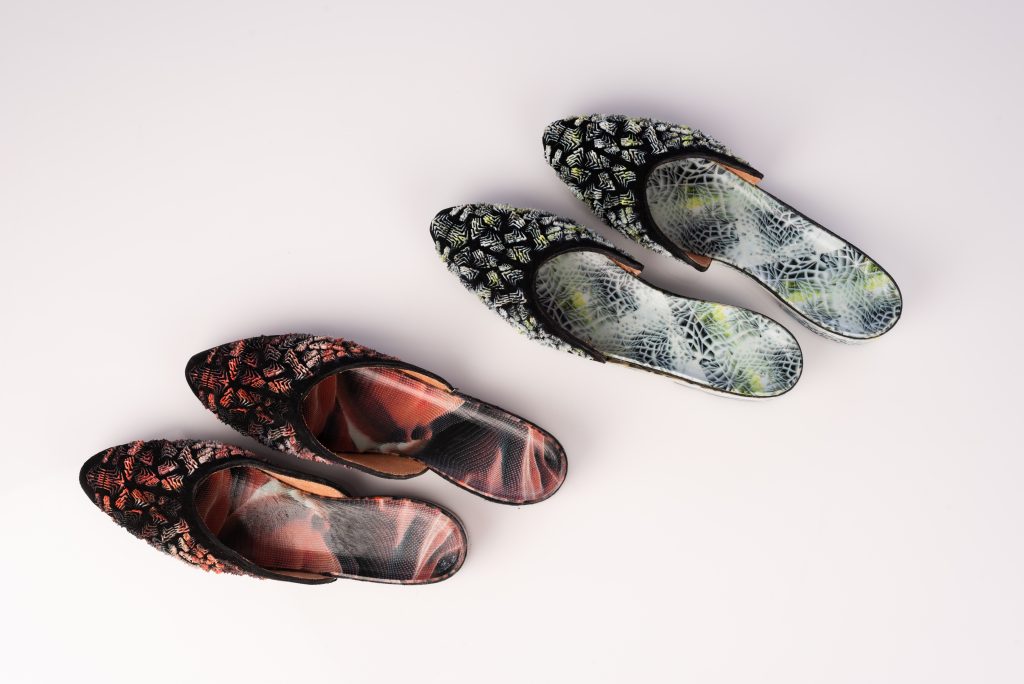
Stratasys and Goldstein Collaboration
What is currently being worked on for you within the 3D printing world?
I am a great believer in collaboration and partnership with great people and open-minded companies. I want to continuously break boundaries, that is my core value, and I understand that in order to do that, I must turn to other disciplines and utilize what they have to offer. The ability to combine both worlds of past and future technique has a big impact on both my past and current projects. This is my take on the future of the 3D printing world.
Harnessing the power of the new technology and utilizing traditional techniques helped me create my own design language. I think that the ability to be open minded in the design process enables me to achieve my goals. I am a great believer of trying new methods, and not putting limits. This works because the design process has ups and downs, and from some failures and material tryout, you can reach better-designed results.
How was it to partner with Stratasys so early on in your journey?
My 3D printing journey started in a small room in my parent’s house, which I filled with 2 desktop printers. That room became my very own printing lab, where I got to experience, try-out materials and utilize the good old “trial and error” method.
I was fortunate enough to gain that experience, because I believe that is what enabled me to work with a “tip of the spear” company such as Stratasys.
The collaboration with Stratasys established after I had many “flight hours”, examples and tryouts. We partnered up during my last year studies. As my vision was to integrate colors inside my printed projects, They allow me to carry out my vision and turn it into reality. I’ve been incredibly lucky, and honored, especially knowing it came at such an early stage of my career. And it also makes me very proud.
I worked closely with the R&D team, and therefore, we shared the same vision of pushing the boundaries of the technology through design research. During the making process, we made some very interesting tryouts with the ability to control any voxel (3D pixel). At the same time, our research was growing, I made it into the final stage of numerous worldwide competitions and exhibitions (‘Talente’ & Milan Design Week), so we were continuing our collaboration for specific events that lead to new developments and exciting processes in each of the projects.
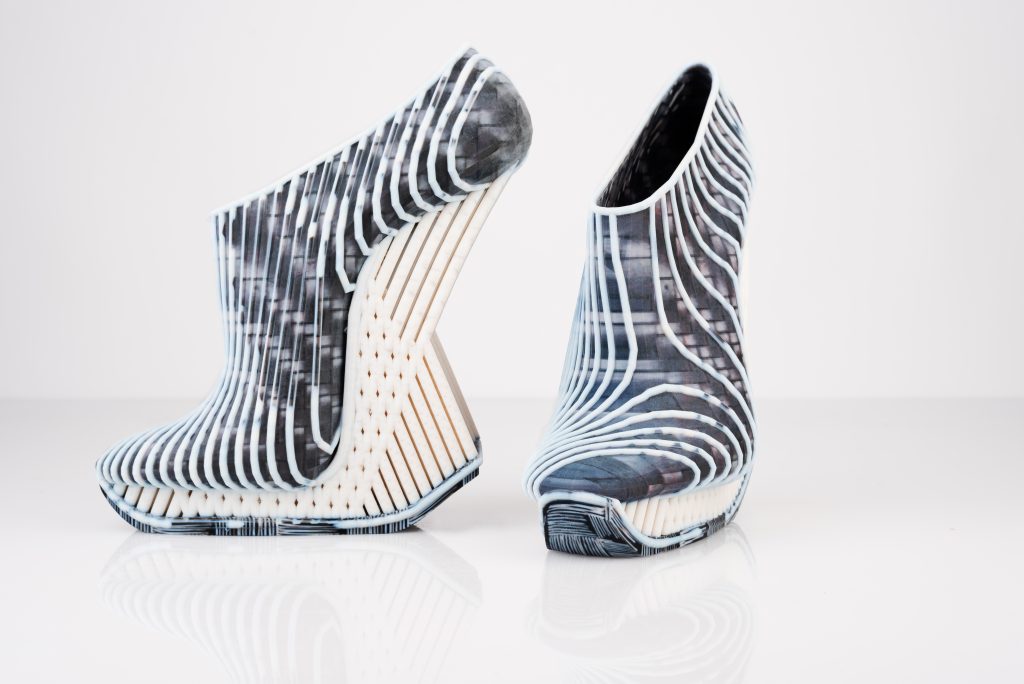
Woven 3D Print Shoes
Do you wish to branch out of just 3D printing?
