Companies, organizations, and individuals continue to attempt to lend support to the COVID-19 pandemic supply effort. We will be providing regular updates about these initiatives where necessary in an attempt to ensure that the 3D printing community is aware of what is being done, what can be done and what shouldn’t be done to provide coronavirus aid.
Established AM service provider, FIT Additive Manufacturing Group, has developed a filter-carrying mask for the general public. The mask is made up of two pieces, a 3D-printed mask and a disposable filter. While the 3D-printed component can be easily disinfected, the filter can be made from just about any cloth material, such as a paper towel or tissue paper, which can then be swapped out and disposed of quickly. According to a study by the University of Cambridge, a vacuum cleaner bag exhibits the performance characteristics most similar to surgical masks.
Given the fact that the Centers for Disease Control is now recommending that the general public wear cloth masks, this may be a suitable method of creating one, while freeing up respirators and surgical masks for medical workers. The president of the German Medical Association too called for the wearing of protective masks. FIT is currently designing a smaller model specifically for children. The file for the existing version, optimized for selective laser sintering, can be found here.
Markforged is the latest company to jump into 3D printing nasal swabs, alongside Carbon, Formlabs, EnvisionTEC and HP. Working with Neurophotometrics, the additive manufacturing (AM) startup is 3D printing 10,000 swabs daily with plans to scale to 100,000 daily. The partners are working with the San Diego Covid Research Enterprise Network (SCREEN) Initiative to manufacture the tools, made with base of 3D-printed nylon and a tip of wrapped rayon.
The group has tested the nasal swabs with 50 volunteers, with patients who tested positive for COVID-19 re-tested three to 14 days later with both commercially available swabs and 3D-printed counterparts. According to Markforged, the commercial swab detected the virus in most but not all of the patients, but all of the 3D-printed swabs came back positive. This indicates the possibility that the 3D-printed swabs may be more effective at collecting viral particles and reduce the rate of false negatives (albeit with an extremely small sample).
Upon completing clinical validation with the institutional review board at Rady Children’s Hospital and the University of California San Diego, Rady Children’s has ordered 30,000 swabs. The swabs are being sold at the Neurophotometrics website. As discussed in yesterday’s update, nasal swabs are in short supply to perform COVID-19 tests; however, they are only one part of the problem. There is also a lack of testing equipment, reagents, and trained staff to process tests.
Metal powder bed fusion (PBF) systems manufacturer SLM Solutions launched a coalition directed toward rapidly producing parts needed for COVID-19 medical supply efforts. The Additive Alliance Against Corona is aimed at leveraging machines and processes already certified to current European “Medical Device Regulation” and ISO 13485 guidelines to make medical parts and tooling for medical parts. According to the company, SLM metal PBF 3D printers in the U.S. are already being used to manufacture metal injection molding tools to produce face shields. Companies that can lend their support are invited to join the coalition via SLM’s dedicated webpage.
GE continues to produce personal protection equipment (PPE), specifically face shields, which can help extend the lifespan of the N95 respirators beneath said shields. GE Additive has designed a 3D-printed adapter that converts a standard hard had and visor into a face shield.
