
A) PLA during mechanical mixing with wood-waste powder, B) PLA and wood-waste powder-based WPC after mixing and cooling to room temperature, C) chipped WPC, and D) homogeneous WPC material after first pass through recyclebot.
From artwork, instruments, and boats to gear shift knobs, cell phone accessories, and even 3D printers, wood has been used often as a 3D printing material. It’s a valuable renewable resource that stores carbon and is easily recycled, so why wouldn’t we think to use it in 3D printing projects?
A trio of researchers from Michigan Technological University recently published a paper, titled “Wood Furniture Waste-Based Recycled 3-D Printing Filament,” that looks to see how viable a solution it is to use wood furniture waste, upcycled into a wood polymer composite (WPC) material, as a 3D printing feedstock for building furniture.
The abstract reads, “The Michigan furniture industry produces >150 tons/day of wood-based waste, which can be upcycled into a wood polymer composite (WPC). This study investigates the viability of using furniture waste as a feedstock for 3-D printer filament to produce furniture components. The process involves: grinding/milling board scraps made of both LDF/MDF/LDF and melamine/particleboard/paper impregnated with phenolic resins; pre-mixing wood-based powder with the biopolymer poly lactic acid (PLA), extruding twice through open-source recyclebots to fabricate homogeneous 3-D printable WPC filament, and printing with open source FFF-based 3-D printers. The results indicate there is a significant opportunity for waste-based composite WPCs to be used as 3-D printing filament.”
While a lot of wood is wasted by burning it, it may be better to upcycle it into WPCs, which contain a wood component in particle form inside a polymer matrix. These materials can help lower costs and environmental impact, as well as offer a greater performance.
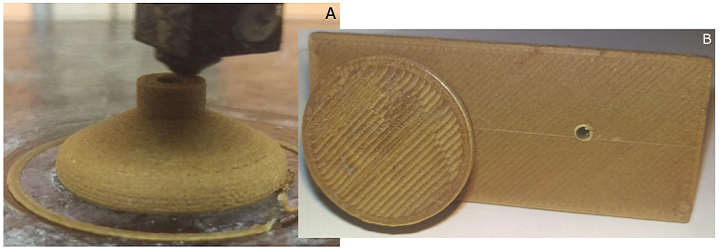
A) 0.15 mm layer height drawer knob being 3D printed with a screw hole for attachment. B) Completed drawer knob fully attached on left of wood block with example pre-printed hole on right of block, 30wt% wood furniture waste.
“There is a wide range of modification techniques for wood either involving active modifications such as thermal or chemical treatments, or passive modification, which changes the physical properties but not the biochemical structure,” the researchers wrote. “However, WPCs still have limitations due to production methods, such as producing waste material or orientation reliant fabrication, which may be alleviated with alternative manufacturing techniques such as additive manufacturing.”
While lots of PLA composite manufacturers are already in the market to make virgin, wood-based 3D printing filaments, the Michigan Tech study investigated using wood furniture waste as a 3D printing feedstock for WPC filament, which could then be used to make new furniture components.
“The process uses grinding and milling of two furniture waste materials – boards scraps made of both LDF/MDF/LDF (where LDF is light density fill and MDF is medium density fill) and melamine/particleboard/paper impregnated with phenolic resins. A pre-mixing process is used for the resultant wood-based powder with PLA pellets,” the researchers wrote. “This material is extruded twice through an open source recyclebot to fabricate homogeneous 3-D printable filament in volume fractions of wood:PLA from 10:100 to 40:100. The filament is tested in an open source FFF-based industrial 3-D printer. The results are presented and discussed to analyze the opportunity for waste based composite filament production.”

Surface contours of a personalized drawer handle with the Herman Miller emblem. A coloration change from the outside to the center is shown due to induced temperature changes during printing to provide a tree ring.
The team received wood-based waste material, in both sawdust and bulk form, from several furniture manufacturing companies, and completed some important steps to turn the wood waste into WPCs for 3D printing filament:
- Size reduction from macro- and meso-scale to micro-scale
- Mix fine wood-based filler material with matrix polymer
- Extrude feed material into filament of homogeneous thickness and density
Then, the material was loaded into a delta RepRap 3D printer, as well as an open source Re:3D Gigabot 3D printer, to make a high-resolution drawer knob that was “attached to a printed wood block using a wood screw threaded through a pre-printed hole.”
“The wood screw was easily twisted through both objects with a Phillips screwdriver and the resulting connection withstood normal forces expected in everyday use. Additionally due to the flexibility of 3-D printing orientations a unique or personalized surfaces may be printed onto objects,” the researchers wrote.
“This is shown through the particular geometries or print directions which may be modified directly by altering gcode, or more conveniently by changing parameters in slicer programs. This enables mass-scale personalization of not only furniture components with wood, but any 3D printed part using recycled waste-based plastic composites.”
Once an optimized 3D printing profile was obtained, the recycled wood furniture waste-based WPC filament was able to produce parts without too many errors. However, there was a greater frequency of filament blockages and nozzle clogging with this material, when compared to pure PLA.
“This study has demonstrated a technically viable methodology of upcycling furniture wood waste into usable 3-D printable parts for the furniture industry,” the researchers concluded. “By mixing PLA pellets and recycled wood waste material filament was produced with a diameter size of 1.65±0.10 mm and used to print a small variety of test parts. This method while developed in the lab may be scaled up to meet industry needs as the process steps are uncomplicated. Small batches of 40wt% wood were created, but showed reduced repeatability, while batches of 30wt% wood showed the most promise with ease of use.”
The researchers wrote that further work on creating waste-based WPC filament should include quantifying the material’s mechanical properties after the first cycle, and then comparing it to other materials, such as pure PLA and modified wood fiber powder. Additionally, industrial equipment and grouped 3D printing nozzles should be evaluated in terms of scaling up the process.
Co-authors of the paper are Adam M. Pringle, Mark Rudnicki, and Joshua Pearce.
Discuss this and other 3D printing topics at 3DPrintBoard.com or share your thoughts below.