I wish to further develop in the field of augmented/virtual reality.
3D printing is already well integrated into our lives and in many industries. From medicine to automobiles, furniture, military equipment, housing, fashion, etc.
I believe in the future of 3D printing and its applications. I also believe that 3D printing is directly linked to 3D scanning and ARVR applications and that this technology will completely alter the user experience in public sites and will be adding new features to the digital medium.
The adoption of the technology by museums to reach new levels of audience experience- multi sensational- rather than just viewing. I believe AR will soon be in every museum, using the newest technology for public use, and even controlling our experiences in different senses- not just by looking at an art piece.
I’m also very interested in the smart- textile field, adding new reactions for textile by using programming software. I find especially the 4D printing process very interesting topic to work on, creating 3D objects that change their shape over time.
What are some key skills needed to be a designer within the 3D printing world?
I believe that the main key is determination. Not to be afraid of failure. 3D printing can be very attractive on the one hand, but on the other hand, it is a relatively new technology, there are some limits and tons of failures in the making process. It takes time unti you figure out the path to the final project, it takes time and extra effort.
Being a Maker- For me, to be a designer in the 3D printing world means to be a ‘maker’, I believe in hard work from the beginning. You need to be experimental with many technology techniques. Building your own printer and so on are examples of how I describe a ‘maker’.
Professionalism and expertise- 3D designing and printing is just like programming. You must “study the language”. You must learn the 3D software skills, be an expert in your field. Luckily, in our times, this information is approachable by everybody via the internet. It is possible to study everything you set your mind to, every single feature is fully covered.
Independence and self-confidence – I believe to fully be in control of your designs, anyone that wishes to be a designer in the 3D printing world, should do the work on his own, and not rely on others people’s skills. The making process changes the way the final object will appear, and for me, this is the main freedom space, that you have the ability to bring your design from your imagination into reality and constantly improve it upon your request.
Who are organizations you want to partner or collaborate with in the future?
I want to continue my work with the partners that supported me and have been fantastic in our collaboration: Stratasys, Prusa Research and Swarovski.
I believe the future of my work also lays in collaborating with companies that have new technological developments and have design potential that can become a platform for combining my design visions. I would love to work with researchers of innovation in material research such as Neri Oxman and designers working in the field such as Iris Van Herpen. I’d like to extend the collaboration for shoe design with companies that develop 3D printed shoes such as Adidas.
Designers are not fully on the 3D printing wave just yet, how does it feel to be an early adopter?
It’s extremely exciting to be a part of a relatively small group that consists of designers and makers, who are investigating into how design can be developed in a sustainable and innovative way, using 3D printing technology.
This era is the most stirring time for pushing the boundaries of this technology, and I’m looking forward to working on new projects that will inspire me to think about “re-inventing” our future.
I feel that there is so much space for designers to grow in this field, working together with researchers and scientists all while keeping an open mind for new opportunities.
I feel blessed and extremely lucky to have become an early adopter in this field. It is a magical time filled with opportunities to seize and enjoy and to continue being excited from any new features, ideas, and projects.
I think 3D printing has great potential in so many fields, and design is one of the most exciting uses for this technology, clearing the way for further development of Art and Design (and maybe the concept of fashion and design as art), presenting each artist’s point of view the production process, from imagination to reality.
Where do you see the field of 3D printing and fashion in 5 years?
I see 3D body scan as a key process that will be an integral part of any fashion development department. I believe that 5 years from now, personalization will receive a different meaning and will bring a drastic change in the fashion industry, moving from mass production to one of a kind customizable piece.
In my opinion, another upcoming major change that will take fashion design forward is the ability to design your own clothing- the customer will be his own designer by, ‘pushing buttons’ (by simplifying the design and programming software) for producing his favorite design.
I’ve also found the development of flexible material as a very important process for 3D printed fashion, and the development of new material will be a major step for 3D printed textile to make 3D printing – wearable.
Where do you see yourself in 5 years?
With 3D printing and 3D scanning, we can utilize the new technology to develop tailored pieces and fit to measure clothing for individuals. I want to take this a step further and produce customized clothes, based on body scans, ready-to-wear fashion and I hope to have designers and partners in the future, bringing innovative approach into daily production methods of fashion.
In the next two years, I will be studying at the Royal College of Arts in London, in the master’s program for smart textile developments called ‘Soft Systems’.
I believe this upcoming period will greatly influence and affect my career, and I hope that 5 years from today I will be able to continue developing my design language, and open my own brand, start-up, lab and continue researching and developing the wearable technology field. I hope to continue being thrilled and excited from any new project, any new printing method and constantly breaking the boundaries of the latest technology