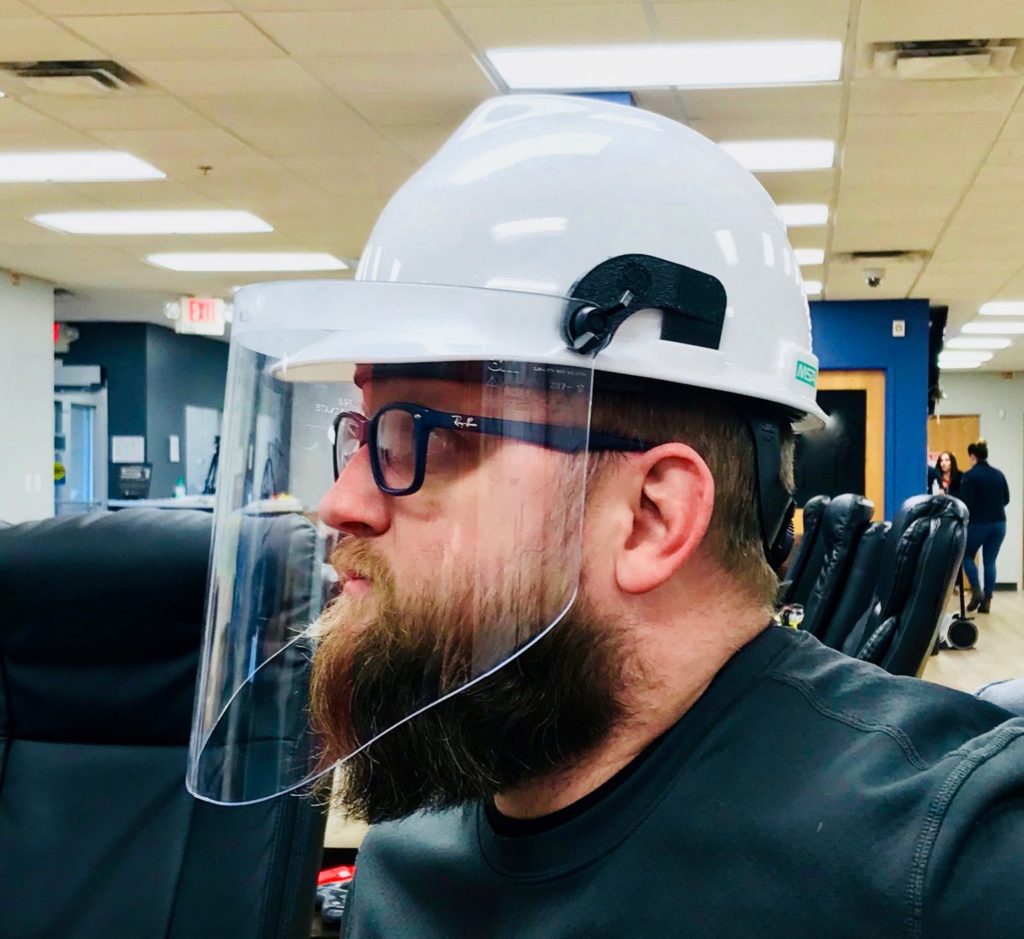
A face shield made with a 3D-printed adapter and a standard hard hat. Image courtesy of GE Additive.
Due to the fact that hard hats have lateral and frontal tabs above the rim for mounting accessories, GE’s solution is a simple one. The adapter fits into the lateral tab of a standard hard hat and features a twist bolt that grabs onto the visor. The visor can also be easily raised and lowered. The adapter is 3D printed on fused deposition modeling systems from ABS plastic. There have been some reported issues with autoclaving 3D printed ABS with parts failing sterilization or warping during the process during both flash and regular autoclave. The company has provided the file online and suggests that any hobbyist system can print it.
Interestingly, the design introduces another element that is dependent on the currently disrupted supply chain: finding hard hats. GE’s partner in the endeavor, TriHealth, reached out to an industrial supply company for the accompanying hard hats.
As mentioned in our interview with Dr. Beth Ripley, Director of the VA 3D Printing Network in the VHA Innovation Ecosystem, 3D printing is currently acting as a stopgap solution for rapidly producing necessary medical supplies until mass manufacturing can produce parts in larger quantities more quickly.
In this case, GE Additive is providing a stopgap in the PPE supply chain while only partially ramping up production in the ventilator supply chain. GE Healthcare has quadrupled ventilator production at its Madison, Wis. location, but GE Aerospace has laid off employees due to financial issues caused by the COVID-19 outbreak as its own aerospace workers demanded the production of jet engines be redirected toward supporting GE Healthcare’s ventilator operations.
As the pandemic continues to grip the world, we will continue to provide regular updates about what the 3D printing community is doing in response. As always, it is important to keep safety in mind, remain critical about the potential marketing and financial interests behind seemingly good humanitarian efforts from businesses, and to do no harm.
The post 3D Printing and COVID-19, April 9, 2020 Update appeared first on 3DPrint.com | The Voice of 3D Printing / Additive Manufacturing.